For industrial operations power problems can lead to millions of dollars of unnecessary costs and --much worse-- dangerous health situations.
In our homes, electrical power interruptions are annoying, but they rarely cause financial losses. For industrial operations, however, power problems can lead to millions of dollars of unnecessary costs and --much worse-- dangerous health situations. These potential consequences are especially troubling for the food and beverage industry.
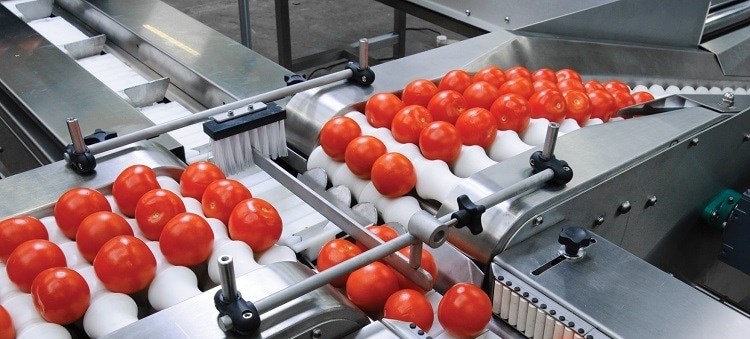
Modern food and beverage manufacturers rely heavily on technology and high-speed continuous pro-cesses to reduce production time and the cost of bringing goods to market. Technology-based systems improve quality and flexibility while reducing variability.
Power-supply disturbances can interrupt the operations of the precision machinery used in food and beverage production, resulting in lost material, loss of certain production units, non-delivery and hours spent clearing and cleaning equipment to restart. Even a momentary interruption in a process may cause contamination issues, which can be an expensive problem to solve. Unscheduled process interruptions can produce long delays as the process may have to be restarted.
In the dairy industry for example, any unexpected downtime can cause spoilage resulting in the dumping of valuable milk products. Lost production time, while more milk is sourced and sterilized can cost many hours and many thousands of dollars.
Instantaneous prevention of power interruptions
Fortunately, the latest power technology can prevent these interruptions from happening. Installed between the incoming supply and equipment loads, the ABB PCS100 active voltage conditioner (AVC) senses power disturbances, such as a voltage sag from a weather event, and acts extremely quickly to correct the event before it can have any effect on critical machinery.
The PCS100 AVC constantly monitors the voltage supply and immediately corrects any impending issu-es. When a voltage anomaly is detected, the system instantaneously corrects the voltage, up or down, to the nominal level by means of a built-in injection transformer and rectifier/inverter pairs.
The PCS 100AVC draws additional energy from the utility to make up the correction voltage at sub-cycle speed, relying on ABB’s leading-edge power electronics. Only one moving part—a cooling fan—is involved, and no batteries are required. The PCS100 AVC’s footprint is extremely small, so it installs easily in equipment rooms and confined spaces.
Throughout the food and beverage industry, processes that rely on continuity of operation can benefit from the PCS100 AVC system. It can save dollars, time and lives in such operations as baking, where the risk of fire exists if a loaded conveyor stops in an oven, or when gas-fired ovens and boilers do not au-tomatically reignite. Packaging products, like glass and foil, have continuous processes that can cause long and expensive delays when disrupted. These operations can benefit from PCS100 AVC protection, as well.
Financial losses from poor power quality can reach around 4 percent of a company’s turnover, according to a Pan-European Power Quality Survey. Moreover, an unstable or fluctuating electricity supply can cause problems beyond unexpected interruptions. Here are some examples of problems that can be avoided by installing PCS100 AVC protection:
- Failure of such components as contactors, release switches and fuses
- Unexplained breakdowns, faults or malfunctions of machinery
- Overheating of transformers and motors, reducing their useful life
- Damage to computers, PLCs, sensors and other precision equipment
- Communication interference in electronic sensors and devices
- Higher distribution system lossesLight flickering
ABB is the global leader in voltage sag and surge protection, with proven technology operating success-fully with heavy industrial load profiles in the world’s worst supply networks. We are dedicated to delivering advanced, reliable solutions that will provide a stable, high-quality power supply for many years.
For further information on this topic read the full interview where Bruce Bennett talks to AZoM about why power protection is hugely important to the food and beverage industry.
Author; Bruce Bennett bruce.bennett@nz.abb.com
Bruce is the Global Channel Manager for ABB Power Conditioning Products based at the Centre of Excellence in Napier, New Zealand. He is a qualified electrician, has a Massey University MBA and has over 25 years’ experience in the industrial electrical industry. His professional history includes establishing his own international distribution business, General Manager for a global helmet manufacturer, and Business Development roles with Danfoss drives and Electrical Process Development Ltd.