Chau Hon Ho ABB Future Labs Baden-Dättwil, Switzerland, chau-hon.ho@ch.abb.com
What if non-living engineered complex-shaped objects could behave like living organisms; by sensing external stimuli and responding by adapting to their environment? And, what if they could revert back to their original condition once that stimulus is removed or another is activated? By changing a fundamental property such as shape, over time, without the need for electro- mechanical or computerized control systems in place, structures could self-assemble, self-adapt, and even self-repair. The implications for society and business would be revolutionary. This seemingly outlandish idea is no longer relegated to the realm of science fiction. Researchers in top institutions and laboratories worldwide are combining advances in 3D printing of complex structures with new smart responsive materials to create 4D printed structures that do just that.
With the Fourth Industrial Revolution well underway, industries that take advantage of its unprecedented possibilities will undoubtedly have an economic advantage. With this knowledge, institutions and corporations are investing in barrier-breaking technologies and 4D printing is one with radical potential.
By combining the 3D printing process, intelligent materials, mathematical modeling, and machine-learning algorithms, researchers are creating 3D objects that react to external stimuli by transforming over time, thereby adding a fourth dimension. The level of structural autonomy achieved is unprecedented.
Such technology could enable analog autonomous products or agents to evolve without the need for computerized power at the device. 4D printed components that change shape or move without engines, wires or active power sources, would behave in much the same way that biological organisms behave, autonomously →01. The future applications of such structures in the building, transportation, textiles, health-care, defense, and aerospace industries are vast.
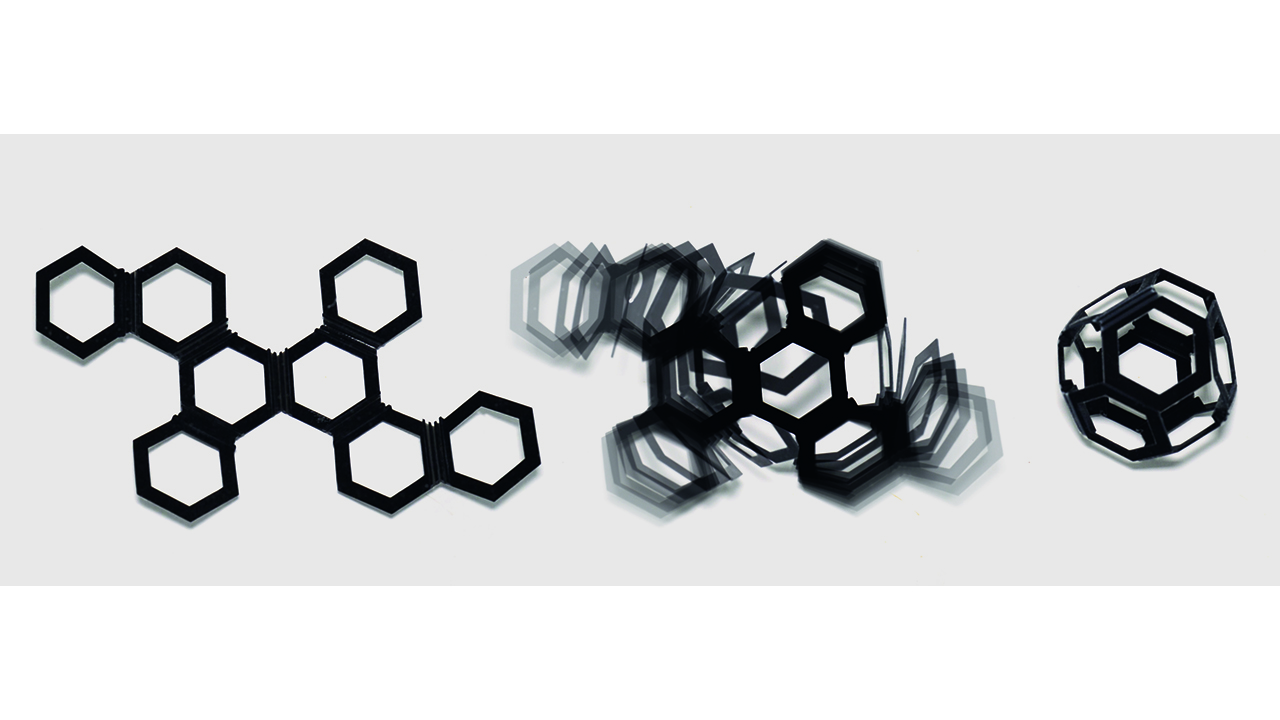
3D printing: the basics
Invented in the 1980s, additive manufacturing, or 3D printing, is unlike traditional manufacturing techniques, in which parts are cast, molded, or milled; material is deposited in successive layers to build up the desired object. Although not yet mainstream, 3D printing is widely used, eg, in robotics, biomedicine, and aerospace science, because it enables the fabrication of unique and customized 3D structures. Nowadays, mathematical modeling and machine learning algorithms are increasingly applied to boost design, material development, and to control printing. In 2019, a robot arm was 3D printed by MX3D, a Dutch company, to customize and optimize an arm of a robot supplied by ABB. A special 3D printing technique, Wire Arc Additive Manufacturing, allowed the complex organic geometries to be printed upright.
Intelligent algorithms determined the optimal printing strategy and toolpath direction for each geometric feature. Here, 3D printing applied to Generative Design Customization, saved time and cut costs by increasing productivity and reducing material waste – important for tailored robotic applications →02 [1].
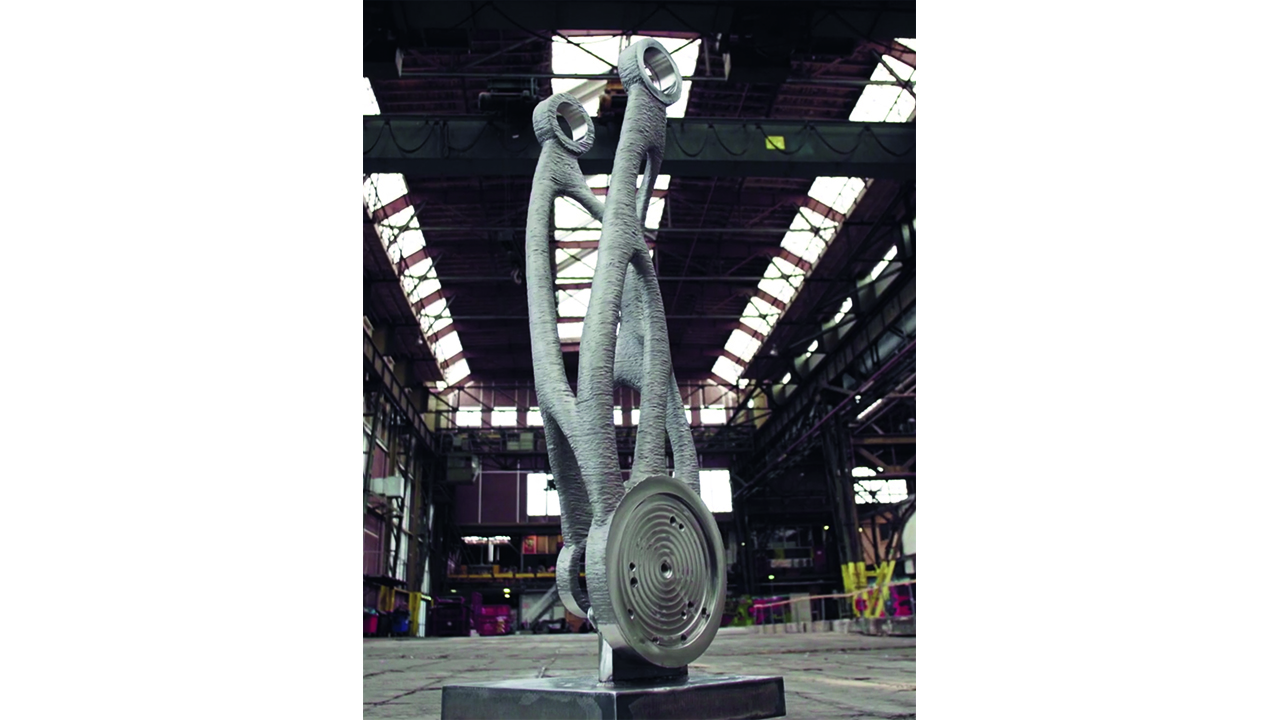
Paving the way for 4D printing
The development of smart materials – materials that contain functional or reactive components designed mathematically to respond to specific external environmental stimuli – and the availability of 3D printing set the stage for 4D printing.
Enter architect and computer scientist Skylar Tibbits who coined the term, 4D printing, in 2013. Although many labs were simultaneously exploring this combination, Tibbits and his group at Massachusetts Institute of Technology (MIT) founded the self-assembly lab in 2014. His ongoing vision focuses on three fundamental functionalities of 4D printed objects: self-assembly, self-adaptability and self-repair.
Self-assembly: If structures could autonomously assemble themselves at a specific time and place without intervention, from either human or electro-mechanical systems, then structures or even buildings could be constructed in difficult to reach or hazardous places. On a macro-scale, space antennae could self-construct in outer space; and on a nanoscale, minute objects could be transported within the human body to a target location and self-assemble for medical purposes.
Self-adaptability: 4D printed structures can also combine sensing and actuation within the printed material, thereby making electro-mechanical systems superfluous. The resultant reduction in parts, assembly time, material, and energy use would translate to lower costs. Imagine building materials that adapt autonomously to weather conditions.
Self-repair: The ability to self-assemble necessitates the ability to disassemble. This opens the door to the concept of self-healing. Imagine leaking water pipes in a war zone that can self-repair without detection and localization systems or human intervention; or medically implanted smart tissues that can self-heal, thereby reducing the need for invasive procedures.
Photos fig. 03a & 03c: Courtesy of Skylar Tibbits: Self-Assembly Lab, MIT + Stratasys + Autodesk; photo fig. 03b: Wyss Institute at Harvard University
Transformational intelligent structures
Successful 4D printing requires 3D printing, smart materials (those that react to an external environmental stimulus trigger), an external stimulus (eg, temperature, humidity, magnetic field etc.), a well-defined mechanism of interaction between the stimulus and material (eg, shape change due to water absorption), and the application of mathematical modeling to design material distribution and functionality and to predict and program movement at a later time. In this way, the desired change in shape, property, or function is achieved.
To shift shape, the smart materials must be able to bend, fold, twist, or curl, once printed, to achieve the desired structure. For instance, a 2D flat layer could become a 3D cubic form by self-folding →03a [2] or a flat 2D sheet could become a 3D flower form by self-bending or curling when submerged in water →03b [3] or a 1D wire strand could change to a 3D wire frame by self-folding →03c [4,5].
03a A 2D layer self-folds into a cube. 03b 4D Materials of varying compositions can achieve specific, measurable, organic-like forms like these printed hydrogel composites that shift shape when exposed to water. 03c 1D strand self-folds into a 3D wire-type cage. The strand, composed of engineered material, morphs when placed in water.
03 Smart materials bend, fold, twist, or curl once printed to morph into the desired form in a specified time.
Changing shape: a two-way street
Nowadays, complex shape memory materials (SMM) are employed to “remember” a specific state: a shape memory effect (SME). This effect requires at least two programming steps: the stimulus is applied; the 3D printed object’s original shape is transformed to a temporary state where the object remains until a second stimulus is applied to change the object back to its original form. Once altered, the structure can, through programming or without programming, re-create the temporary state again, and again – a reversible process [6].
The most common SMMs explored for 4D printing are based on hydrogels or liquid crystal elastomers, and various hybrids thereof. These hydrophilic polymeric substances can absorb vast amounts of water without dissolving: synthetic varieties are preferred due to their long life and gel strength [7]. Liquid crystal elastomers are polymer networks that can undergo a fully reversible large-amplitude shape change. They combine the elasticity of elastomers with the self-organization, and therefore programmable, property of liquid crystals. Due to their structures, this material shows promise in biomedicine, eg artificial muscle tissue and soft micro-robots.
Research and development drive the expansion
Currently, other top-notch research facilities such as the Wyss Research Institute for Biomedical Research at Harvard University, Rutgers University, the Swiss Federal Institute of Technology (ETH) in Zurich, and the California Institute of Technology (CIT) in addition to MIT, are making phenomenal advances in 4D printing.
The possibility of 4D printing to replicate biology is being studied by teams at the Wyss Institute at Harvard University, led by Jennifer Lewis. These researchers study how hydrogel changes shape and form in the presence of chemical stimuli, eg, water. Used as an ink, hydrogel enables the objects that it prints on to change shape to form different structures that are similar to those found in flowers. The tissue microstructures and compositions of different plants change depending on their environment. This research team replicated this organic process by mixing a 4D-printed hydrogel with cellulose fibrils to create composites programmed to control swelling. The resultant 3D-printed flower forms change shape when exposed to water, thereby mimicking plant organs’ responses to humidity, temperature, or other environmental stimuli →03b.
Other teams are printing hydrogels that respond to physical stimuli, eg, temperature. At Rutgers University, a lithography-based technique, projection micro-stereo-lithography (PμSL), printed temperature-dependent shape-shifting gels into 3D shapes. Such 4D printed structures could be used to develop atenuators in soft robotics or enable targeted drug delivery →04 [8].
04a Schematic showing the PµSL printing process, which relies on UV light. 04b Curing depth study results are shown. 04c The temperature-dependent swelling of the printed hydrogel is shown.
04 The procedure for printing temperature-responsive hydrogel using a process developed at Rutgers University [8].
At NASA’s Jet Propulsion Laboratory at CIT, researchers are studying woven metal fabrics – so-called space chain mail. The fabrics have four essential functions: reflectivity, passive heat management, foldability and tensile strength. One side of the fabric reflects light, while the other absorbs it, thereby acting as a means of thermal control. The fabric can fold in many different ways and adapt to shapes without succumbing to negative force influences. The ability to program new functions into the material creates almost infinite possibilities. One day these materials could be used to construct large antennae in space, create protective suits for astronauts or act as meteorite shields [9].
Researchers, Kristina Shea and Tian Chen, at ETH Zurich, used a Stratasys Objet3 Connex500 printer to create objects made of shape memory polymers; a temperature-resistant rigid polymer; and an elastomer-like polymer. The objects were printed as flat 2D structures that unfolded into load-bearing 3D shapes when placed in warm water. The ability to alter load-bearing capabilities over time could be of particular interest in the fields of space exploration, architecture and construction and the automotive industry [10,11].
Challenges and limitations
Despite advances in 4D printing, challenges and limitations must be addressed before 4D printing can leave the research labs; these include physical inertia, materials, durability, dependency factors, and cost. Currently, the transformation process takes from milliseconds to seconds to complete because large molecules must re-locate, moving over specific distances; this timing can be appropriate, too slow, or too rapid depending on the application, (eg, for building materials the process would be just right). Furthermore, stimuli-responsive materials are typically made of a limited range of polymers and thus restricted to specific environmental conditions, eg, heat, pressure, chemicals etc. To increase the reliability and durability of smart materials, composites that include metals and ceramics could also be used. And, because the structural transformation and its duration depend on multiple factors, different environmental conditions might cause different response times; this could be problematic. Moreover, 4D printing is currently rooted in well-funded niches, eg, medical, military, and luxury; but will scale to mainstream sectors in the future.
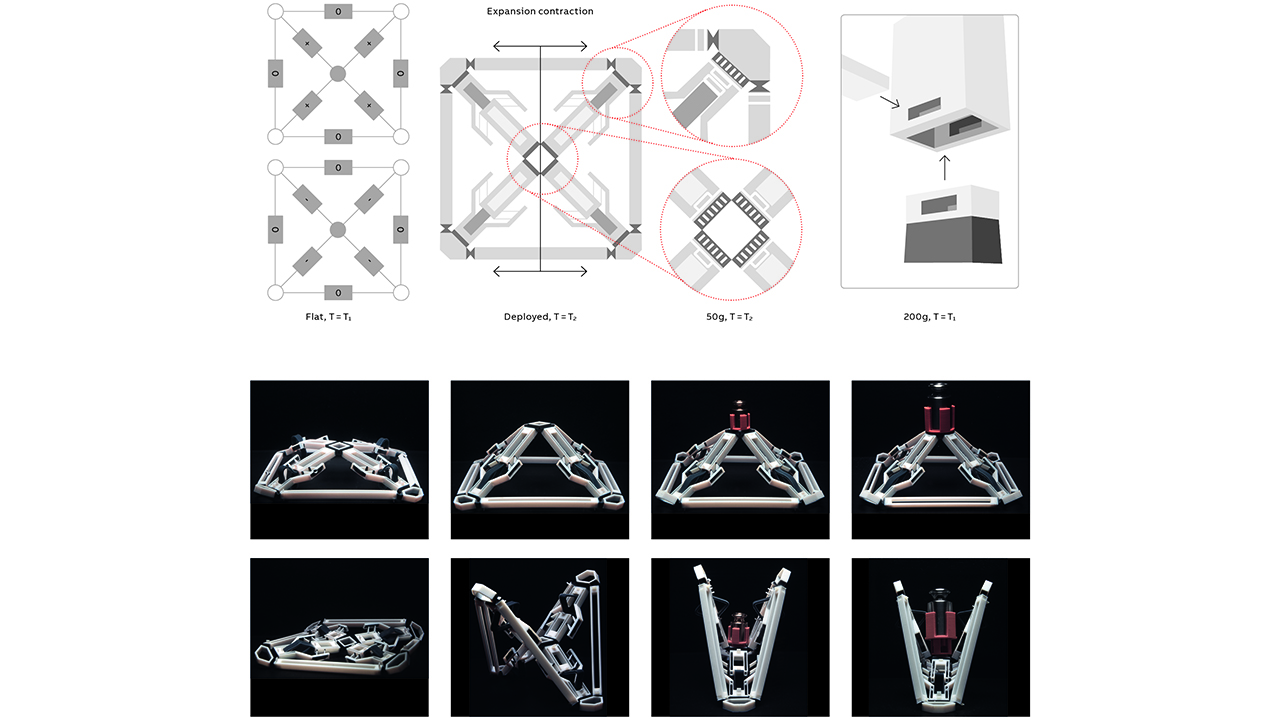
The future is 4D
Even though currently confined to research and development, the promise of benefits is expected to energize 4D printing over the next decade. The health-care, aerospace, defense, and automotive industries are beginning to seize on the possibilities.
Nevertheless, a range of product design possibilities and added functionality have yet to be adequately explored. For instance, design features with 4D printed connections, to allow ease of product disassembly could be integrated, thereby fostering reuse (or recycling) of components. And, to meet broader environmental requirements, a wider range of suitable materials and composites are needed. Additionally, more effort should be made to control the 4D printed object’s stability and optimize the 4D printing process. Nonetheless, businesses that desire to reap the rewards of digital innovation should contemplate the unprecedented potential of 4D printing, especially as an enabler for the creation of autonomous moving agents.
As the Fourth Industrial Revolution expands; and advances in smart material design, 4D printing technology, and robotics gain momentum, before you know it, it might not only be possible to print customized robotic arms to support industrial processes, robots might be able to design, construct, and repair themselves, anywhere at any time.
References
[1] Altair, ABB, “MX3D Robot Arm”, 2019, Online. Available: https://mx3d.com/projects/robot-arm/
[2] S. Tibbets et al., “4D Printing: multi-material shape change” Architect Design, vol. 84, 2014, pp. 116–121.
[3] Wyss Institute at Harvard, “Novel 4D printing method blossoms from botanical inspiration”, 2016, Online. Available: https://wyss.harvard.edu/news/novel-4d-printing-method/ Accessed on 9 Dec. 2019.
[4] S. Tibbets et al., “4D printing and universal transformation”, in Material Agency, 2014. pp. 539–548.
[5] F. Momeni et al., “A review of 4D printing” in Materials and Design, 2017, pp. 42–79.
[6] Zhou et al., “Reversible shape-shifting in polymeric materials”, in Journal of Polymer Science & Polymer Physics, vol. 54, 2016, pp. 1365–1380.
[7] “Hydrogel: Preparation, characterization, and applications: A review”, in Journal of Advanced Research, vol. 6 issue 2, 2015, pp. 105–121. Online. Available: https://www.sciencedirect.com/science/article/pii/S2090123213000 969
[8] D. Han, Z. Lu, C. Shaun and H. Lee, “Micro 3D Printing of a Temperature-Responsive Hydrogel Using Projection Micro- Stereolithography”, in Sci. Reports, no. 8, 31 Jan. 2018, Online. Available: https://www.nature.com/articles/s41598-018-20385-2
[9] NASA Jet Propulsion Laboratory, “Space Fabric links Fashion and Engineering”, April 18, 2017, Online. Available: https://www.jpl.nasa.gov/news/news.php?feature=6816
[10] C. Scott, “ETH Zurich Researchers Develop 4D Printed Load-Bearing Polymer Structures”, 2018, Online. Available: https://3dprint.com/219758/eth-zurich-4d-printed- structures-2/
[11] Tian Chen and Kristina Shea, “An Autonomous Programmable Actuator and Shape Reconfigurable Structures Using Bistability and Shape Memory Polymers” in 3D Printing and Additive Manufacturing, vol. 5, No 2. 1 June 2018 https://doi.org/10.3929/ethz-b-000267291