Ralf Gitzel, Holger Kaul, Aydin Boyaci, Jörg Gebhardt, Ido Amihai, Martin W Hoffmann, Stephan Wildermuth Industrial Automation, Corporate Research Ladenburg, Germany, ralf.gitzel@de.abb.com, holger.kaul@de.abb.com, aydin.boyaci@de.abb.com, joerg.gebhardt@de.abb.com, ido.amihai@de.abb.com, martin.w.hoffmann@de.abb.com, stephan.wildermuth@de.abb.com; Callisto Gatti ABB ELDS Dalmine, Italy, callisto.gatti@it.abb.com
Many countries are working on ways to reduce their CO₂ emissions. This effort puts two technical aspects of modern life onto center stage: power generation and personal mobility. These two areas are undergoing great change: Ever more low-CO₂ electrical power is generated from wind and solar sources while, in the mobility sector, electricity is steadily replacing fossil fuels as a vehicle power source, often with the implicit assumption that the electricity will come from green sources.
Connecting renewable energy sources and electric vehicles to the distribution grid adds stress to an already stressed system: Renewable sources are intermittent and can fluctuate, and large fleets of electric vehicles will produce new peak loads and a general demand increase. Therefore, grid operators must find ways to increase the flexibility of their network operations and deal with a higher occurrence of irregularities and switching events. The increased stress also challenges traditional maintenance strategies and without condition-based maintenance, costs are likely to explode.
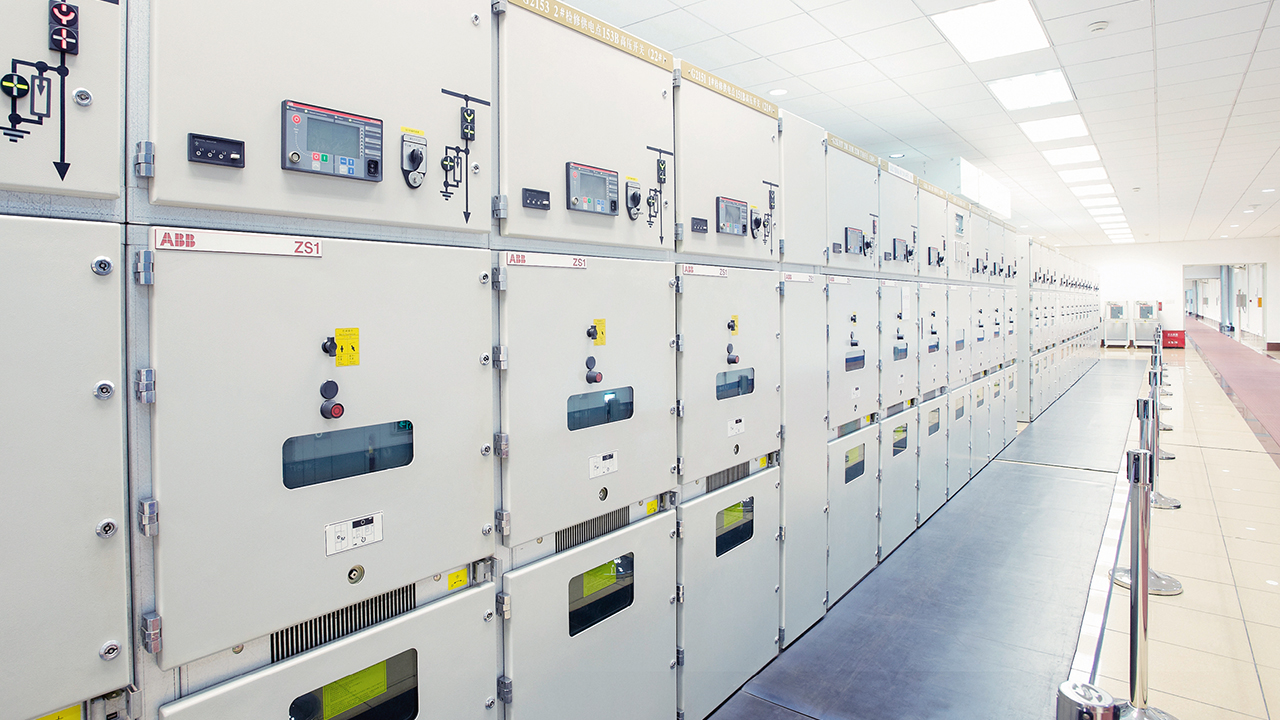
This article describes how infrared cameras combined with AI can help to detect developing faults in medium-voltage (MV) switchgear and enable condition-based maintenance →01-03. The work was conducted jointly by ABB and partners in the context of the FLEMING research project. In the FLEMING project, a consortium drawn from research and industry is investigating how the current use of sensors in distribution networks can be fundamentally improved by using AI methods together with an expansion of sensor technology. The aim is to make a significant contribution to the success of the energy and mobility transition in Germany. Lessons learned can be later applied elsewhere.
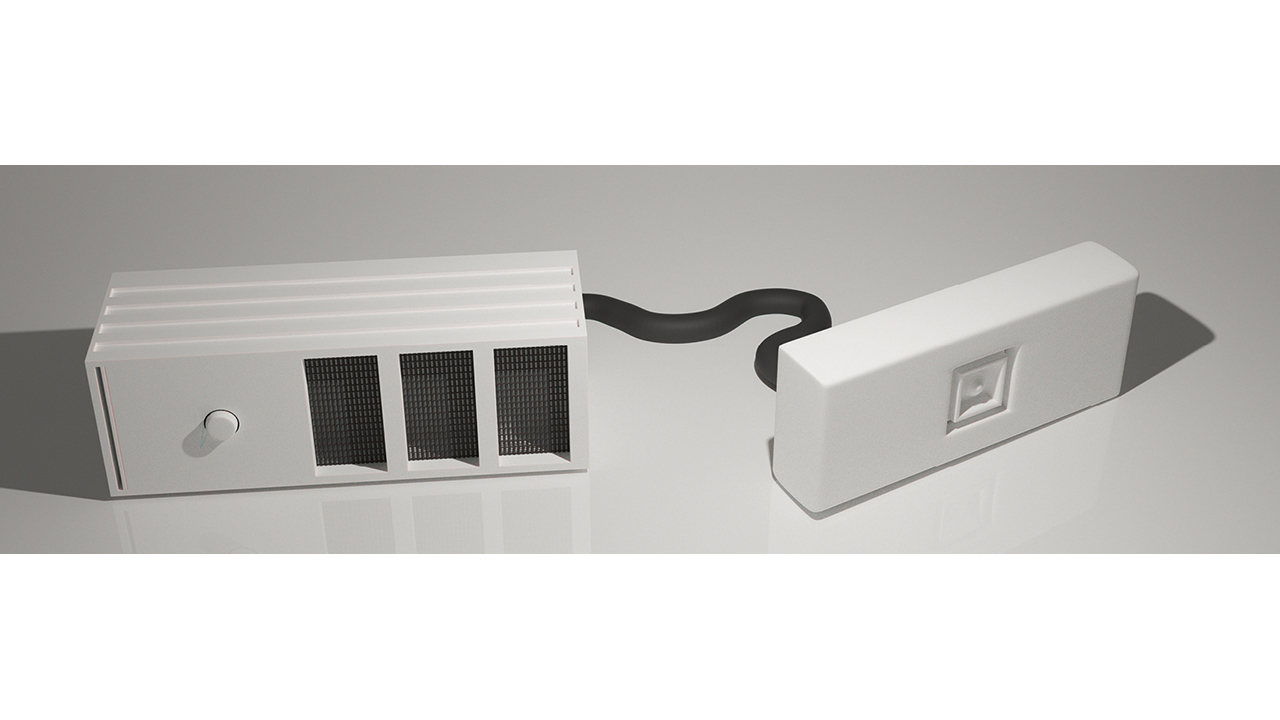
ABB leads the FLEMING consortium. Partners are from industry and the world of academia: the University of Paderborn’s SICP Software Innovation Campus; RWTH Aachen, Forschungsinstitut für Rationalisierung e. V. (FIR); Karlsruhe Institute of Technology, Institute of Electrical Energy Generation Systems and High-Voltage Technology; and Heimann Sensor GmbH (a manufacturer of high-quality infrared sensors). Associate partners are the Städtische Werke Überlandwerke Coburg GmbH (a power company) and WestfalenWIND GmbH (a wind park operator in the Paderborn area).
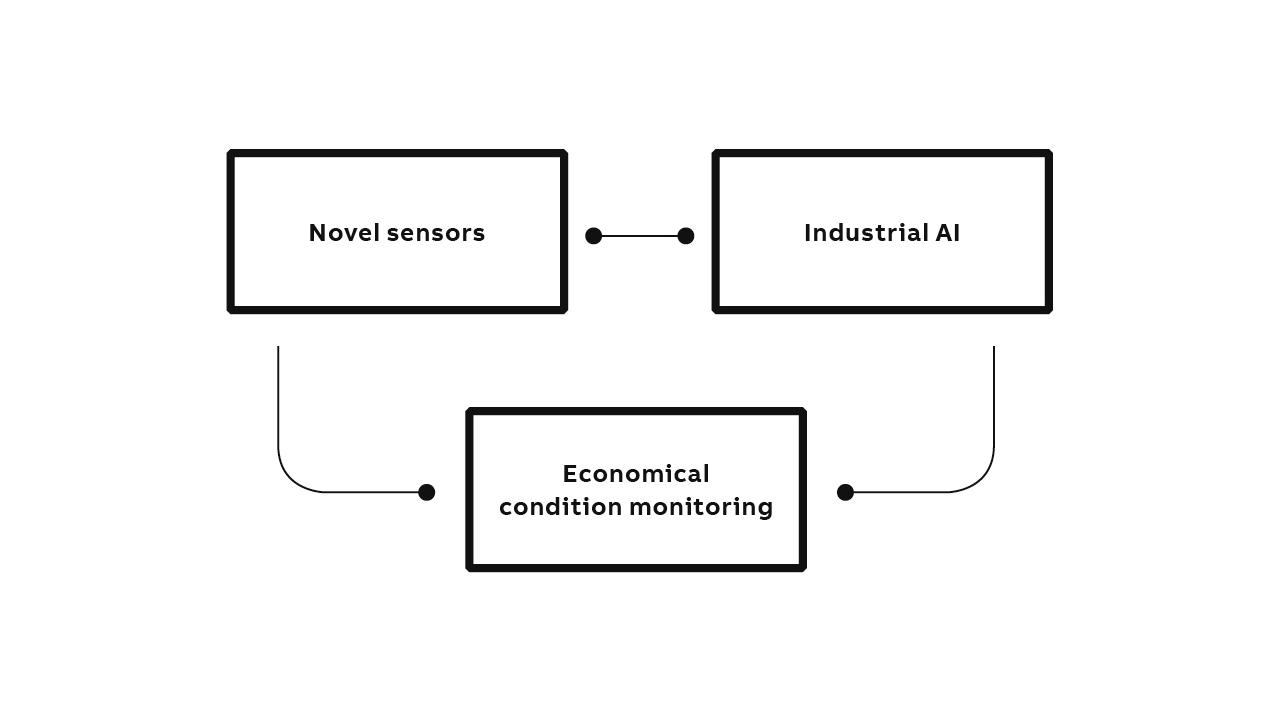
Thermal monitoring
Thermal monitoring is a useful way of detecting technical problems in an electrical system. Electrical conductors heat up via so-called Joule heating when current passes through them. This principle is exploited by everyday items such as heating rods or electric kettles.
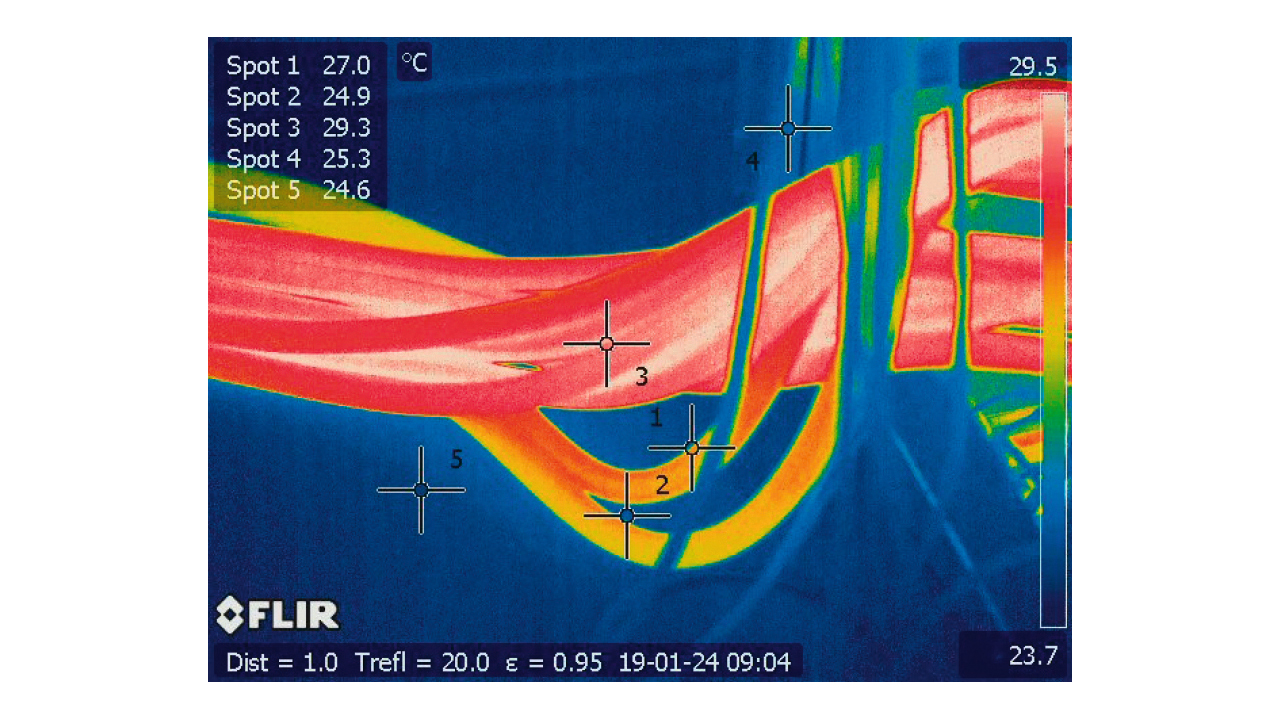
The amount of heat generated depends not just on the level of current but also the resistance of the conductor. Therefore, a resistance increase – due to, eg, corrosion or switchgear elements such as busbars bolts that have been improperly installed or vibrated loose (a problem found particularly in marine vessels) – will create a local hot spot. Such hot spots, and, thus, actual and incipient failure locations, can be made visible by infrared thermographic (IRT) imaging [1-3]. For example, in →04-05, an IRT image reveals the heating due to recent or ongoing flow of current through cables. As extended periods of abnormally high temperature can cause degradation, early detection of hotspots is desirable [1].
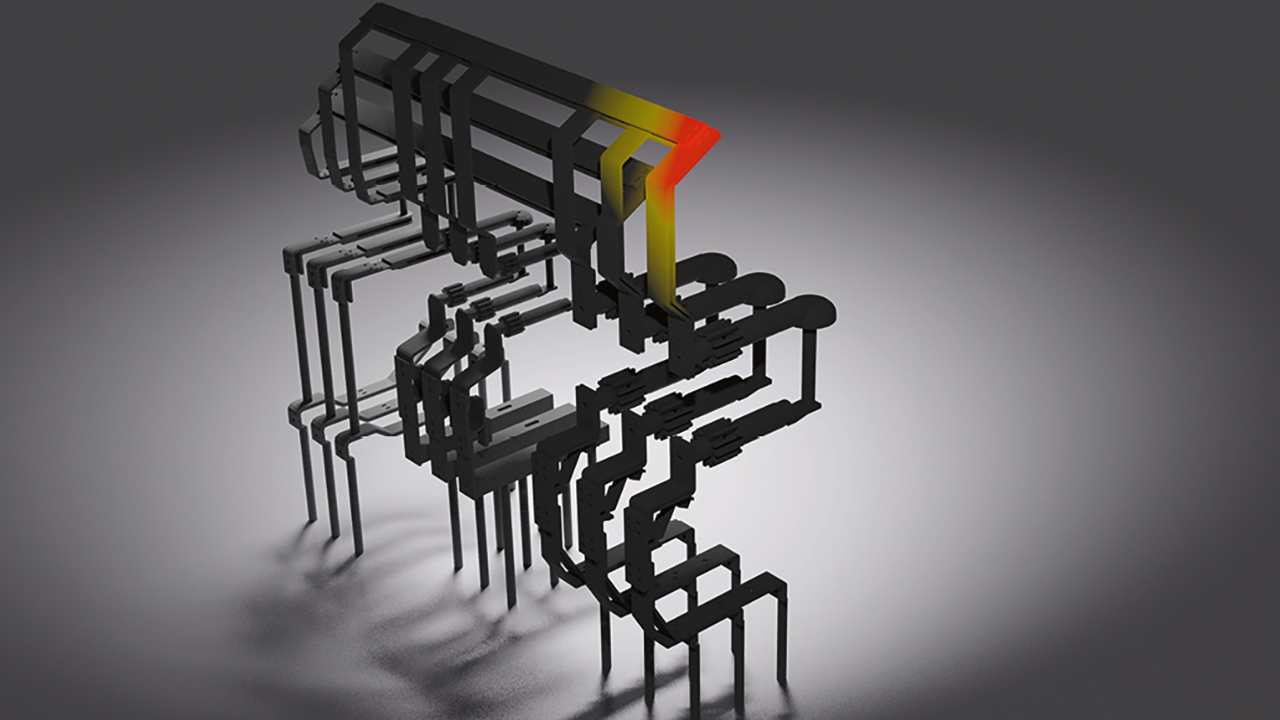
Thermal monitoring sensors
While it is possible to use contacting measurement techniques to assess the thermal state of equipment, these methods come with certain drawbacks:
• Contact measurement on potential introduces the risk of interfering with the dielectric requirements of the switchgear and reduces equipment safety [1].
• If the monitoring equipment is placed in regions with high magnetic or electric fields, there might be some electromagnetic interference with the measurement process [4,5].
IRT cameras do not suffer from these issues. Additionally, unlike a point measurement, IRT can cover a large area, greatly reducing sensor-related cost [4,6].
Sensors put into switchgear for condition monitoring must deliver a high measurement accuracy over a broad ambient temperature range. They also need to have a long lifetime and the measurements they supply must be reliable and stable (ie, low sensor drift) over this period. While there are several measuring principles for infrared temperature (eg, bolometric and pyroelectric approaches), thermoelectric sensors such as thermopiles meet these requirements best.
Thermoelectric sensors generally consist of several thermocouples on a thin membrane. When the incoming infrared radiation increases the membrane’s temperature, the sensor generates an output voltage that is proportional to the infrared radiation detected. By using a pixel array of such sensors, an infrared image is produced. The absence of moving elements, such as shutters, is one contributor to the longevity of these sensors.
Algorithms
The data provided by the IRT sensors records hot spots resulting from technical defects that alter the resistance of the conductor. However, while a human can easily spot these issues in a visualization of the sensor data, an algorithm is needed if the system is to be monitored without human intervention.
To realize such a system, the data is first cleaned. Often, the notoriously low contrast of the IRT image has to be improved. Also, noise in the pixel signals has to be removed or reduced to avoid skewing values used for statistical analyses.
Once the data is preprocessed, several different types of algorithms can be applied. A classic approach is to implement an expert system. With a collection of human-defined rules, the system essentially uses a checklist to determine whether a state is problematic or not. Expert opinion can be refined by referring to simulations based on the laws of physics that show the characteristics of abnormal states. In both cases, one needs to find the right balance between creating a near-perfect model that is too expensive and a simplistic model that is not good enough to capture reality adequately.
Another method is to use machine-learning algorithms from the field of AI that automatically understand common patterns in large data sets. While they take a statistical approach, these algorithms can still benefit from expert knowledge. For example, an expert knows that the maximum temperature within an IRT image, as well as the temperature differences between certain regions, are quite important. Which combinations of temperature levels and differences are still acceptable or not can be determined automatically by the statistical analysis performed by the algorithm, provided it is trained appropriately. The algorithms in the scope of the FLEMING project cover the spectrum from pure expert systems to convolutional neural networks, which mimic the human visual cortex.
Predictive and condition-based maintenance
The tool chain described above can be used to recognize problems when they occur and allows the maintenance team to take immediate action. But, of course, it is preferable to receive an early warning of a failure. Both expert knowledge and statistical analysis can be used to identify situations that represent the early stages of a failure or events that will lead to damage. This approach leads to a series of possible algorithm types that can be used for predictive or condition-based maintenance.
At its most basic level, an algorithm classifies an input as showing a fault in an otherwise healthy situation. Combined with knowledge of deterioration mechanisms, this classification can be refined to characterize the further evolution of the fault. This leads to the creation of a failure prediction or an asset health index. With more data and/or even better understanding of how failures develop, one can not only predict the upcoming occurrence of a failure but also the estimated time until it occurs, which is a prediction of remaining useful life (RUL). Although it is the most difficult parameter to obtain, RUL is the most useful indicator of all as it allows the operator to schedule repairs into a planned downtime window. RUL is hard to obtain because it relies not only on a profound understanding of failure-stage mechanisms but also on a prediction of usage patterns, which is not always possible.
All of these algorithms are purely informational. However, an intelligent system can and should use the information they provide to recommend actions, maintenance schedules and repair instructions.
The vision of FLEMING
The significant changes confronting the electrical grid place an unprecedented strain on its components – even high-reliability equipment such as switchgear faces a faster rate of deterioration. The vision of FLEMING is to improve existing condition-monitoring solutions to make them ready for these new challenges. While automated failure detection has been developed prior to FLEMING, the project will explore extended prediction and RUL calculations. The goal is to combine highly reliable sensor technologies, such as IRT, and AI to achieve actionable predictions that minimize the unscheduled downtime of equipment. The IRT-based solution for the critical MV equipment described here can probably be adapted to other types of switchgear.
In future articles, additional failure modes and monitoring solutions such as vibration sensors will be discussed.
References
[1] H. Niancang, “The infrared thermography diagnostic technique of high-voltage electrical equipment with internal faults,” Proceedings of the POWERCON ’98, 1998 International Conference on Power System Technology, Beijing, China, volume 1, pp. 110–115, 1998.
[2] T. Craig, “Condition monitoring in low-voltage circuit-breaker technology,” Proceedings of the IET International Conference on Resilience of Transmission and Distribution Networks, RTDN 2017, Birmingham, UK, pp. 1–6, 2017.
[3] A. S. N. Huda and S. Taib, “Application of infrared thermography for predictive/preventive maintenance of thermal defect in electrical equipment,” Applied Thermal Engineering, 61, pp. 220–227, 2013.
[4] M. S. Jadin, and S. Taib, “Recent progress in diagnosing the reliability of electrical equipment by using infrared thermography,” Infrared Physics and Technology, volume 55, issue 4, pp. 236–245, 2012.
[5] B. Li et al., “HV Power equipment diagnosis based on infrared imaging analyzing,” Proceedings of the 2006 International Conference on Power System Technology, pp. 1–4, 2006.
[6] Y. Chou and L. Yao, “Automatic diagnostic system of electrical equipment using infrared thermography,” Proceedings of the 2009 International Conference of Soft Computing and Pattern Recognition, pp. 155–160, 2009.