Marius Rutkevičius and Julia Viertel
Low friction coatings with good substrate adhesion are difficult to formulate, especially at low cost. ABB undertook a project beginning in 2017 to explore a novel inexpensive lubricating coating using polytetrafluoroethylene-polydopamine (PTFE-PDA). The coating was developed by Surftec, a startup affiliated with the University of Arkansas Technology Development Foundation and led by CEO and U of A PhD Samuel Beckford and CTO and U of A professor of mechanical engineering Min Zou.
Surftec’s material was inspired by ocean mussels, whose legendary ability to stick to rocks comes from the animals’ secretion of polydopamine. ABB and Surftec together are exploring the potential to use PDA with PTFE in journal bearing liners to improve the wear resistance of PTFE surfaces. Journal bearings are simple devices used to reduce friction between moving parts in machinery. PTFE is used as a low friction coating in a wide range of applications, so a more durable formula would yield substantial benefits.
Solid lubricants traditionally are more difficult to apply and can be more expensive compared to oils and greases, but they reduce complexity in assembly, are easier to maintain and deliver very low friction. In work on flat substrates carried out in 2017 and 2018, the new coating showed low friction and good lifetime (see figure 1). The wear and friction properties were tested with a pin-on-disk tribometer with sliding contact of varying speed and 100Cr6 steel as counterpart.
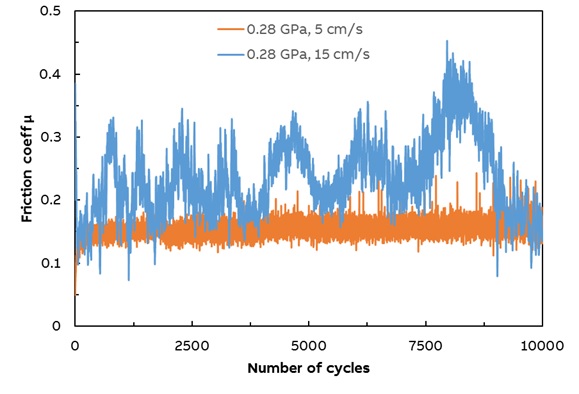
This analysis of flat substrates revealed that the Surftec coating does not lose its performance during the 10,000 cycles of analysis at a contact pressure of 0.28 GPa. Images of the sample after testing shown in Figure 2 show no peeling or flaking. Instead, the coating shows only some smearing in the wear track. Smearing is also typical for journal bearing liners, which are coated with a tin-based substance called Babbitt.
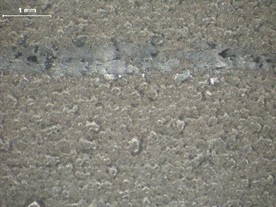
ABB’s investigation will yield greater understanding of the benefits that the coating can offer to journal bearings, before work moves on to a similar analysis using sleeve oil bearings in the next phase of the project. Evaluations are being carried out at ABB’s Greenville, SC testing laboratory using the bearing testing rig shown in Figure 3.
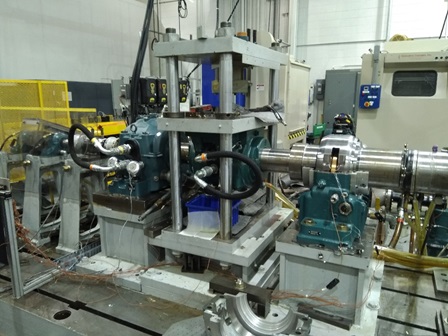
The results will be compared to the existing products. According to Surftec’s CEO Beckford, the new coating could reduce friction by 10% and extend the life of mechanical parts by 40%.