Cellier, Blending and Formulation Solutions, part of ABB France, has brought to the market the High Viscosity Drum Decanting System, designed to pump and dose highly viscous liquids stored in drums and incorporating them into the formulation process.
Widely used in the chemicals industry to store high-value raw materials and additives, drums and barrels regularly require emptying, dosing, and rinsing. Increasingly, the materials being kept within have a high viscosity level.
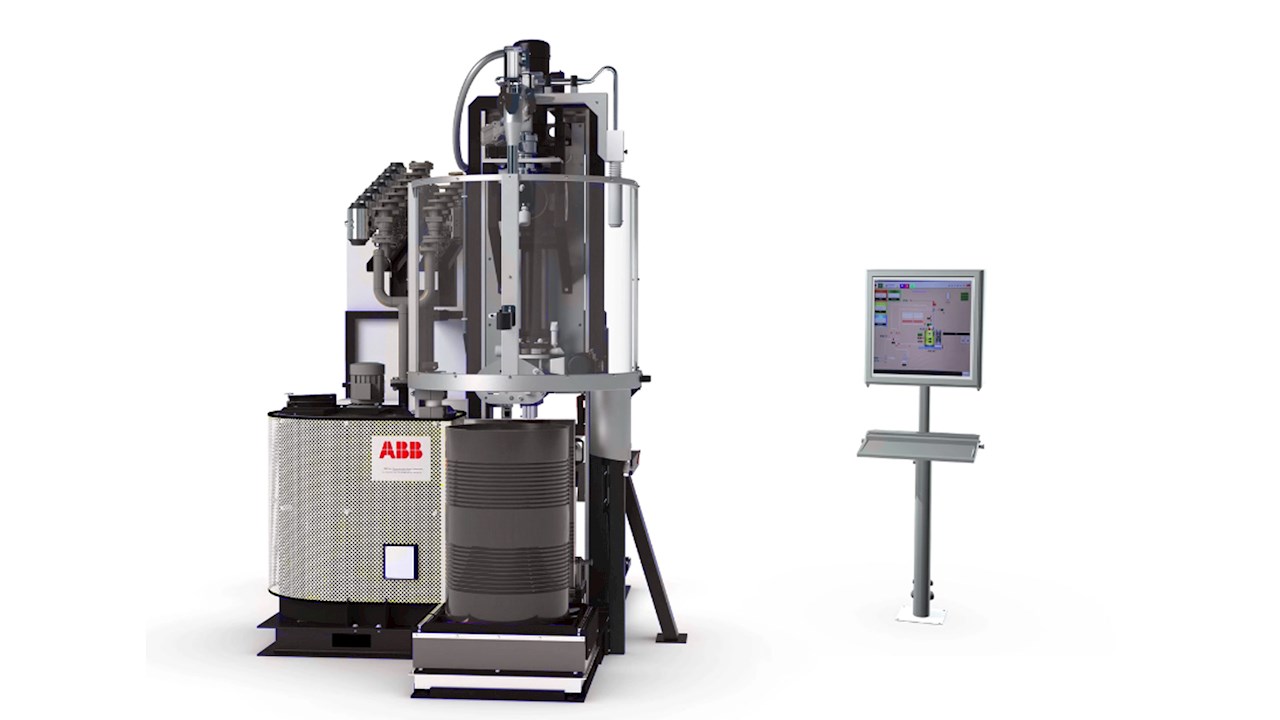
Nicolas Vairyo, R&D Technology Manager Cellier B&F solutions in ABB said: “Viscosity determines how well the mate-rial will flow in production and transportation. Sticky and thicker materials are harder to pump which makes the decanting process longer, more energy intensive and impacts the production process cycle time. The Drum Decanting process re-mains largely manual and in order to break down the viscosity, drum ovens are used. Reaching extremely high tempera-tures these can be dangerous to operate, can damage the chemicals’ properties and have an impact on plant energy consumption.”
ABB’s High Viscosity Drum Decanting System is an automated station designed to increase pumping capacity of highly viscous products by up to 20,000 centistokes and to reduce operator drum handling time by 50 percent. Immediately after pumping is completed, materials are automatically transferred via pigged lines to its required destination.
Roger Gabriel, HSE Manager B&F solutions in ABB commented: “Worker safety is paramount in this process and we have worked hard to ensure operator exposure to hazards is nil. As part of our system, we have developed a screen barrier as well as incorporating a camera into the machine casing which acts as a virtual “safety perimeter” around the machine. If this safety perimeter is crossed while the machine is processing, movement and action are automatically stopped.”
Incorporating a high-pressure rinsing nozzle for cleaning the drums after use, and by automating the entire decanting process, ABB ensures reduction of waste by up to 90 percent, removing any residual quantity in the drums, minimizing cross contamination of pumped products and recycling effluents in the production cycle.
Supplied with an operator terminal for recipe management, the system also ensures accurate dosing within 0.2Kg, which increases first pass yield (FPY), driving up product quality by adding the exact dose required the first time.
ABB Energy Industries is enabling safe, smart, and sustainable projects and operations for businesses across the oil, gas, chemicals, life sciences, power generation and water sectors. Driving integrated solutions that automate, digitalize, and electrify industry we connect our people and technology to help our customers adapt and succeed. With over 50 years do-main expertise, we continue to innovate and reshape traditional approaches across the energy sector with our technologies designed to improve operational efficiency, reduce risk, reduce energy consumption and waste.
ABB (ABBN: SIX Swiss Ex) is a leading global technology company that energizes the transformation of society and in-dustry to achieve a more productive, sustainable future. By connecting software to its electrification, robotics, automation and motion portfolio, ABB pushes the boundaries of technology to drive performance to new levels. With a history of ex-cellence stretching back more than 130 years, ABB’s success is driven by about 110,000 talented employees in over 100 countries.
www.abb.com
For more information, please contact:
ABB Media Relations
Sarah Andrews
Global Marketing Communications Manager
Energy Industries
Phone: +1 919 413 2556 Email: sarah.andrews@us.abb.com
ABB Ltd
Affolternstrasse 44
8050 Zurich