ABB Ability™ Smart Sensors and remote monitoring systems boost safety, extend equipment life, and significantly, or even completely, eliminate downtime. They are also opening the door to the Factory of the Future – a concept in which data collected from equipment such as motors, mounted bearings, gearing, variable-speed drives, and pumps is combined and can be accessed and analyzed remotely, providing deep insights into the health of entire processes.
Artur Rdzanek Sensore, Products ABB Dodge® Power Transmission, Greenville, SC, United States, artur.rdzanek@us.abb.com
Smaller, smarter, safer. These are some of the key characteristics that describe the evolution of sensors over the last decade. More recently, however, the value of sensors has been further accentuated by three separate developments: the availability of cloud computing, data analytics, and mobile data transmission [1]. These developments have opened the door to the arrival of IoT-based wireless sensors that allow for permanent monitoring of a vast range of devices and processes at a fraction of the cost of traditional condition monitoring systems →01.
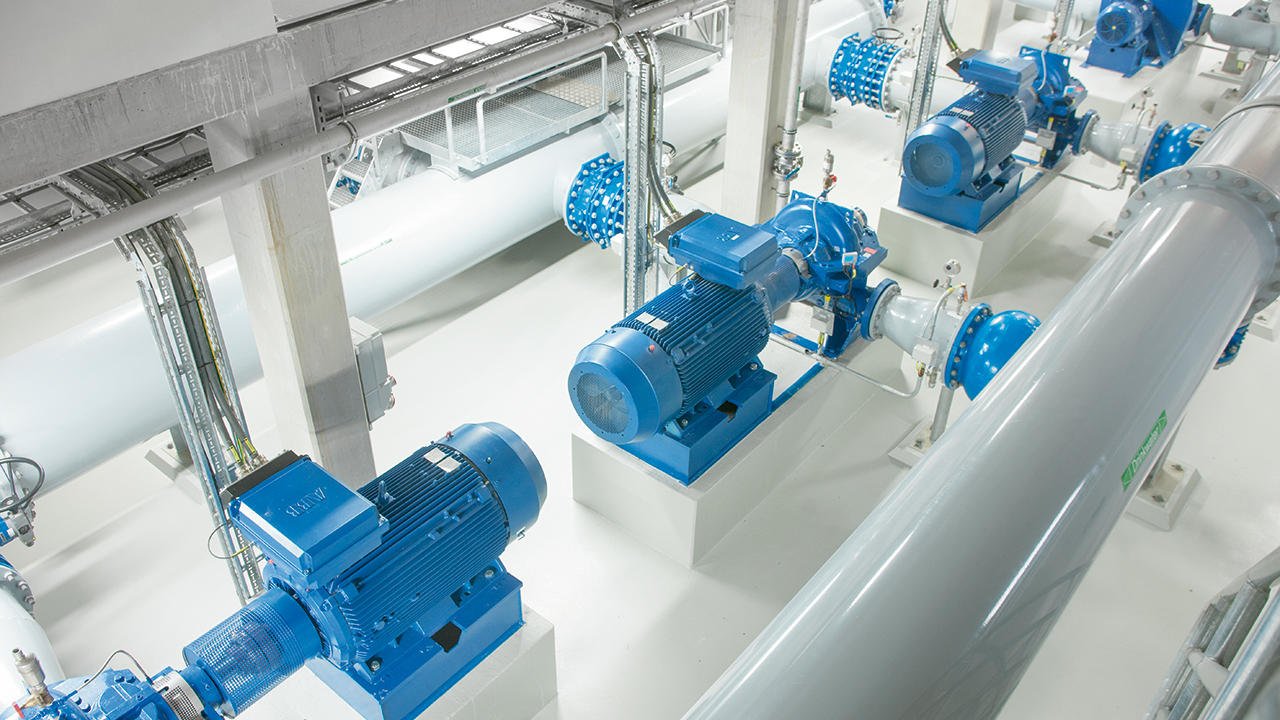
Indeed, smart sensor-based condition monitoring is providing users with the data tools to follow their equipment throughout its entire life cycle and track exactly how such equipment reacts to a user’s specific conditions and processes. Users can track, quantify, and eventually predict maintenance intervals, life-expectancy, and replacement schedules.
Representing a quantum shift away from traditional vibration measures, which require physically attaching discrete-point sensors to collect data, long periods between measurements, and potential safety risks to maintenance personnel, the world of digitized sensing produces continuous, consistent, high-quality information that supports reliable operation and optimization, while making it possible to capture any deviations in standards, thus ensuring real-time quality control [2].
A smart sensor is born
An example of the convergence of these trends and capabilities is the ABB Ability™ Smart Sensor for mechanical products →02. Essentially a monitoring solution that provides an indication of a device’s overall health, the sensor delivers an indication of whether maintenance is needed. In the course of this process it provides warnings, allowing users to plan maintenance before problems arise, and thus avoiding downtime →03.
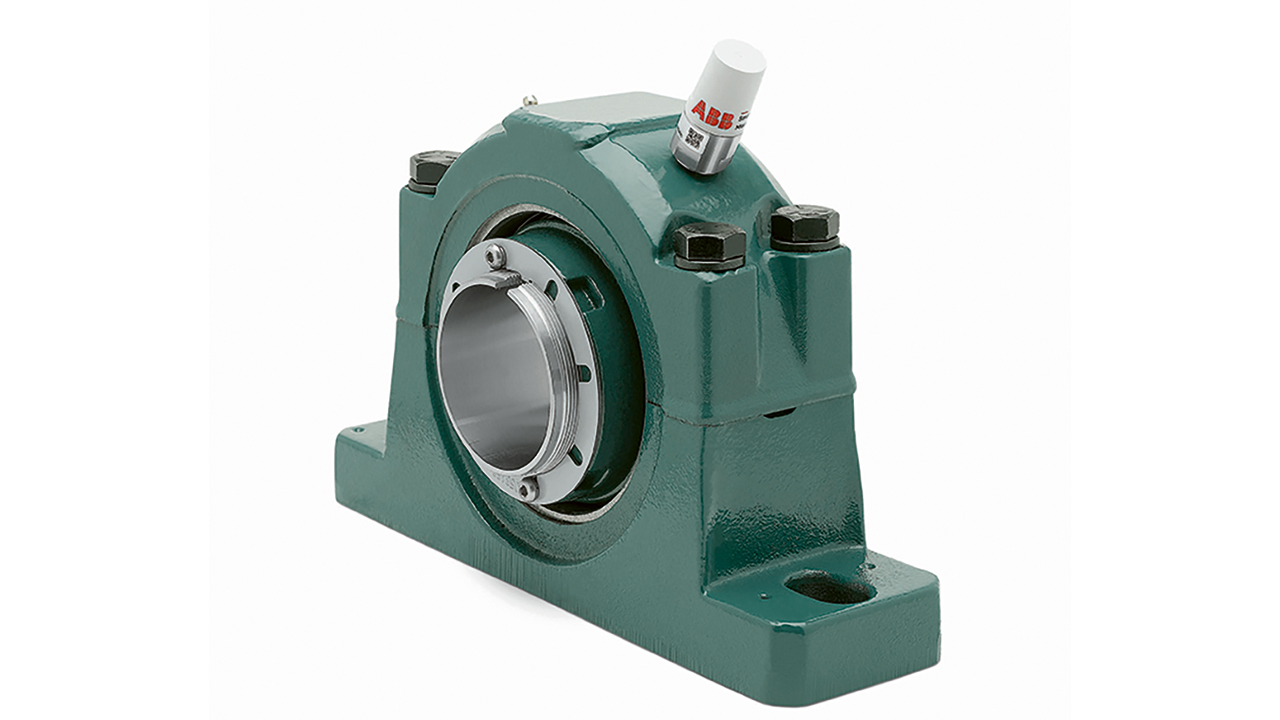
Furthermore, thanks to the sensor’s ability to monitor equipment remotely, maintenance teams can safely check equipment health without the risk of physical contact – a key feature since it obviates the need for technicians to remove safety guards to access equipment for routine maintenance.
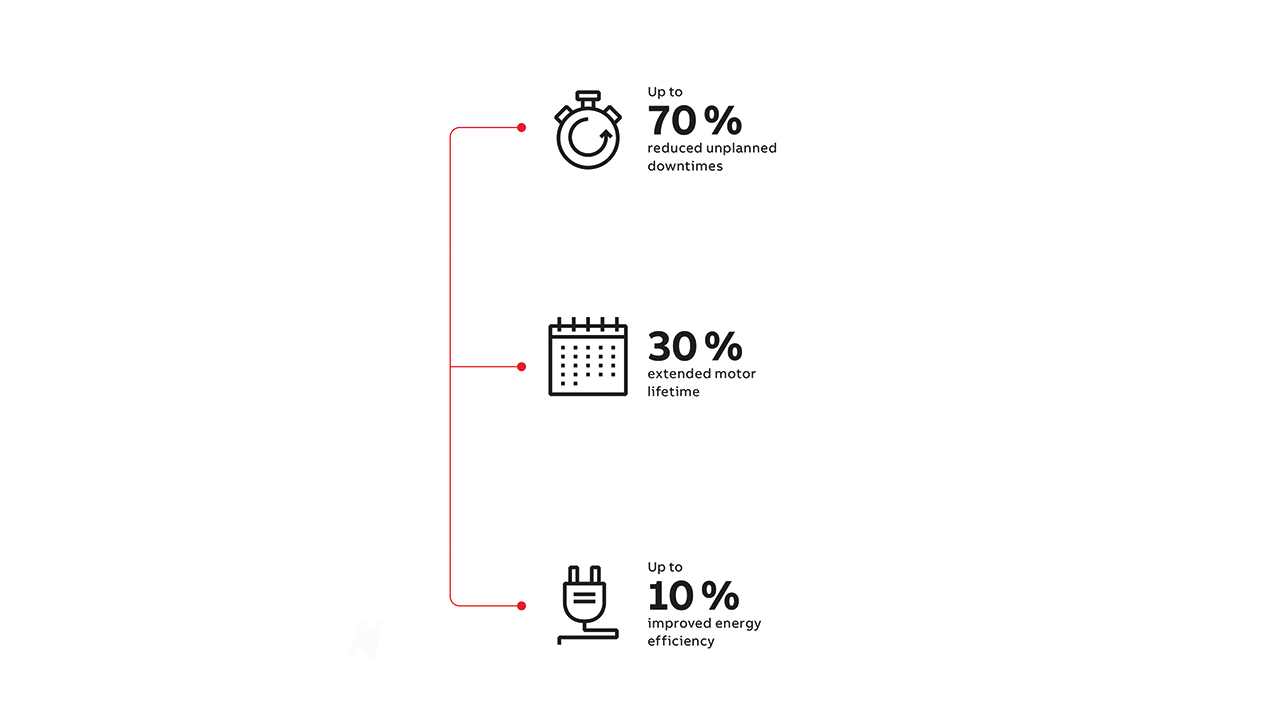
Another big advantage for maintenance teams and operators is that sensor data allows them to focus specifically on those pieces of equipment that actually need attention rather than inspecting every machine – and trying to figure out if a certain level or type of vibration or temperature potentially spells trouble. Rather than calling in experts, the Smart Sensor provides maintenance personnel with the data to make decisions and avoid breakdowns →04.
04a The University of Virginia was founded in 1819. 04b A Smart Sensor in an HVAC application similar to those at the University of Virginia.
04 Over 65 ABB Ability™ Smart Sensors for mechanical products keep critical lab environments stable and equipment performing at the University of Virginia.
Wireless options
Operators can choose how often data is collected – say once every 15 minutes or once every 12 hours – depending on the dynamics of a process. And technicians have several wireless options for accessing and collecting the resulting data: through ABB’s gateway, through a new Plug & Play gateway →05, or by means of a smart phone app, thus making it possible to monitor conditions on the spot or from a remote location.
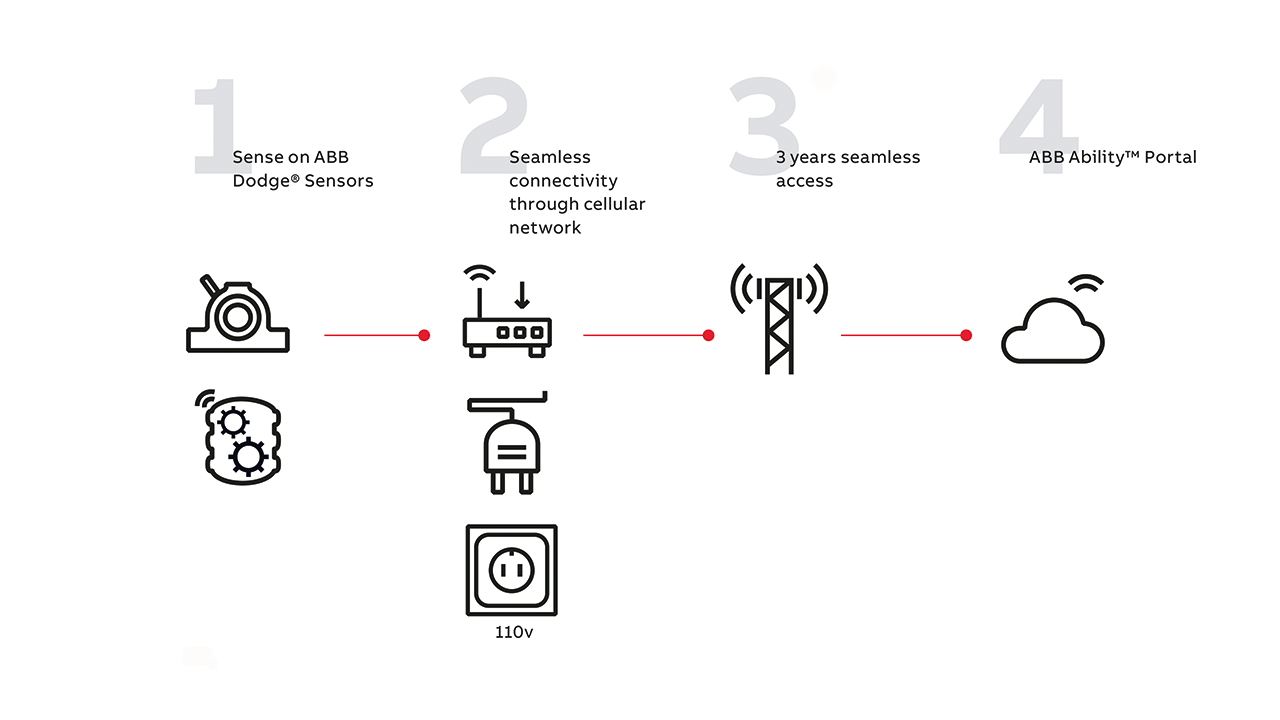
Users can check the status of equipment, for instance, at any time with a smartphone via the ABB Ability™ Smart Sensor app →06. The interface includes a red, yellow and green “traffic light” display that provides a quick overview of the condition of every asset that is being monitored.
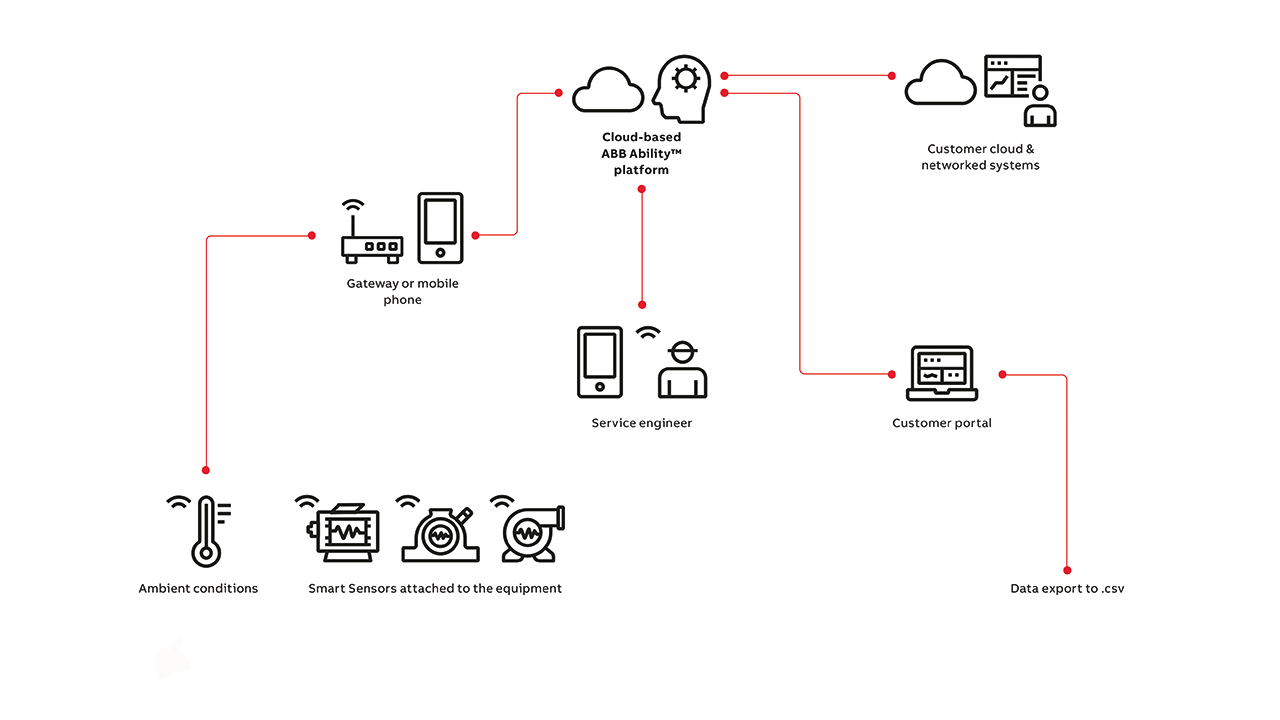
Factory of the future
Smart, connected factories are the future of manufacturing. ABB Ability™ connects users to the power of the Industrial Internet of Things (IIoT) by combining data collected from equipment such as motors, mounted bearings, gearing, variable-speed drives, and pumps. This data can be accessed and analyzed remotely, providing deep insight into the health of the entire process.
Specifically, data can be transferred to the ABB Ability™ Digital Powertrain monitoring platform. This offering is a suite of digital solutions, including devices, software, and services that combines connectivity and data analytics to make customer operations efficient, predictable, and safe.
Data from multiple sensors can be transmitted by a user’s smartphone or the gateway to a secure, cloud-based server, where it can be analyzed by advanced algorithms to identify faults. The data is stored in the ABB Ability™ digital portal, from which it can be accessed and graphically displayed for further analysis. Naturally, all of these capabilities are based on the highest level of cybersecurity. Users have the option of setting up a personal identification number for each sensor and all communications are based on the latest Transport Layer Security (TLS) protocols.
The new plug & play gateway solution, which relies on two of the most popular cellular providers in the U.S., provides seamless connectivity from sensors all the way to the ABB Ability™ digital portal.
All in all, the ABB Ability™ Smart Sensor converts traditional motors, pumps, mounted bearings, and gearings into smart, wirelessly connected devices. It measures key parameters, such as vibrations and temperature-related conditions from the surface of equipment, which can be used to gain meaningful information regarding condition and performance. This enables users to identify inefficiencies within their systems and reduce risks related to operations and maintenance →07.
07a GrainCorp has worked with ABB and A1 Electric Motors to develop a custom solution based on ABB Ability™ Smart Sensor technology. 07b ABB Ability™ Smart Sensor technology is helping GrainCorp by alerting the company to spikes in the temperature of its cooker bearings.
07 ABB Ability™ Smart Sensors have given GrainCorp the ability to actively monitor its equipment bearings.
Furthermore, thanks to new firmware, the Smart Sensor can be updated to also display features such as velocity RMS, change measurement interval, change accelerometer range, and start/stop detection. These features, all of which are the result of customer feedback, significantly enhance the Smart Sensor’s existing capabilities.
Keeping a historic campus operational
The ABB Ability™ Smart Sensor is already paying dividends at the University of Virginia in Charlottesville, US →04a [3]. When the Covid-19 pandemic forced the closing of the University in early 2020, a maintenance team responsible for the campus’s McCormick zone relied on over sixty-five ABB Ability™ Smart Sensors for mechanical products to keep critical lab environments stable and equipment performing. The ability to know when there was a problem – without physically being there – also allowed the university maintenance team to operate safely.
The maintenance team is responsible for ensuring that approximately ten buildings on campus maintain comfortable temperatures for students and faculty, and that each research laboratory in the zone maintains the stable environment needed for controlled experiments. Past maintenance practices required nearly daily adjustment of air handling equipment, much of which is impossible to access without shutting down equipment →04b.
Late in 2019, the team learned about ABB Ability™ Smart Sensors for mechanical products and decided to test a number of them on bearings. The sensors, which immediately began providing real-time information regarding the status of equipment, operated so efficiently that more were soon added to critical air handling unit bearings across the facility. This, in turn, led to the discovery of unidentified problems in equipment that had not previously appeared to require maintenance or replacement. After each correction, the team added a sensor and compared pre- and post-repair results, ultimately determining that post-repair vibration levels were nearly perfect and proving that repairs had been properly performed.
Thanks to the quality of the resulting information, the maintenance team’s schedules and spare parts inventory management have become increasingly predictable. The team now knows what truly needs attention each day, rather than merely relying on a prescribed maintenance schedule, and has been able to minimize and optimize downtime.
Improving the efficiency of the oilseed industry’s refining
The ABB Ability™ Smart Sensor is bringing improved efficiency and savings to Australia’s oilseed industry. GrainCorp Oilseeds →07a is a regional Australia canola seed crusher and oil refiner with a 20-year track record producing canola oil and a range of oils and meals for domestic and international markets [4].
In response to alignment issues and associated overheating in its main cooker bearings, GrainCorp worked with ABB and its channel partner, A1 Electric Motors, to develop a custom solution based on ABB Ability™ Smart Sensor technology. The system designed for GrainCorp featured bearing sensors, motor sensors and a gateway. This has given GrainCorp the ability to actively monitor its equipment bearings and assess their condition with a view to preventing failures.
Indeed, the implementation has been so successful that GrainCorp is now in talks to integrate the sensors into the ABB Ability™ Digital Powertrain monitoring platform. Consolidation into this complete program would enhance A1 Electric Motors’ capability to remotely monitor GrainCorp’s assets on its behalf, which is particularly important since site access is strictly limited and traditional condition monitoring activities are restricted to limited periods. All in all, empowering GrainCorp to proactively monitor its primary cooker bearings and motors and to support these steps with expert service has boosted process efficiency and virtually eliminated the potential of system failure →07b.
References
[1] Eros. L., World Cement, Progress in Real-Time, May, 2020. available: https://search.abb.com/library/Download.aspx?DocumentID=9AKK107680A6860&LanguageCode=en&DocumentPartId=&Action=Launch
[2] Eros. L., World Coal, September/October, 2020. Available: https://www.worldcoal.com/magazine/world-coal/september-2020/
[3] ABB, University of Virginia maintenance team relies on ABB to keep campus running, May 5, 2020. Available: https://new.abb.com/news/detail/61748/university-of-virginia-maintenance-team-relies-on-abb-to-keep-campus-running
[4] ABB, Digital trends: Smart sensors in oil refineries, July 16, 2020. Available: https://new.abb.com/news/detail/65329/digital-trends-smart-sensors-in-oil-refineries