MyRemoteCare, part of the ABB AbilityTM digital offering, collects data from the field to enable service engineers and operations teams to continuously monitor the performance trends of remote assets and define the correct, timely maintenance procedures to allow predictive rather than time-base maintenance.
ABB Ability™ brings together ABB digital devices, equipment and solutions and digital-enabling services to deliver a quantum leap in industrial digitalization.
ABB service engineers perform asset analysis by exchanging information with site operators on a virtual whiteboard, an instant messaging tool where questions, answers and comments are exchanged. This allows both sides to look at the real-time condition of the equipment.
The product collects diagnostic information from dedicated intelligent electronic devices that provide specific sensors for health condition monitoring. It optimizes maintenance schedules, increases uptime and safety, and reduces operational costs for electrical equipment.
This new version of MyRemoteCare includes a new remote condition monitoring system and MySiteCare 5.2, a circuit breaker and switchgear diagnostic unit.
"We can connect ABB experts from anywhere in the world to our customers in the field in remote locations or to oversee the electrical system for a pump in a desert or for equipment at the bottom of a mine," said Bruno Melles, managing director of ABB's Medium Voltage business.
"ABB Ability™, our solutions platform for all of our digital products and services, connects our customers to the power of the industrial internet of things to help turn data insights into the direct action that 'closes the loop' and generates customer value in the physical world."
MyRemoteCare enables savings in operations as maintenance work can be optimized by moving from time-based to predictive maintenance strategies. Studies have shown that up to 25 percent of operational budgets can be used more effectively. Liabilities can be lowered as the available failure prediction function means avoiding unscheduled downtime and loss of production. Asset lifetime can be extended by 10 to 50 percent due to better health condition traceability and focused maintenance. MyRemoteCare can be utilized in any customer segment with medium-voltage power distribution.
MyRemoteCare
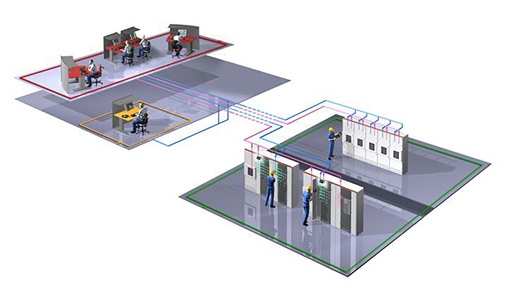
This edition of MyRemoteCare introduces new software functionalities and enhancements, such as the HTML 5 web portal. The benefits of HTML 5 make MyRemoteCare 2.2 easier and friendlier to use now that the product can be accessed through mobile devices like smartphones, tablets and laptops, saving valuable man hours, which itself translates into significant cost savings for the customer.
MySiteCare
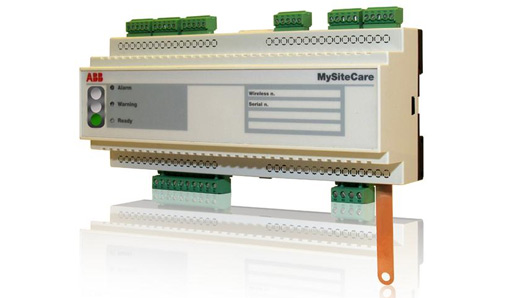
The monitoring feature of MySiteCare 5.2, which was previously focusing on the circuit-breaker, now also includes an effective algorithm that detects temperature hot spots in switchgear and signals an alert to the operator. Specifically, the system monitors the temperature of the primary circuit or near the critical points of the current path and joints. Such hot spots can dramatically increase the probability of failure within the switchgear, which means this new functionality has a significant impact on the effectiveness and life expectancy of the switchgear. New and existing UniGear type ZS1 panels can be equipped with the hot spot temperature monitoring kit either at the factory or at the customer's site, whichever suits their needs. Kits for different types of switchgear are available for retrofits. The added monitoring of contactors - which can now be implemented for both low- and medium-voltage contactors - also improves the predictability and analysis of the overall health condition of the equipment.
The new release of MySiteCare has added features for spring charging gear motor current analysis, which previously included charging time, slipping and failed spring charging attempts. In the new release, a current sensor clamped onto the motor feeding cable measures the absorbed current during its operation, carrying out a frequency spectrum analysis of the waveform in order to detect mechanical and/or electrical wear and tear. Thanks to these added sensors and a specially designed algorithm, the accuracy of the diagnostic information received is significantly increased, which improves the operator's ability to assess the conditions of the system and allows maintenance work to be planned more precisely.