As far-fetched as this may sound, automakers are increasingly looking to Formula E, the electric car racing series, as a test bed for innovative technologies. Lessons from the racetrack — especially battery technology — will prove critical in improving consumer electric vehicles (EVs), engineers say.
EVs will account for almost one-third of new car sales globally by 2030, according to a report from the management consulting arm of Deloitte. However, consumers harbour concerns about the cost and driving range of current models, as well as the lack of a comprehensive charging network.
“Motorsport develops your technology very quickly. Nobody likes to lose. And if you do lose, you go home and work on it straight away because there’s another race in three or four weeks,” says Allan McNish, a retired Formula 1 and Le Mans racing driver who is now principal of Audi’s Formula E team.
Normally consumer cars follow production cycles of up to five years from conception to their appearance in dealerships. But in Formula E, technology is moving from race cars to production vehicles in as little as 12 months.
Unlike Formula 1, where aerodynamics is a key differentiating factor between competitors, Formula E hardware is standardised. Teams share a common battery, chassis and other bodywork. What sets them apart is their power train — the mechanism that transmits the drive from the engine to the vehicle’s axle — and the software used to manage that system.
“Tomorrow you could take the power train from one of my race cars as it is, bolt it on to a sports car for the road and drive that car to London,” says Sylvain Filippi, managing director at Envision Virgin Racing, a Formula E team.
While the first generation Formula E battery in season one (2014-15) highlighted the ability to race electric cars, the launch of Gen2 last year demonstrated a doubling of the car’s range and a higher maximum speed on the same volume of battery, says James Barclay, team director at Panasonic Jaguar.
Formula E is now looking to go a step further, with Williams Advanced Engineering (WAE) designing a new battery system (Gen3) for the 2022-23 season.
Although Formula E’s power train is 95 per cent energy efficient, there is capacity to add a second regenerative unit to the front axle. This technology recovers the car’s kinetic energy when it slows and puts the electric motor into reverse — becoming a generator that returns energy to the battery. The driver does not need to tap the brakes.
Besides being smaller, lighter and more powerful than previous versions, the Gen3 battery will also be able to regenerate fast enough to allow for charging pit stops during races.
Previously, drivers of the first-generation model had to switch to a second car to complete the circuit as recently as 2018. Such advances in charging technology could similarly be used in consumer vehicles.
Nevertheless, some challenges remain, says Bob Stojanovic, director of electric vehicle infrastructure at ABB, the energy technology group. Although larger batteries charge faster, the charging rate diminishes once it hits 80 per cent capacity.
The voltage of a car is also a limiting factor insofar as it determines the level of current that can pass through. A close though imperfect analogy, says Mr Stojanovic, is that if you were to increase the diameter of a garden hose, more water would flow and at a faster rate. The Porsche Taycan, for example, has double the standard EV voltage at 800V, which has halved its charging time — an industry first.
ABB’s new 160kW-rated chargers for Formula E, which can charge two cars simultaneously, will also be available for consumers and drive down expenses as operators can deliver twice the power for the price of installing a single charging unit. Meanwhile, peers such as Enel X have used Formula E to test the resilience of their charging equipment across temperatures varying from 5C to 40C on racetracks in Santiago de Chile and Marrakesh.
This is buttressed by developments on the software side. By utilising battery temperature data collected from the eTrophy race series, Jaguar added 20km of range to its consumer EV, the I-Pace, taking its total distance to 470km on a single charge. Tesla uses an automated approach whereby new software is installed into its cars online.
“We’ve seen a rash of vehicles where, in the rush to bring products to market, manufacturers have basically taken the engine out and filled the engine bay with batteries,” says Douglas Campling, chief engineer at WAE. But the industry is missing a trick. In future, batteries will be intrinsic to “the structure of the vehicle”, allowing for greater flexibility in how the interior is packaged and designed.
But for Mr Agag, the answer is simple: “The only way to motivate these big companies to develop more and more technologies is to get them to [compete] against one another. To win.”
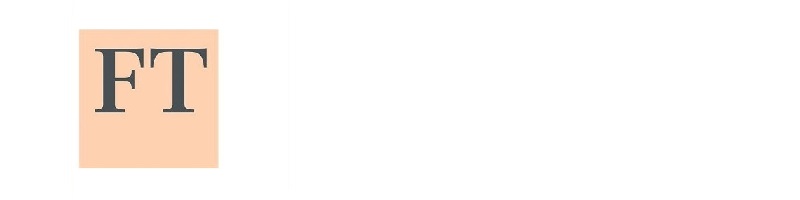
Source: Patrick Mulholland, 09 September 2020, Financial Times. Used under licence from the Financial Times. All Rights Reserved.
Copyright The Financial Times Limited 2020
© 2020 The Financial Times Ltd. All rights reserved. Please do not copy and paste FT articles and redistribute by email or post to the web.