As demand for data centers increases, ABB Power Grids* is helping to reduce the carbon and real estate footprint of these facilities. The company’s latest generation of smart data center substations [1] meets these challenges by using smart modular components while reducing the quantity of copper control cables by over 50 percent. Furthermore, ABB’s smart substations provide a high level of reliability and are set to streamline maintenance work through the use of digitized data and condition-based asset management.
*a planned joint venture between Hitachi and ABB.
William K. Mao Power Grids Houston, TX, United States, william.k.mao@us.abb.com, Dave Sterlace ABB Data Center Solutions Philadelphia, PA, United States, dave.sterlace@us.abb.com
Recent innovative developments in key substation assets, such as gas insulated switchgear (GIS) [2], power transformers (PT), high-voltage circuit breakers (HVB) and fiber-optic current sensors (FOCS) have all moved into the digital age →01. For instance, the ABB Ability™ Power Transformer (TXpert™) →04 is the first native digital PT to offer real-time data on load, temperature, and dissolved gas analysis (DGA) of transformer oil or fluids.
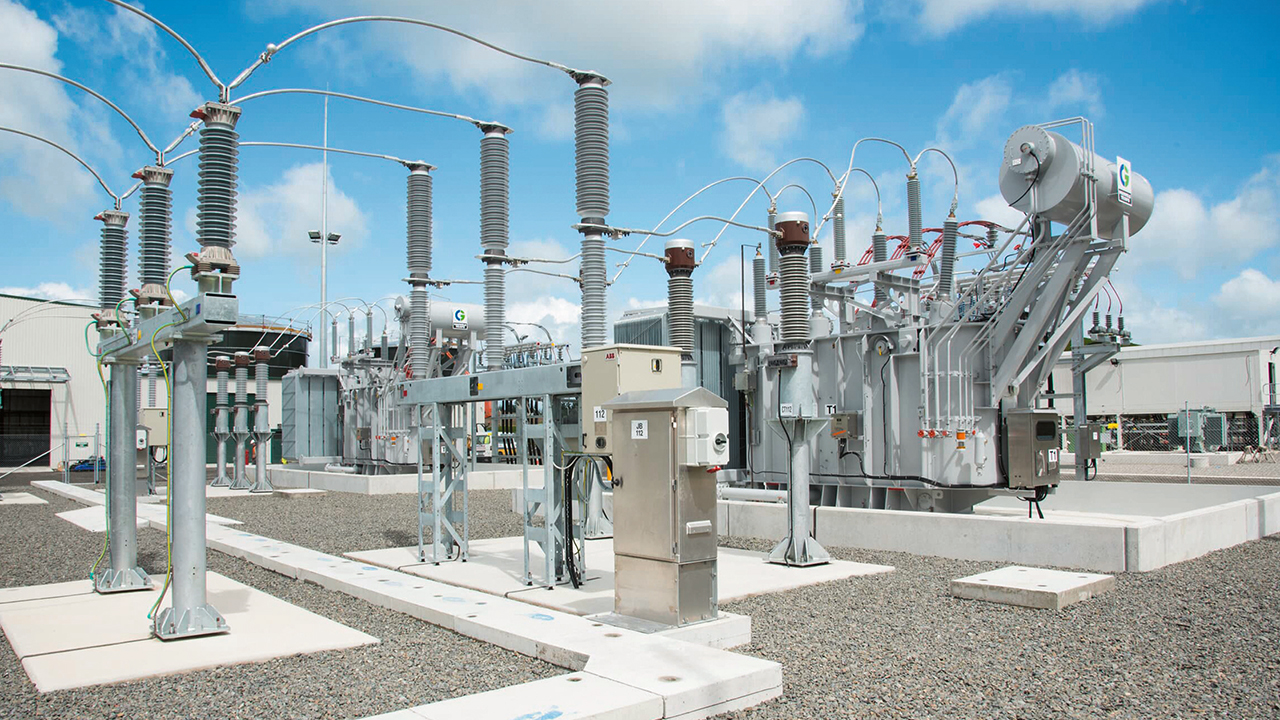
Several of these assets, including high-voltage circuit breakers, switchgear, and other electrical equipment, have traditionally used SF6 (sulfur hexafluoride), an inorganic, colorless, odorless, non-flammable, non-toxic gaseous dielectric medium. However, SF6 is also an extremely potent greenhouse gas. In view of this, ABB Power Grids has introduced eco-efficient switchgear with new AirPlus™, a groundbreaking gas mixture with 99.99 percent lower global warming potential (GWP) than SF6.
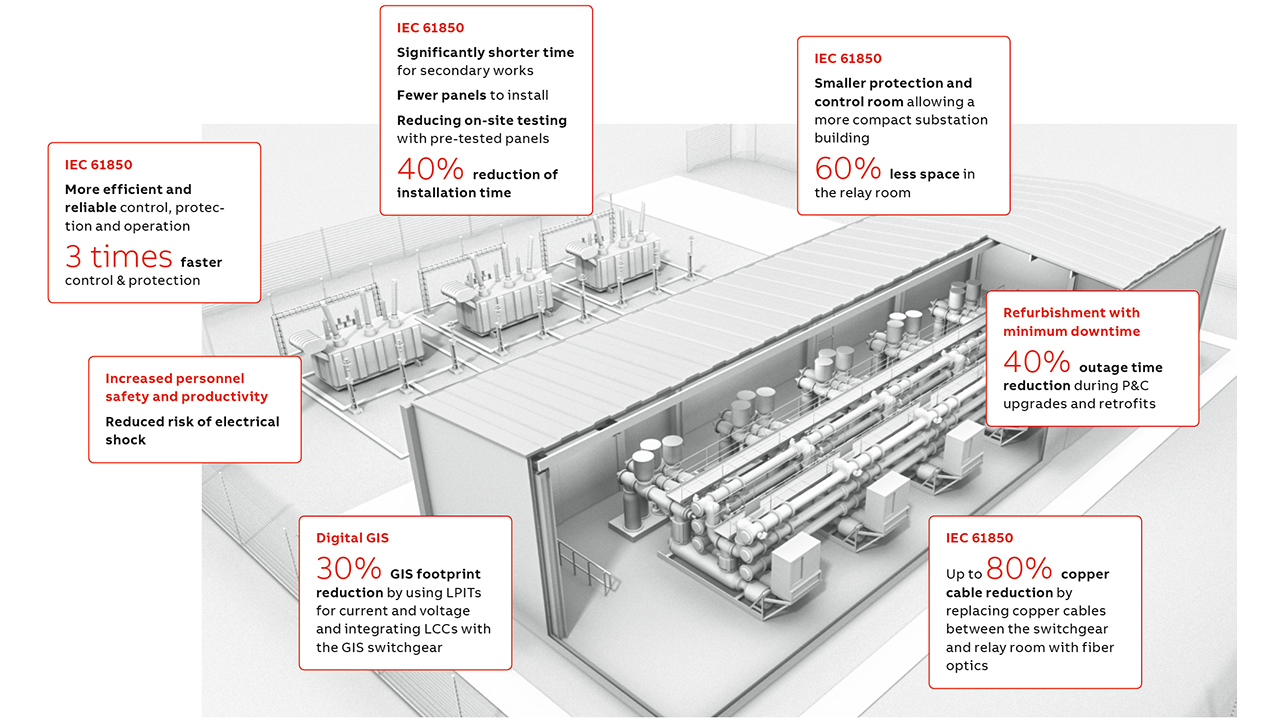
Furthermore, with a view to offering tailored solutions to the rapidly growing data center industry, ABB has introduced a purpose-built substation →02 that is designed to be highly reliable and safe, while facilitating efficient operation and maintenance throughout its entire lifecycle. The new smart substation is over 30 percent smaller than its predecessor and uses 50 percent less copper on control cables. Fewer cables means fewer field electrician man-hours stripping cables, crimping connections, testing out contact points, etc. In short, the new substation design reduces site construction time and lowers risk.
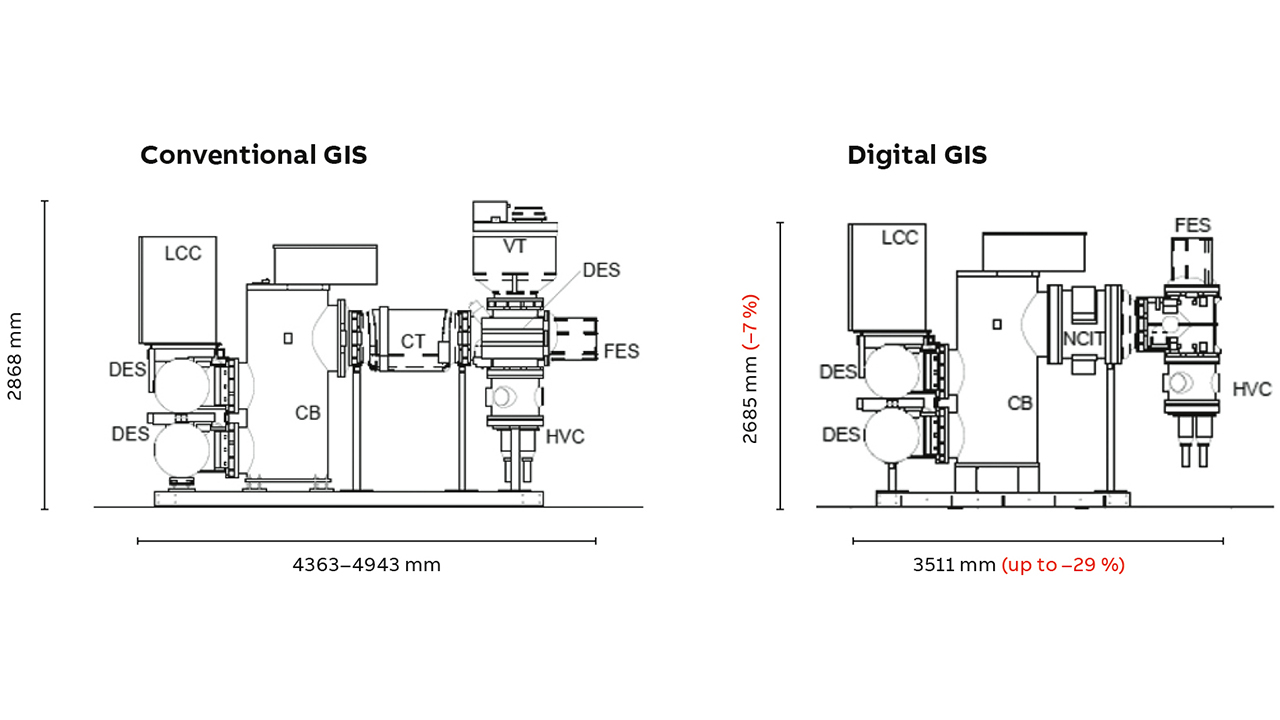
ABB’s new smart data center digital substations offer many advantages compared with traditional substations. They:
• require 30 percent less physical space for digital GIS →03 – 04 by using non-conventional low-power instrument transformers (LPITs) for current and voltage measurement and for integrating local control cubicles (LCCs) with high-voltage switchgear.
• use 50 percent less copper cabling by replacing copper cables with fiber optics and reducing the number of physical connections through digitization. A typical data center substation equipped with two HV feeders yields savings of ~4,000 lbs. (~1,800 kg) of copper control wires.
• require 60 percent less physical space for relay control rooms because:
– fiber optics replace copper cables
– modern intelligent electronic devices are smaller, allowing more units per rack, and are multi-functional, allowing one unit to replace multiple older legacy relays
• require fewer and lighter components and smaller foundations
• result in a reduced carbon footprint due to diminished material weight to be transported and elimination of harmful SF6 gas handling
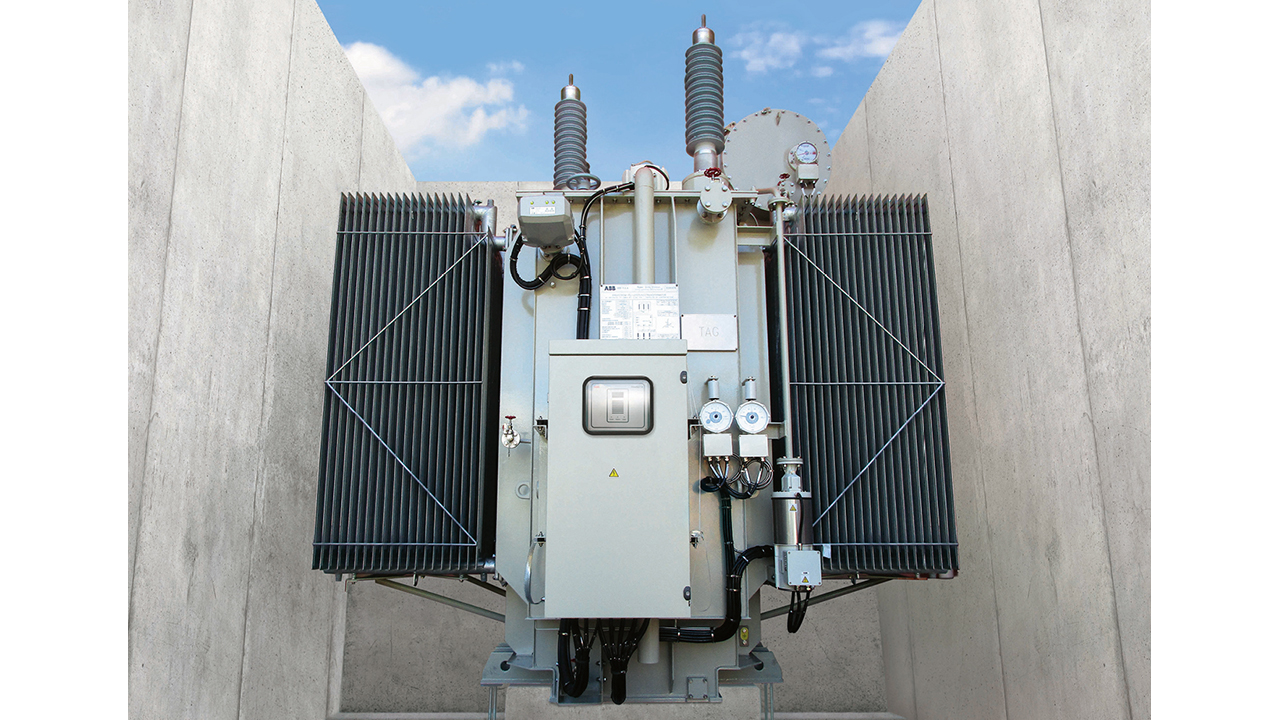
Sustainable asset performance management
To round out the sustainability picture for smart data center substations, it is important to take a look at how condition-based asset performance management (APM) saves resources by reducing man hours and contributes to improved safety by reducing human interactions with high-voltage equipment.
ABB Ability™ Ellipse® APM Edge →05 [4] is a quick and cost-effective entry into data center substation transformer asset management. It combines ABB’s industry-leading asset performance management software (Ellipse® APM) with the company’s proven transformer expertise in a compact package that grows with the customer’s needs [3].
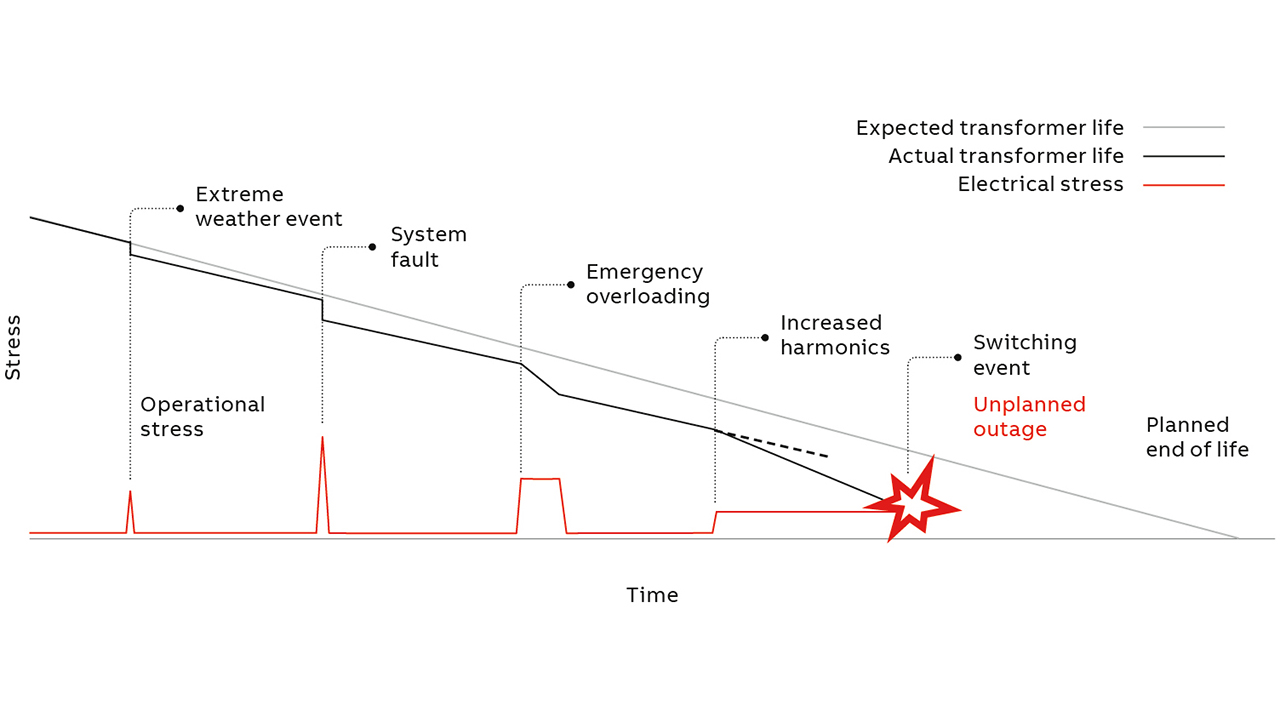
Ellipse Edge runs on the customer’s premises and interacts with most industrial communication standards over low-cost, standard hardware. It offers a quick and efficient way to run Ellipse APM with minimal capital expense. For instance, it features a plug-and-play capability with ABB sensors and direct-to-sensor connectivity, eliminating the need for a dedicated historical database and enhancing the value of existing transformer sensors and hardware. By combining online and offline data into a common scheme, Ellipse Edge plots and trends data using globally recognized standards (IEEE, IEC). A dashboard accurately identifies and predicts risk probability while helping to optimize asset performance. Ellipse Edge also features a human-trained deterministic model that correlates data components to each other and known failure modes, thus delivering actionable intelligence – including maintenance recommendations [5].
All in all, Ellipse Edge provides the following advantages:
• Improved asset availability with minimal-to-zero planned and unplanned outages, which is crucial for mission-critical installations such as data center substations
• Extended asset life – it is greener to run assets longer instead of replacing them prematurely
• Enhanced predictive maintenance, which reduces waste and diminishes routine tasks
• Prevention of catastrophic failures that are often accompanied by environmental impacts
• Integration of renewable energy resources for self-consumption
• Reduction of overall energy consumption from the grid with smart energy management
Whether a data center’s substation operates one transformer or a fleet of dozens, the operator can scale up on-premises or in the cloud as demand grows, benefiting from Ellipse Edge software without significant capital investment. Furthermore, since the platform runs on an independent network or intranet, it reduces security risks by meeting ABB’s stringent cyber security standards, which are based on industry requirements.
All in all, smart data center substation design reduces an installation’s dimensions and material requirements, which results in considerably less weight, both in terms of metal enclosures and internal insulating gas volume. Furthermore, digital substitutions use fiber optic wires to connect the GIS to freestanding control panels, thus eliminating the need for hundreds of copper control cables. This reduces installation costs as well as the costs associated with decommissioning and recycling.
References
[1] ABB Substation Automation Systems, “We are bridging the gap.” Available: https://new.abb.com/substation-automation/systems/digital-substation/bridging-the-gap
[2] ABB Power Grids, ”Eco-efficient switchgear with innovative insulation gases.” Available: https://new.abb.com/grid/technology/eco-efficient-gas-insulated-switchgear
[3] ABB Smart Transformers, “Smart transformers.“ Available: https://new.abb.com/products/transformers/transformer-events/smart-transformers
[4] Calculation is based on a typical data center HV substation with 400 hardwired connections, 12 gauge.
[5] ABB Power Grids, ”ABB Ability™ Power Transformer – the world’s first digitally integrated power transformer.” Available: https://www.youtube.com/watch?v=j2DL_DVZ3-E. For additional ideas see: https://new.abb.com/distributed-energy-microgrids