Background
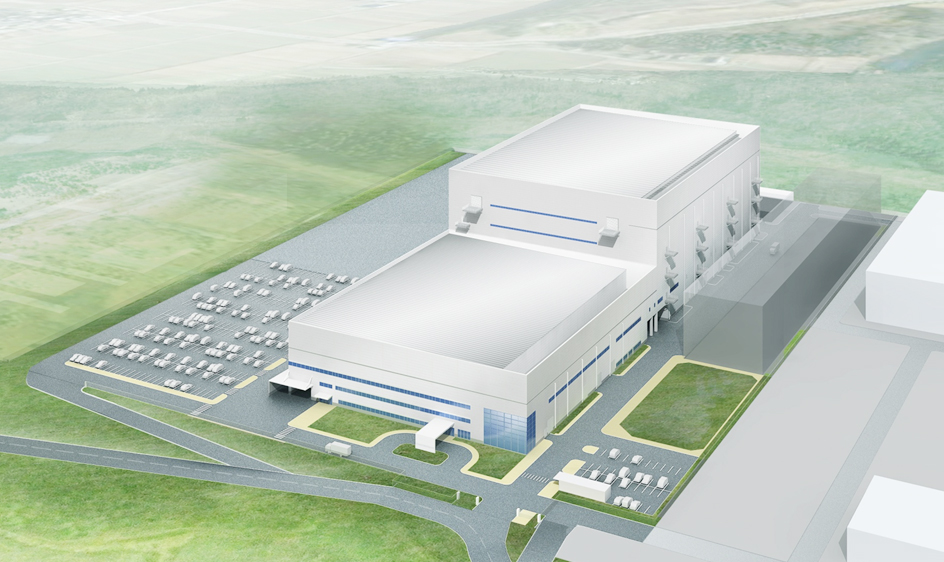
Toshiba Mobile Display (TMD) is a fully owned subsidiary of Toshiba Co., Ltd, and is one of the leading manufacturers of middle to small sized thin-film transistor liquid crystal modules. It also deals with sales, R&D, and manufacturing of low-temperature polysilicon, thin-film transistor liquid crystal display and amorphous silicon. Its products are renowned for the affinity to touch screen function. | An impression of TMD's new factory in Japan |
Toshiba Mobile Display (TMD) is a fully owned subsidiary of Toshiba Co., Ltd, and is one of the leading manufacturers of middle to small sized thin-film transistor liquid crystal modules. It also deals with sales, R&D, and manufacturing of low-temperature polysilicon, thin-film transistor liquid crystal display and amorphous silicon. Its products are renowned for the affinity to touch screen function. |
One of TMD's key challenges in constructing the new factory was how to manage the voltage sags. A voltage sag can potentially cause a day of checking and recovering production lines and product quality, at the cost of millions of yen of lost production depending on the scale. TMD had found in other factories that voltage sags were mainly caused by extreme weather, such as thunderstorms. To prevent this, TDM had been predicting thunderstorms and temporarily were stopping their production lines to avoid the effect of voltage sags. However, this practice meant there was a potential of increased electricity costs with the use of the co-generator system to back-up the power supply. The strategy then, was to mitigate voltage sags by implementing ABB's technology.
ABB's solution
TMD analyzed all the data for lost time and the reason for the past voltage sags in its main power equipment, for connection units, and for other existing factories in Ishikawa. TMD chose ABB's PCS100 AVC (Active Voltage Conditioner) and PCS100 UPS-I due to the proven market and cost performance in power quality and protection. The PCS100 AVC is a battery free solution leading to less maintenance costs, which poses as one of its advantages, along with sag and swell protection and continuous voltage regulation. The PCS100 UPS-I is tailored towards the demands of industrial applications such as motors, drives, transformers and tools. It also provides protection during deep sag and swell, plus outages between seconds and minutes depending on storage (super capacitors or batteries) and system loading. The solution chosen for this project was, two 480 V AVCs protecting down to 40% sags and one UPS-I battery system rated to supply 500 kVA at 208 V/3 phase for five minutes.
Mr. Shinji Kubomae, TMD's Specialist Production Engineering Group 2, Process and Manufacturing Engineering Dept. states, "Since PCS100 AVC was introduced, we were able to be flexible in deciding whether or not to have full back up to the protected load. As a result, we achieved significant cost cut, as well as space saving and energy efficiency. "
In addition, TMD experienced other benefits from working with ABB, including the achievement of a tight timescale for an intensive installation process that was required to be in place prior to the start of winter, in order to test the full extremities of environmental forces.
Mr. Yoshiyuki Iida, TMD's Group Manager, Manufacturing Group, New Clean room Promotion Dept. comments, "We appreciate ABB's efficient installation operation with professionalism and dedication of staff members demonstrated in the project. "
Since the installation, both products have performed to a high standard and full operation is expected for the factory by spring 2012. In the future, TDM predicts ABB will provide them with power protection technology as highlighted by Mr. Yoshiyuki Iida, "We are also looking forward to communicating with your team to exchange technical information on your wide range of portfolio."