ABB is expanding its collaborative robot portfolio with the introduction of the new 6-axis GoFa™ CRB (Collaborative RoBot) 15000, to support the growing demand for a collaborative robot capable of handling heavier payloads to enhance productivity and flexibility.
Designed to safely work directly and continuously alongside humans and to be very easy to install and use, GoFa will help businesses automate processes involving heavier loads and longer reaches to assist workers with repetitive and ergonomically challenging tasks.
With a class-leading reach of 950mm, and offering speeds up to 2.2 meters per second, GoFa offers an effective solution for a variety of applications, including material handling, machine tending, component assembly, packaging and inspection*, as well as laboratory automation.
GoFa incorporates a range of features that allow it to be used directly alongside human workers without the space and expense associated with physical barriers or fences. Enabling a robot and human to continuously share the same workspace and cooperate on the same tasks, without jeopardizing speed and safety, allows for maximum flexibility and efficiency.
GoFa features intelligent torque and position sensors in each of its six joints to offer superior power and force limiting performance. These joints eliminate the risk of injury to human workers by sensing any unexpected contact between the cobot’s arm and a human to bring the robot arm to a stop within milliseconds.
GoFa and SWIFTi™, the new collaborative version of ABB’s IRB 1100 industrial robot, will both be available from February 24 2021, and together they are the next generation of cobots from ABB, joining YuMi® and Single Arm YuMi® to create an industry-leading cobot portfolio for applications ranging from from less than 0.5kg to 5kg.
Image currently unavailable
Image currently unavailable
Image currently unavailable
Image currently unavailable
Image currently unavailable
Image currently unavailable
Image currently unavailable
Image currently unavailable
Image currently unavailable
Image currently unavailable
Image currently unavailable
Image currently unavailable
“Our new GoFa cobot builds on the success of ABB’s YuMi family, which has been helping businesses safely automate key tasks since YuMi launched in 2015. With its greater payload capability and class-leading reach and speed, GoFa is a gamechanger for collaborative robotics. It will significantly expand the potential for cobots globally, by safely and accurately supporting a range of new tasks and applications,” said Andie Zhang, Global Product Manager, Collaborative Robotics for ABB Robotics.
Pronounced ‘go-fa’, GoFa is designed to help businesses ‘go further and do more’ with a robotic helping hand. With a payload 4.5 kg higher than YuMi, GoFa unlocks opportunities for both new and established users, from SME’s to larger companies, by enabling easy automation without the need for in-depth programming skills or prior training.
Users can easily program GoFa via lead-through programming and ABB’s new Wizard easy programming software. Based on simple graphical blocks, Wizard makes it easy for non-specialists to automate their applications. The blocks represent actions such as ‘move to location’, ‘pick up an object’, and ‘repeat task’, making it easy and intuitive to build a series of simple processes for the robot to perform.
“With their ease-of-use digital tools, integrated safety features and higher payloads, our new cobots represent the future of human and robot collaboration. This next generation will enable even more businesses to automate repetitive, mundane and dangerous processes, to enhance productivity and flexibility while leaving employees free to do more value-add activities,” added Andie Zhang.
Every ABB cobot installation includes a start-up package that provides ABB Ability™ condition moni-toring & diagnostics as well as a support hotline free for the first six months to access ABB’s expert technical assistance, which is offering support across all industry segments.
Key features
- 5kg payload and 950mm reach.
- Max Tool Center Point (TCP) speed up to 2.2 meters per second (the exact safe collaborative speed may be lower, as it will depend on the specific application, tooling, payload etc. Users can refer to the SafeMove Configurator App for a recommendation. Users should always carry out a risk assessment of their application).
- Small footprint, lightweight manipulator and ability to mount in any direction (wall and floor mount etc.).
- 6-axis agility.
- Standard flange on axis 6.
- Cobot label and white/gray color scheme.
- Integrated joint design with torque and positioning sensors in each of GoFa’s six joints for superior power and force limiting to offer safe contact with humans.
- Interaction status light to communicate cobot status - white (standby)/ green (running production) / yellow (programming) / red (stop).
- SafeMove Configurator app on the ABB FlexPendant.
- Powered by OmniCore™ controller with best-in-class motion control functions.
- PL d certified safety functions built in. Safety certified PL d Cat 3.
- IP54 protection.
- Ease of use: quick calibration and configuration.
- Ease of use: Wizard Easy Programming.
- Ease of use: Lead-through programming by ‘grabbing’ anywhere on the robot.
- Ease of use: Arm-Side Interface (ASI) on axis 6.
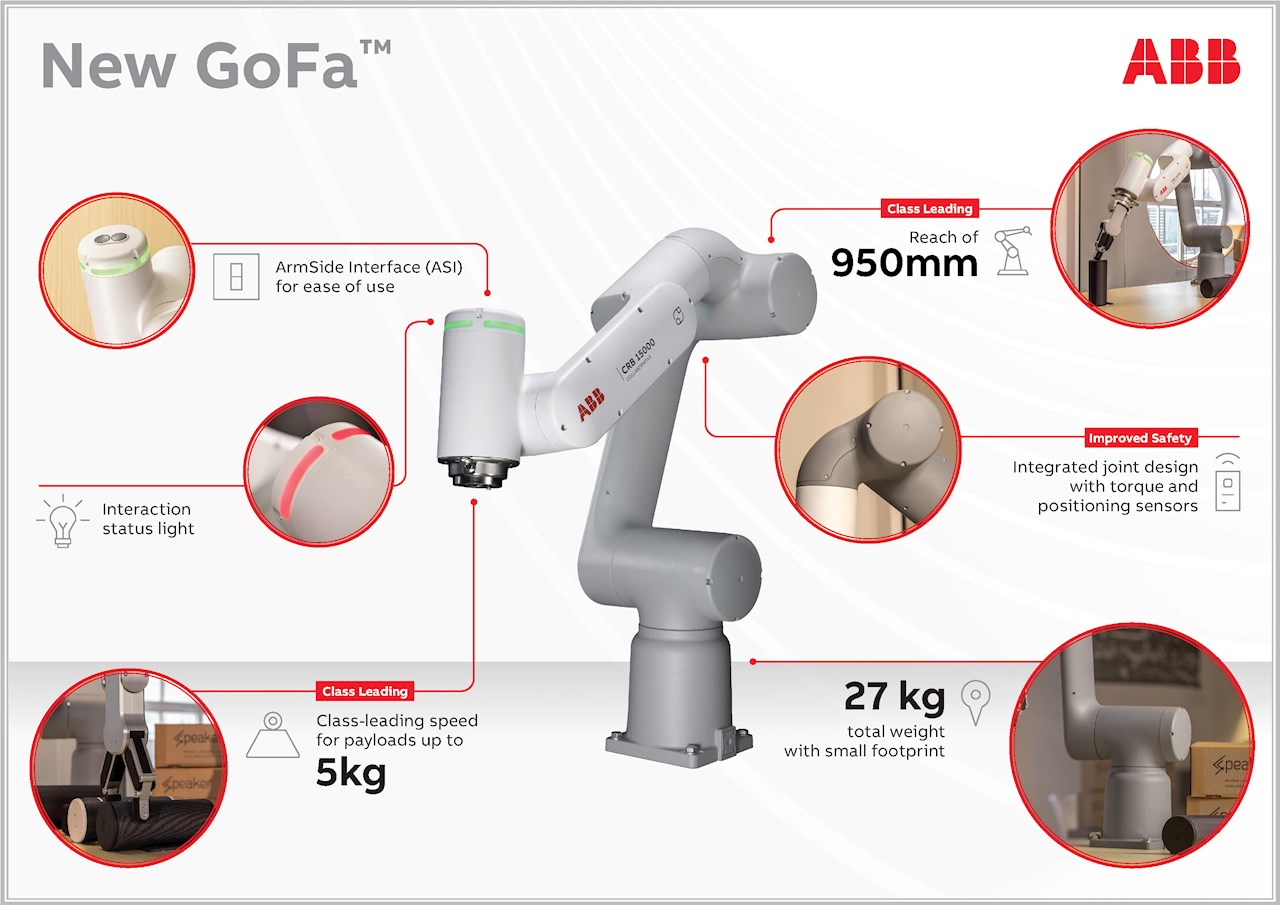
1. Design and engineering
One of the key elements in the successful implementation of collaborative robots is their approachable, sleek, compact and lightweight design that allows them to be easily moved between locations so they can be used when and where necessary, to support short-term process changes, or to automate a task while an employee is off sick or on holiday.
Weighing a manageable 27kg, with a footprint of just 165mm2 and able to be mounted in any direction, GoFa, like YuMi and Single Arm YuMi, gives users the advantage of a slim, compact and portable cobot that offers the flexibility to take automation to where it’s needed.
Another key feature is GoFa’s reach which, at 950mm, outperforms other 5kg cobots by around 12 per cent. With a 70 per cent longer reach than ABB’s YuMi single arm robot, GoFa enables loads to be picked up and moved over greater distances, making it an effective solution for a variety of applications, from machine tending and material handling through to packing and packaging. With the ability to accurately pick up, move and place objects over greater distances than other robots in its class, GoFa can help to reduce the number of cobots that may be needed in a single space.
“The design of GoFa is focused on minimizing its footprint and weight while maximizing speed and reach, to provide the highest levels of flexibility. Our aim is to add value over and above what can be achieved with other collaborative solutions available on the market in the same payload range,” said Andie Zhang. “GoFa’s portability and ease of use means customers will be able to operate their cobot within minutes of installation, enabling even first-time users to feel comfortable with configuring and operating it, while offering an unprecedented degree of collaboration to boost productivity and efficiency and, ultimately, their competitiveness.”
GoFA is designed to work with ABB’s OmniCore robot controller family. Offering high levels of flexibility, connectivity and performance, OmniCore features a 50 per cent reduction in footprint compared with previous robot controllers, together with best-in-class motion control and path accuracy. OmniCore can be easily integrated with the latest digital production technologies, including a wide variety of fieldbuses, advanced vision systems and force control.
GoFa’s exterior design will also stand out on the shop floor, with the same distinctive white and gray color scheme as ABB’s other new collaborative robots, as well as ABB’s new collaborative robot signifier icon, which features a stylized depiction of a robot and human hand working together.
2. Speed and performance
With its expanded payload capability of up to 5kg, GoFa complements ABB’s single and dual-arm YuMi robots, while its integrated torque and position sensors in each of its six joints are key to its collaborative design.
Capable of operating up to 2.2 meters per second*, GoFa is faster than other cobots in its class, enabling it to perform more operations in a set period than competing cobots, making it ideal for assembly or picking and packaging tasks where items need to be quickly and accurately transferred between locations.
“Offering high speed, a 5kg payload, precise performance and a small footprint, coupled with simple set up and programming, GoFa can be quickly and easily deployed to help fill gaps in production lines wherever and whenever needed,” added Andie Zhang. “This provides users of all sizes, from SMEs to large companies, with the flexibility to quickly adapt to changing circumstances and respond instantly to changing customer demand without having to incur delays arising from having to find extra staff at short notice.”
*The exact safe collaborative speed may be lower, as it will depend on the specific application, tooling, payload etc. Users can refer to the SafeMove configurator App for a recommendation. Users should always carry out a risk assessment of their application).
3. Safe by design
For a robot to be considered collaborative, it must have the necessary safety functions which prevent injury to a human operator. This means factoring in the robot’s speed, the combined mass of the robot and its payload and the ability of the robot to quickly come to a halt. With its pioneering intelligent joints, GoFa fulfils this requirement by automatically coming to a halt if contact with a human or another robot occurs. GoFa’s plastic and aluminum joints also feature rounded geometry, with no pinch points that could trap limbs.
Another safety feature is the inclusion of a visual safety configurator on GoFa’s FlexPendant. Developed to ensure that even first-time users can configure the robot in a safe way, SafeMove allows users to easily set up GoFa to avoid issues such as clamping that can affect safe robot operation. GoFa also features an interaction status light, which changes color between white, green, yellow and red depending on GoFa’s operating status. This light provides an easy way for users to quickly ascertain the status of the cobot to understand if it is in standby, programming, operating or stop mode.
“Ultimately the true test of any collaborative robot is how comfortable and safe people feel working alongside it. For this reason, the design of a collaborative robot needs to make it approachable, providing the highest level of reassurance that every measure has been taken to protect workers from injury,” said Andie Zhang. “We know from our five years of experience with YuMi that workers feel safe working alongside it. As with our YuMi robots, we have designed GoFa with the user at the forefront, using a combination of technological and physical features to eliminate the risk of harm in the event of contact, but also features to make our new cobots incredibly easy to use.”
4. Ease of use
GoFa has simplicity baked into its design with features that allow it to be configured and operated even by someone with no prior knowledge or experience of using a robot.
Lead-through programming anywhere on the cobot allows users to move GoFa into various positions to create a tailored program, with each position then being set using GoFa’s arm-side interface (ASI), which features user-customizable buttons and a light ring housed on the robot arm. Aimed at encouraging greater user interaction, these buttons can be used to set positions during a lead-through routine, enabling the operator to program GoFa without their hands leaving the robot.
Lead-through programming is intended to be used with ABB’s Wizard easy programming software. Already launched for ABB’s single-arm YuMi collaborative robot and IRB 1100 industrial robot, ABB’s Wizard easy programming software can be used to create a program for GoFa in a matter of minutes. With Wizard, the programming process is reduced to simply dragging and dropping the required block on the screen of the ABB FlexPendant, with the user able to see the results immediately and adjust the cobot’s actions if required. By linking these blocks together, complete programs can be built with no need for any knowledge of robot programming languages. More experienced users can continue to program with RAPID coding and jog with the joystick on the ABB FlexPendant.
“The easier robots become to set up and operate, the more sectors and businesses can benefit. With ease of use features including GoFa’s arm side interface lead-through programming and our Wizard drag and drop easy programming tool, customers will be able to operate their GoFa cobot within minutes of installation, with no specialized training or programming skills required,” said Andie Zhang. “If you can use an ipad, you can program one of our new cobots with ease.”
For companies with more specialized programming needs, new Wizard blocks can also be created to perform specific tasks. This is achieved through ABB’s Skill Creator software which is available for free for anyone to use to turn standard RAPID programming routines into Wizard blocks and make them ready for use by non-programmers. The custom blocks, known as skills, can be produced to control grippers or create actions for specific applications such as laboratory automation.
GoFa users will also be able to use RobotStudio®, ABB's simulation and offline programming software. This is the industry’s leading PC-based solution for programming, configuration and virtual commissioning before installation.
To help support GoFa, ABB has also created a series of online tutorials covering a range of topics, from set- up and programming through to operation and troubleshooting. Please click here for more information.
5. Cobot portfolio
The new GoFa cobot builds on the success of ABB’s YuMi family, which has been helping businesses safely automate key tasks since YuMi, the world’s first truly collaborative robot, was launched in 2015. ABB’s portfolio of collaborative robots now offers three different families – YuMi, GoFa and SWIFTI, with payload options ranging from less than 0.5kg to 5kg, to support the most diverse range of collaborative applications.
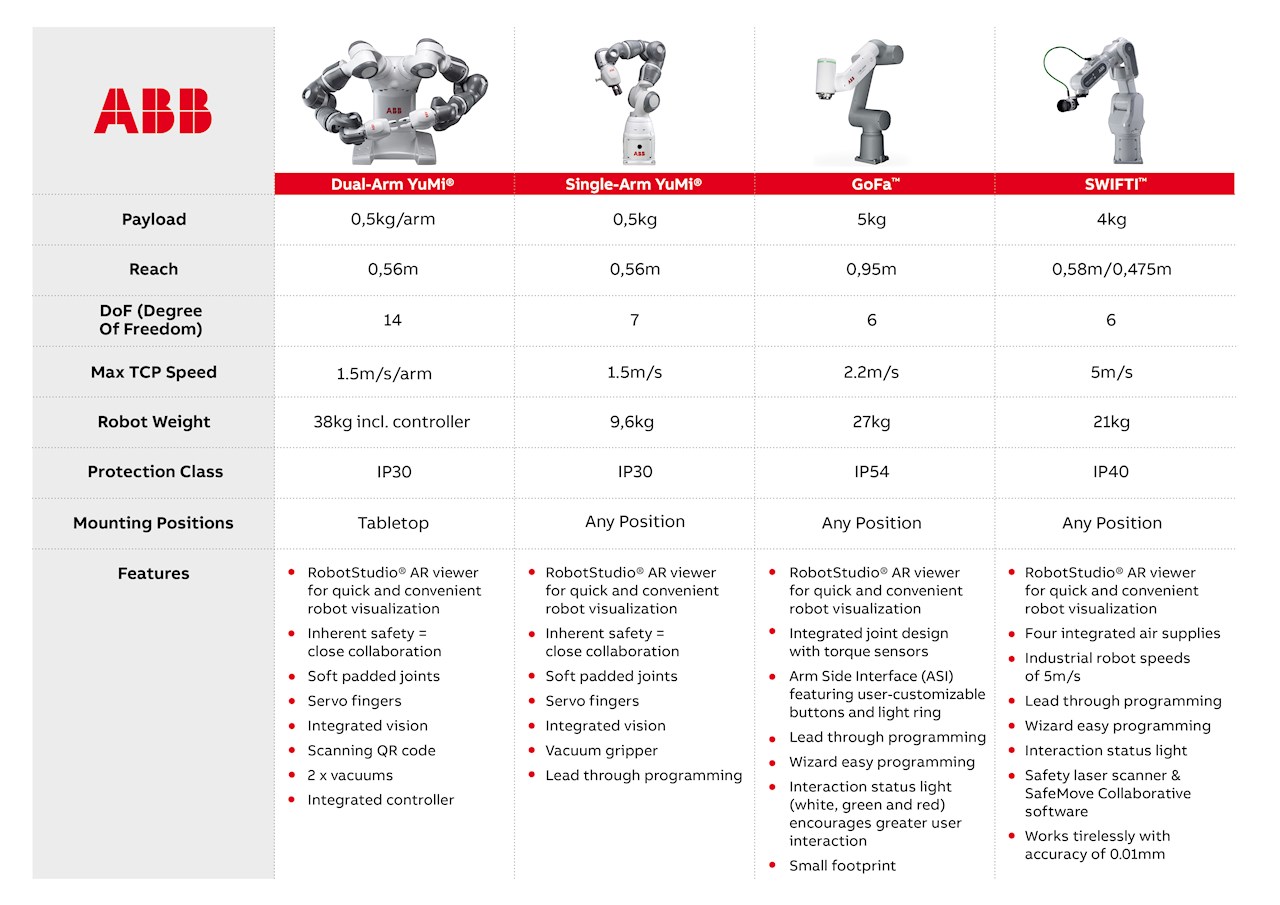