Michael D. Christensen
Vice President, Global Sales, Dry Cargo Vessels
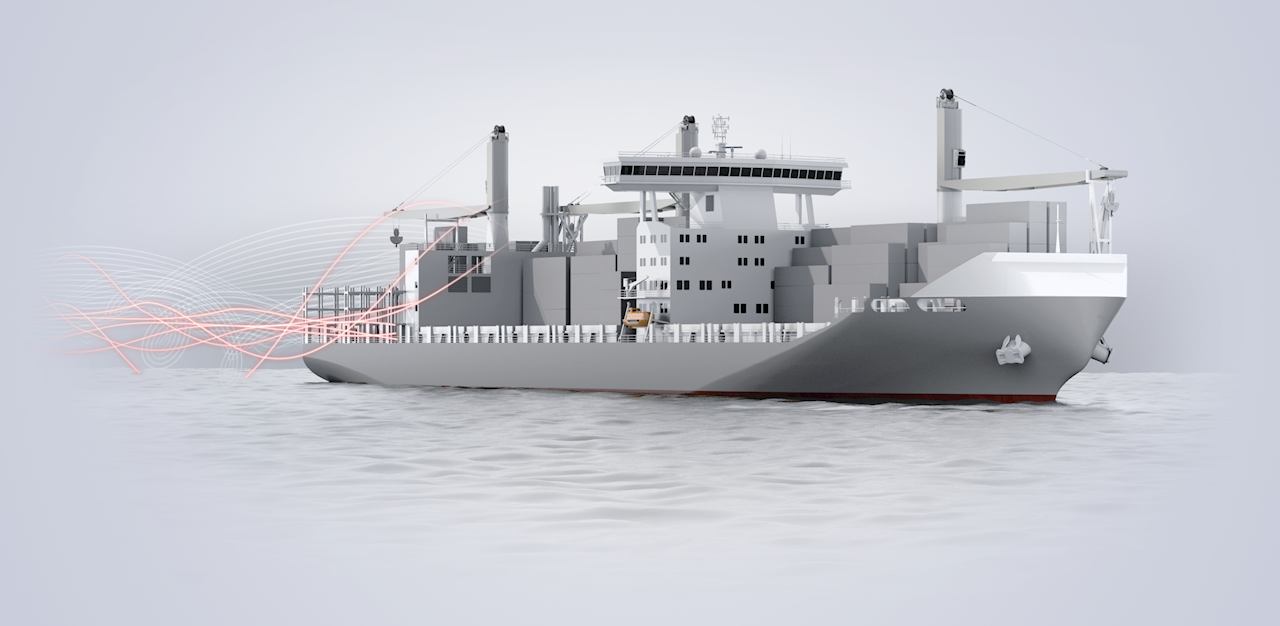
Electric, digital and connected solutions provide a direction of travel for dry cargo vessels towards greater efficiency and lower emissions using proven technology. In this, it is the ship’s electrical propulsion system that acts as the key enabler for the integrated automation and control systems that can deliver transformative operations.
In recent years, ABB has built a significant presence in the dry cargo vessel market, with an increasing number of vessels specified with electric or hybrid propulsion solutions for OPEX and CAPEX reasons, as well as for environmental impact.
Between 55-60 percent of the world shipping fleet (in gross tons) are container ships, Ro- Ro and RoPax vessels, pure car and truck carriers, bulk carriers and other dry cargo types, according to research company Clarksons. Given that these ships also consume over 50 percent of maritime fuel every year, more electric and/or hybrid propulsion solutions clearly represent a significant part of the answer to the industry’s greenhouse gas emissions challenge.
Efficient response
Based on operational needs, Germany’s largest bulk carrier company Oldendorff Carriers ordered two first ever self-unloading bulk carriers to feature ABB’s Azipod® electric propulsion. Each of these ships will include a pair of 1.9MW electric propulsion units plus diesel-electric power plant and power management from ABB. Both Azipod® propulsion and diesel-electric power management are more responsive to load variations, which will make these self-unloaders more maneuverable in shallow waters, better able to hold station and more power-efficient during frequent loading/unloading operations.
Efficiency gains are also behind the selection of electric solutions by other mainstream dry cargo shipowners, as demonstrated by ferry operator DFDS. The Danish owner is already operating the first two of six new freight ships featuring shaft generators from ABB. Used in combination with variable frequency drives, shaft generators improve fuel efficiency by optimizing the performance of main engines, auxiliary engines and propeller pitch no matter what the vessel speed. They also support vessel power during maneuvering in harbors.
Shaft generators are not new, of course, but their use in the marine setting in combination with variable frequency drives and battery application enables power to be created more cheaply than what is possible using an auxiliary diesel generator set. Their use also means the number of auxiliary engines – to run reefer plant on a container ship, for example – can be minimized, bringing not only environmental and day-to-day OPEX gains, but CAPEX and maintenance savings.
Wide-ranging power
Recent years have also seen ship efficiency gains enabled by DC-based or DC-linked distributed networks which improve power management by allowing systems to draw on a variety of energy sources on a single line-up, including shaft generators, batteries or even fuel cells. The power and energy management system and variable frequency drive is integral in any such solution and therefore offers dry cargo operators a further and decisive signpost towards hybrid-electric solutions in order to move to their 2050 obligations.
Within distributed networks, ABB believes battery power as a source of spinning reserve, peak load shaving or providing hotel load will become an accepted fuel efficiency optimization technology aboard mainstream dry cargo vessels. Following the adoption of the International Maritime Organization’s 2020 sulphur cap regulation, even advocates of heavy fuel oil might agree that the exhaust gas scrubber is the sort of power-hungry device that would also benefit from peak load shaving.
ABB is working with a range of stakeholders to address the hard targets for greenhouse gas emissions set out by the IMO. Supported by its experiences over the last 30 years in particular, ABB believes that intelligent electrical systems that enable optimized ship design and operation will be central, in either case.