For businesses in Africa, the Fourth Industrial Revolution is a tremendous opportunity to raise their competitiveness globally and to play a more important, decisive role in shaping the future of this country. In the Fourth Industrial Revolution, productivity and performance depend increasingly on intelligence. If you know in advance when a machine or a robot is going to break down, you can intervene pre-emptively to avert a disruption in your supply chain, saving huge amounts of money and keeping your customers happy. Increasingly, ABB’s business is centred on providing this kind of actionable intelligence to its customers. More than 5,000 ABB industrial robots worldwide are cloud connected, permitting remote monitoring and preventive maintenance, based on operating models that have been honed over time.
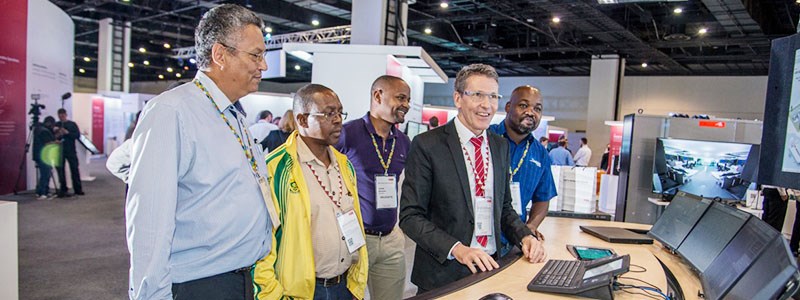
The mining industry currently faces a unique set of challenges. The solution to these, and the future of mining, lies in automation and integration. In addition to the productivity shift, the industry is also being driven by a plethora of challenges including, but not limited to:
- Improving safety
- Managing capital projects
- Maximizing productivity
- Ensuring equipment operates reliably and predictably
- Encouraging collaboration between different departments
Competitive pressure is driving mining industry to find ways to optimize operations and reduce the cost per ton. People and asset productivity have to rise too as flat commodity prices, rising production costs and high price volatility are currently forcing the industry to reduce capital expenditure. Indeed, the productivity improvement is now fast becoming a key competitive differentiator and being integrated in to financial projection models.
Added to all this is an aging workforce. In common with other industries, the age profile in mining is slowly creeping up and retiring workers are leaving with valuable know-how and experience. The situation is exacerbated by the remote and inhospitable location of many mines, which makes it difficult to bring in experts and recruit and retain competent staff.
The solution to all these challenges, and the future of mining, lies in automation and integration of information and the use of that knowledge for real-time optimization of the mining processes. Automation is not new to mining, but the automation employed in mines is generally more basic than in other industries and is often limited to simple control of motors, equipment or certain parts of processes.
Further, mines tend to have a large number of independent pieces of equipment and systems from different suppliers. Each of these “islands of automation” can have its own data, data format and interfaces, and operators and control room staff must scrutinize a multitude of conceptually disconnected screens in order to coordinate different parts of the process.
The key to the future of mining, then, lies in total integration of data and work processes.
- To improve its competitiveness, profitability and sustainability the sector needs to focus along the value chain: Intelligent production for better people and asset productivity
- Improved response to critical asset condition in real time
- Demand-driven planning improving profitability
- Reduced energy consumption and waste
- Safer mine operations of assets and people
Some examples of how ABB’s technology and expertise in the field, is becoming a game changer:
- Boliden's Aitik Mine, (Swedish mining company), the world's most productive opencast copper mine, suffered a leak and flooding. The pumps that pump the water were suddenly themselves submerged. The mine risked being idle for several weeks. As Boliden has a service agreement with ABB, service engineers were on site very quickly and worked round the clock. As soon as the water was drained off, they started work loading the motors for shipment down to Luleå and then install the back-up motor. Even though the works could not be operated with just one motor, when it was started it would enable Boliden to gain access to the important fire prevention and rinsing water. Just over 72 hours after the original alarm, and 48 hours ahead of the most optimistic forecast – Boliden Aitik was back on full power. Had Boliden and ABB not had such a close partnership – not least geographically – it would have taken far longer.
- ABB received an order from Vale in Mozambique for complete electrification and automation solutions to maximize productivity, monitor energy use and minimize energy consumption at a new coal mine. The new mine is one of Vale’s major investments in Africa and will be built at Moatize, in the Tete province of Mozambique.
- ABB will provide four hoists to the Venetia Mine, South Africa’s largest producer of diamonds. ABB will supply one double drum hoist for personnel and material conveyance, two friction hoists for production, and one single drum hoist for service duty. ABB will provide the design, supply, manufacture, installation and commissioning of all four hoists, including hoist mechanicals, motors, and electrical drive and control, all certified to the highest safety integrity levels (SIL). This is the first time that multiple, turnkey large friction mine hoists are delivered to the South African mining industry. The installation will commence in July 2018. All four hoists are due to become operational in April 2020.
By embracing technologies of the 4th industrial revolution, the mining sector stands to gain in terms of improved efficiency across the entire value chain. Africa’s potential is infinite, and together with partners like ABB, can become a global player having adopted technologies that give them the business edge.