While rail is already among the cleanest modes of transportation, there is still considerable potential for improvement. Consequently, the industry is moving towards sustainable solutions that significantly reduce carbon emissions and environmental impact.
Müller Technologie’s diesel locomotives were originally built in the mid-1990s and have already been operating for 30 years. The locomotives are generally used in construction and maintenance, and one of their tasks is to supply power for electric tools. This previously meant that the diesel engine had to be run in idle mode all the time the locomotive was at the work site. The resulting fumes and noise were an inconvenience, especially in urban areas, tunnels and during the night. Nevertheless, the company is constantly renewing its fleet using the latest technology to continuously reduce CO2 emissions.
Therefore, Müller Technologie’s innovative Aeam 841 hybrid locomotives are based on the originally diesel locomotives that are now being converted to enable the three mode operation (tribrid). They are mainly used in construction, maintenance, shunting and cargo service markets. Following the conversion, the locomotives will be able to use power from overhead lines, traction batteries, and new model diesel generator. The main aim is to minimize CO2 emissions to meet new environmental requirements.
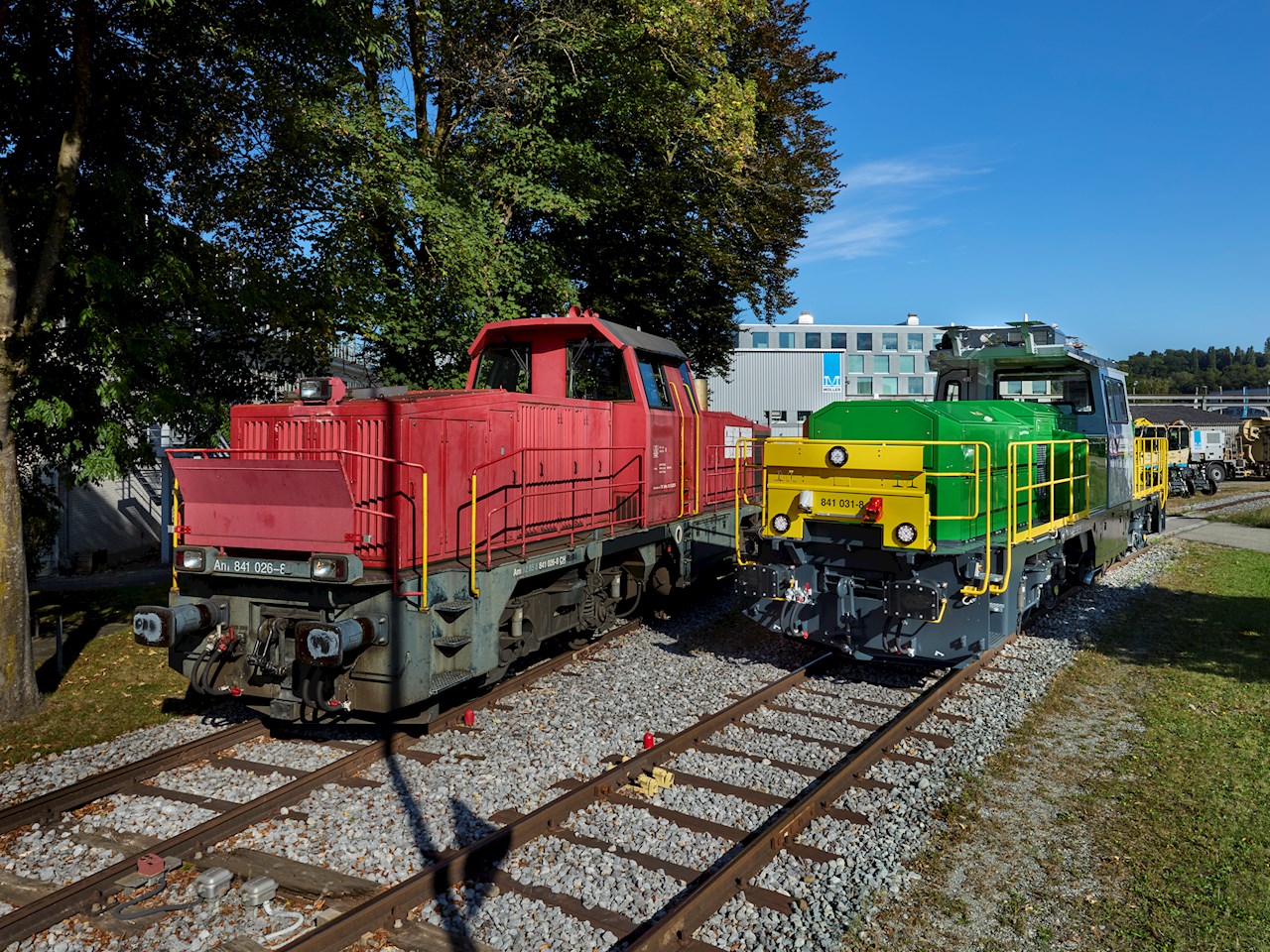
Seeking a technology partner to help develop the traction chain solution and supply the necessary equipment, Müller approached ABB. The project required high operational reliability and cost efficiency, as well as the need to fit the traction equipment into very limited space. It was also necessary to implement the conversion without modifying the locomotive body, as this would ensure a more straightforward homologation process.
The existing diesel-electric locomotives had a 920 kW engine powering a generator, with the output fed via a two-level traction converter of 724 kW being upgraded to four motors totaling 1000 kW. During the conversion the diesel engine was replaced with a 500 kW unit capable of running on renewable fuel, and the original electric motors were completely overhauled and retained.
Advanced traction solution
The traction system supplied by ABB consists of BORDLINE® CC1500 AC Compact Converter, eBox, Traction Batteries, and a traction transformer.
The BORDLINE® Compact Converter is a highly integrated solution which includes a line converter, two traction converters, two auxiliary converters and a Traction Battery Chopper including low pass filter. Its three-level traction converters are around 7-9% more energy efficient than the locomotives’ original two-level units. They put less stress on the motor insulation and have lower harmonic losses which means additional energy savings in the motors. The regenerative braking function provides further energy savings by feeding braking energy into the Traction Batteries or overhead line.
The eBox provides an interface between the converter and batteries and includes the Battery Management System. The traction batteries are based on LTO (lithium-titanium-oxide ) cell technology, which has the advantage of very short charging times. It will be possible to charge the locomotive’s batteries from empty in around 20 minutes, enabling a full recharge during a short break in the working day.
The traction batteries can be charged from the overhead line, diesel generator or depot power supply.
Close collaboration on system development
“We worked closely together with ABB, not only to develop the traction chain solution but also to ensure it would fit into the locomotives,” says Railway Vehicles Project Team of Müller Technologie AG. “ABB is a reliable partner, and we were pleased with the smooth way that our two companies cooperated. We are already discussing new opportunities for collaboration.”
“We developed and implemented this three mode operation together with the team at Müller,” says Mike Bamberger, Head of Traction Sales of ABB Switzerland. We reused as much as possible from the existing locomotives, and we designed the system so it would work with the original motors. They have been completely refurbished, but they did not need any modifications.”
We worked closely together with ABB, not only to develop the traction chain solution but also to ensure it would fit into the locomotives."
Sustainability through low-emission operation
The retrofit project prepares the 5 locomotives for a sustainable future and will extend their lifetime by further 25 years. The project itself is being implemented on an environmentally-friendly basis, with 28 tons of steel - including the old engine, traction converter, and some body panels – being recycled from each locomotive. As well as retaining the existing motors, the chassis and bogie frames have been overhauled and adapted to meet new requirements. This way, the vehicles are given back to the market as rental locomotives, with important savings of steel. Retrofitting old locomotives with energy efficient technologies aligns with climate protection goals, promoting sustainable rail transport.
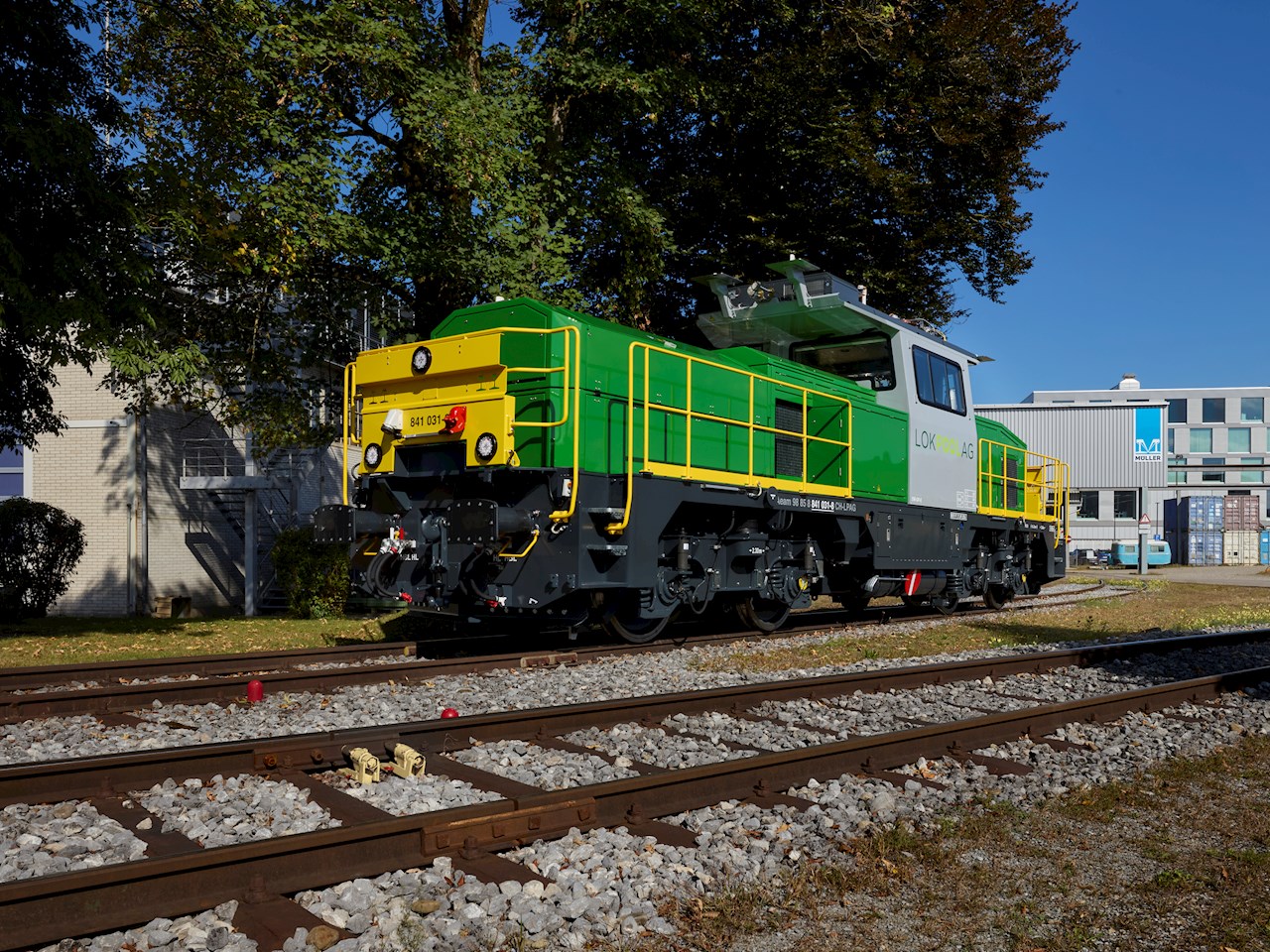
The locomotives will reduce CO2 emissions to a minimum improving the working conditions of the personnel, by reducing fumes and noise. ABB’s traction chain allows silent operation during the night and in densely populated urban areas.
The hybrid locomotives will be capable of operating without the need for external energy sources over several assignments. Müller Technologie has calculated that they can use overhead lines to power 80% of their trips, with the remainder covered by the traction batteries or diesel generator. Overall, diesel consumption is expected to be reduced by up to 85% compared to the pre-conversion figure. This equates to 8,500 liters of diesel fuel per locomotive that will be saved every year.
The capability to operate emission free at work sites is an important advantage of the new locomotives. The Traction Batteries are therefore not only used for propulsion, but also supply the tools used on site.
As a result of the converted locomotives’ sustainability benefits, the retrofit project will play its own part in helping Switzerland reach its target of net-zero emissions by 2050.
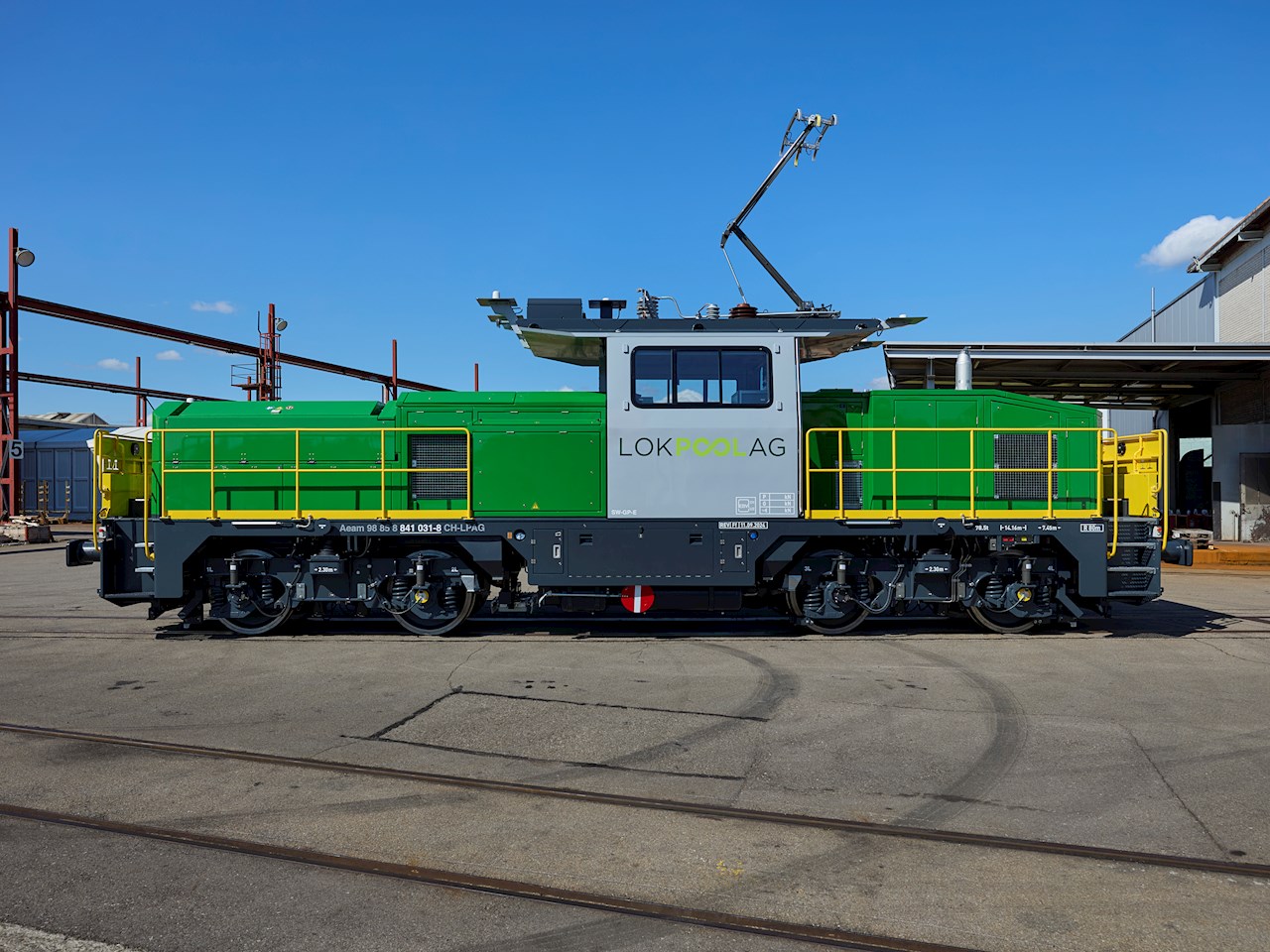
Adopting sustainable alternatives to traditional diesel engines significantly reduces carbon emissions and helps the rail industry to decarbonize. ABB’s extensive expertise along with the comprehensive traction solutions for sustainable transportation will pave the way for a leaner and cleaner future.
Müller Technologie AG is based in Frauenfeld, around 50 km northeast of Zurich, Switzerland. The family-operated company develops, builds and maintains machinery for rail track construction, as well as special rail and road vehicles. In addition to the Aeam 841 hybrid locomotive, the company is developing a fire and rescue vehicle. Other Müller group companies undertake construction and maintenance of tracks, as well as ensuring safety at railway construction sites.