In a highly optimized industrial process, the continuous availability of systems is extremely important. It has been calculated that the cost of an unanticipated disturbance for a Finnish industrial sector customer is an average of 15 000€ per hour if production is temporarily interrupted.
ABB’s availability stock service maintains customer-specific equipment storage that covers the replacement equipment for the customer’s main functions. The service can be used to efficiently identify possible incidents.
“We can deliver a replacement unit extremely quickly,” says Janne Sutinen of ABB’s customer services. “In practice, the response time is one hour plus the driving time from our warehouse to the customer”.
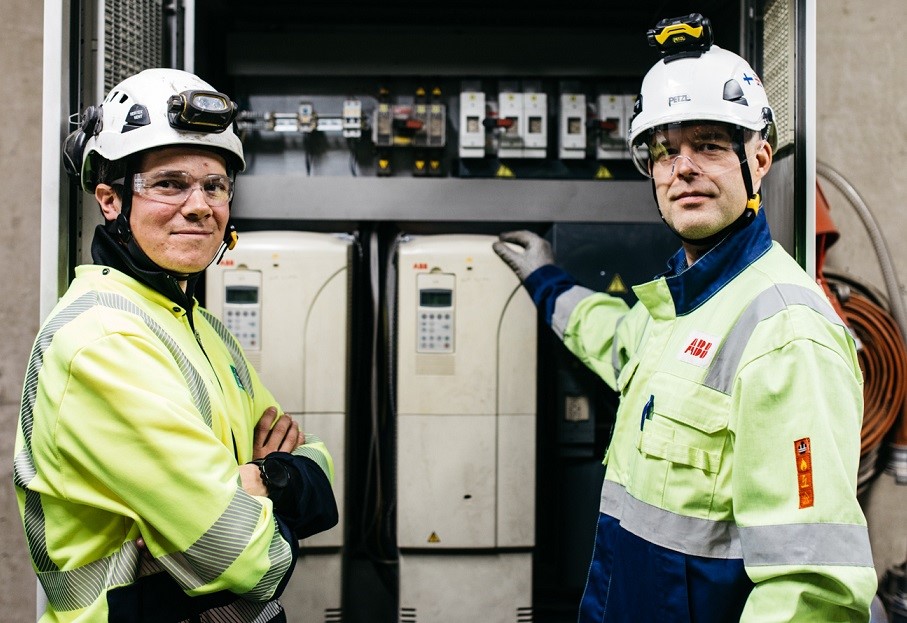
Always ready and up to date
Lassila & Tikanoja uses ABB’s drives in its crusher line at its recycling facility in Turku, where energy fractions are used to make recycled fuels for power plants and cement mills. In the line, the drives control the electric motors of various conveyers and separators.
“Work at the plant is carried out in three shifts from Sunday evening to Friday evening. The capacity of the line is in full use almost all of the time, so there is no time for long periods of downtime,” says work manager Esa Ekola of Lassila & Tikanoja.
ABB’s availability stock service reduces customers’ maintenance and storage costs by keeping a continually up-to-date equipment inventory. Drives identified as critical to the customer’s operations are always available and in good working order. ABB is also responsible for storage, which means that the customer’s facilities and resources are not tied up with warehouse maintenance. The warranty for the backup drive begins only from when they are delivered to the customer.
The warehouse has made it possible to optimize the model range of spare units used by Lassila & Tikanoja. Three different type of drives that represent the latest generation of ABB's drives are enough to back up the approximately ten drives used in the recycling plant. “The set of backup units have been planned in conjunction with the customer, and the backup plan can also be updated as needed”, explains Sutinen. “It is essential that we handle the maintenance of the reserve units on a turnkey basis on behalf of the customer”.
Flexible expansion
Lassila & Tikanoja has been using ABB’s availability stock service for its recycling facility’s drives since the end of 2018. So far, no backup units has had to be used, but Ekola is nonetheless pleased with the reliability of operations made possible by the service and the facilitation of maintenance. “We will be able to react really quickly to any possible disruptions, and with the availability stock service we do not need to maintain inventory of drives that in a few years’ time would require updating. “With ABB’s service, we always get the latest drives quickly deployed if needed.”
ABB’s availability stock service is also ideal for several production plants at the same time. “Many of our customers have one service agreement covering several sites, which may be in different locations,” says Sutinen. “The cost of the service can be also shared between several factories, and it is easy to add new locations to the service as well.”
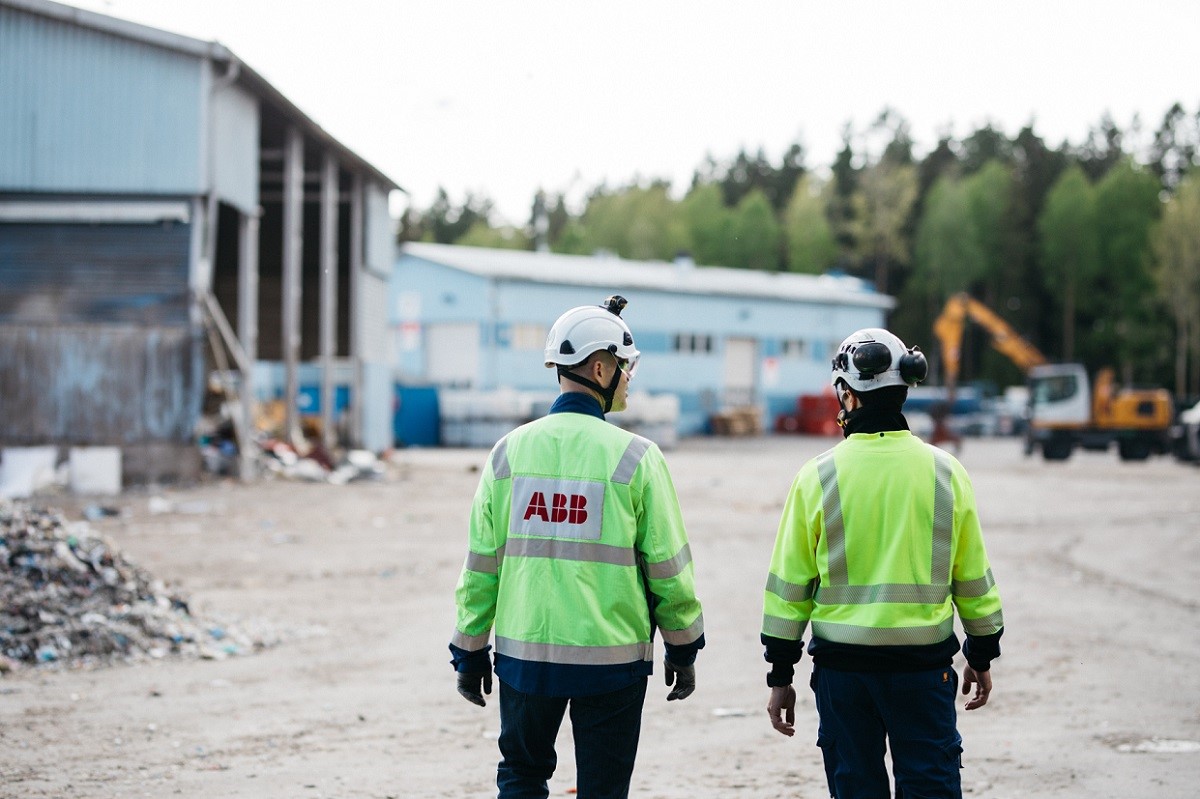