Located in Victoria, ABB Australia Robotics Value Provider Automation Innovation has developed a new turnkey robotic cell laser cleaner that incorporates artificial intelligence and robotic automation as an answer to manufacturers’ needs for a safer, environmentally friendly, and more economical solution to cleaning glass moulds.
In 2020, the glass and glass product manufacturing market size in Australia reached $4.2 billion. It’s grown 2.1% in the last five years. Glass and glass product manufacturing in Australia as an industry continues to increase faster than the Australian manufacturing sector overall. The growth is attributed to increasing investments in building construction, and a heightened awareness of glass as a more sustainable material in comparison to plastic. Glass is also fully recyclable, and lasts several years longer than plastic, which gives the material its conspicuous environmental appeal.
The art behind glass cleaning and raised concerns
Glass moulds are used in the manufacture of these products and are made up of interlocking parts, small features, and pinhole-sized cooling vents. In glass bottle manufacturing processes, lubricant is used to help release the glass from the mould. This paves the way for surface contamination to build on the mould which causes product quality issues and requires frequent residue removal every one to two weeks.
When it comes to contaminant removal, methods include ultrasonic (often with the use of chemicals), bead or dry ice blasting. This is then followed by a manual hand polish and re-machining of the mould to remove surface imperfections which is caused by the physical cleaning.
Automation Innovation recognised the safety concerns for employees in this manufacturing space and their exposure to cleaning chemicals, as well as the substantial loss in operating costs for manufacturers because of outdated cleaning processes.
This led Automation Innovation to embark on their own research to understand a more advanced way in which they could help glass manufacturers intelligently run their mould cleaning operations, particularly over large product production volumes.
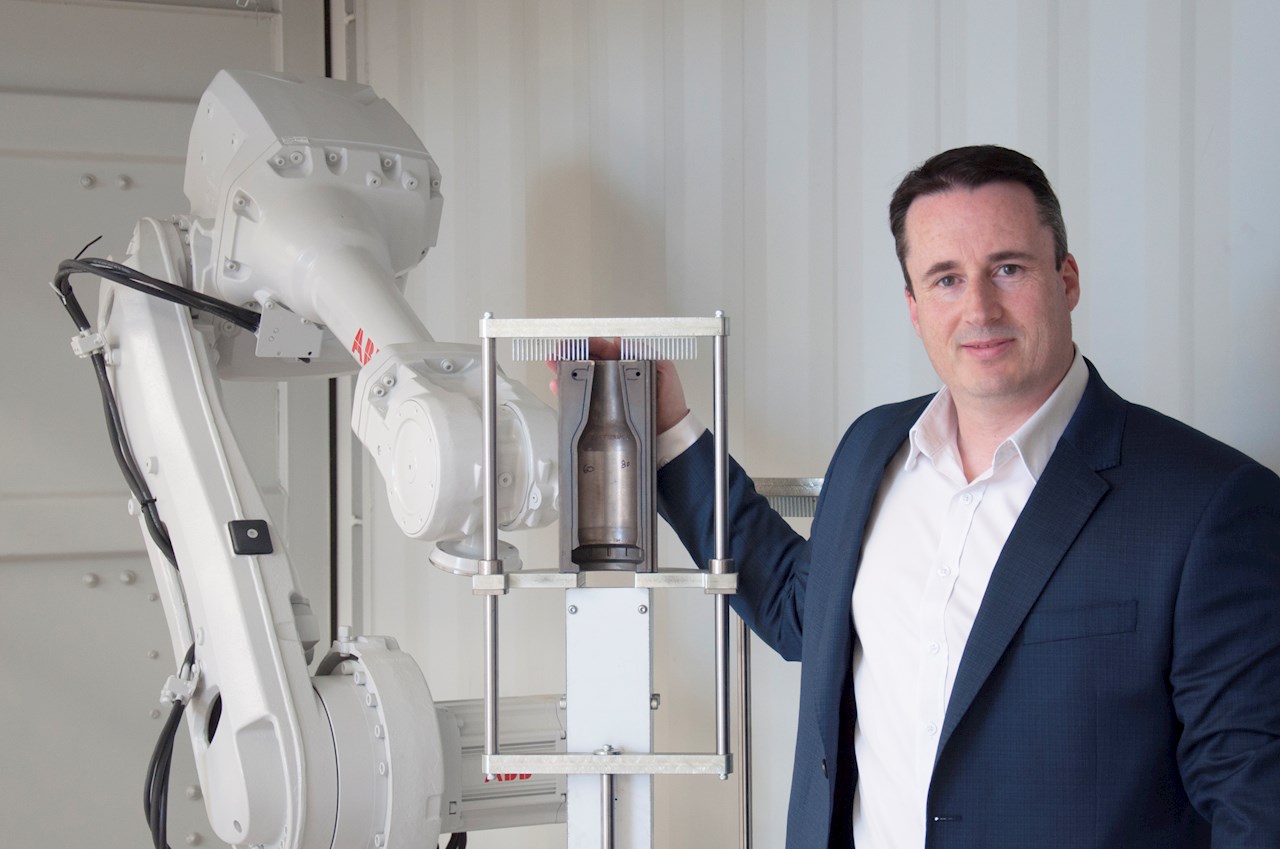
Laser cleaning for a greener, intelligent, cost-efficient alternative
Automation Innovation has developed the AiMC-1000. It’s an automated robotics cell which delivers superior glass mould cleaning. The AiMC-1000 incorporates ABB’s IRB 4600-60 industrial handling robot and the IRB 4600-45 laser robot, to deliver a safer, chemical free, and repeatable cleaning process. This is currently unattainable using traditional techniques.
The AiMC-1000 utilises a higher intensity laser light to clean the surface of the moulds, ensuring that only the surface contaminant is removed, with minimal damage to the parent mould material.
The AiMC-1000 utilises a higher intensity laser light to clean the surface of the moulds, ensuring that only the surface contaminant is removed, with minimal damage to the parent mould material. It facilitates 24/7 operational environment, increased daily clean volume, lower replacement costs, removal of additionally required materials, and the discontinuation of the use of chemicals which avoids harmful environmental impacts.
Serious occupational health and safety concerns for workers are also minimised with the reduction of manual handling, and elimination of the need for mildly radioactive ceramic beads used in other cleaning methods, as well as exposure to noxious fumes which are now securely contained.
Increasing product output and quality with artificial intelligence and 3-D scanning
A true adaptation of Industry 4.0, the AiMC-1000 features software that can be linked with mould management systems and supports remote monitoring and reporting. The entire process is controlled by a single operator, who places and receives trolleys to the loading area. Robotic arms are required to handle the movement of the moulds and manipulate the laser head in order to accomplish the most optimal cleaning finish. This is important because glass moulds have specific needs when it comes to cleaning. Base material should not be degraded as that leads to an increase in the volume of mould and the amount of glass needed to fill it. Closing edges must be preserved to ensure no burrs are introduced to the logo imprint area. The pinhole-sized cooling vents that release air need to be strategically cleaned without leaving residue behind.
Example of glass mould The bottle manufacturing process Glass bottles about to enter moulds Working with 3D camera technology Process control trolley working with ABB robots Laser cleaning in action AiMC's laser mould cleaning container ABB robotic arms handle the movement of the moulds ABB's IRB 4600 robot
It’s an art and a science, and thanks to the AiMC-1000, glass and glass product manufacturers can experience precision cleaning, product quality improvements, consistent reliability and the certain prevention of mould growth. Aesthetically pleasing, their logos can also now remain crisp and clear.
Sophisticated technology integrating 3-D cameras are used with patented software algorithms to live scan data and cleaning parameters and allow them to be changed as needed. By manipulating the laser characteristics, it’s pulse energy and frequency, the amount of material removed by a single laser pulse can be controlled with recorded accuracy. Contaminants are vaporised from cavities and channels leaving absolutely no residue.
Optional Artificial Intelligence (AI) capabilities of this system can also be a major benefit. For all AiMC-1000 machines around the world, data is scanned for each mould cleaning process. This data can then be delivered to the cloud, where it goes through an AI processor. Using this information, the algorithm becomes more defined, and smarter each time. That data is then delivered by the Internet of Things (IoT) to other machines across the network ensuring only the highest of standards.
For glass and glass product manufacturers, the AiMC-1000 gives them a completely autonomous and future-proof cleaning system. With no chemicals or excess waste, automated robotic laser cleaning has become the more cost-effective, green alternative to traditional cleaning methods. Mould lifespan substantially increases as mould growth is eliminated which helps to lower replacement costs. Industry 4.0 integration capabilities ensures manufactures will be able to remotely manage their operations and assets to keep them at the forefront of their industry.
ABB (ABBN: SIX Swiss Ex) is a leading global technology company that energizes the transformation of society and industry to achieve a more productive, sustainable future. By connecting software to its electrification, robotics, automation and motion portfolio, ABB pushes the boundaries of technology to drive performance to new levels. With a history of excellence stretching back more than 130 years, ABB’s success is driven by about 110,000 talented employees in over 100 countries. www.abb.com