Christopher Ganz, Group Service R&D Manager Zurich, Switzerland
The fourth installment of ABB Review’s Buzzword Demystifier explores the meaning of the term, “digital twin.”
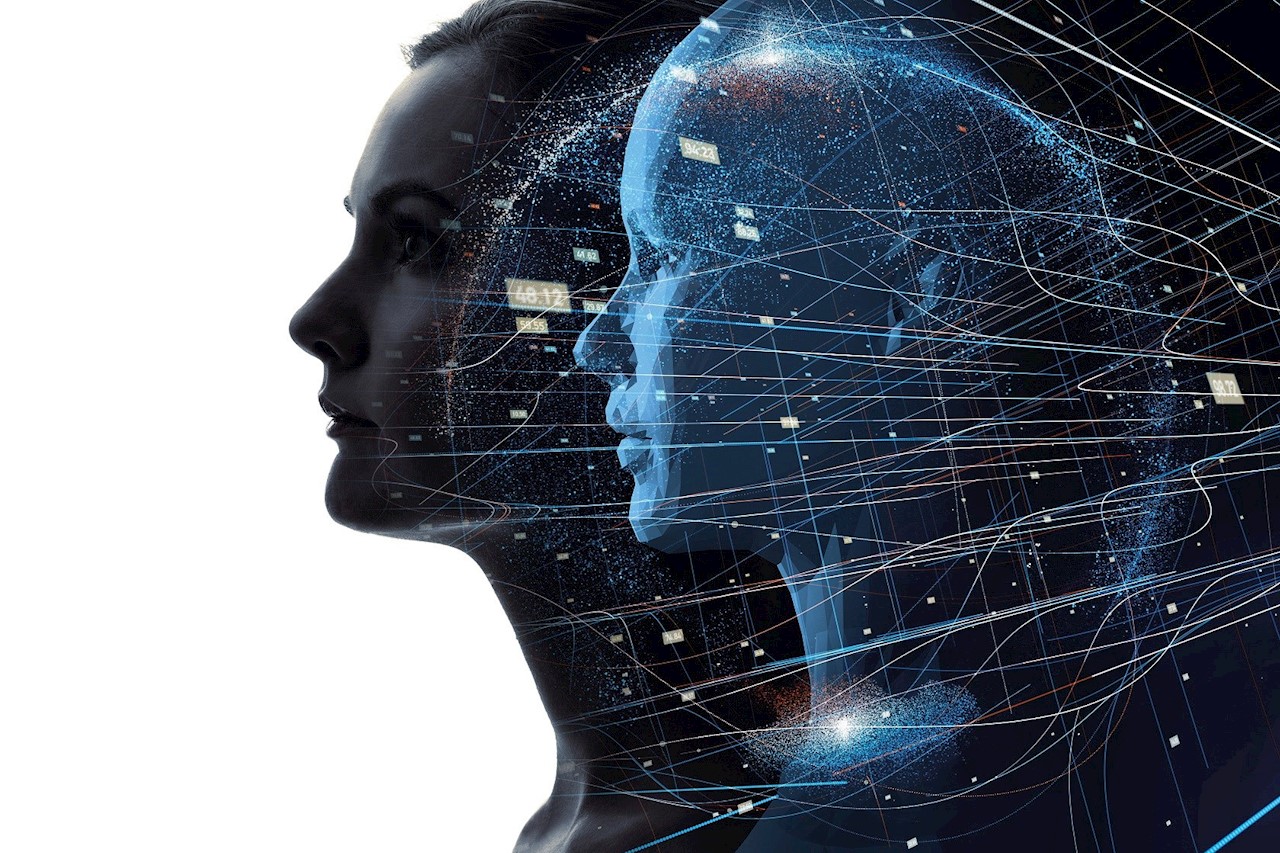
A typical modern industrial device already creates a formidable digital data-trail. This includes CAD drawings and simulations during the design phase, information on location, connected equipment and configuration from the integration phase, as well as subsequently collected utilization, diagnostic and maintenance data. In addition to such definable, measurable or observable data, algorithms can calculate or simulate non-observable parameters, both actual and predicted.
These data and algorithms typically already exist in various locations or formats. If they could be accessed from one virtual directory – the digital twin – this would provide a comprehensive digital image of the physical equipment. More than being just a static description, this information can be used to simulate the behavior of the physical object. 3-D visualization tools also allow virtual inspection and observation of the equipment and enhance understanding and insight.
Applications of a digital twin include:
Design: Simulation and visualization during the design phase can be used to verify and inspect the overall 3-D design and make sure all parts fit together. Simulations include mechanical, thermal and electrical as well as interrelationships between these aspects.
System integration: 3-D visualizations on a system level can verify constraints such as spatial foot- print and physical connections. By connecting to the digital twins of other components, interactions can be simulated, including data transfer and control functionality as well as mechanical and electrical behavior and what-if scenarios. Integration effort on site and the associated downtime for the customer is reduced.
Diagnostics: Observation of the digital twin, for example in a 3-D visualization, can support trouble- shooting. Virtual-reality glasses can provide field technicians with an overlay over the real equipment to visualize parameters. Simulations can add non-observable data, such as temperatures of non-accessible parts or material stress.
Prediction: Past and present operational and sensor data in combination with predictive algorithms provide insights into the condition of equipment and the likelihood of different failure modes. This helps plan rational maintenance and reduce unplanned downtime.
Advanced services: If all the advanced service parameters (IoT connectivity, analytics algorithms, etc) are preconfigured in the digital twin, they can be enabled when the equipment is installed and the customer subscribes to these services. In the optimal case, no further engineering is required.
The key to these diverse aspects of a digital twin is the capability to refer to data stored in different places from one common digital twin directory. The digital twin is capable of providing the data required for the different use cases by accessing data from elsewhere in the product lifecycle.
In summary, a digital twin is a complete and operational virtual representation of an asset, subsystem or system, combining digital aspects of how the equipment is built (PLM data, design models, manufacturing data) with real-time aspects of how it is operated and maintained.
The digital twin allows the consistent collection and distribution of information across the physical asset’s complete lifecycle to maximize business outcomes, optimize operations and investment (for both customer and ABB) through data processing (eg, simulation, advanced analytics).