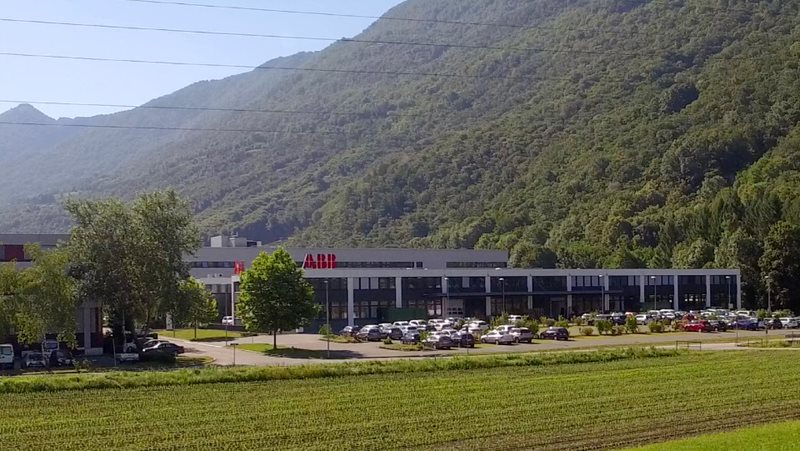
The COVID-19 pandemic has prompted a flurry of technological developments to help businesses surmount the travel and communication restrictions imposed during lockdowns all across the globe. A new augmented reality (AR) tool, Acty, now being employed by ABB Electrification Service experts is one of the most significant examples of such high-tech advancements for customers requiring installations and maintenance.
The augmented reality software—available to techs on mobile devices and desktop computers—recently proved its value when a customer in Iceland needed assistance from ABB in starting up a UPS system. Ordinarily, startups are performed by ABB factory-trained and certified technicians on-site to avoid any possibility of costly damage and delays from a customer attempting commissioning while equipped only with the detailed user manual and a telephone.
With the pandemic raging, however, travel to Switzerland for formal training was not possible and, likewise, ABB Service techs were unable to travel to Iceland. Consequently, the ABB Quartino team developed a highly effective remote solution. They first created a dedicated webinar session and an online e-learning module to deliver the theoretical content of the training to a field team at the customer’s site.
Then the Quartino team provided live support through augmented reality, guiding and directing the field team throughout the day. With the AR app, the operator in ABB’s service center could view video that the operator on site was showing with his smartphone, and vice versa. Experts in Quartino could sketch on the video, freeze the image and chat with real-time translation.
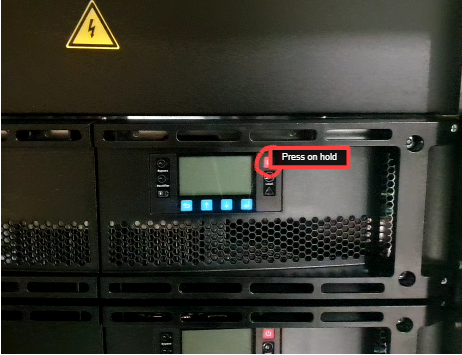
“Marking in the picture what point to measure or button to press is much more immediate than describing over the phone,” said ABB Service Engineer Fabrizio Massaini. “This solution allows us to guide a technician in the field and avoid misunderstandings that can happen over the phone.”
Reducing errors with live interaction
This was Quartino’s first support engagement to use AR and led to three more support cases employing this method. Coincidentally, the remote methodology is saving travel costs for partners who otherwise would come to Switzerland for training.
“The augmented reality app proved to be of great help,” added Mauro Scappini, ABB Service Manager, “reducing the risk of errors and clearly indicating the steps to follow. Cellular bandwidth allowed for a great video quality, paired with audio and interactive tools.”
While in-person classroom training will remain the preferred delivery method, the Quartino team reports they now feel confident in using AR as a standard when travel to a customer site or to the ABB training center is not an option. The team currently is developing a set of training sessions for re-certification and other applications where augmented reality will complement the webinar and online module, allowing for live interaction with the student.