Simulations and digital twins are revolutionizing the way we think about the development and deployment of products.
Marek Florkowski, Daniel Szary ABB Corporate Research Krakow, Poland, marek.florkowski@ pl.abb.com, daniel.szary@pl.abb.com; Andreas Moglestue ABB Review Baden-Daettwil, Switzerland, andreas.moglestue@ch.abb.com
The phrase “all is number,” attributed to Pythagoras, is more pertinent now than ever before. Numbers enable us to capture and process physical magnitudes, be they positions, temperatures, flow rates, field strengths and many other quantities. A vast inventory of ingenious methods exists for measuring, or in other words, describing the physical world using numbers. The age of computing has added a new and highly versatile tool: simulation.
Simulation permits the inference of data that is not directly available for measurement. It is possible, for example, to gauge the temperature deep inside an object from measurements of the surface temperature, combined with physical understanding of what is happening inside the object. The inaccessibility of a measurement point must not be strictly spatial. The data of interest can also be in the future, or even in a system that has not physically been built.
Compared to physical testing, simulation can deliver huge savings in time and costs, as well as avoiding waste and potentially dangerous situations. Physical laboratory testing incurs a considerable time latency due to the need to prepare and build test samples and setups, constraints imposed by the capability and capacity of the lab, not to mention inflexibility should developers request a last second modification. In a design process requiring numerous design iterations, with each iteration having to await the results of the previous test, such a time penalty can be immense.
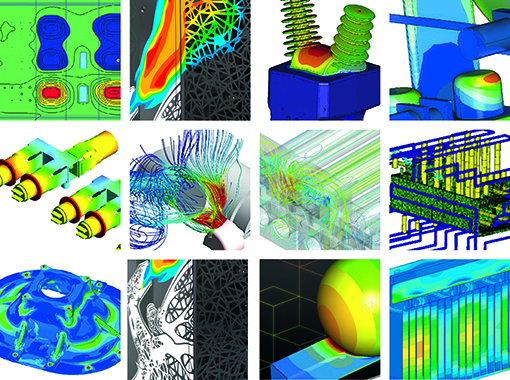
Time and cost advantages apart, simulations also permit a far broader range of variants to be studied. Product developers have more scope to be innovative, can test a far greater number and combination of variants, and can experiment with unorthodox approaches. The result is a more optimized solution.
In some cases, simulations are the only viable way to verify a design because physical tests are not realistically feasible, for example large scale seismic tests.
Today, almost all aspects of a product’s lifecycle can be simulated: manufacturing, virtual testing, transportation, regular operation, aging, harsh environmental conditions, extreme situations (earthquakes, arcs, thunder strikes, overloads, etc.).
Simulations in ABB
ABB makes broad use of simulation in product development. Simulations cover a wide range of fields, including, electromagnetics, thermodynamics, mechanics, fluid dynamics and material science. Increasingly, simulations also combine several of these domains and capture not only the sum of their effects but also the coupling and interactions between them in what are called multi-physical simulations.
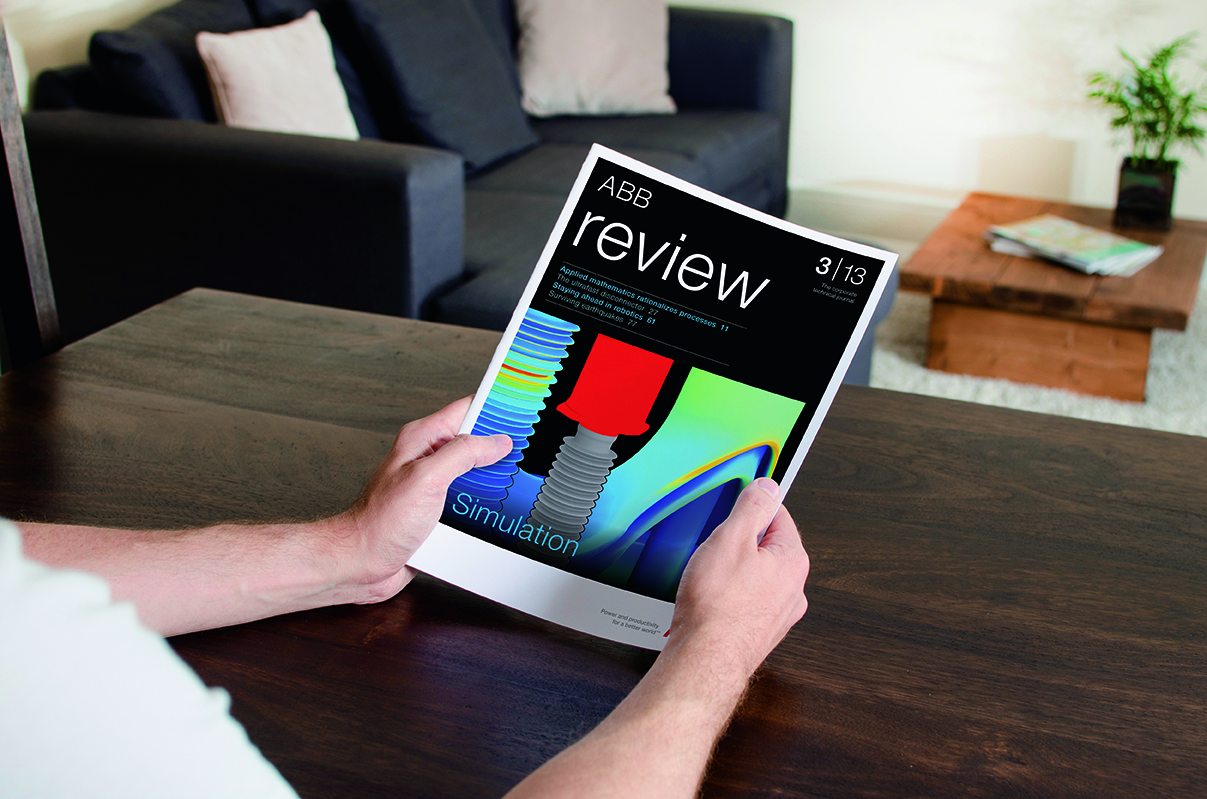
In 2013, ABB Review dedicated an issue to simulations →1. A look back on that publication today reveals just how far the field has advanced since then. Capabilities that at the time were considered wishful and futuristic are now tested and proven components of the simulation toolbox. The present issue of ABB Review brings the picture up to date and looks towards future developments.
Progress in simulations
Major drivers in advancing the capability of simulations have been growth in computing power and speed as well as affordability, but also ease of use. What would have been a major, processor-hungry job 25 or 30 years ago can now easily be completed in less than half an hour (plus preparation of the model). Besides the overall increase in speed, today’s simulations can take a larger number of variables into account, adding to the overall accuracy of the simulation.
Further to the hardware and cost aspects, there have been considerable changes in the roles of simulation engineers. In the early days, experienced engineers would typically have invested a lot of time in creating models and setting up simulations. Such is the advancement of knowledge and computer literacy, but also improvements in automation and the tools themselves, that today many such tasks can easily be performed by junior staff or students. Far from implying a de-skilling, this shift means simulations experts can now concentrate on the interpretation of results and on guiding and advising design decisions →2.
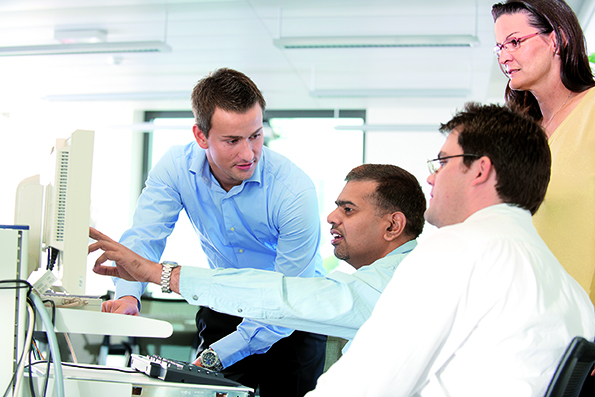
Year by year, simulations are becoming simpler to use. This “democratization” is enabling the adoption of simulation in more and more areas.
Feedback from the physical world
The most sophisticated simulation is of no value if the results do not adequately reflect what happens in the physical world. Confidence in simulations is improved by comparing simulation results with physical tests as well as field experience. It is the hallmark of a good simulation method that results do indeed prove a good match to laboratory tests →3.
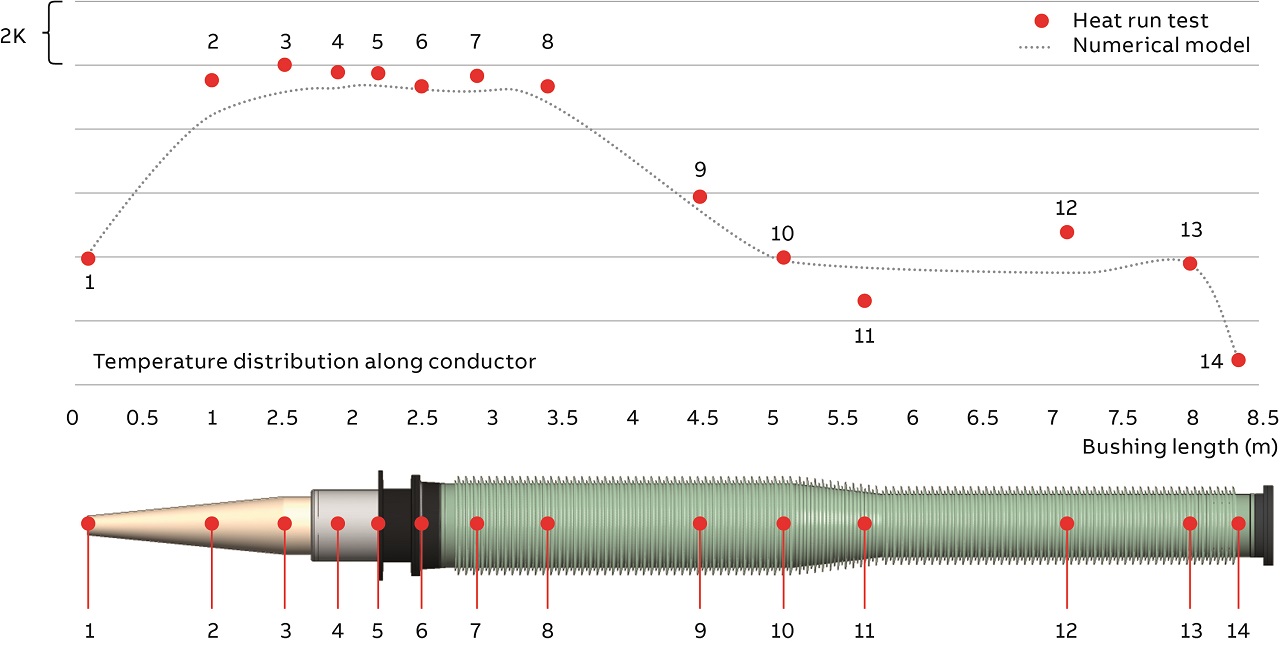
Multiphysical simulations
A simulation must digitally mirror phenomena occurring within a physical object or system. As in the real world, multiple physical effects act on an object simultaneously. For example - looking at an installation purely from the electrical point of view – it is relatively straightforward to determine an optimal cable cross-section. But taking into account other phenomena, such as thermal effects or mechanical vibrations, this optimum may need to be reconsidered. Simulations must thus reflect effects in different physical domains (electrical, mechanical, thermal).
Often, the interdependence of these effects needs to be considered. For example, simulation of an arc requires simulation of the dynamics of the plasma, as well as of its electromagnetic behavior and heat generation and cooling. These phenomena are all mutually linked as, for example, the local conductivity of the plasma influences the heat generated, and the resulting temperature feeds back into conductivity. The heat also affects the spatial movement and redistribution of the plasma which in turn affects changes in local conductivity, and so on. The chain of influence is thus highly meshed and the respective calculations of the individual domains must run concurrently and exchange information.
Before simulations were available, design decisions of this type were often based on experience, backed up by observation. Simulations enable a far more detailed understanding of what occurs within a phenomenon such as an arc than was previously possible.
Digital twins
A simulation requires, as a starting point, basic data about a device or system. With different simulations being performed on the same product, computational efficiency can be gained by relevant data being shared between simulations rather than totally separate and incompatible inputs being generated manually in every case. This data can also be used for myriad other purposes in different phases of the product’s lifecycle, including system integration, diagnostics, prediction and advanced services.
A virtual image of the physical device or system is created that simplifies the accessibility of data and verification of properties. This structured collection of data and algorithms forms the device’s digital twin.1
A digital twin can provide a unified repository serving all relevant data associated with a device. This can range from CAD information and documentation to lifetime and service history, operating hours and a wealth of other pertinent information. It can also embed simulation algorithms that can, for example, advise a system configurator or operator whether a planned operation will overload a device or take it outside a specified envelope. Allowing, for example, a temperature to rise above a critical value may shorten the device’s service interval or lifetime, but an informed operator or plant manager may choose to do so nevertheless for operational reasons. Such data can be provided with a one-click query. The usability of such a tool can be improved with augmented reality (a technician looks at objects through the camera of his or her mobile phone and the pictures are automatically annotated or overlaid with interactive information).
In addition to being available on workstations and hand-held devices, querying tools of this type can be embedded directly into the next generation of control-system interfaces so as to be constantly available without requiring any manual transfer of data.
Besides individual devices, larger processes and systems (such as for example a group of collaborating machines in a factory) can also have digital twins comprised of the individual digital twins of the components plus data on their configuration and interaction. Digital twins can also capture the interfaces between devices and thus support system configuration, testing and troubleshooting.
Tools and methods of simulation
In its simulations, ABB uses a mix of commercial, open-source and self-developed tools. The choice depends on the precise problem, and part of the skill in simulation lies in knowing how to select the best tool.
The model for simulation is prepared based on information from the design (such as CAD data). Factors such as boundary conditions, loads etc. are taken into account.
The process of preparing this data is already supported by a certain degree of automation. Such tools becoming easier to use has led to a “democratization” of simulation.
The computing power required depends on the simulation type. For example, in the electro-thermal analysis of complete medium voltage switchgear (approximately 50 million of cells in a finite volume mesh) a high-performance computer might be needed →4 (the simulation referred to runs for 24 hours on 160 cores). In case of simpler models or different applications, a good laptop is sufficient. For example, a calculation of electric field emissions around a power station (90 m x 150 m) with a mesh size (in the areas of greatest interest) of around 2 cm was completed on laptop in two hours. For network calculations, a single run can take a few seconds only while returning a result of reasonable quality.
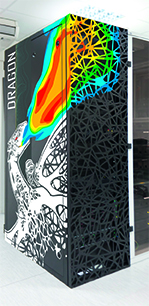
Artificial intelligence (AI) is playing an increasing role in simulations, for example in creating the models and in recognizing and interpreting phenomena. One great strength of AI lies in the optimization of data correlation. AI can, for example, recognize which parameters have the greatest effect on optimization and suggest design variants that come closer to a design optimum.
Simulations and 3D/4D printing
The simulations described so far are typically performed well ahead of or independently of manufacturing or application, and are thus not considered real-time operations. An example where simulations may have to run in real-time occurs in 3D and 4D printing (a 4D object is a 3D object that embeds additional functionality). A simulation running concurrently to printing can be used to correct parameters during printing. For example, temporary temperature gradients caused by the printing process can be compensated.
Finding the optimum
Simulation is about much more than replacing laboratory tests or speeding up product development. Because it is so much easier to run a simulation than set up a test, it is possible to run a far larger number of simulations and thus explore a broader range of variants, including out-of-the-box thinking and “what if” ideas. By not artificially limiting simulation users to a given solution from the beginning, simulation is opening new avenues, not only in product design, but in manufacturing processes, business decisions, testing and verification, as well as service. Staff can play with different geometries and ideas and refine parameters in multiple iterations. Simulation removes barriers to creativity.
This issue of ABB Review presents selected examples of simulation from across the ABB Group.
Footnote
1) See also “Digital twin – virtually identical?” in ABB Review 2/2018, pages 94–95.