Max Luedtke Global Product Group Manager Mining, Aluminum and Cement, ABB Industrial Automation, Process Industries Baden-Dättwil, Switzerland, max.luedtke@ch.abb.com; Mehrzad Ashnagaran Global Product Line Manager, Electrification and Composite Plants, ABB Industrial Automation, Process Industries Baden-Dättwil, Switzerland, mehrzad.ashnagaran@ch.abb.com; Marcos Hillal Global Product Line Manager, Automation and digital, ABB Industrial Automation, Process Industries São Paulo, Brazil, macos.hillal@br.abb.com
Mining companies face many challenges: easy-to-reach minerals are mostly gone and known ore reserves are dwindling; mines are often in remote locations; and labor and energy costs remain a constant overhead. There are pressures, too, to improve energy efficiency and reduce CO₂ emissions.
To meet these challenges, the mine of the future is envisaged as one that is CO₂-free and autonomous – a safe digital mining enterprise in which every operational detail is connected and which is built around sustainability. ABB already offers comprehensive, integrated solutions across electrification, automation, drives, motors and infrastructure to help optimize the overall performance of mining customers, from mine to port. ABB's digital technology boosts the power and productivity of mines, increases equipment availability and lowers lifetime operating costs by bringing people, equipment and services together. The company is also helping mines go all-electric and maximize energy efficiency by optimizing processes.
Moving toward autonomous mining
Currently, no mine is fully autonomous. Indeed, 100 percent mine autonomy is unlikely to ever be reached and, at present, many mines have only islands of autonomous equipment.
The benefits of autonomous operation in mines are manifold. For example, autonomous technology allows the relocation of personnel from unsafe, polluted and dusty areas to safer places. In the future, fewer people will work in the mine – instead, they will monitor the mine production remotely and more personnel will be located in comfortable centralized control rooms in urban areas, where employees are easier to recruit →01.
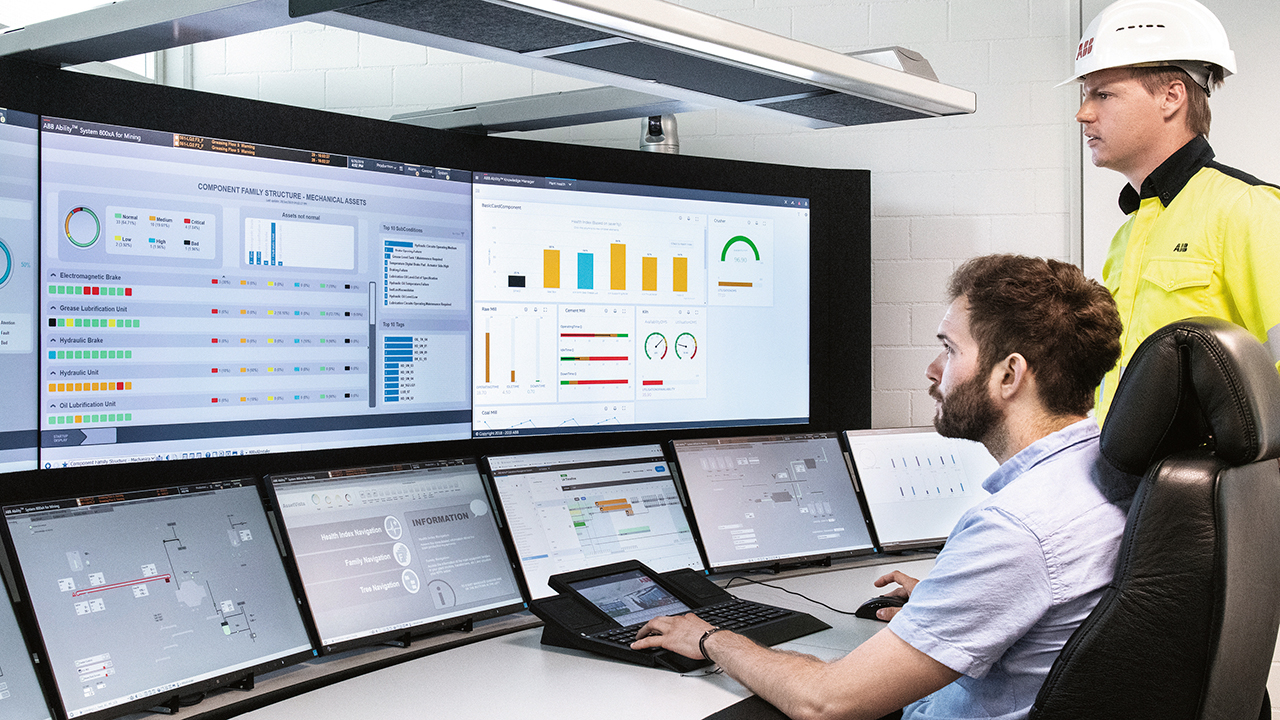
Autonomous operation also supports predictive maintenance, which reduces repair costs and unplanned downtime and can enable process optimization so that CO₂ emissions and resource use (eg, water) are reduced. Autonomous or semi-autonomous equipment is already starting to play a role in drilling and blasting and in the stockyard →02. For example, the stockyard and belt conveyors system at MIBRAG's Schleenhain lignite mine in Germany are automatically operated by an ABB Advant System from a central control room. A recent upgrade to an ABB Ability™ System 800xA migrated all control and drive installations to the latest technology, opening new possibilities of further operational improvements. The two portal scrapers and one stacker at the Schleenhain mine are also operated autonomously and the scope of the project also encompassed drives, instrumentation, auxiliaries, closed-circuit television (CCTV), communication infrastructure and an early version of the ABB Ability™ Stockyard Management System.
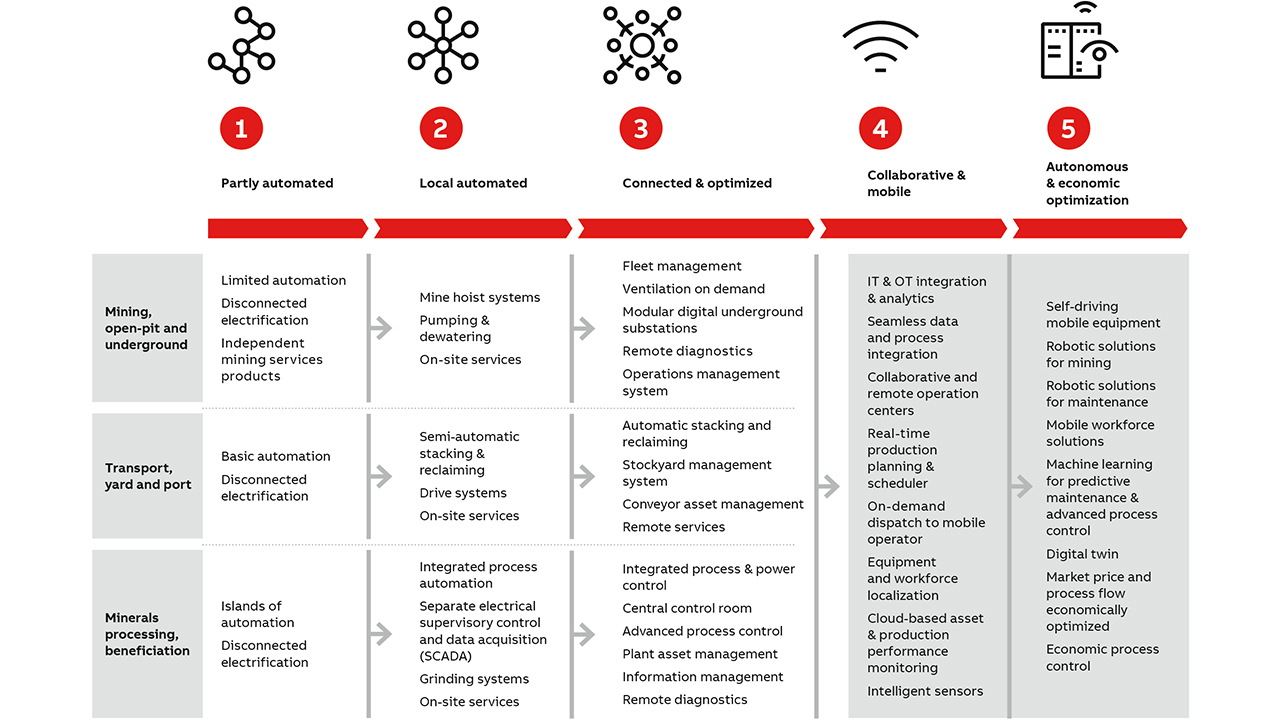
When moving to an autonomous operation like the material handling process just described, collaboration between ABB’s mining and technology experts and customers is essential. Original equipment manufacturers (OEMs) will play an important role, too, as product interoperability and standardization are indispensable.
Technology for mining automation
Innovations in artificial intelligence (AI), machine learning and the industrial Internet of things (IIoT) have the potential to save the mining sector an estimated $373 billion by 2025 by automating machinery operation, facilitating predictive maintenance, improving traceability, harnessing the power of real-time data and analytics, and providing visibility across the mine-to-market value chain [2].
For automation in mining, access to accurate, real-time operational data is key. While such data has always been important, good business decision making now requires a steady input of data from physical assets, factories, plants spread across multiple geographies, industry domains and regulatory frameworks. This data evolution has necessitated the vertical integration of traditionally separate top-down information technology (IT) and bottom-up operational technology (OT) models.
For the modern manufacturer, data has become unified and ubiquitous across the organization – from supply chain management to manufacturing operations to post-sales service – and is one of the most valuable assets it has. Today, data-optimized smart machines and processes can receive input from a wide range of sources to enable more agile manufacturing, improve production safety and efficiency, enable remote and mobile operations and provide greater insight into operational performance. Integrating data from equipment, processes, plants and business systems gives business leaders organization-wide visibility and control. Connected systems can communicate to detect unbalanced load flows and automatically make corrections to prevent outages. Integrating IT and OT is the starting point for the digital enterprise.
Another European mine provides a good example of how data and digitalization can transform a mature mining asset. At this mine, ABB installed a distributed control system (DCS) to integrate data from all critical functions, such as water management, crushing, conveyor belt transportation, skip loading, pumping and the concentrator, into one efficient operation. Round-the-clock remote monitoring services provide access to real-time data about mission-critical equipment, so engineers have the ability to make predictive maintenance decisions before something goes wrong.
A new ventilation-on-demand system, ABB Ability™ Ventilation Optimizer, now recognizes the location of people and vehicles in the mine and delivers fresh air where needed →03. Ventilation Optimizer can deliver up to 50 percent ventilation energy savings (40 percent reduction of ventilation energy consumption at the mine mentioned). It also improves safety in case of fire by, for example, preventing the spread of smoke and enabling faster fume expulsion. Ventilation Optimizer easily accommodates additional fans, or fans that are temporarily moved to where they are needed most. In another mine, Ventilation Optimizer made ventilation energy savings of 54 percent, plus air heating energy savings of 21 percent, during its first year of use.
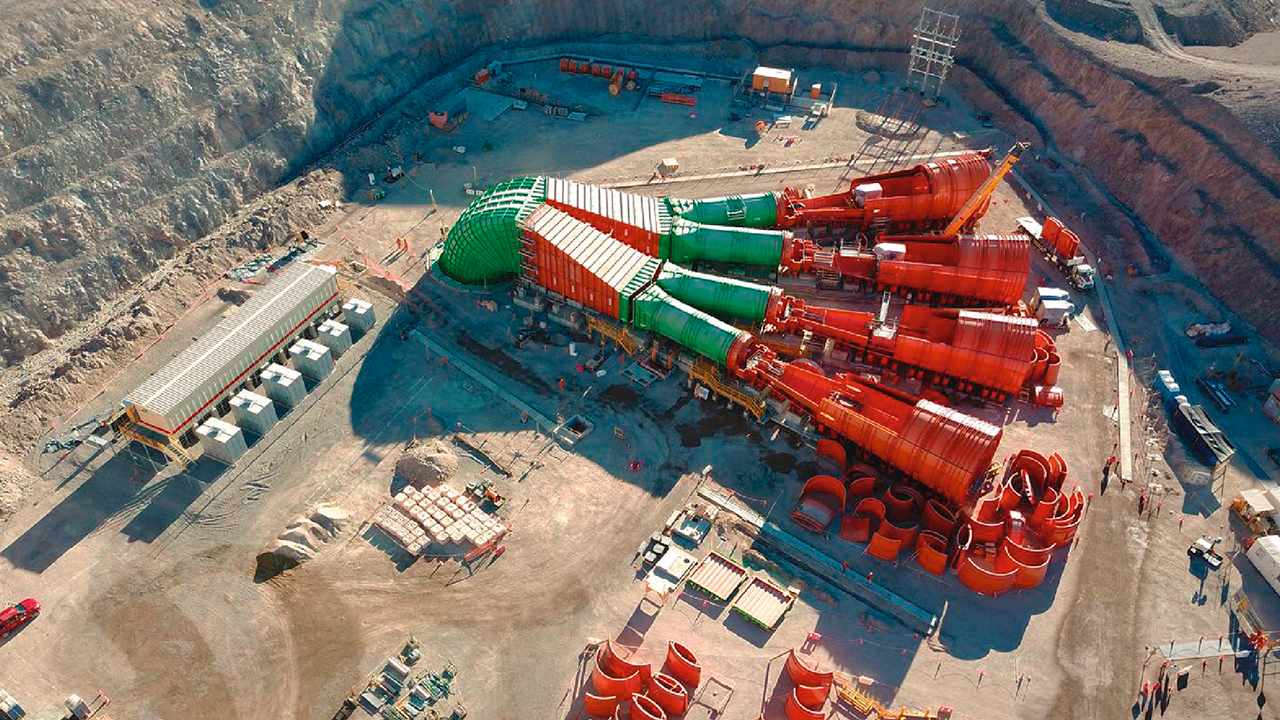
As mining becomes increasingly automated and digitalized, cybersecurity becomes critical to the running of the business. For this reason, companies need to embrace a cybersecurity framework, including the functions Identify, Protect, Detect, Respond and Recover, which is a way to provide proactive safeguards along with preparing for worst-case scenarios. ABB Ability™ Cyber Security Fingerprint covers the Identify function as the service identifies critical control system vulnerabilities at mining facilities by focusing on three areas: procedures and protocols; group security policies; and server and workstation settings. The solution combines information from an ABB control system with insights gained from interviews with working personnel. The solution then generates a detailed report on gaps in the enterprise’s existing cybersecurity measures and uses an analytics tool to compare the results with recognized industry standards. Utilizing this tool, a company can reduce vulnerabilities, and implement a focused and sustainable security strategy.
The age of all-electric mines
As mines step up their efforts to cut costs and increase efficiency, the supply of energy emerges as one of their biggest challenges. On top of the expense of delivering diesel fuel to remote sites, come also costs for the service, repair and replacement of diesel-powered vehicles. Moreover, mining is an energy-intensive industry and falling ore grades require more energy to be expended per ton of end product extracted. Tighter commodity prices narrow margins yet more. Further, rigorous standards apply to the allowable levels of air pollutants in mines – for example, diesel particulate matter, total carbon, elemental carbon and nitrogen dioxide. Compliance with these standards incurs mitigation costs.
Electrification can help alleviate this situation. For example, electric vehicles (EVs) not only produce zero emissions but also produce less waste heat, thus reducing cooling costs. By 2028, it is expected that mining operations will employ over 30,000 EVs (hybrid and pure electric), with a market value of $9 billion [2].
Such electrical assets, when connected to digital and automation systems, can monitor and control processes so that operations and energy usage can be optimized and made more sustainable.
In one particular copper mine, ABB’s electrification and automation efforts involving an electric trolley assist system for mine trucks help to save 830 m³ of diesel annually and reduce greenhouse gas emissions by 80 percent with a 700 m test lane and 2,700 V DC, 10 MW rectifier station →04. Four trucks, each rated at 4.5 MW (all four trucks will not run at the same time), are equipped with pantographs. Other benefits include improved local air quality, reduced production cost, less engine maintenance, higher velocities (almost double those of diesel vehicles), fewer trucks are needed, and reduced noise, vibration and cycle times.
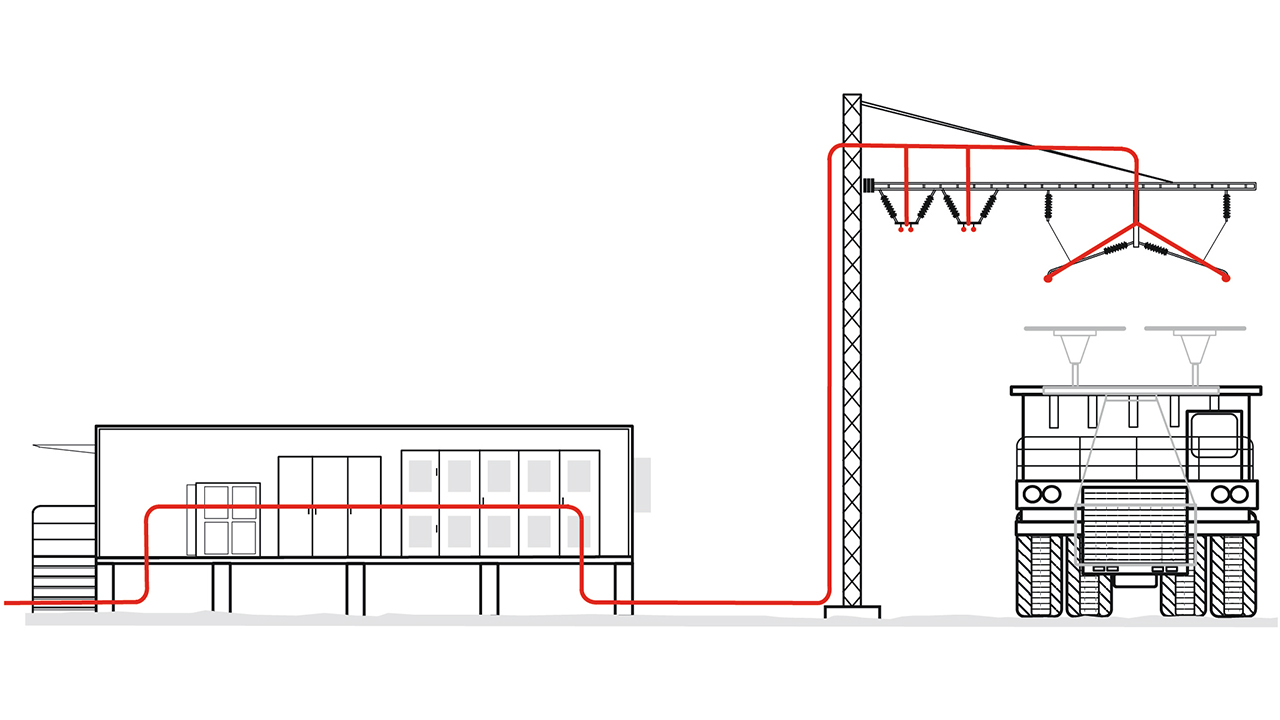
Digitalization, electrification and automation for mining
Digitalization, electrification and automation are helping the mining sector meet the challenges of declining ore resources, remote locations and rising labor and electricity costs. These technologies also help miners improve overall energy efficiency, reduce CO₂ emissions and thus operate in a more sustainable manner. ABB’s comprehensive and integrated offering – called ABB Ability™ MineOptimize – covers from electrification all the way to digital solutions and enables mining companies to achieve productivity and sustainability from mine to port →05.
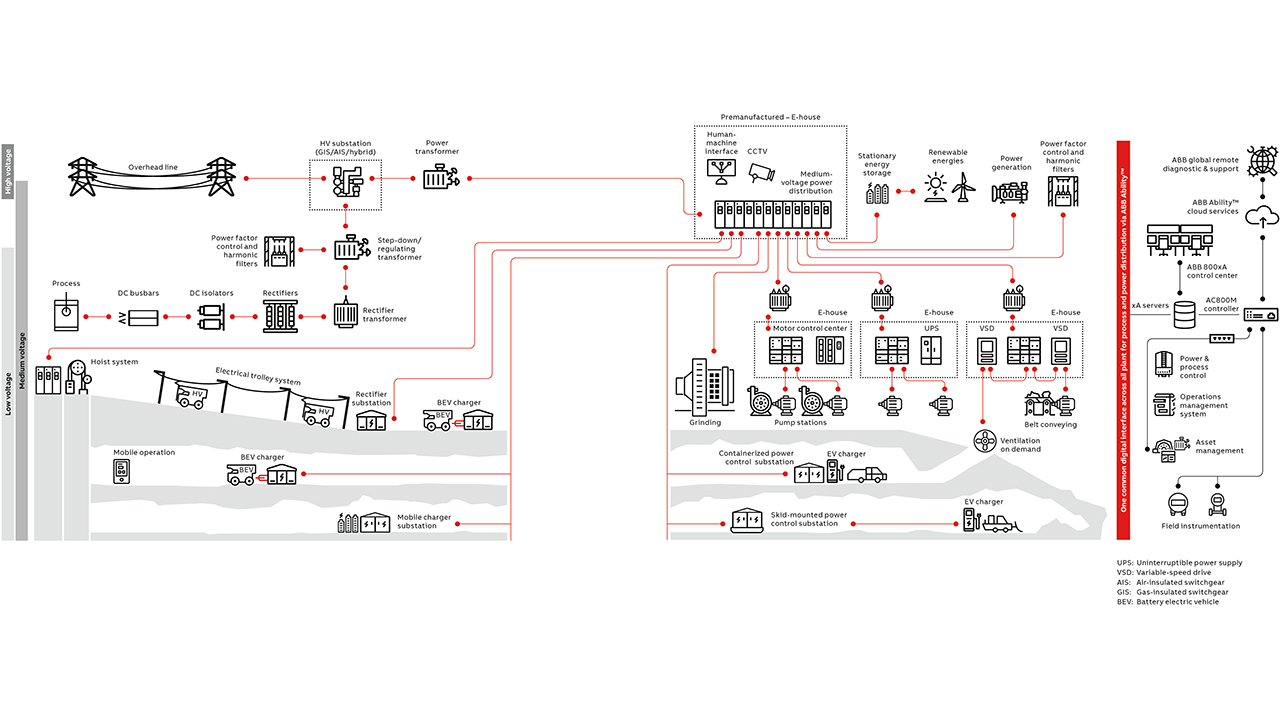
References
[1] McKinsey & Company, “How digital innovation can improve mining productivity,” November 1, 2015. Available: https://www.mckinsey.com/industries/metals-and-mining/our-insights/how-digital-innovation-can-improve-mining-productivity. [Accessed July 7, 2020].
[2] A. Atak, “Electric vehicles for mining will be a $9 billion market in 2028,” May 3, 2018. Available: https://www.idtechex.com/en/research-article/electric-vehicles-for-mining-will-be-a-9-billion-market-in-2028/14214. [Accessed May 28, 2020].