The Halifax Herald Ltd. in Nova Scotia is the largest independently owned newspaper publisher in Canada. The publisher has just the one press at its print site just outside Halifax. With no backup press, the commissioning of the new systems had to be undertaken without interrupting the normal daily production.
The Herald’s Wifag OF370 printing press at their print center just outside Halifax consists of two 4/1 printing towers, one 2/2 printing unit and one 4/4 tower, a double folder, and five reelstands. The project to upgrade the press was divided into three phases. ABB reported previously about the successful completion of the first phase – the commissioning of the controls on the printing units and folder, the control consoles and the production management systems. The remaining phases, i.e. the replacement of all the press drives and then the controls and drives of the reelstands, have now been completed too.
The drives retrofit phase involved the replacement of all major drive components on the press, including those for the printing units, folders and the draw rollers. In order to ensure that the production work at the Halifax Herald was not hindered in any way, the new drives and motion control had to be commissioned in parallel with the existing systems. The new drives were initially installed in temporary cabinets, which made it possible for the ABB commissioning team to switch easily and quickly between the old and new systems. This was essential to take advantages of the short periods when the press was not in production, typically between about 3am and 10am on weekdays with a larger window at the weekends.
Matthias Bilgerig, Automation Team Leader at ABB Printing in Switzerland, explains “much of the effort and even more of the complexity of a project like this lie in the transitional phase where old and new systems need to run together with high precision. That is a challenge for us engineers, but is essential if the press is to stay in production on a daily basis”.
The final phase consisted of the replacement of the controls and drives on the five reelstands. The Halifax Herald can print all its normal products with just four reelstands, so one reelstand at a time could be taken out of service for the retrofit. The plan foresaw a shutdown time of two weeks per reelstand for all the installation, commissioning and testing work. By the fifth reelstand the ABB crew had cut this down to three days.
Mike Murtha, Director Production and Facilities at the Halifax Herald, is full of praise for the ABB solutions. “The replacement of the original EAE controls with the ABB systems has given us a lot of extra flexibility. We can now use our double folder for two independent productions, which was previously not possible. We have also eliminated single points of failure and now have a control system for which spare parts will be available for at least the next 10 years”, says Murtha. “Now, with the completion of the drives and reelstand retrofits, we have modern, reliable, state-of-the-art systems everywhere on the press. That is a great reassurance for us all at the Halifax Herald.”
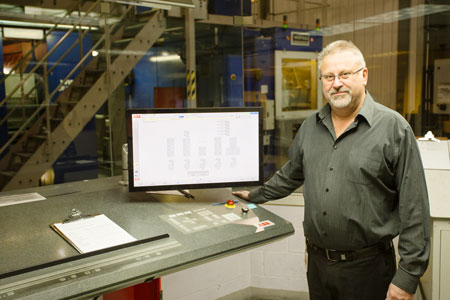
“Projects like this are always a challenge for everyone involved”, continues Murtha. “We had to make sure that our daily production could carry on without hindrance and the ABB team did a great job to ensure this. Their ingenious solutions during the transition phases were only part of the story. They worked with us as real partners to guarantee the success of the project.
”One of the other contributing factors to the success of the project was the excellent cooperation between the ABB Printing team in Switzerland and ABB in Canada. “One of the advantages of being in a global organization like ABB is that we have very capable teams locally in so many countries,” says Steve Kirk, project manager for the Halifax project. “This is not only a great administrative help, but also gives us advantages in areas like the rapid supply of spare parts.”
ABB is a leading automation supplier to the newspaper industry. ABB Printing (www.abb.com/printing) delivers solutions that provide unique and totally integrated end-to-end control, protect existing investments and provide management information essential to improving profitability.
ABB (ABBN: SIX Swiss Ex) is a pioneering technology leader in electrification products, robotics and motion, industrial automation and power grids, serving customers in utilities, industry and transport & infrastructure globally. Continuing a history of innovation spanning more than 130 years, ABB today is writing the future of industrial digitalization with two clear value propositions: bringing electricity from any power plant to any plug and automating industries from natural resources to finished products. As title partner of Formula E, the fully electric international FIA motorsport class, ABB is pushing the boundaries of e-mobility to contribute to a sustainable future. ABB operates in more than 100 countries with about 135,000 employees. www.abb.com