Neste is the world’s largest producer of renewable diesel and renewable jet fuel refined from waste and residues, and a forerunner in introducing renewable solutions to the polymers and chemicals industries. The company is also a technologically advanced refiner of high-quality oil products.
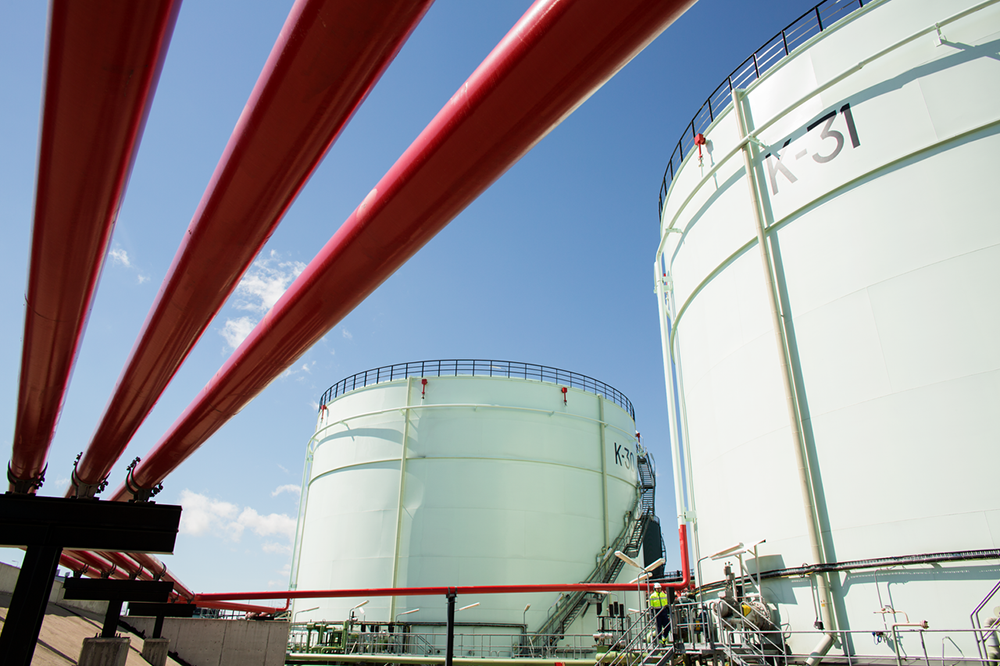
Neste's Porvoo refinery is located in the Kilpilahti industrial area in southern Finland. With highly automated production, the state-of-the art facility is one of the most advanced in Europe. The refinery processes approximately 10.5 million tons of crude oil every year, or 206,000 barrels per day. In addition to crude oil, the Porvoo refinery receives other raw materials for a total production capacity of 13.5 million tons per year. The refinery also includes two process units that manufacture renewable diesel.
Porvoo's aboveground and underground tanks have nearly eight million cubic meters of storage capacity for raw materials and refined products. Neste's port in Kilpilahti is Finland's largest by tonnage, and the port is visited annually by 1,100 to 1,400 vessels.
ABB systems at the core of production
Automation is a central part of modern oil refining processes. Neste's Porvoo refinery operates four production lines that include approximately 30 different process units.
Process data is relayed from the refinery's automation systems to the TOP process information system, which is provided by ABB. The TOP system is used in optimizing the total production of the entire refinery. It combines data from multiple automation systems and provides a complete view of the oil refining processes of the facility. TOP also includes high-level control applications, and it provides process data from production to Neste's other IT systems, where it is utilized by over 1,000 users. IT security is a key part of the system architecture at every level.
The system to be upgraded was originally delivered by ABB in the mid-1980s. Over the years, the TOP system had been updated, expanded and maintained, but the solution was coming to the end of its service life.
"The limitations of the old system were beginning to limit our operations. We were getting close to reaching the physical limits of the legacy database," recounts Janne Penttinen, System Manager, Neste.
Neste purchased the planning, implementation and support services of the project from ABB as a total offering. In the upgrade, the functionality of the old system was transferred to the ABB Ability™ History process data management platform, which enables flexible scaling of the solution in the future. The agreement also includes ongoing support of the system.
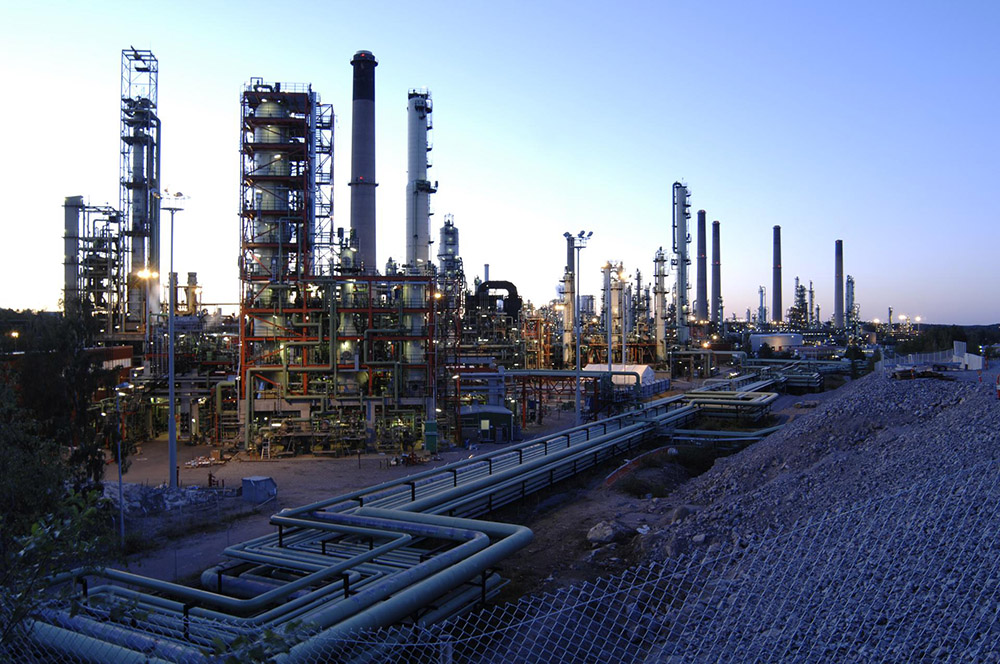
Demanding system update
Neste's TOP process information system is critical to the operation of the Porvoo oil refinery, and it differs significantly from traditional ICT systems. The key benefit of the solution is providing a unified view of the process data of all automation systems, and TOP also provides control setpoints to automation systems from multiple vendors across the refinery. Fast and logical usability of the system is extremely important for the day-to-day operations of the facility.
"In an oil refinery, errors in process control can lead to interruption of production or even physical injury, whereas mistakes in ordinary ICT systems typically only lead to lost data at worst," says Jouko Karjalainen, Senior Sales Manager, ABB. "For this reason, the update of the TOP system had to be considered primarily from the perspective of an industrial automation system and not an IT solution."
From the beginning of the project, it was specified that the TOP update would be carried out at the refinery without any interruption or disruption to production, making the upgrade an exceptionally challenging project. In the upgrade, the focus was on maintaining existing functionality while modernizing the underlying IT architecture. The delivery includes new computing and networking equipment, and involved migrating the system from the HPE OpenVMS platform to a Microsoft Windows environment.
Long-term collaboration
Neste has years of experience working with ABB. The original TOP system was designed as a collaboration between ABB and Neste as far back as 1986.
"A familiar, experienced project team was a key factor in our decision to continue developing the system with ABB," says Janne Penttinen from Neste. "ABB's strong local presence in Finland made the work much easier, especially in the more laborious project phases such as transferring process diagrams."
Careful advance planning was essential for the success of the project. A key part of the design work was defining Neste's exact needs for the process information system, and deciding which functionalities would be migrated from the old system and which would be rebuilt. Coordinating the project required extensive communication and scheduling so that each upgrade step could fit into the current production situation.
During the update project, the new servers was brought online alongside the old installation, and production units were brought under control of the new system one at a time. The project included over 50 system interfaces that needed to be updated.
"The project also offered us numerous opportunities to modernize our processes. The TOP system is a key part of our production, and the upgrade will future-proof our operations for a long time to come," says Team leader Jukka Viertorinne from Neste.
Multi-layered IT security
In addition to usability, the system upgrade had a strong focus on cybersecurity. "From a technical perspective, the project comprised two major updates. TOP was migrated from the old OpenVMS operating system to a Microsoft Windows environment, and the security architecture of the system was revamped thoroughly," says TOP project manager Harri Klemetti from ABB.
The updated system is based on a segregated, multi-layered security architecture in which all interfaces between equipment and software are protected by powerful, modern firewalls. The system also serves as a cybersecurity buffer between production at the refinery and Neste's other IT systems.
"TOP is not only an information system, but it also takes part in controlling the actual production process at the refinery by feeding setpoint values to various systems. For this reason, it is critically important to ensure the faultless operation of the system," says Klemetti. "In addition to the strengthened cybersecurity architecture, the system utilizes several existing IT security products in addition to ABB's proprietary tools for user interface and database management. The security of the solution has been strengthened further by the adoption of the OPC UA machine-to-machine communication protocol as well as encrypted network connections within the system."
Flexibility for future production
Team leader Jukka Viertorinne from Neste has been very satisfied with ABB's work on the project.
"The ABB team was always there to help us quickly when needed. Of course there were some challenges along the way, but this is to be expected when upgrading such a large, critical system in the midst of production. With the exception of a few minor issues, the system update went very smoothly. ABB's project team took any problems very seriously and they were always on top of their game. Long experience leads to assurance."
In a rapidly changing business environment, process industry companies must optimize and manage their processes more efficiently and precisely than ever. Viertorinne expects that over the next several years, Neste's Porvoo refinery may need to update its production models over shorter timeframes than before. Neste's business units will also benefit from new insights gained from analysis of production data.
"We need to have flexibility and agility to modify the system, and it is very likely that we will be developing our data analysis tools further over the upcoming years. The upgraded TOP system has already given us greatly improved trend monitoring tools, which has made it much easier for us to monitor our production units."