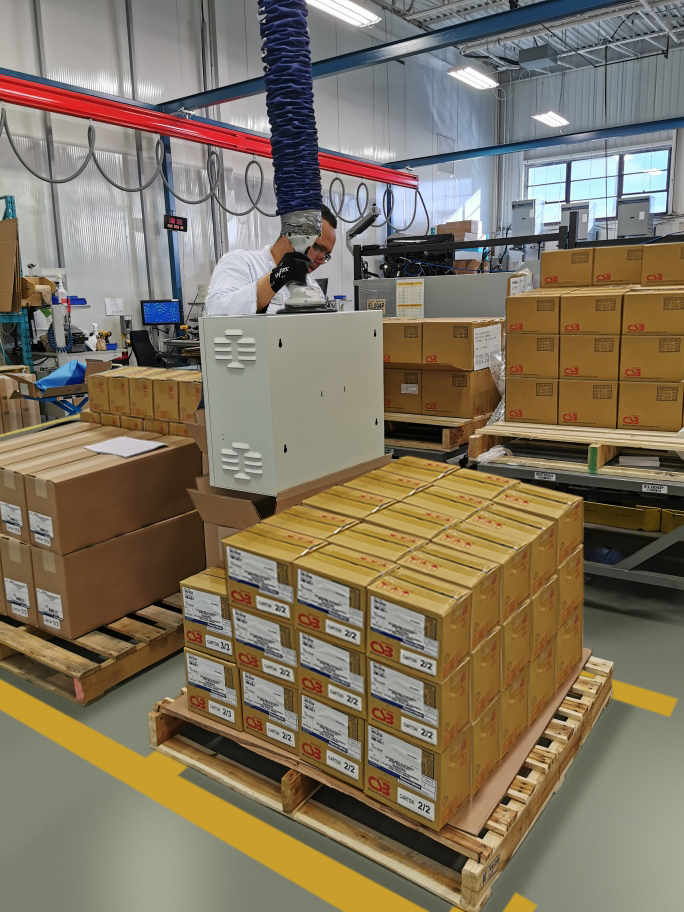
March 30 – 8:00 AM
It’s Tuesday morning. Employees come into work at the ABB Emergency Lighting facility in Dorval, Quebec, Canada like any other day. Compared to three weeks prior, morning activities look very different at the facility. The COVID-19 crisis has changed how the office and production facility functions normally. With most working from home, our production facility is still up and running with safety and strict sanitation measures in place. Like people around the world, everyone is concerned about the health of their families, their children’s schooling, and their jobs. Just like at companies everywhere, it’s far from business as usual for the ABB team.
March 30 – 1:00 PM
Wendy Williams, Inside Sales Representative, receives a phone call. It’s an order for mini-inverters, which are make-to-order units. It’s far from a typical order in a week that will quickly become anything but typical.
The customer, a Richmond, British Columbia based distributor, needs to ship the units to provide AC/DC power for Hamilton Care Center, a temporary hospital facility being built to accommodate an expected surge of patients with COVID-19.
Locally, surge load modeling by the regional governing body for healthcare in Richmond, BC paints a picture of hospitals near capacity and potentially overcapacity.
In the back of everyone’s mind, a what-if scenario plays out. What if parts are on backorder? What if there are shipping problems? What if the auxiliary ICU space is not ready on time? The real importance of the order sinks in.
March 30 – 2:15 PM
Relaying the order to Debra Vanloo in Customer Service, Wendy did not mince words. “A hospital in Richmond needs the inverters right now.” It would usually take 24 hours to process an order for inverters and have it released for production. Lead time for mini inverters would have been five days. All that would have to change and change fast.
With a wide portfolio and a state-of-the-art manufacturing facility, the ABB Dorval team enhances building safety for its customers by providing emergency lighting products, support, and resources. Although the division’s equipment is designed to respond to emergencies, this inverter order gives the team a heightened sense of responsibility and highlights the importance of their work real in a way they never felt before.
Danny Coté, Manufacturing Unit Manager, is reminded of the true value of the products and it is life-saving nature the team at ABB Dorval delivers every day, and the impact they can have on people’s lives. “This is the WHY we do things. The work makes a difference. This is for real.”
March 30 – 5:00 PM
The team rewrites the entire fulfillment process while executing it. Tina Tzimopoulos, Customer Service and Planning Supervisor, works closely with Audrey-Eve Trottier, Production Supervisor, and her team in the PCB department. They connect with Luiz Carlos Silva in Inverters to put the order into production. Production Manager Jean-Sebastien Ouimet is proud of the team and its proactiveness. To be able to execute this order and serve the customer in a critical time of need in this way takes tremendous team spirit. By expediting the order entry and work order release process and having team members work in parallel, the PCB team is in place when the work order arrives on the floor.
March 30 – 7:00 PM
Material for the order is picked from the warehouse to make sure everything is ready for next morning’s production.
March 31
A full day of production and assembly.
April 1 – 7:00 AM
The Inverter team starts assembly and testing of the units. It will take them four hours to produce the units.
When you typically work shoulder to shoulder with people as a cohesive team, social distancing, and other safety measures keep everyone slightly off balance and add to stress levels that are already running high. But a sense of urgency and new challenges with real life and death consequences bring out the very best in people, and the ABB Emergency Lighting Dorval team is no exception. From the initial call to the ultimate shipping of the order, the team demonstrates its capacity to step way out of its comfort zone, communicate effectively and come up with new ways of doing things that meet the urgent customer’s needs.
April 1 – 11:15 AM
The inverters are shipped, less than 48 hours from the initial customer request.
Thinking about the courage of the doctors, nurses, and other vital support staff on the front lines inspired the ABB Dorval team to go beyond and deliver on a timeline that weeks earlier would have been considered impossible. The importance of providing critical electrical infrastructure so hospitals can care for their patients really hit home. Three weeks can change everything, and the ABB Dorval team is proud to have quickly adapted and raised its game to meet a critical new challenge.