ABB India to support the increasing digitalization of Delhi’s energy distribution network
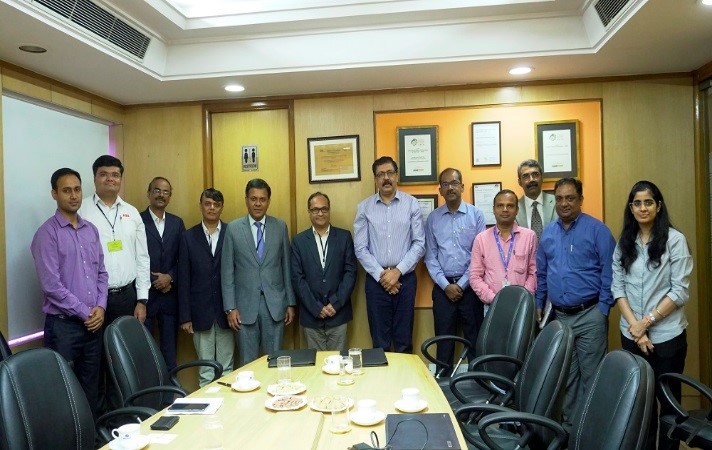
ABB India Ltd. signed an MoU with Tata Power Delhi Distribution Limited for centralized protection and control of medium voltage electric substation
Tata Power Delhi Distribution Limited (Tata Power-DDL), a joint venture between Tata Power and the Government of National Capital Territory (NCT) of Delhi distribute electricity in North and North-West parts of Delhi and serve a populace of over seven million with a registered consumer base of approx. 1.64 million.
Tata Power DDL was looking to improve the network, focusing on safety, reliability and flexibility for future needs and chose to pilot ABB’s smart substation control and protection device. To meet complex protection requirements arising due to addition of renewables and distributed generation and get benefitted from the latest developments in technology, Tata Power-DDL and ABB India Ltd signed a Memorandum of Understanding (MoU) for the pilot project of SSC600- ABB’s smart substation control and protection solution.
For detailed news please visit here
Marketing Automation-For Strategic sales and lead generation.
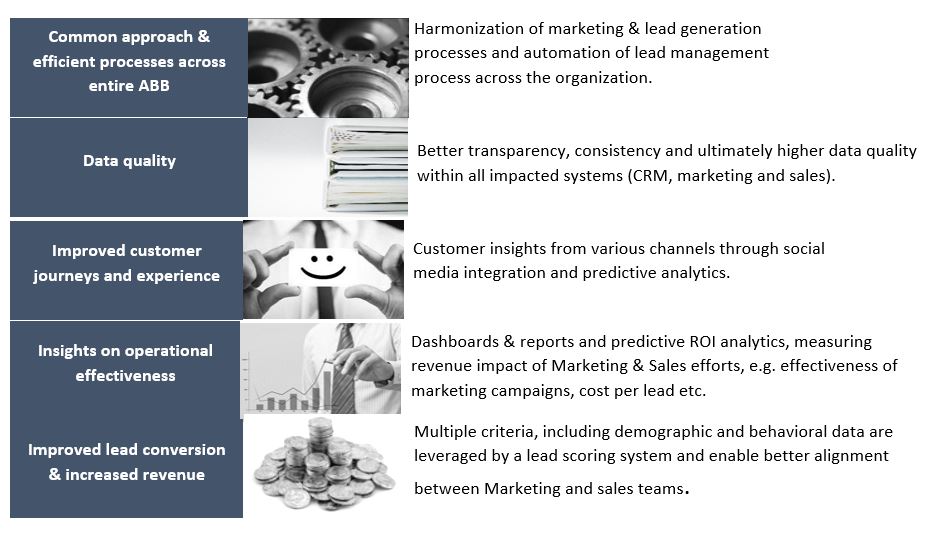
Smart Factory – A transformation journey.
Industry 4.0 is an overarching term for the most recent phase of industrial advancement, which integrates cyber-physical systems and the Internet of Things into production line manufacturing. In line with a similar view, the digital team was formed at IN ELDS with a vision to “Bring the speed and transparency in the entire value chain by the end to end integration and thereby improving the efficacy and response to stakeholders by providing the real-time actionable information.”
Accordingly formulated a roadmap of Supplier – Factory – Customer integration.
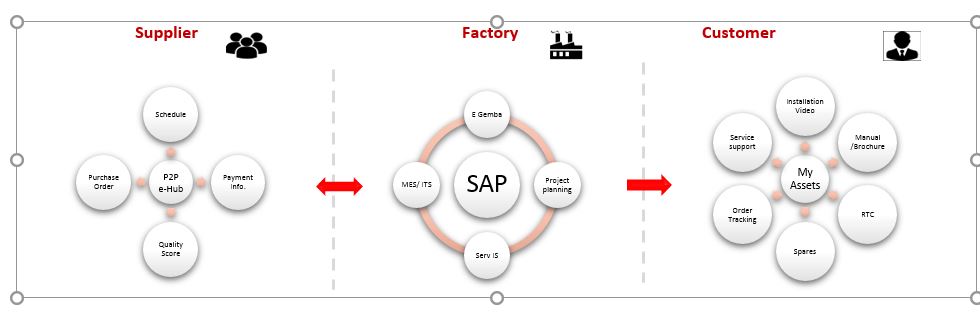
Supplier Factory Customer
The key digital concepts of this drive were Data (D), Connectivity (C) and Analytics (A).
- Data – Information in digital form
- Connectivity- Data exchanged between man and machine
- Analytics- Systematic analysis of data for better and quick decisions.
As a pilot run, the Outdoor product factory was taken into consideration. Following methodology was adopted by the team to achieve the vision:
- Interviewed several stake holders, to grab their expectation and then map the dots to provide a seamless flow of information.
- Mapping of existing tools across value chain followed by the reviewing of Global tools, to ensure the alignment with Global strategy.
- Identified opportunities for enhancement of exiting tools, for their effective utilization.
- Training from internal and external experts.
- Explored innovative ways to reduce Non Value-added Activities and to promote Paperless transactions
- Spotted new enablers for smart factory
- Identified tools for integration for end to end connectivity.
Accordingly, several initiatives were taken by the team. Following are the glimpse of it.
- eGallery: Display of factory information, layout, Product gallery and relevant manufacturing information in interactive and digital form.
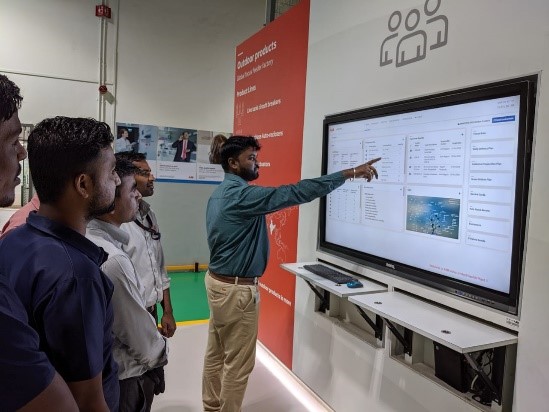
- eGemba : Daily operations planning through a web-based tool, which improves the overall efficiency and effectiveness of the Gemba meeting. Reduces nonvalue added activities like record keeping sending MOM, etc.
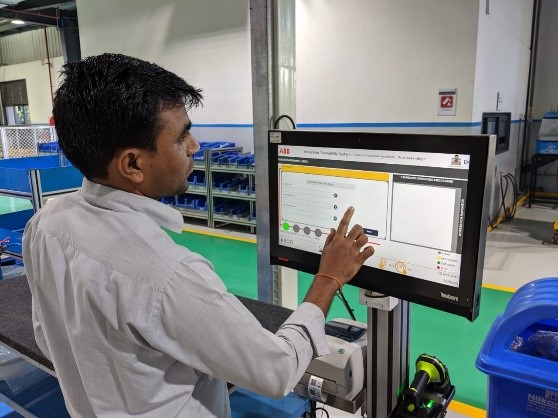
- ITS System: Integrated traceability system ensure traceability of critical component and processes also ensures Poka-yoke to reduce customer complaints. This system acts as an operator assisting tool with interactive touch screen displays to provide SOP, product specifications, PPE and other important information.
- My Asset: Customer-centric mobile application to provide service assistance and documentation in the easiest way.
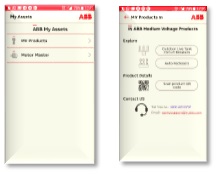
The above initiatives accelerated the smart factory journey of Outdoor products. The factory was thus equipped with lots of recent advance technologies. State of the art onsite digital screens provide information transparency across the factory and its products, for key parameters that can be adjusted to increase the efficiency of operators. Mobile applications thus developed would help customers to access information about products specifications, installation support, factory test results, etc. just by scanning the QR code on the product.
These developments took place over the strong backbone of the ABB Ability™ team. The factory provides the best example for connectivity, where all the machines send real-time data which is connected through a web-based integrated traceability system which can then plan and analyze the system effectively. Horizontal deployment of these initiatives of the Outdoor Products factory is planned to have harmony across the Distribution Solution factories.