Benedikt Schmidt, Marco Gärtler ABB Corporate Research Ladenburg, Germany, benedikt.schmidt@de.abb.com, marco.gaertler@de.abb.com; David Funderburg ABB Industrial Automation Chemicals and Refining Cleveland, OH, USA, david.funderburg@us.abb.com; Zied M. Ouertani ABB Industrial Automation Chemicals and Refining Mannheim, Germany, mohamed-zied.ouertani@de.abb.com
The Fourth Industrial Revolution promises a massive increase in efficiency through digitization of industrial processes. Initially, the lure of large-scale digital data collection by plant sensors is dizzying – think of the integration of data flows and data availability. But, if Industry 4.0 stops here, then digitization will fall short and those promises of unleashed productivity and increasing top-line will be just a memory. More worrisome, the breath of information available could complicate plant operations. Consequently, workforce efficiency could plummet as employees struggle to integrate data and information into their time-critical work processes. Information overload from chatty applications that complicate operations are well-known, eg, tackling alarm floods can delay the resolution of operational issues. To combat this, industry 4.0 must do more than increase data volume, variety and speed of transmission; it must optimize data access and enrich the information provided by adjusting the knowledge level of data and information supplied. The information needs to remain valid and correct for the domain on the one hand and yet be able to be efficiently applied by the workforce on the other. Leading edge assistance applications are one valuable way to accomplish this. These applications take raw data, from various sources, and service information; this information/data is transformed to a suitable, easy-to-understand, situation-specific, high-quality-form of knowledge for users.
A potential boon for industry, these applications address both domain-specific and technology-oriented challenges as well as the overarching societal changes facing industry: aging workforces, loss of expertise and fears about regrowth. By adapting to the user’s expertise level and domain understanding, assistance applications generate tailored, enriched responses and a positive user experience.
To explore such applications, ABB initiated a research project, in 2018, that focused on the architecture, feasibility and usability of the industrial digital assistant concept. ABB’s result is a research prototype of the Intelligent Knowledge Assistant (IKA) with a customer tested proof-of-concept. IKA is a digital sage, a workforce companion that stands by with advice and action as needed. Rooted in Industry 4.0 infrastructure and recent advances in artificial intelligence (AI), IKA has situational awareness and integrates with the information of industry’s process-specific needs.
Solving challenges with digital assistance
Industries that apply digital solutions observe an increase in heterogeneity and lack of data control; this seeming chaos can translate to high-risk problems. Even though these solutions initially lead to very targeted and isolated systems, complexity increases rapidly; and there’s the rub: Because newly developed systems are connected in networks, users are confronted with dozens of applications and hundreds of databases – an overwhelming situation. The process that initially brings targeted value to a plant or industry morphs into a needle in a haystack of systems and dumbfounds employees who lose the overview →01.
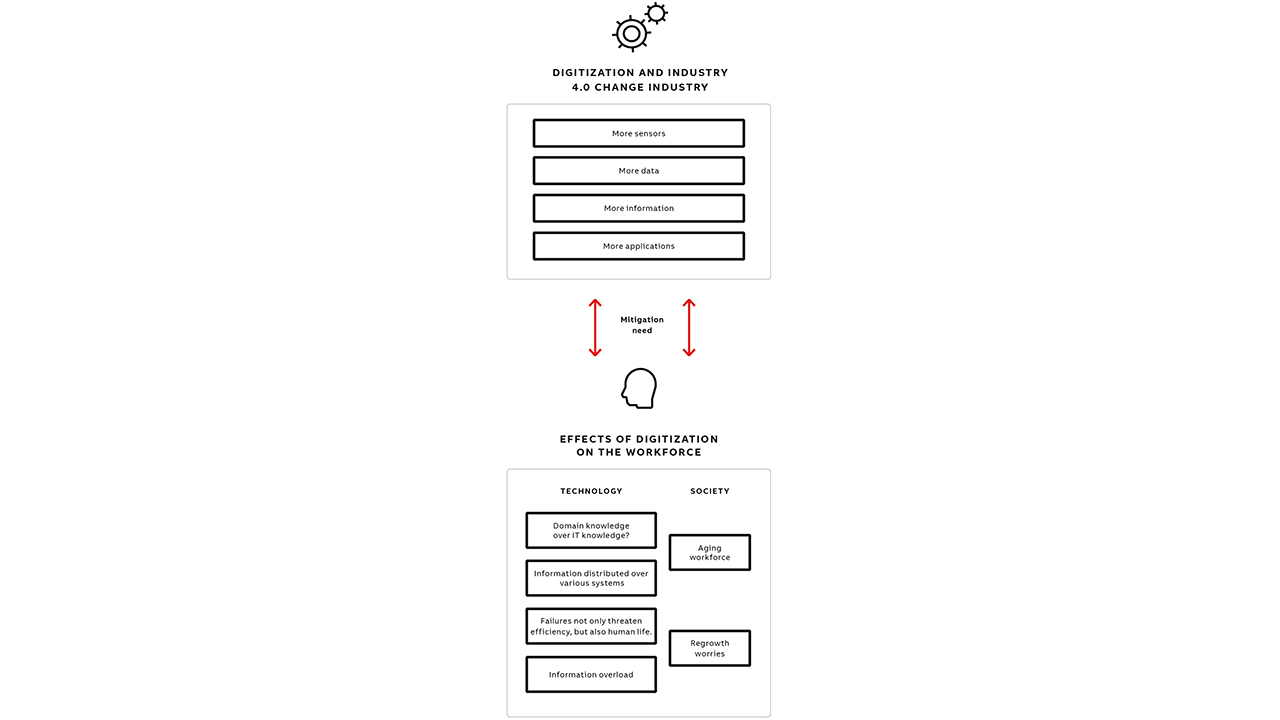
Although most jobs require some basic ability to handle computer programs, just how much expertise is needed is a matter of debate. Clearly, IT knowledge should not supersede domain expertise, especially in industrial engineering and operations. So, industrial software tools target experts and are tailored to domain requirements: usability and user-experience have traditionally played an important role in the design of industrial systems. Examples are the early work of NASA on interface design and cognitive workload [1] or the enduring tradition of designing air traffic controller applications for maximal usability [2]. ABB takes this insight even further.
As a driver of Industry 4.0, ABB grasps the need to ensure safety and maximize efficiency as industries accelerate their digital transformation. Their core values: serving customers and providing product quality, enable ABB to maximize usability and user experience. IKA is ABB’s answer to these needs. This system provides targeted support for the workforce; a diverse population with various competencies who must grapple with an increasingly complex digital infrastructure to ensure the safe and efficient operation of industrial devices and processes.
The rise of integrated assistant systems
With the advent of cheap personal computers in the 1980s, mobile phones in the 2000s and the expansion of smart devices (smart phones, tablets, wearables) over the last decade, digitization is unstoppable. Simple, intuitive and easy-to-use, these products and services target a massive audience of broad competencies. Today, consumer digitalization is a commodity and users have quickly adapted their behavior to reflect this. They expect mutual product integration and ways to create information flows that span multiple components. The digital assistant grew out of this digitalization ecosystem and consumer anticipation.
Nowadays, assistance applications are ubiquitous in the consumer domain: wizard dialogs, static and interactive, help systems. Wizard dialogs guide the user through a set of questions and input options to obtain all necessary parameters to trigger an action. Such digital assistants are common to industrial installation procedures and multi-step workflows, eg, ordering. Static and interactive help systems support users to answer specific questions, educate themselves to achieve certain outcomes or become familiar with services or products. Initially reliant on simple (hypertext) manuals, frequently asked questions, etc., this type of assistant currently introduces scenarios and tutorials that permit walk-through experiences: chatbots and interactive avatars drive the conversation. Consisting of invisible routines that fetch additional helpful information or execute auxiliary steps in the background, these assistants perform spell-checks, auto-completion, filter for inputs and recommendations. Although the immediate benefit of these products and their service usability is considered minor and non-critical, they are crucial for user acceptance and convenience and hence widely available.
An integrated assistant for industry
Can industries more gainfully apply assistance application principles gleaned from the consumer domain? And, if so, how? Clearly there are obstacles. Firstly, an assistance system needs to obtain information from different data sources, background and value-added services and make them available in concise, aggregated and filtered ways to a broad range of applications. Secondly, the system should respect the various domain specific languages and seamlessly translate between them. For example, the type of language used in a process plant is very specific and differs significantly from usual conversational language. Moreover, the type and presentation of the answer should reflect the level of competency and experience of the user. Thirdly, the system should actively notify the user about relevant items that require attention, while simultaneously factoring in the potential information flood from related systems.
The IKA system architecture
IKA is an industrial virtual assistant grounded in consumer domain principles that successfully addresses the aforementioned problems: it is built upon the principle of shared responsibilities; ie, the focus is on the accessibility of fetched, filtered and aggregated information that originate from existing, established services and early prototypes; there is no need to re-implement functionality from the ground up. Monitoring, describing, prescribing and forecasting are all relevant functions in line with the automation pyramid. Moreover, in the foreseeable future, ABB envisions IKA’s functionality to extend further, to the level of control→02.
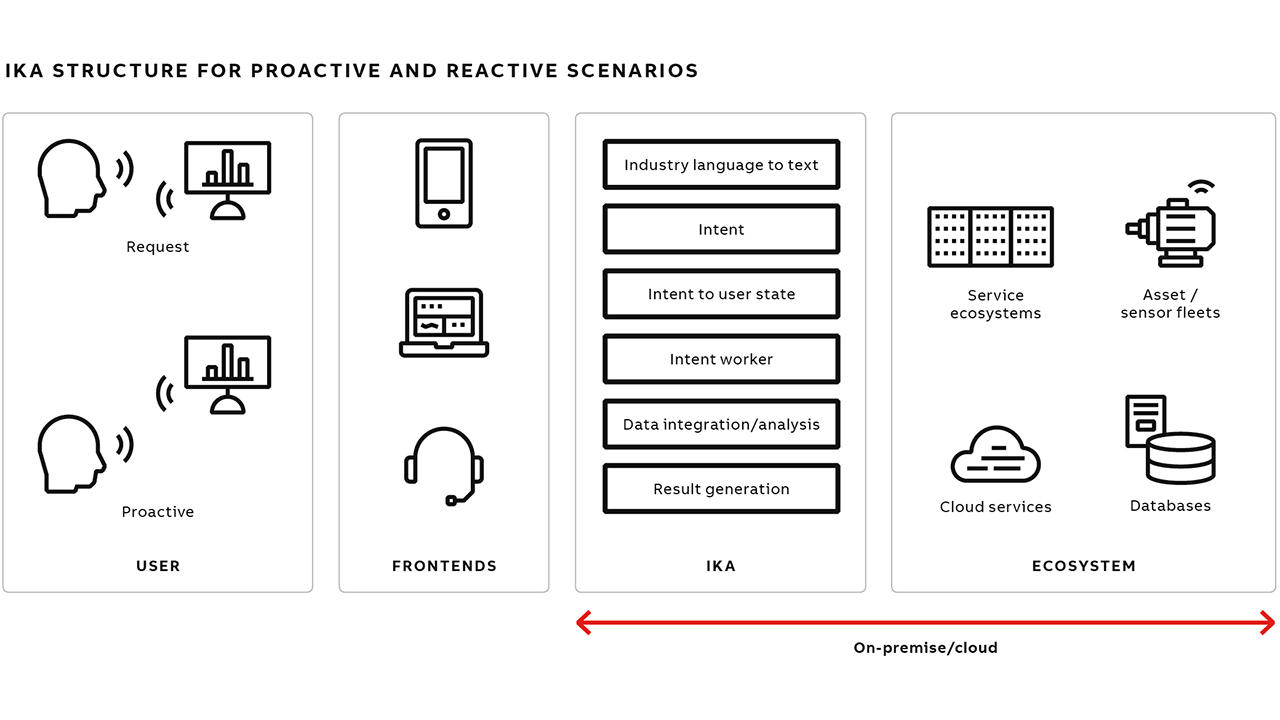
The system receives questions in natural language given in text or spoken form and transforms them to a notation of intents that can be mapped to technical requests. Those queries will be sent to several services that provide a corresponding technical answer. These answers are then filtered and aggregated before they are translated back into natural language. Additionally, images, links and recommendations can be adjusted to further enhance the experience and usability of the textual/spoken answer. Natural language is used in a common and ubiquitous way to express requests and intents intuitively; the user has no need to learn an artificial set of interactions.
On a technical level, the assistant acts as an application programmable interface (API); it focuses requests to a single homogeneous endpoint while internally delegating tasks to the various back-end services. As such, it is represented in a microservice architecture that uses internal components for the natural language part and external components for knowledge retrieval. This design guarantees customers a large degree of freedom; ensures the rapid development of standalone applications, easy integration into existing applications and use in a broad range of platforms, eg, classical desktop, smartphones, tablets, wearables, and augmented reality devices.
Use cases foreshadow a shiny new world
ABB’s IKA system can be deployed in any domain that already has an ecosystem of services and databases or in those that are transitioning to a service ecosystem. For instance, IKA can extend the function of a field engineer executing a process or a company dashboard →01. Because monitoring abilities are embedded, IKA can be readily adapted to realize user support.
03a A view of IKA being employed on a tablet by a field operator (4.0 App). 03b IKA has been integrated into a dashboard specifically for the OGC industry.
03 IKA is currently being integrated into various industrial systems with the focus on the user and ABB’s valuable customer
Use cases demonstrate IKA’s easy and situation-aware data access and decision-supportive properties →03. IKA allows the workforce to focus on tasks using domain language: IKA automatically translates domain-specific language to infrastructure protocols, eg, Distributed Control Systems (DCS), key performance indicators (KPIs), etc. The plant operator simply asks the system about options to handle a specific situation; IKA looks up historical data in the audit trails and operator notes and IKA delivers a reliable answer. If a process variable behaves unusually, IKA proactively informs the operator and asks if a forecast should be displayed. In these cases, the operator focuses on their role – the efficient plant operation – no need to memorize which sub-system analyzes the process status or where to find relevant historical data. Thus, IKA performs the seamless integration of services and information infrastructure into the workflow and work situation. With IKA, users really do “get what they ask for”.
By focusing on user competence, ABB’s system design ensures that IKA services both experts and novices. Experts are not bothered with information they already know by heart and novices can receive a detailed situation explanation and instructions. For instance, a field operator asks IKA to support his/her execution of a maintenance procedure. IKA checks how often the person successfully executed the task at hand. If executed for the first time, more information is provided about success factors and involved equipment. Without a history of successful task execution, the information is limited and focused on the dynamic control system information. And, if desired, the user can always override the system settings to get another support level.
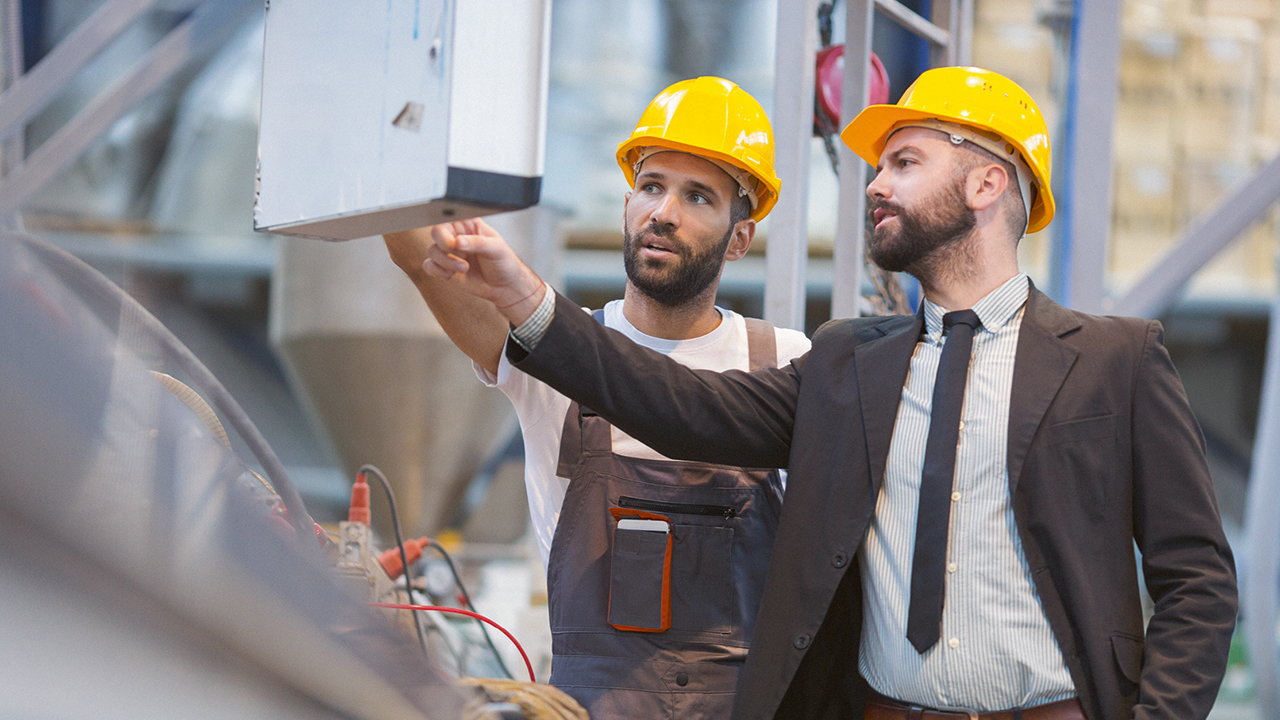
IKA can also improve alarm management. Vital to most process industries [3,4], alarms are customarily monitored by dedicated access applications like terminals or dashboards associated with control system. Alarm information is propagated to the user, an experienced domain expert, irrespective of the current situation, location or workflow. But, alarms are considered standalone objects that require contextualization. Because IKA has situational awareness based on the integration of various data sources, both – near-real time and historical – alarms are aligned with the system and user situation; these can be combined to inspect the related domain and provide much needed decision-support →04–05. In this way, the operator is not only informed that, eg, a pressure value exceeds a threshold, additional valuable information is supplied, eg, the frequency of overshooting the threshold value, and/or hints about ways colleagues previously resolved such events, thus, alleviating confusion.
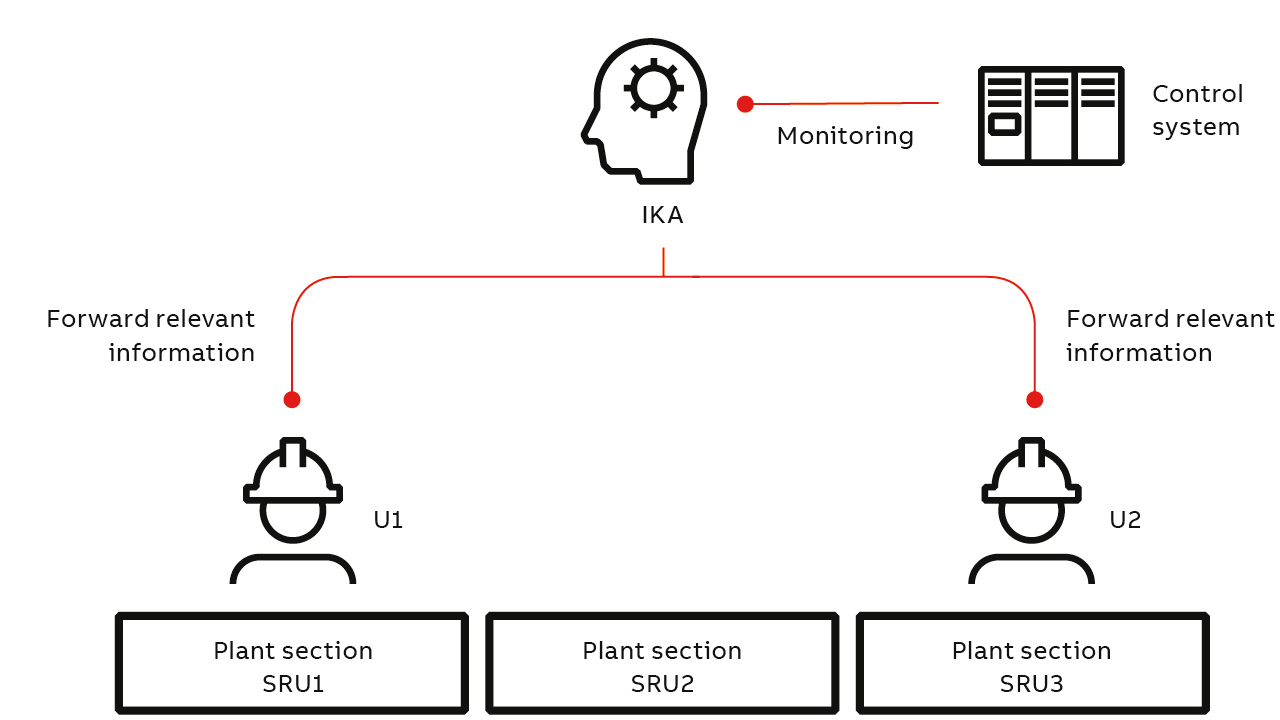
By providing users with easy access to a plant’s evolving information landscape, IKA will allow businesses to heighten productivity and workforce efficiency, thereby keeping the promise of Industry 4.0.
Outlook
Currently, ABB is integrating IKA with existing ABB products and value-added services to conclusively verify the viability of the system. Although preliminary, IKA working prototypes and demonstrators yield encouraging results. Successful customer field tests and trade fair demonstrations, eg, ABB Customer World and CERA week, indicate that ABB is on the right track with IKA – focusing on customers and a digital future.
References
[1] S. G. Hart, et al., “Development of NASA-TLX (Task Load Index): Results of empirical and theoretical research.”, Advances in psychology, vol. 52, North-Holland, 1988, pp. 139 – 183.
[2] D. V. Hopkin, “Man-machine interface problems in designing air traffic control systems”, Proceedings of the IEEE 77, vol. 11, 1989, pp. 1634 – 1642.
[3] N. Li, et al.,“Unravelling events and alarms with data analytics tools”, in ABB Review, 3/2019, pp. 36 – 43.
[4] A. Dagnino, et al., “ABB’s smart alarm system directs plant operators to critical events”, in ABB Review, 2/2020, pp. 28 – 33.