Vincent Duong ABB Digital Solution Center Lake Mary, FL United States, vincent.duong@us.abb.com
It is fair to say that the publication of the IEC 61850 standard in 2004 transformed the world of substation automation. IEC 61850 – to which ABB made significant contributions – provides a standardized framework for substation integration that specifies the communications requirements, the functional characteristics, the structure of data in devices, the naming conventions for the data, how applications interact and control the devices, and how conformity to the standard should be tested.
The abilities of IEC 61850 to marry protection and supervision in low- and medium-voltage installations were quickly recognized and the standard is now being increasingly used in applications in low voltage, medium voltage and high voltage. Equipment now benefiting from IEC 61850 functionality includes protection relays, circuit breakers, communication gateways, programmable logic controllers (PLCs) and supervisory control and data acquisition (SCADA) architectures. Together, these devices make it possible to design and operate a fully integrated protection and supervision system that spans the voltage ranges just described. This comprehensive approach is made possible by exploiting IEC 61850 to create features such as advanced logic selectivity based on device-to-device communication, real-time diagnostics and integrated engineering.
IEC 61850 is ideally suited to the automation of data center power infrastructure →01.
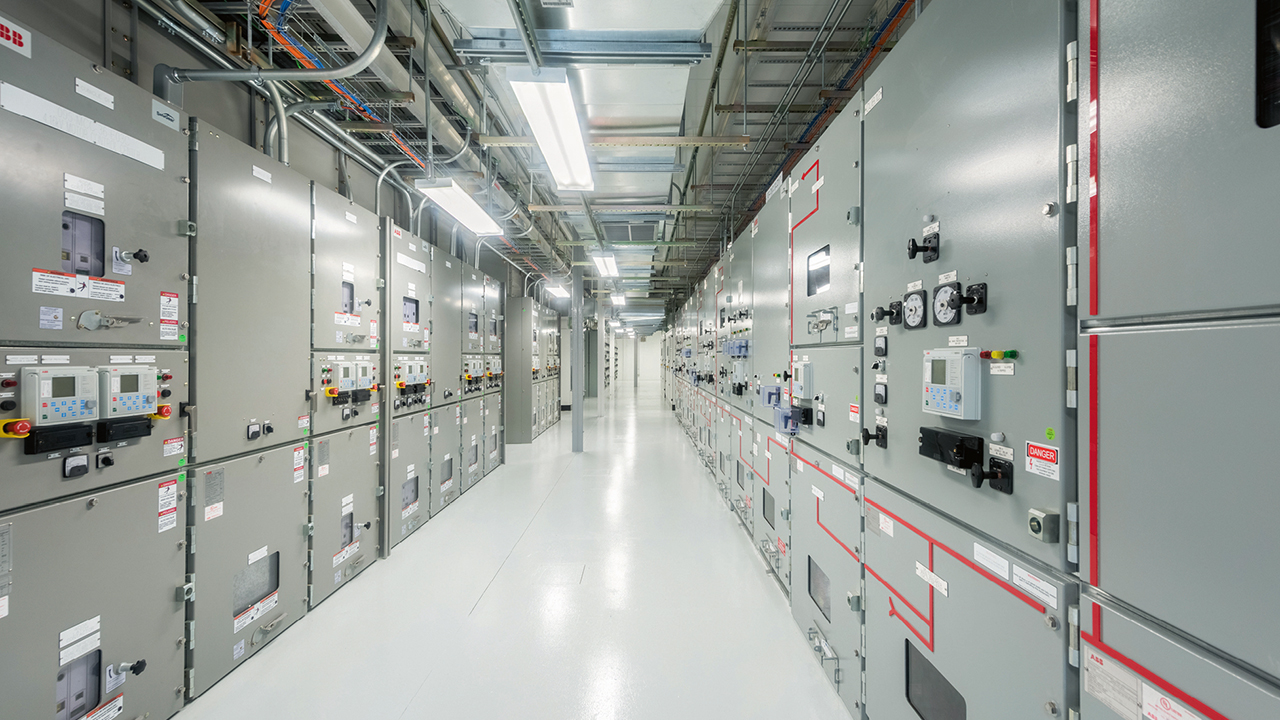
IEC 61850 and data centers
The world is experiencing a data explosion. Not only is the quantity of data increasing at a dizzying rate, but the extent to which society relies on that data is also growing by the day. These trends elevate the data center to the status of critical infrastructure in many countries. If a data center fails, chaos ensues, which makes a reliable power supply indispensable. Generally, data centers do have well-thought-out power backup provisions – such as uninterruptible power supplies (UPSs), diesel generators, etc.
By employing IEC 61850-enabled devices and IEC 61850-based GOOSE (generic object-oriented substation event) communication to automate the data center power infrastructure, significant improvements can be made: better power supply reliability, greater operational control and reduced cost, to name but a few →02.
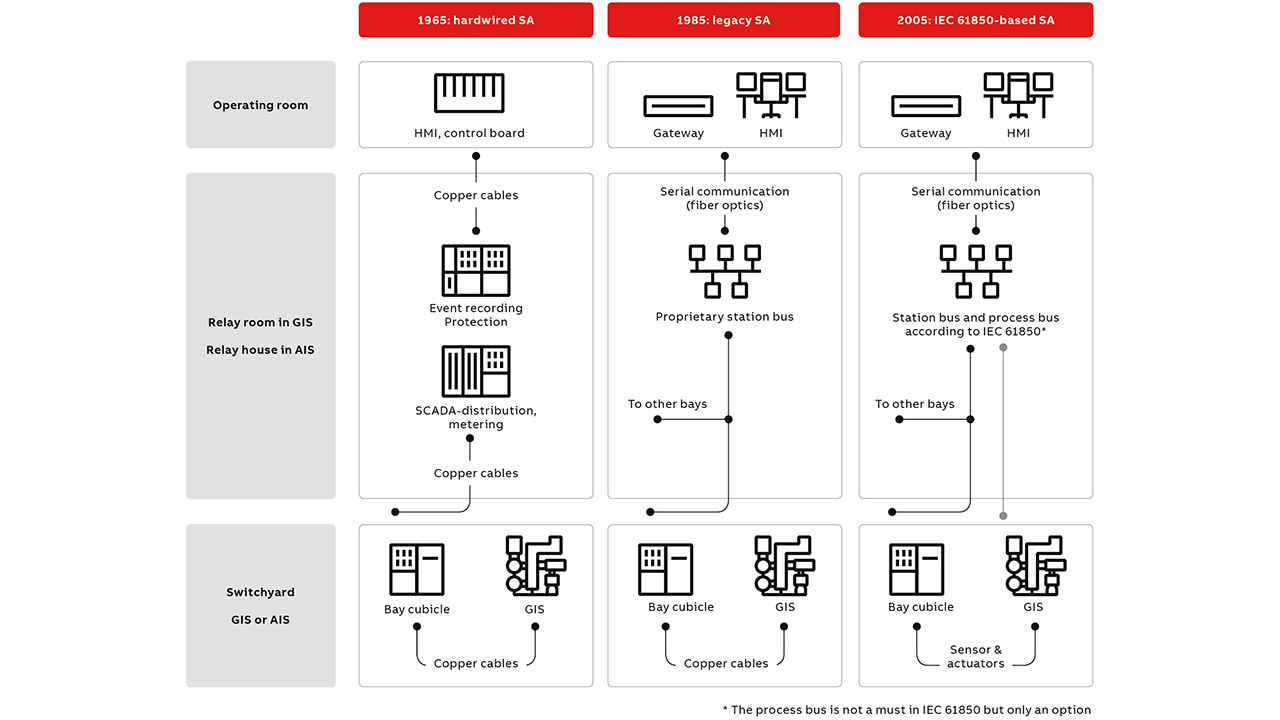
GOOSE
When a fault occurs in a data center power component, the protection device that detected it must transmit fault information as quickly as possible to the devices that decide which breaker should trip. Arranging such transmissions in a round-robin – or other cyclic fashion – that requires the device to wait its turn for access to the communication media would introduce unacceptable delays. The effective handling of such unscheduled, on-event communication is one of the differentiating features of IEC 61850 and it is implemented using special data packets called GOOSE messages. Instead of cycle time, with GOOSE messages the key engineering consideration is latency, ie, the delay between an event and the transmission of relevant information on the network.
A key feature of GOOSE messages is that they can be used for horizontal (ie, peer-to-peer) communication between devices in addition to the usual vertical communication from device to supervision system. So, a logic selectivity or an interlock between two circuit breakers can be implemented by direct message exchange between the relevant devices without relying on a central processing unit to manage the process. Horizontal communication improves both performance (shorter overall reaction time and more efficient use of the communication channel) and reliability (as a failure of the central processing unit would impair the whole protection scheme).
In addition to fault signaling, GOOSE messages can be used to implement a built-in diagnostic mechanism in the data center power protection system. Each device can be configured to send a “ping” message to others regularly (eg, every second) to report that their status is normal. If the relevant devices fail to receive the appropriate message, they may, in turn, send alarm messages, switch to a predefined safe mode, or take other actions as required. Diagnostic messages use the same communication medium as other data packets, so no additional hardware is required.
Practical GOOSE-enabled bus protection
IEC 61850 allows the data center’s dedicated bus protection relay to be eliminated. Instead, each breaker’s relay, such as the feeder protection relay or breaker failure relay, is relied upon. A “master” relay performs the bus-protection role, with another relay assigned as a backup to the master. All relays involved in IEC 61850-enabled data center power bus protection communicate via GOOSE protocols →03.

IEC 61850-compliant relays, such as ABB’s Relion relays and Emax 2, are usually equipped with multiple Ethernet ports with parallel redundancy protocol (PRP). PRP enables double-star network topologies using self-healing rings that effectively achieve 100 percent communication availability. Of these two approaches – double-star and self-healing – the former configuration creates less network disturbance during future expansions, offers faster troubleshooting, has minimum communication latency and is easier to maintain.
A data center power protection scheme based on IEC 61850 also has other advantages over traditional approaches: Because it uses a fiber-optic Ethernet network, the expensive, space-consuming, complicated and error-prone point-to-point copper wiring found in traditional data center power arrangements can be reduced or eliminated. The reduction (or elimination) of this cross-wiring of related relays also brings substantial savings in engineering, installation labor and time, and materials. The reduction in copper wiring alone has a significant positive financial impact as well as major benefits when it comes to increased reliability and decreased life cycle costs. For new installations, costs are also reduced by avoiding the expense of additional protective relays. IEC 61850 bus also makes future modifications or expansion simpler.
Automatic transfer switch (ATS)
Another example of an IEC 61850 application can be found in the ATS. Power availability and stability are critical to data center operations so, typically, the site is fed by two incoming utility sources, usually in a medium-voltage Main-Tie-Main (M-T-M) bus configuration →04. The ATS offers an effective and reliable way to automatically transfer to a healthy bus from one that has lost its incoming source. To seek out quickly the available alternate source and transfer loads from the lost-source bus to the healthy bus, relays exchange GOOSE messages containing condition data such as the source-voltage-loss event itself, state of health of the alternate source, pending overcurrent or bus protection trips, normal status of main and tie circuit breakers, etc. Utilizing IEC 61850 in this way delivers the following benefits:
• Reduction of wiring materials and labor.
• Minimization of system loss time.
• A secure operation that minimizes the stress on standby generators and UPSs.
• Full IEC 61850 data visibility of relays for system reporting, monitoring and analysis.
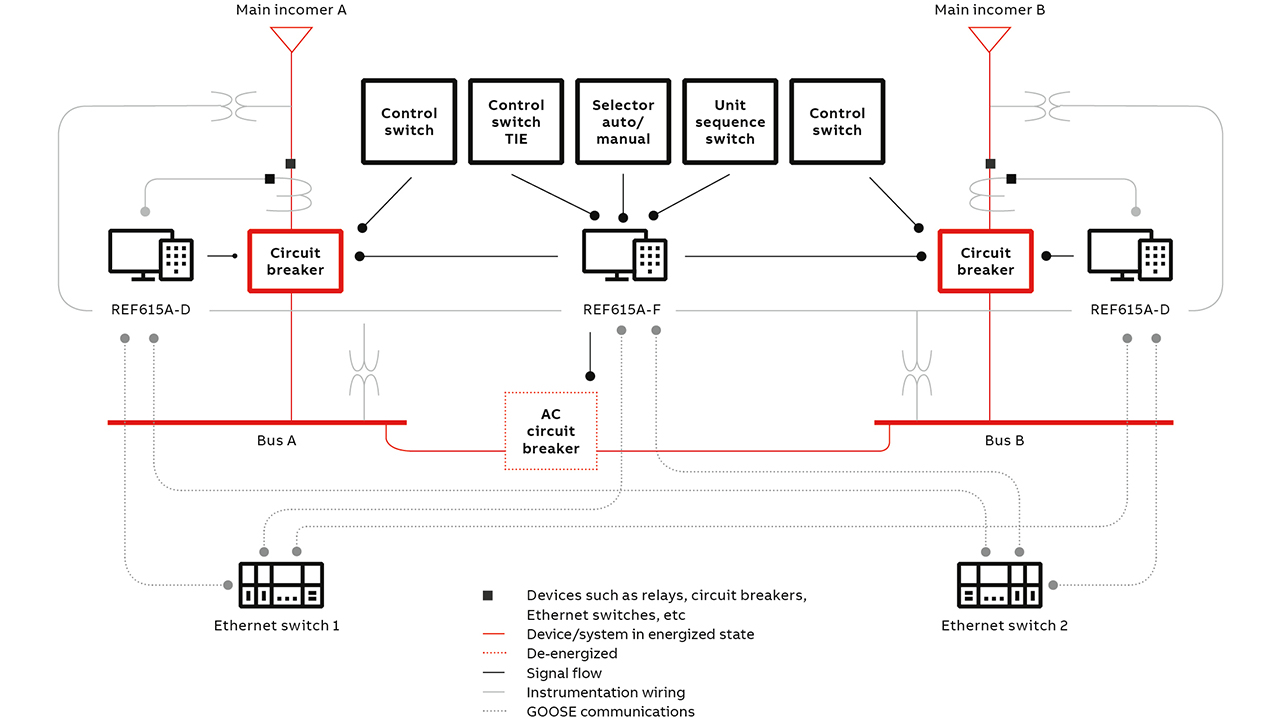
Engineering and configuration made easy
Additional advantages of IEC 61850 are related to engineering and configuration processes. Because of the complexity and number of the devices involved in a typical data center power system, designing a protection system without a structured, computer-assisted process is difficult; the sheer number of configuration and operational details invites critical errors. To prevent these errors, IEC 61850 relies on standardization of objects and data types, and formal electronic descriptions.
IED (intelligent electronic device) complexity is managed in IEC 61850 by describing each device as a set of logical objects, which can be published in the final application. Such objects are abstract enough to be applicable to devices of different types or from different vendors, yet realistic enough to be applicable to the engineering job in hand. Examples of such objects are overcurrent protection, current and voltage measurement, control of a switch, etc.
A cornerstone of the IEC 61850 data model is a catalog of standardized logical objects with well-defined meanings, and applicable parameters and data items. All devices compliant with IEC 61850 use the same objects to implement the same function, making it possible to combine objects in a common way in a final data center power implementation. Such standardization goes down to object names (eg, PTOC always represents an overcurrent protection), which makes them easy to recognize and use by the design engineer. Data types are also set by IEC 61850, so that, for example, the result of a measurement is defined together with its name, measurement units, quality indicators and so on, thus reducing the probability of errors.
To complement this standardization, IEC 61850 describes a common electronic format in which devices and systems are described. All devices – IEDs – are each described by a file, written in SCL (Substation Configuration description Language), that lists all its properties and logical objects. SCL files can be read and manipulated by IEC 61850 software engineering tools, allowing a smooth process and a reduced number of errors.
Such a formalized electronic description language has the important side benefit of easing interoperability between devices from different vendors that are installed in the data center: As long as the objects they implement are described by the SCL file, the user need not be concerned with their inner workings.
Ideal for data center power infrastructure automation
IEC 61850 is eminently suited to data center power infrastructure automation, where it can form the bedrock of a complete electrical design concept that includes the entire protection, control and supervision system as well as cyber security – using just one protocol.
By using optical fiber instead of copper wire, wiring costs are lowered, space requirements are substantially reduced and safety is increased. IEC 61850 also delivers the capability to monitor and control IEDs remotely, and the convenience that devices supplied by different manufacturers can communicate with each other without custom-designed gateways or other engineering-intensive complications.
Taking a wider perspective, the IEC 61850 standard allows digitalization of the data center power system in a way that opens it to collaboration with other digital entities in the data center, such as a building management system (BMS), power management system (PMS), data center infrastructure management (DCIM) or ABB Ability™ Data Center Automation. These are all important parts of the final goal: the “single plane of glass” that orchestrates the entire data center. Decathlon for Data Centers, for instance, gives power and cooling visibility, and IEC 61850’s open protocols allow integration of existing equipment and systems. With IEC 61850 peer-to-peer communication capabilities in components like ABB’s Relion relays and Emax circuit breakers, one can go from the DCIM system controlling or supervising software to having real-time interaction with the subsystem (such as a UPS breaker) itself.
Increased reliability, finer selectivity, shorter fault reaction times and the possibility to implement fault tolerance and integrated diagnostics as well as a host of other advantages make IEC 61850 the ideal standard for data centers.