A double sensor design for industrial surface temperature measurement uses model calculations to enhance accuracy and strongly reduce response time. Surface temperature estimates are comparable to intrusive methods. This fit-for-industry design provides flexibility without loss of performance.
Jörg Gebhardt and Guruprasad Sosale ABB Corporate Research, Ladenburg, Germany, joerg.gebhardt@de.abb.com, guruprasad.sosale@de.abb.com; Wilhelm Daake, Peter Ude, Karsten Schröder, Horst Schwanzer ABB Industrial Automation, Minden, Germany, wilhelm.daake@de.abb.com, peter.ude@de.abb.com, karsten.schroeder@de.abb.com, horst.schwanzer@de.abb.com
By linking communication between people, services and things, Industry 4.0, appears to offer many opportunities and yet, the disruption poses a threat for some companies. High-flying promises are made about new automation paradigms, but concepts for successful implementation are often lacking. A reasonable digitalization strategy would provide customers with enormous benefits: the reduction of risks for existing processes and flexible answers to the challenges of increased pace and reduced workforce availability.
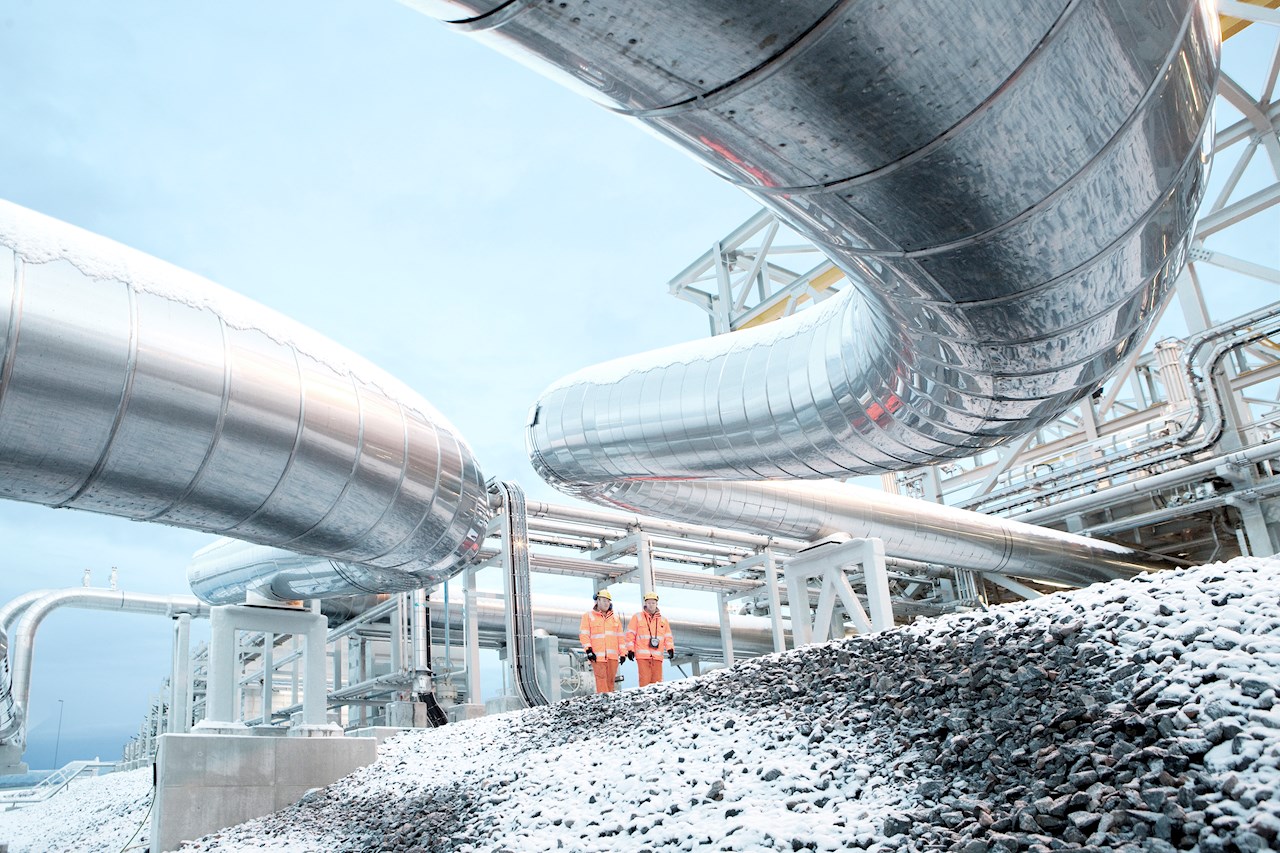
The “Normenausschuss für Mess- und Regeltechnik” (NAMUR) in the NAMUR Open Architecture provides decision-makers with a reassuring risk-minimizing digitization overview [1]. Sensors play a fundamental role in Industry 4.0 →1, the information they provide at the field level underpin any advanced use of plant data to increase productivity, efficiency and safety by preempting interruptions and failures, thereby making production agile.
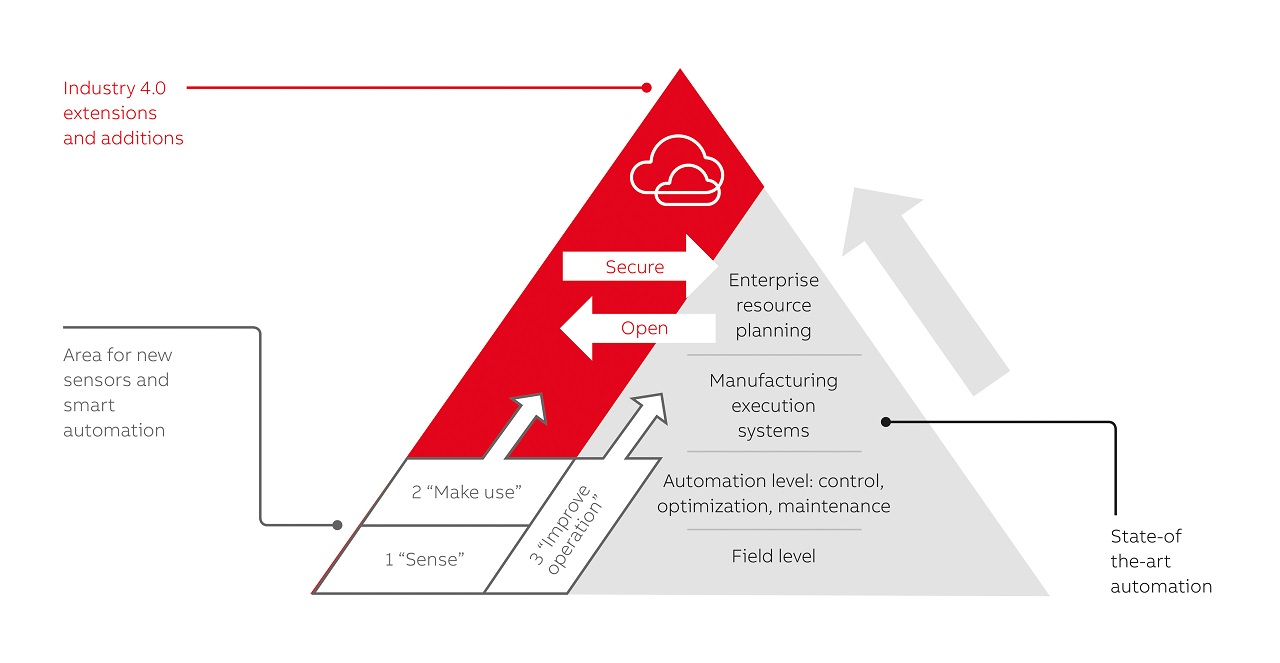
Recognizing customers’ need to keep a competitive edge, ABB’s experts develop accurate sensor products and the theoretical groundwork for enabling algorithms to be combined with artificial intelligence (AI) to allow enterprises to gain that edge. Existing initially outside of the classical automation pyramid, ie, in condition monitoring, the same methods could produce gains that can be applied to conventional plant operations and process control, once experience and confidence in the novel technology has been gained.
Clearly, the digitization of industrial processes in oil, gas and chemicals (OGC) and the food and beverage industries relies on copious amounts of sensor information to enable recognition of trends, predict problems and, above all, allow strategic decisions to be made [2]. Yet, for companies to accumulate vast data sets, sensing must be accurate, have a rapid response time, and must be cost-efficient to produce and use, it must be non-disruptive to plant processes and able to communicate intelligently with all areas of measurement and analytics.
ABB’s new noninvasive temperature sensor, NiTemp, is just such a device; it is poised and ready to act as a first step – ensuring that process industries can exploit the benefits of Industry 4.0.
Conventional invasive methods
Traditionally, temperature measurements relied on invasive methods. A temperature sensor was inserted with a thermowell through an opening in a pipe or vessel into the medium to be measured, making accurate and rapid response measurements possible. Despite this, such solutions entail enormous risk to employees, and possible damage to the facility. Hot, abrasive or corrosive media can damage thermowells requiring replacement or repair and even the need to shut down facilities or reroute processes. Also, rapidly flowing media can cause thermowells to rupture due to vortex formation and subsequent oscillations; the result can be catastrophic failure [2].
Noninvasive temperature measurement has been practiced in industry for decades, generally as a fallback option when insertion of a thermowell was either an extreme nuisance to the process or posed unacceptable safety risks. The food and beverage industry avoids the use of thermowells because of the risk of contamination.
In brownfield installations, the facility must be shut down and pipes emptied for invasive measurement devices to be installed – a costly nuisance. Additionally, intrusive techniques affect the measurement itself: the result of the temperature drop induced between the process medium and the sensor [3] – clearly this is suboptimal. Furthermore, thermowells are complicated and expensive to engineer [3,4].
A highly skilled workforce is necessary for the realization of the measurement point. In all retrofit use cases the process is shut down and pipes cleared. This can delay the setup process for months. Once the thermometer is inserted and operation begins, there is a real risk of process disturbance, fouling and damage of the equipment. This, in combination with high costs, leads plants to design control instrumentation minimally with as few measurement points as possible, even though more measurements would be useful, eg, for process optimization and, analyses of problem root causes. This is especially true for industries that endeavor to exploit the rich value of Industry 4.0. To be useful for process control, a temperature measurement point must be designed to be noninvasive and compatible with digitization technologies.
Advantages of noninvasive temperature measurement
ABB’s novel design approach to products that generate highly quality-relevant process data, especially for sensors that do not directly influence plant operations, will enable process industries to take full advantage of Industry 4.0. By eliminating the need to open the pipe, installation cost and work time are drastically reduced, especially if the sensors work with wireless communication and an autonomous energy supply method, such as battery or, energy harvesting [5]. The advantages, however, do not come without a cost. Thorough knowledge is required about the thermal behavior of the measurement instrument, the process medium and their connection.
Two-step approach to noninvasive temperature measurement
The main barrier to establishment of noninvasive sensing is the effect of the ambient environment on accuracy and response time. Fluid flow with average temperature, Tm, in a process pipe, may cause a non-trivial thermal field across the flow profile, pipe wall, insulation and ambient air.
Two cases are distinguished:
Case 1: The temperature Twa on the outer surface of the process pipe often very accurately matches Tm. This is particularly true for aqueous solutions in practically all relevant use cases encountered. Consequently, the measurement can be installed without any knowledge of the process or pipe parameters. A first compensation algorithm calculates Twa using only device-internal features.
Case 2: In the case of more viscous and/or low-heat conductive liquids, such as certain oil, and for gases, Tm can be calculated from Twa online with a second algorithm; some pipe and or process parameters must be provided to the algorithm.
In both cases, the reliable determination of the pipe surface temperature, Twa is crucial, ie, the performance of the first algorithm mentioned above must occur. In the simplest setup, the algorithm works with signals delivered from:
• a primary sensor that is located as close as possible to the pipe surface, and
• from a secondary sensor that is located in a definite distance from the pipe surface: the reference sensor.
The following section shows how the measurement performance is influenced by the design of the sensing device and the positioning of the primary and reference sensors on the vessel to be measured.
Design rationale
The temperature of a surface may be inferred from a measurement of two temperatures located within the vicinity using knowledge about the thermal resistance between the points. In practice, this method can be very slow due to the finite velocity of heat waves along the thermal path.
At an abstract level, the one-dimensional heat equation in a homogeneous material is an illustrative example:

For the numeric examples below, a stainless steel bar has been taken as example, with a quadratic cross-section and length and diffusion constant, respectively:

A situation of particular relevance is a step heating of one end of a bar, eg, at x=0, up to T0 = 80 °C, the bar being initially in equilibrium at TL = 20 °C, which is also kept as a Dirichlet boundary condition at x = L.
Obviously, the bar will approach a linear T-profile over time. The thermal field evolution is given by:

f is the decaying part, and f(0,x) can be expanded in Fourier components to determine its temporal behavior. Since f(0,0)=f(0,L) = 0 due to boundary conditions, only sine components with wavelength are considered, with corresponding decay rates:

This analytical result is plotted for a number of time points →2.
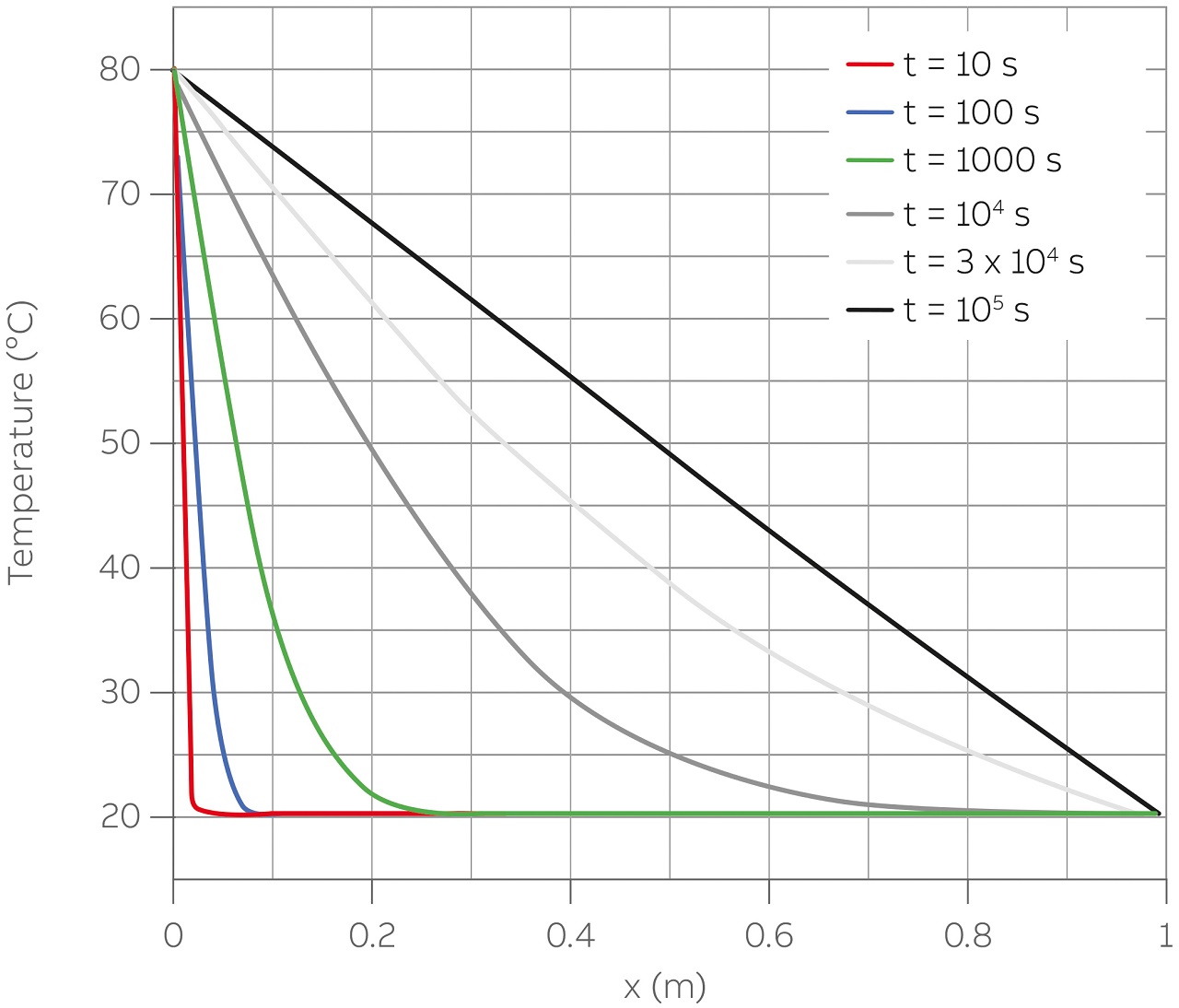
Obviously, relaxation times for points at a distance of about 1 m from the left end are of the order of one day; whereas, points located closer to the surface reach their equilibrium much faster. These numerical solutions are critical to the system design of noninvasive measurement.
Algorithm performance depends on sensor location
If the primary sensor is assumed to be located at 0.01 m from the heated end of the bar, a number of reference sensor locations at various distances to the primary sensor are considered: x = 0.001; 0.01; 0.1; 1 m. The model-based signal is computed from the primary and reference signals [5].
Typically, the time derivatives of the measurement signal are used in order to invert the delay of heat-conduction signal transfer and reduce response times. However, noise amplification can lead to severe problems. Relying on the analysis and simulation of the dispersive, or dissipative behavior of the heat equation, a derivative-free signal processing is sufficient for practical purposes if the reference sensor is suitably located.
A strong convergence acceleration of the measurement is achieved by shifting the reference sensor towards the surface →3. Consequently, the reference sensor should be located as close as practically possible to the primary sensor.
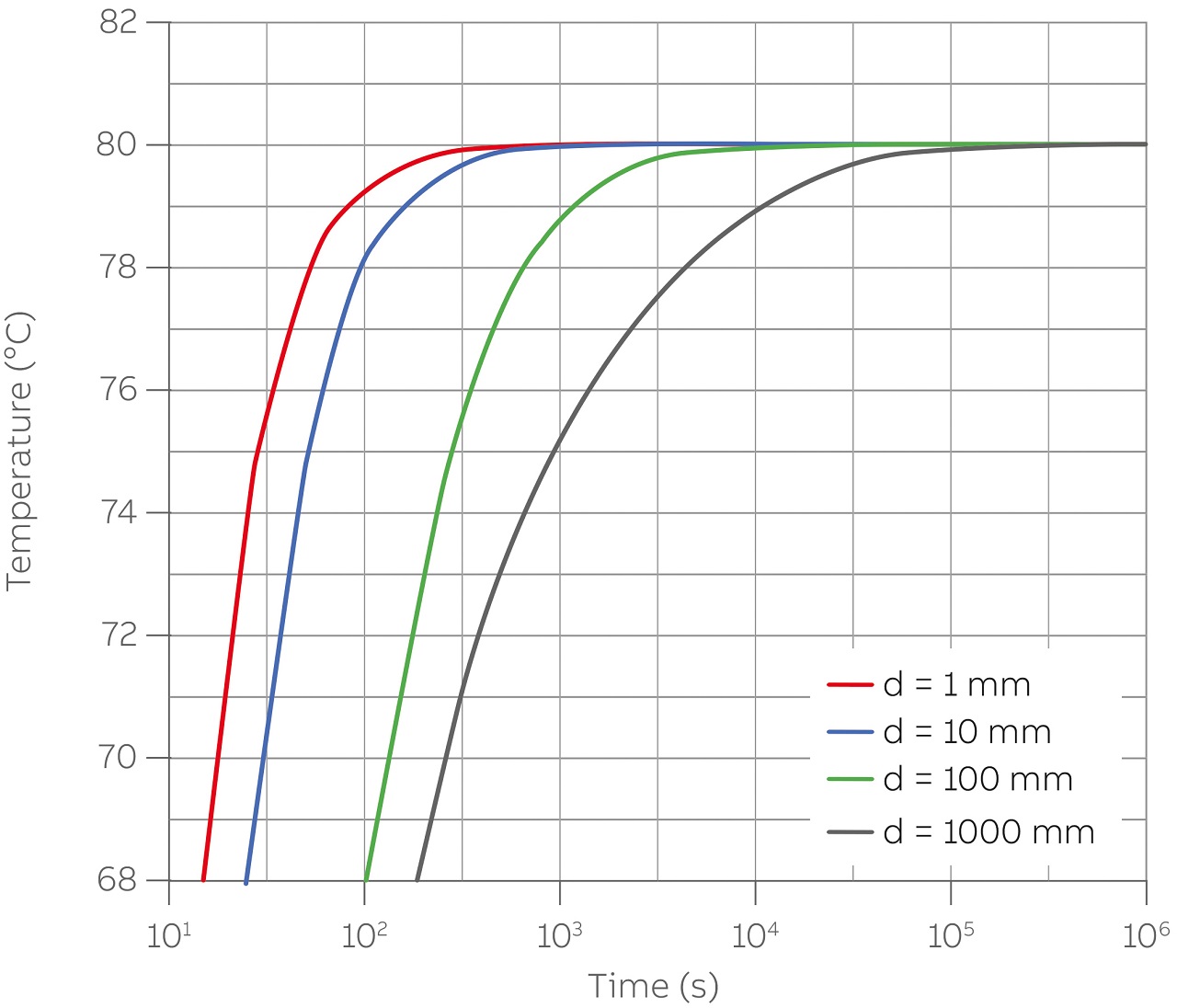
NiTemp design and validation
The NiTemp design consists of a combination of two thermometer inset rods, each with a diameter of 3 mm →4; these are married in a reproducible way to ensure thermodynamic definiteness. Only the primary sensor inset is pressed directly to the pipe surface.
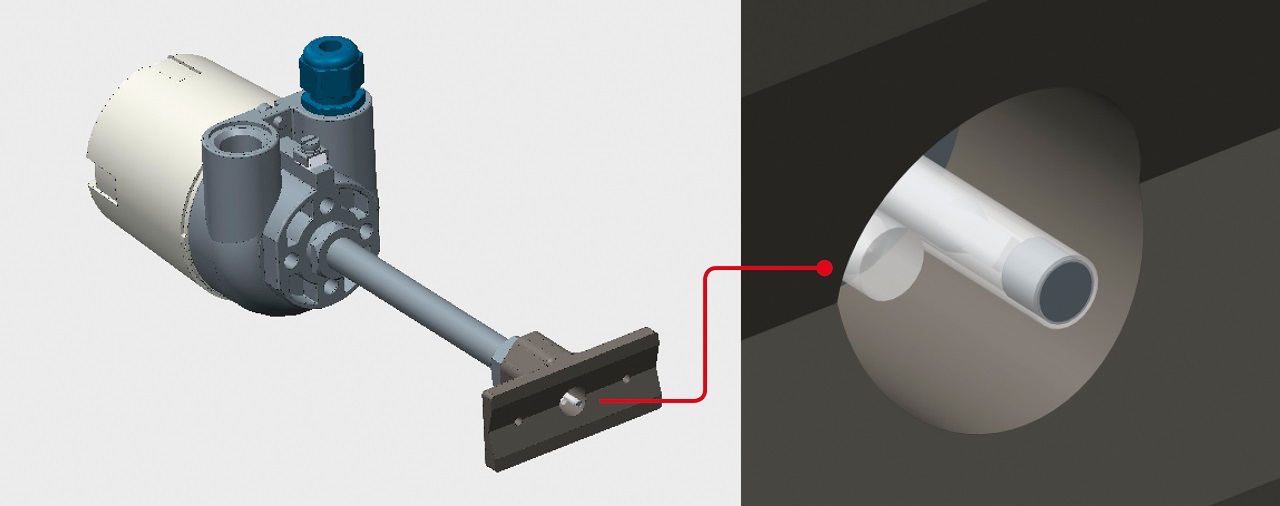
Design validation
Accuracy and stability were assessed under varying ambient temperature changes →5a using a heatable aluminum block and the two devices situated in a climate chamber. The benchmark surface temperature is measured by a Pt100-resistance sensor that is glued directly on the surface. The accuracy achieved with NiTemp, if the ambient temperature (Tambient) changes strongly, is approximately +/– 1 °C →5b.
Image currently unavailable
Image currently unavailable
Image currently unavailable
Image currently unavailable
Image currently unavailable
Image currently unavailable
05a ABB’s climate chamber for testing on-site. 05b Stability of surface measurement: The non-invasive device stays firmly close to the ideal surface reference even when T-ambient varies between -40°C and +80 °C.
05 The robustness of the two devices to changes in ambient temperature was tested by ABB’s scientists.
The step response time of the NiTemp double sensor configuration has been extracted from the behavior observed when the sensor is exposed to a temperature step function, eg, by contacting it to a hot surface at a specific time →6.
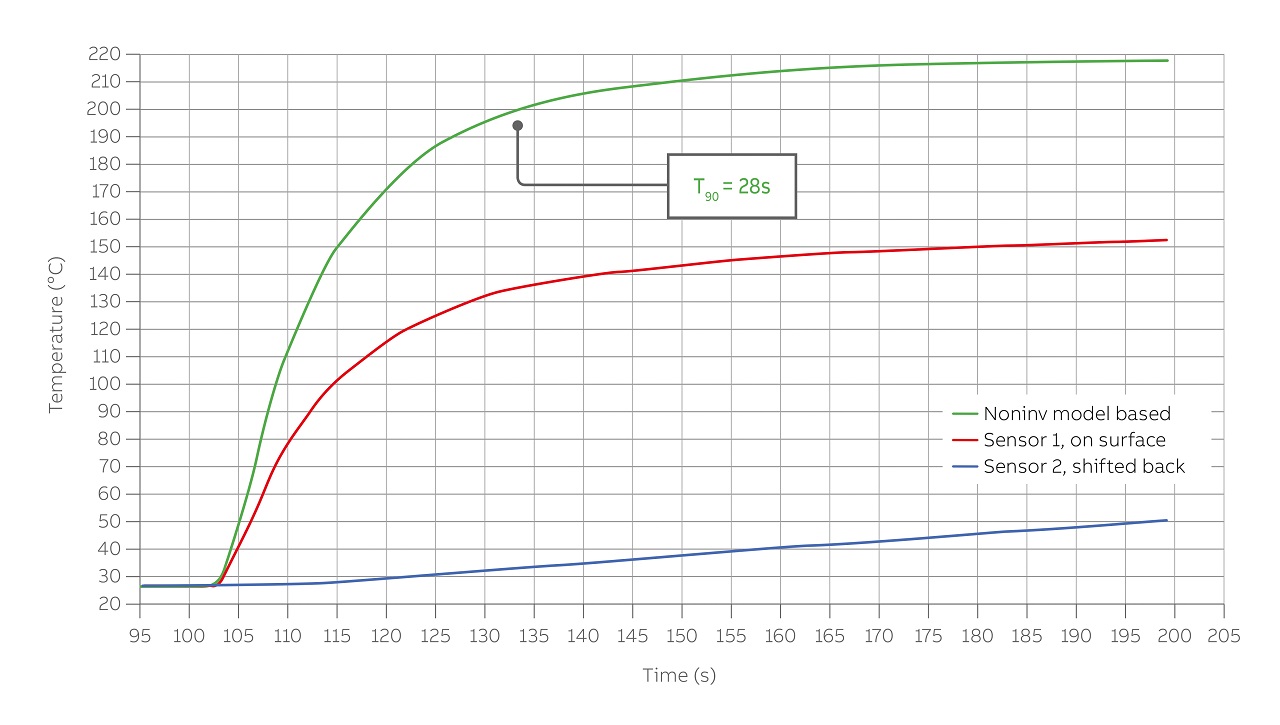
A response time of T90 ≈ 28 s was measured, which is a phenomenal value — more than competitive with standard invasive measurement setups in use.
How would the noninvasive sensor compare to an invasive one that is installed, in parallel, in the same process? ABB evaluated the behavior of both invasive and noninvasive measurements when a temperature step change is created in a process pipe to address this question →7.
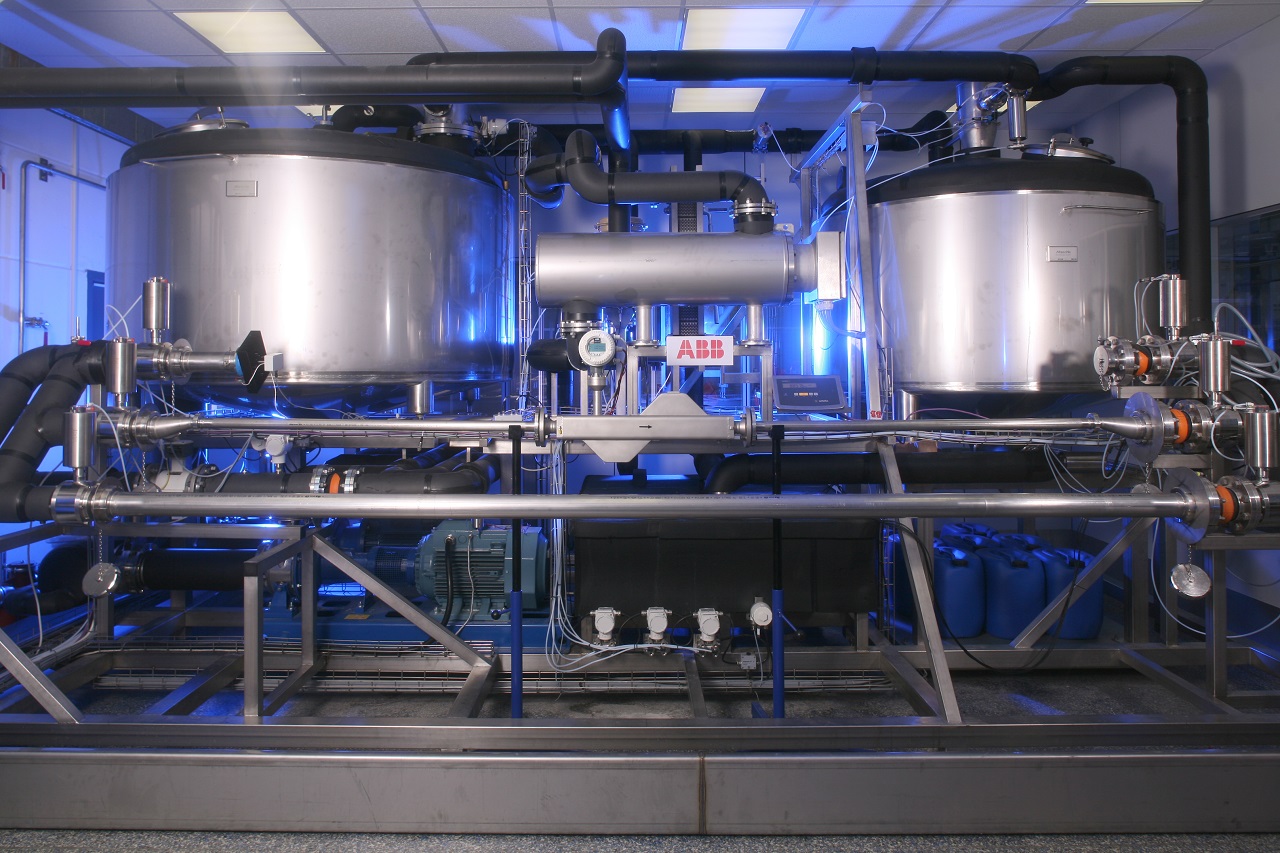
A water tank was heated to ≈ 80°C; the ambient temperature was ≈ 23°C. The test area examined was a pipe that could be closed by ball valves on both sides. When the tank was heated, a pump started to work against the closed entry valve of the test pipe. The valves of the test pipe opened quickly at a specific time such that a front of hot water entered the pipe at a speed of ≈ 1 m/s.
The test pipe size DN80 was equipped with a state-of-the-art invasive T-measurement with a thin-walled thermowell. The noninvasive device was clamped onto the pipe at a distance of 20 cm from the invasive point.
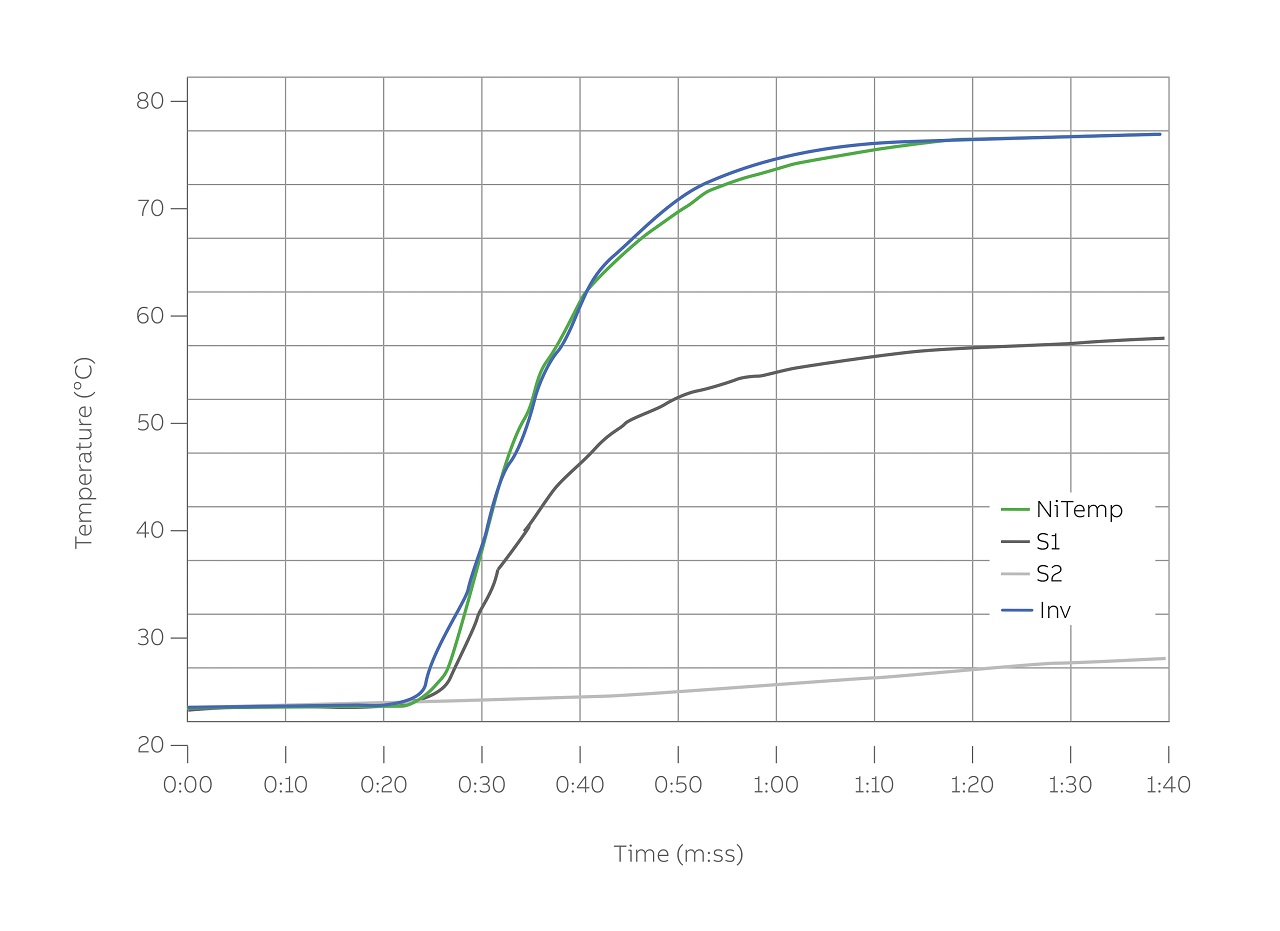
The measurement response of the two devices to the temperature step of the medium in the pipe→8 shows that the invasive and noninvasive measurement curves are in agreement. Mostly:

In practice, all slowly decaying deviations are thus so small that there is no negative influence on the measurement.
Another consideration is the use of more massive thermowells required by regulation today. Hence, in an industrial setting, invasive sensors would show a longer response time than observed in the experiment conducted by ABB [3].
New applications for noninvasive measurements
ABB’s experimental results and physical predictions show that noninvasive temperature measurement can successfully compete with conventional invasive measurement if the application is of a type where Tm ≈ Twa and if the pipe surface is suitably measured: ABB’s NiTemp sensor is perfectly designed for this purpose.
So, ABB’s NiTemp model-based device can be used in a large number of applications, especially for processes with aqueous solutions, even those with low flow velocities. It is applicable to processes that use liquids, like oils, or for gases, as well. Calculations of expected deviations can be made and compared with results of acceptable use cases such as for water and crude oil →9.
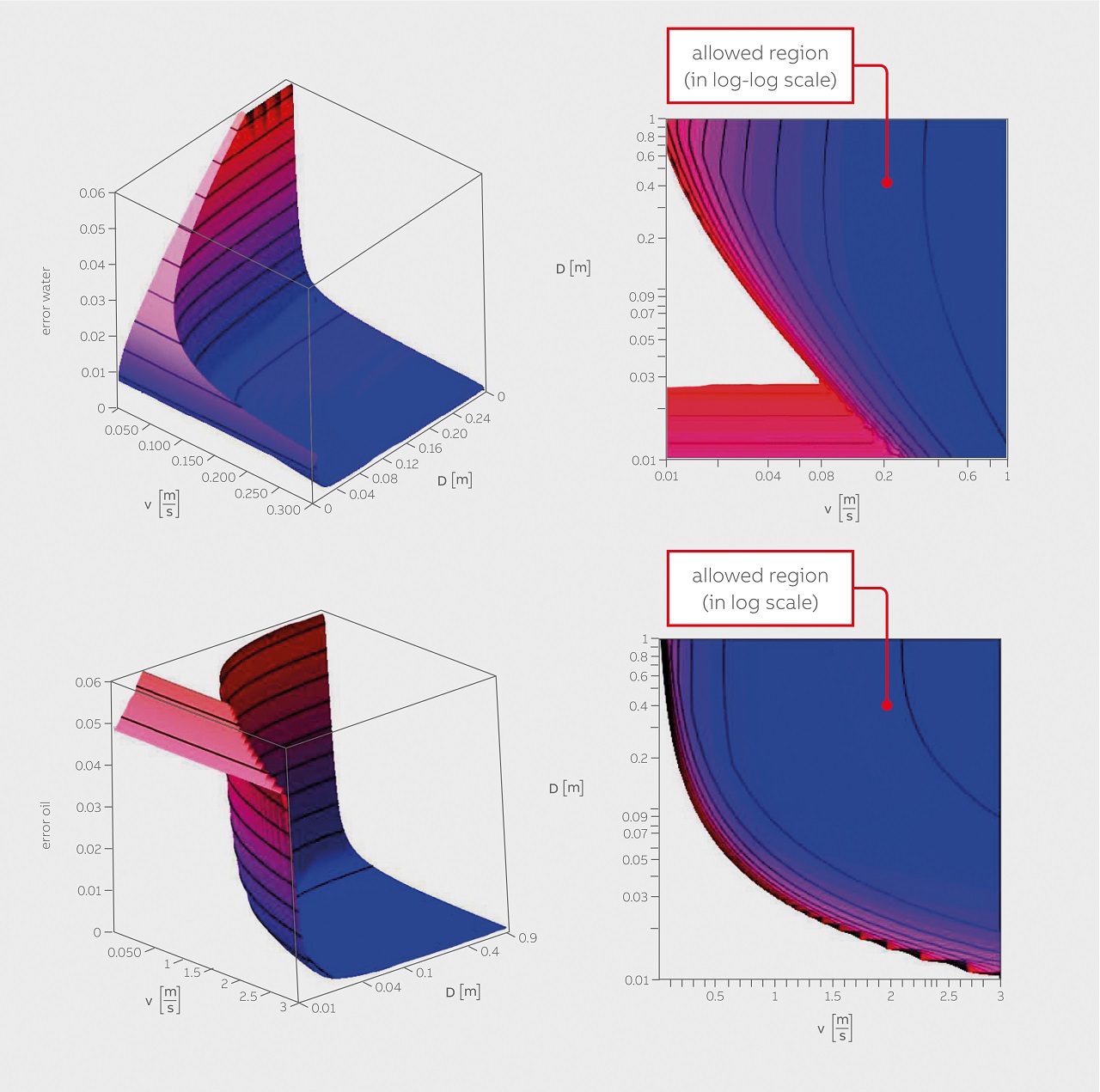
Noninvasive temperature measurement has the potential to replace a large number of invasive instruments in greenfield and brownfield applications. The superior accuracy and rapid response time, in combination with improved safety and lower cost and logistical effort associated with the elimination of the thermowell, make the gathering of vast amounts of field data easier and more efficient. ABB goes one step further by launching this innovative technology as a wireless device, in 2019; this device will be fully integrated in ABB’s state-of-the-art connected services. Data will be available for all areas of measurement and analytics, production and decision-making. This advanced technology will allow the food and beverage and OGC industries and others to fully embrace the benefits of Industry 4.0 and be at the vanguard of automation.
References
[1] J. De Caigny. 2017, November. NOA – NAMUR Open Architecture [Online].
Available: https://www.namur.net/fokusthemen/namuropen-architecture
[2] Projektgruppe “Technologie-Roadmap”, VDI/VDE-GMA/NAMUR, „Prozesssensoren 4.0, Thesen und Handlungsfelder“, 11/2015.
[3] T. Merlin, A. Decker, J. Gebhardt, and C. Johansson. “Absolute zero invasion“. ABB Review, 2015(4):58–63, November 2015.
[4] Standard: ASME PTC 19.3 TW–2016 Thermowells, 2016.
[5] S. Wildermuth, A. Decker, J. Gebhardt, T. Merlin, and H. Schwanzer. “Non-invasive, energyautonomous, and wireless temperature sensor for the process industry”. In: IEEE 21st International Conference on Emerging Technologies and Factory Automation (ETFA), 2016.