Tobias Geyer ABB Medium Voltage Drives Turgi, Switzerland, tobias.geyer@ch.abb.com; Wim van der Merwe ABB Medium Voltage Drives Lodz, Poland, wim.van-der-merwe@pl.abb.com; Vedrana Spudic ABB Process Industries Baden-Dättwil, Switzerland, vedrana.spudic@ch.abb.com; Jess Galang, Ester Guidi, Gerald Scheuer ABB Medium Voltage Drives Turgi, Switzerland, jess.galang@ch.abb.com, ester.guidi@ch.abb.com, gerald-a.scheuer@ch.abb.com
Today’s ships depend on advanced technology and superior performance to efficiently navigate the world’s oceans even in harsh marine environments →01. Fuel efficiency is critical to lower the cost of shipping and has the additional benefit of lowering CO₂ emissions [1]. ABB’s marine propulsion Azipod® family lowers fuel consumption and achieves superior maneuverability and fast power adjustments, eg, for ice breakers, thereby helping the shipping industry meet sustainability targets while reducing costs [2]. But, how does the Azipod® electric propulsion accomplish this even in the ice-packed regions of the world's oceans? Azipod®’s gearless steerable propulsion system utilizes an electric motor located in a pod beneath the hull of the ship, which can rotate 360 degrees, permitting thrust in all directions. For this amazing feat, variable speed drives (VSD) are required that need to be precisely controlled. This necessitates motor friendliness (to minimize the motor temperature, noise and vibration) and superior dynamic performance, eg, during network events; the high power also mandates low switching frequencies. Enter ABB’s breakthrough technology: Model Predictive Pulse Pattern Control (MP3C) to maximize operating efficiency and attain superb dynamic performance for such electric drives →02.
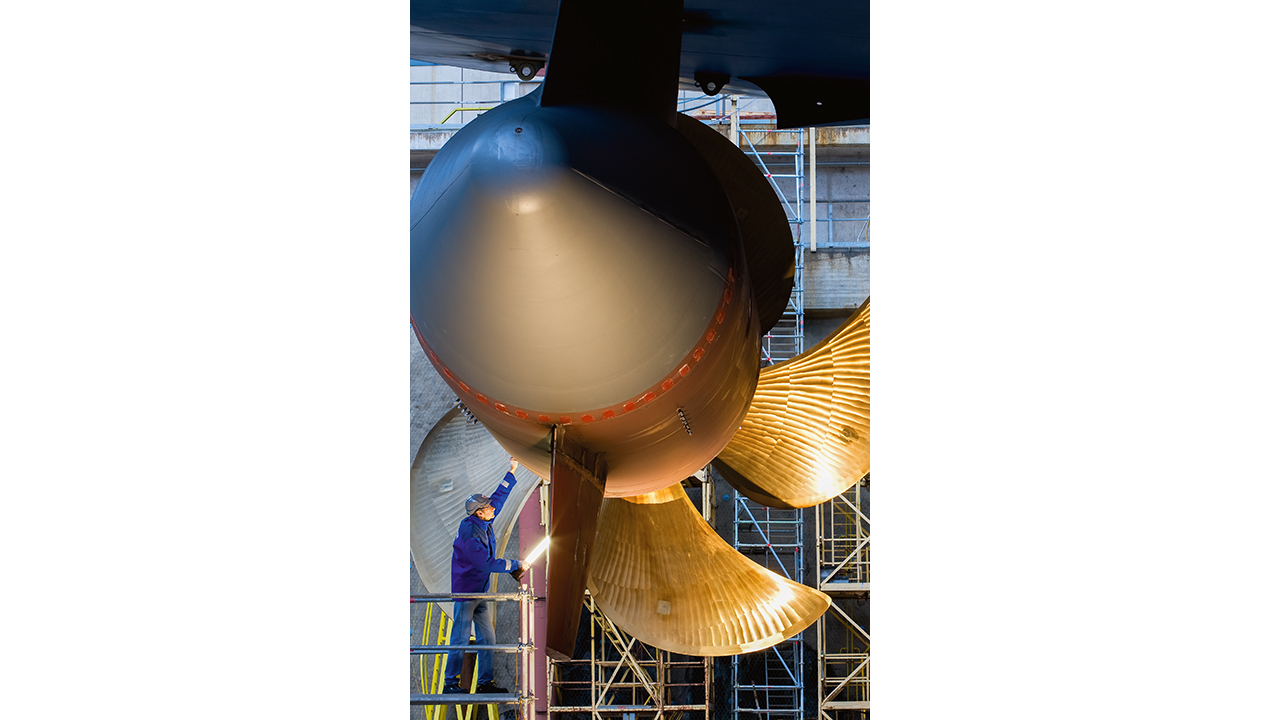
Achieving propulsion drive power and efficiency
For systems such as Azipod®, propulsion drive power is regulated by the power electronics converter, which controls the speed by varying motor frequency and voltage. If a network disturbance occurs, and it easily can, the control system must maintain the dc-link voltage adequately to keep the drive system functioning safely. To increase efficiency, the number of switching events per fundamental cycle must be kept at a minimum. Moreover, the energy stored in the dc-link capacitors is typically reduced to a minimum to increase safety in the event of medium-voltage (MV) faults.
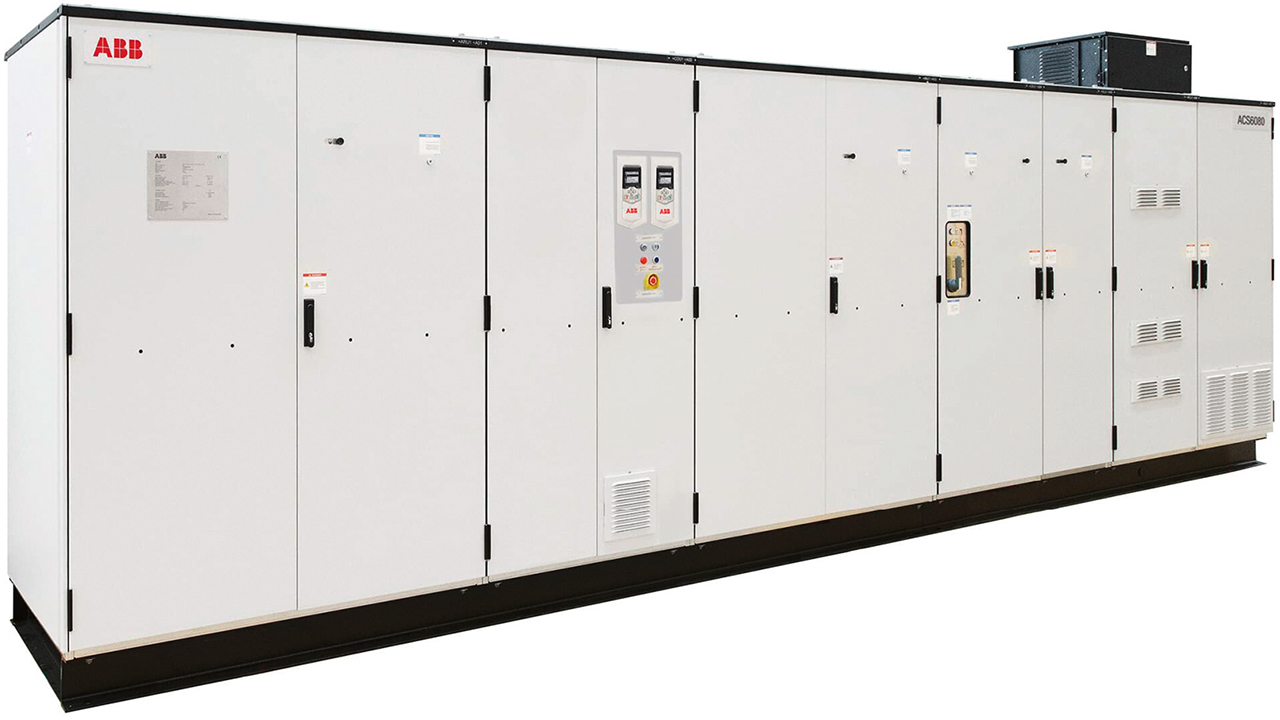
Switching induces current and torque ripples that entail mechanical vibrations; these tend to be pronounced at low switching frequencies. Moreover, ice breakers operating in polar regions must meet strict underwater noise limits to minimize the adverse impact on marine wildlife. Traditional converter control methods require high switching frequencies to meet these noise limits, incurring high converter losses. Achieving these boundary conditions is essential but arduous for traditional control methods. Now, ABB’s MP3C applied to VSDs opens up the possibility to achieve them all.
Delivering dynamic performance with ACS6080 and MP3C
Saving energy, maintaining safety and incorporating quick, exact and robust control is also crucial for process industries. For the mining and metals sector, both cold and hot rolling mills rely on control of the rotational speed and the torque of the roll to achieve high quality products. Because the material enters and leaves the roll abruptly, rapid load changes between no load and full load make torque control difficult →03.
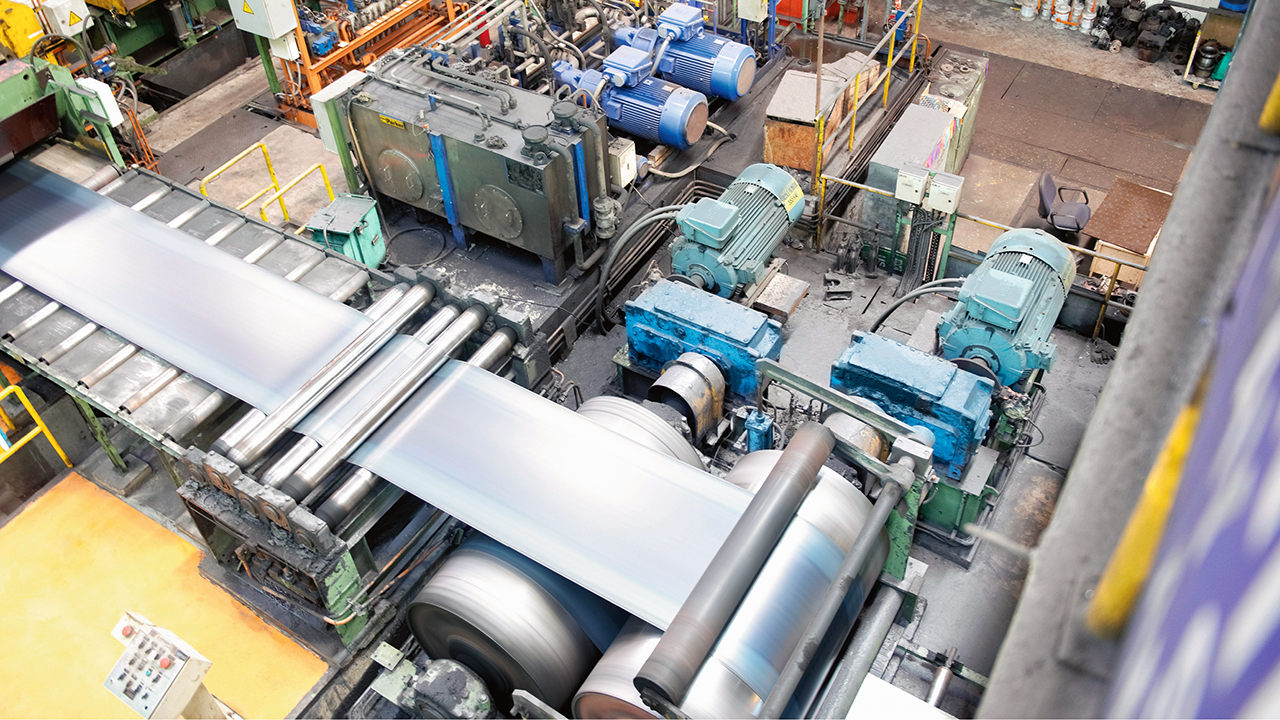
Despite these requirements, harmonic distortions result in harmonic losses and the need for additional cooling and oversized machines. Finding the right drive with the right control and lowering harmonic losses for critical applications is a key goal of ABB. Reducing losses leads to greater efficiency and hence more sustainability. Enter ABB’s ACS6080 drive with the breakthrough technology MP3C to control the semiconductors. Developed over the past decade, this control method maximizes dynamic performance and efficiency and minimizes harmonic distortions to deliver optimal motor operation in all situations.
Control methodologies: a brief history
For many decades, combining superior harmonic performance (especially the ability to minimize distortions per switching frequency) with excellent dynamics has been elusive and fraught with compromise.
Direct Torque Control (DTC), developed in the 1980s, and Field-oriented Control (FOC) showcase this dilemma →04. Because DTC uses a sampling frequency (about 40 kHz) and relies on hysteresis controllers with a switching table to control the electromagnetic torque and the magnetization of the electric machine, torque response is fast and precise. The result is a superb dynamic performance of the drive and a system robust to dc-link fluctuations and other disturbances.
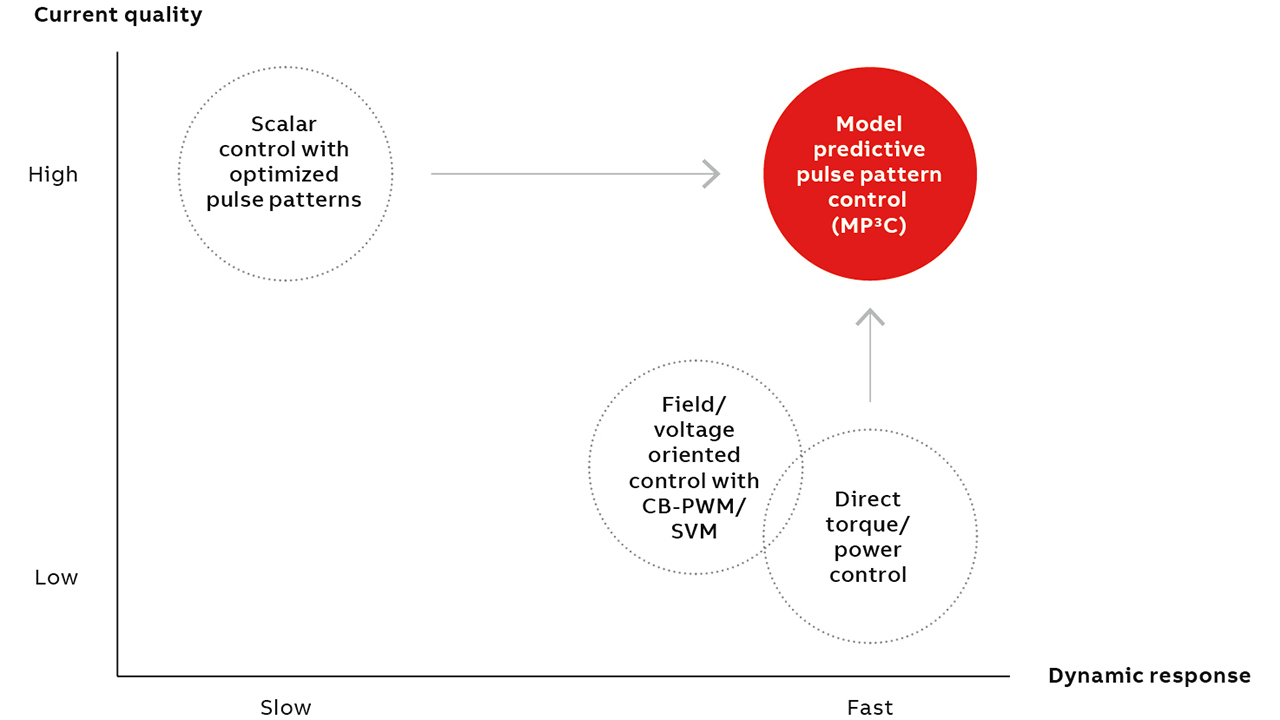
Alternatively, FOC, set in a rotating orthogonal reference frame, uses linear controllers that provide voltage references to a Pulse Width Modulator (PWM) based on Carrier-based PWM (CB-PWM) or Space Vector Modulation (SVM). Since MV converters operate at low switching frequencies (few hundred Hertz), the pulse number (switching frequency over fundamental frequency) is less than 10, leading to large harmonic distortions. Moreover, the sampling frequency of the linear field-oriented controller is four times the switching frequency (here, around 1 kHz). This limits the bandwidth of the controller, making it slow and resulting in a poor dynamic performance and poor rejection of disturbances →04.
These disadvantages can be overcome with the help of Optimized Pulse Patterns (OPPs) that minimize the current distortions for a given switching frequency – a superior choice for MV converter systems →05. However, achieving high-bandwidth control with linear controllers and OPPs is intrinsically difficult because strong current ripples adversely affect the controller. Using a slow control loop, eg, volts per frequency control for OPPs, is theoretically possible but is impractical for most MV drives applications. During torque reference changes or when transitions between pulse patterns occur, the controller does not react fast enough, leading to excessive transient currents and poor dynamic performance.
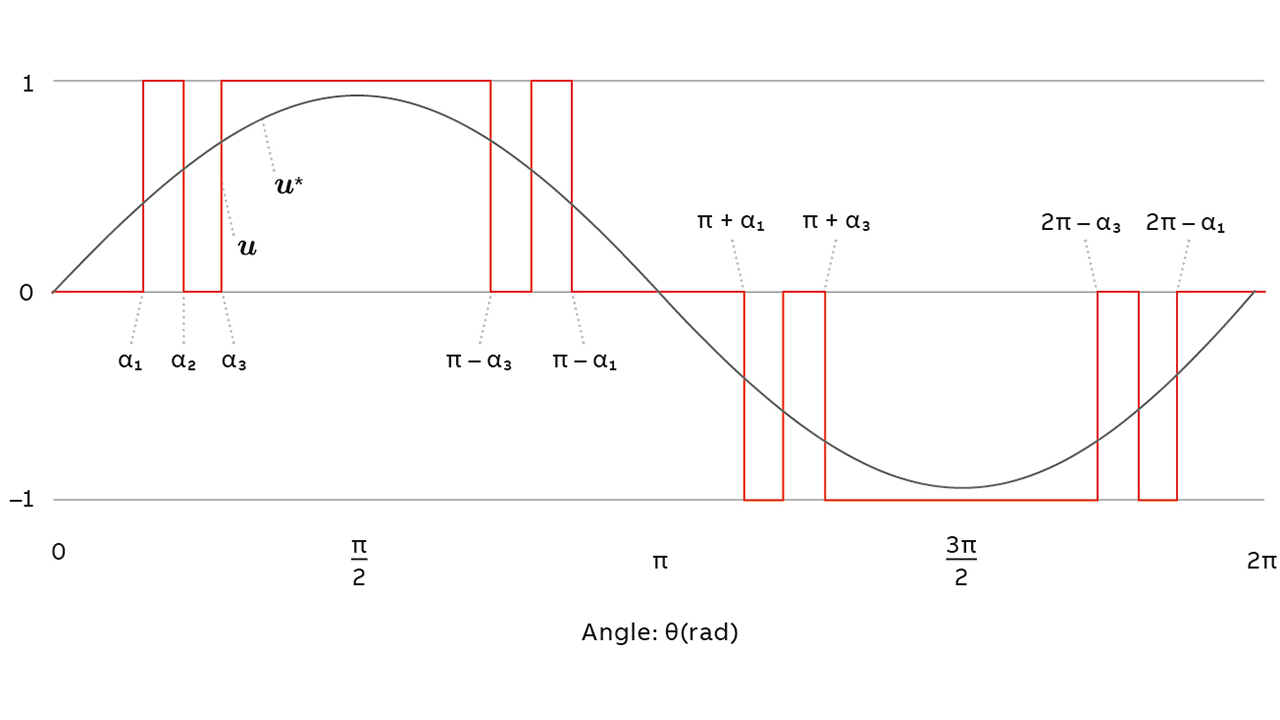
The small dc-link energy stored in MV systems (energy stored < 5 ms) requires a fast torque reversal during network events to avoid dc-link over- or under-voltages. Thus, traditionally, DTC or FOC methods have been used in lieu of OPP-based schemes.
ABB’s 45 years of experience developing VSDs including DTC – an ABB innovation – has enabled unprecedented performance in electric motors and delivered dramatic energy savings by matching motor speed and torque to actual requirements of the driven load. This desire to provide efficiency and power savings without compromising dynamic performance led to the development of MP3C – the ultimate control system for the most demanding applications.
Finding the balance
With MP3C, ABB has found the sweet spot – where enhanced dynamic performance meets excellent harmonic performance, exemplified by OPPs during steady-state conditions →04.
Here, ABB employs a well-known approach, Model Predictive Control (MPC), in which a mathematical model of the controlled drive system predicts its future evolution over a prediction horizon and chooses the best control input by solving a mathematical optimization problem. Once accomplished, the system obtains new measurements and re-plans over a shifted or receding horizon [3].
Superb control principle with MP3C
Basically, MP3C combines MPC with OPP technology; OPPs provide minimal harmonic distortions per switching frequency and MPC tracks the ideal stator flux trajectory of the OPP by minimizing a cost function and manipulating the switching instants of the OPP [4]. Using a high sampling frequency (40 kHz) with receding horizon policy, a fast dynamic response and superior disturbance rejection is attained.
In OPPs, the fixed modulation interval of classic PWM, with two switching transitions per phase and modulation interval, is abandoned. Instead, OPPs are computed offline by calculating the optimal switching angles and switching transitions to minimize the current distortions for a given switching frequency. Quarter and half-wave symmetry is typically imposed. Assuming an inductive load, the current distortions are proportional to the sum of the squared-differential-mode voltage harmonics divided by the harmonic order. The optimal switching angles, αi, and switching transitions, Δui, can then be calculated for a given modulation index, m, and pulse number, d, minimizing the current distortions:
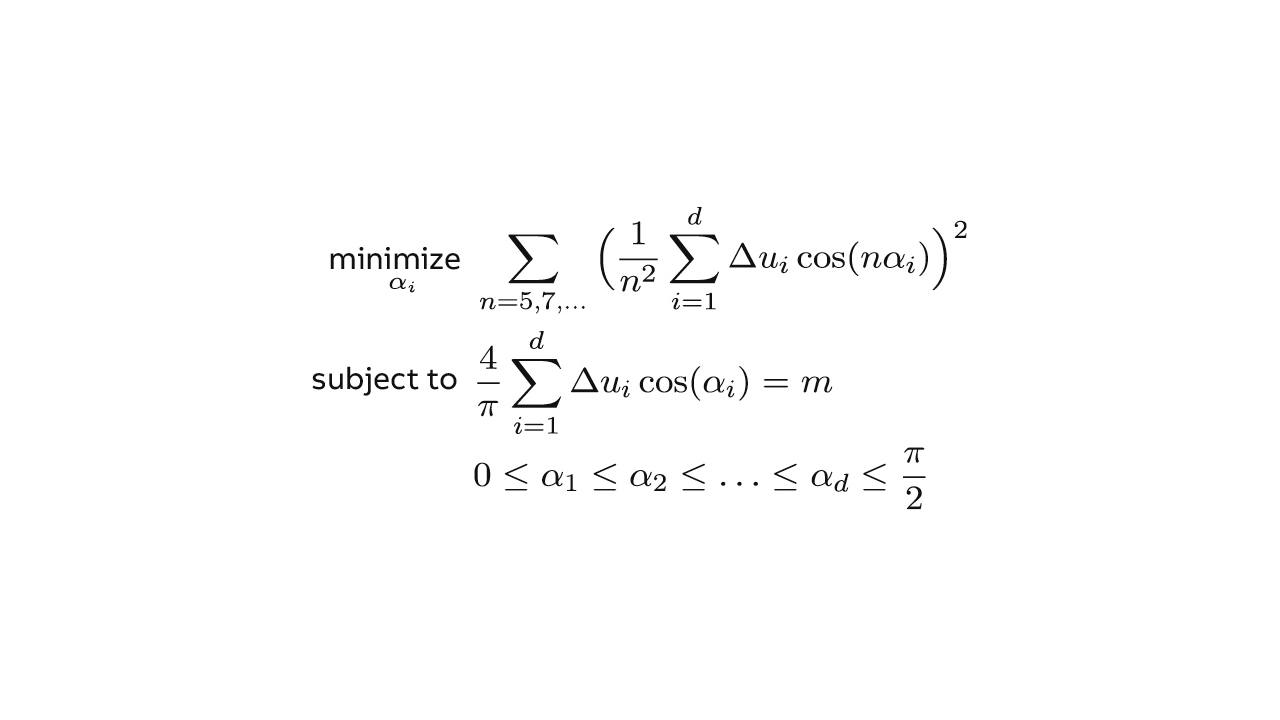
The modulation index corresponds to the output voltage and the pulse number relates to the switching frequency.
Image currently unavailable
Image currently unavailable
Image currently unavailable
Image currently unavailable
Image currently unavailable
Image currently unavailable
Image currently unavailable
Image currently unavailable
Image currently unavailable
06a The optimal stator flux trajectory (minimum THD) is derived by integrating the OPP as shown. 06b The Stator flux vector is modified by manipulating the time-instants of the switching transitions (shown here in phase a). Fast closed-loop control is achieved. 06c Trajectory tracking of MP3C is achieved by regulating the stator flux along the stator flux reference trajectory (integral of the OPP). This minimizes the current TDD.
06 The control principle of MP3C is illustrated with the stator flux trajectory, stator flux correction and trajectory tracking. Rotor flux vector r, αβ, stator flux vector s, αβ, reference stator flux vector *s, αβ and stator flux error s, αβ, err are shown in stationary orthogonal coordinates.
The reference trajectory of the stator flux vector results from the integrations of the stator voltage of the OPP over time →06. Per definition, this trajectory is optimal; tracking the trajectory tightly, the Total Demand Distortion (TDD) of the stator currents is minimized by modifying the time-instants of the switching transitions accordingly – important in the presence of large disturbances, eg, a strong dc-link voltage ripple. By tightly tracking the stator flux reference trajectory, MP3C achieves a close-to-optimal harmonic current spectrum and minimizes the adverse impact of the dc-link voltage ripple on the stator current TDD.
Evidence-based performance yields benefits
Simulations, lab and field experimental results demonstrate the superiority of MP3C compared to conventional methods. For instance, the trade-off between the inverter losses and the harmonic losses of machines when varying the switching frequency show that MP3C performs better than FOC in terms of losses →07a. Here, MP3C with a pulse number of three achieves a total loss reduction of 25 kW with respect to SVM (carrier ratio nine). This can positively impact both capital and operating costs. Assuming an electricity price of 80 Euro per MWh, the loss reduction of 25 kW would reduce the annual electricity bill by 17,500 Euros.
Image currently unavailable
Image currently unavailable
Image currently unavailable
Image currently unavailable
Image currently unavailable
Image currently unavailable
07a MP3C performs better than FOC in terms of inverter losses when the switching frequency is varied. For both MP3C (black circles) and FOC (red circles), a regression line is included as a guide (the non-solid data points were considered outliers). 07b Use of MP3C reduces the torque TDD by 33 percent in this case. Comparison of SVM with the carrier ratio 9 and MP3C with pulse number 4 shows a reduction of the torque TDD from 3.3 percent to 2.2 percent.
07 Simulation results demonstrate the superiority of MP3C over FOC schemes in terms of inverter losses and torque distortions.
Similar benefits are observed in terms of reduced TDD →07b. Because lower stator current distortions imply lower torque distortions, the air gap torque TDD can be reduced for similar inverter losses for MP3C compared to FOC with SVM. The lower mechanical and thermal stresses extend the lifespan of electric machines and prolong maintenance intervals, ultimately translating to lower operational expenditure (opex).
Results obtained for a 3.3 kV induction machine rated at 1,140 kVA affirmed the efficacy of MP3C →08. Here, MP3C achieves a nearly optimum ratio of harmonic current distortions per switching frequency at steady state. Moreover, during transients, very short current and torque responses are achieved that are similar to those of DTC, if additional pulses can be inserted when required [5].
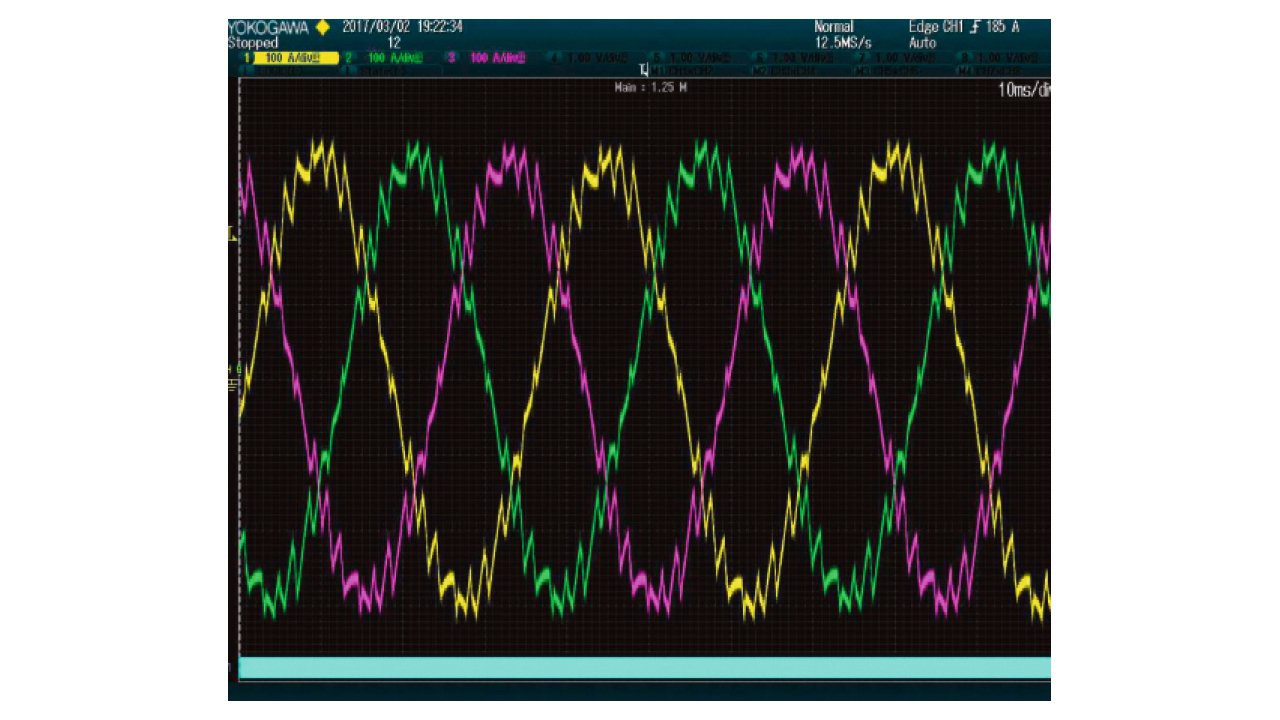
Thanks to MP3C’s low harmonic distortions at low pulse numbers, increasing the fundamental frequency is possible. This increases the system design space for applications such as compressors, which require high-speed motors. By increasing the output speed of the drive, the size and weight of an additional gearbox can be decreased or avoided, leading to significant cost savings in terms of initial investment, the capital expenditure (capex).
MP3C use cases
ABB’s ACS6000 MV drives have been used to achieve fully controllable testing conditions for test stands. In one case, ABB examined the problem of excessively high temperatures observed for machines connected to the ACS6000 drive, which limited the power achieved by the motor test stand. The use of MP3C lowered the motor temperature (eg, 40 K instead of 65 K) and reduced harmonic distortion of the motor currents. The test stand could then be operated at a higher power – a solid result.
Moreover, ABB has delivered the first ACS6080 used in a pumped storage power plant, utilizing MP3C. By combining the benefits of high efficiency and higher output frequency, MP3C opens up new possibilities for customers to modernize their existing frequency converter system.
Best in class: ACS6080 drive with MP3C
In 2019, ABB launched the ACS6080 drive with MP3C for superb control and best-in-class drive train optimization. In several important cases, higher system efficiency and motor output power compared with conventional systems is attained: the output power can be increased at high fundamental frequencies. Overall, ABB’s ACS6080 drive with MP3C control results in lower capex (lower initial investment and system cost optimization) and reduced opex, such as lower running- and maintenance costs.
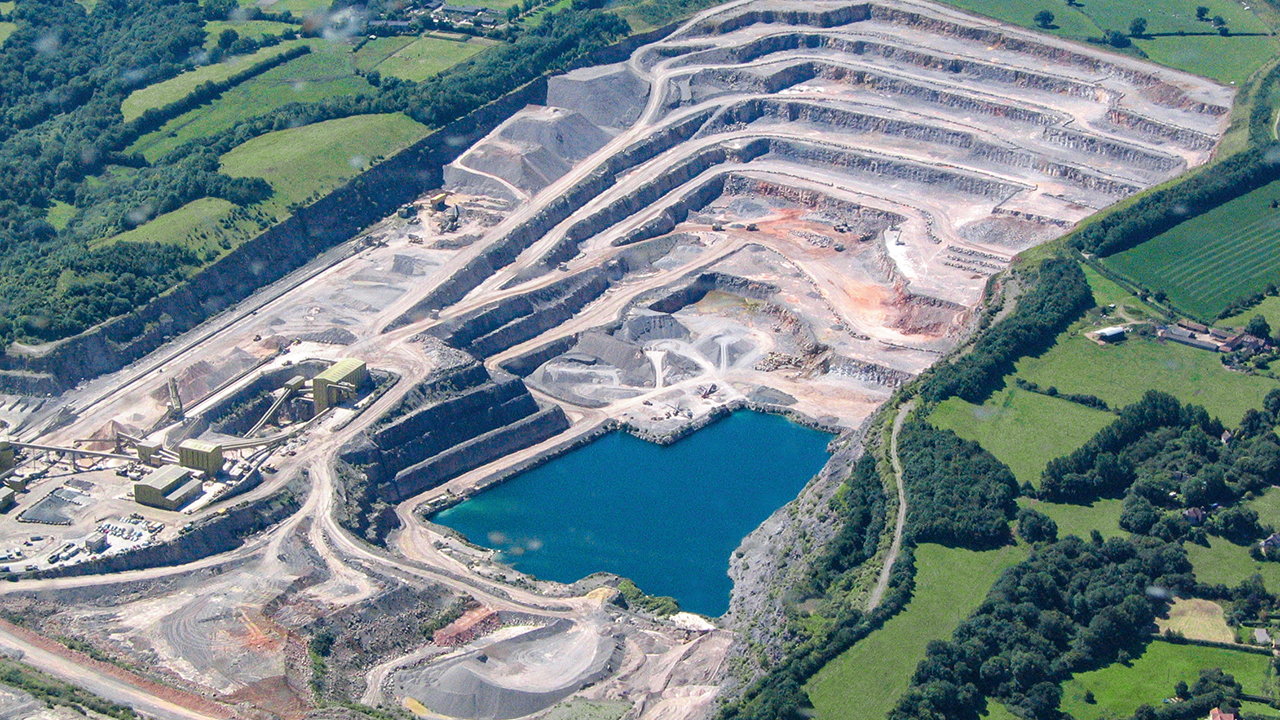
By combining MPC with OPP, ABB’s new MP3C with ACS6080 meets industry’s demand for low current distortions and high dynamic performance. Consequently, the metals and mining industries, the marine sector and industries that rely on test stand applications now have a beneficial additional degree of freedom →09. MP3C pushes efficiency and motor friendliness to what is physically possible while preserving the dynamic performance and robustness of DTC.
References
[1] ABB, “ABB Azipod® electric propulsion can save $1.7 million in fuel costs annually, study shows”, ABB Group Press Release, June 5, 2019, [Online]. Available: https://new.abb.com/news/detail/24879/abb-azipodr-electric-propulsion-can-save-17-million-in-fuel-costs-annually-study-shows. Accessed July 12, 2020.
[2] ABB, “ABB Azipod® takes marine propulsion to the North Pole and beyond”, ABB Group article, Aug. 23, 2019, [Online]. Available: https://new.abb.com/news/detail/30623/abb-azipodr-takes-marine-propulsion-to-the-north-pole-and-beyond. Accessed July 12, 2020.
[3] J. B. Rawlings and D. Q. Mayne. “Model predictive control: Theory and design”, Nob Hill Publ., Madison, WI, USA, 2009.
[4] T. Geyer, et al., “Model Predictive Pulse Pattern Control”, IEEE Trans. on Industry Applications, vol. 48, no 2, March/April 2012, pp. 663–676.
[5] T. Geyer and N. Oikonomou, “Model predictive pulse pattern control with very fast transient responses”, in Proc. IEEE Energy Convers. Congr. Expo., Pittsburgh, PA, USA, Sep. 2014.