Anurag Nandwana, Gautham Madenoor Ramapriya, Ulaganathan Nallasivam ABB Corporate Research Bangalore, India, anurag.n@in.abb.com, gautham.madenoor-ramapriya@in.abb.com, ulaganathan.nallasivam@in.abb.com; Tarun Mathur ABB Metals Mannheim, Germany, tarun.mathur@in.abb.com; Thota Phanindra, Suraj Kotian, Praveen KC, Amitkumar Chakraborty ABB Metals Bangalore, India, venkata.phanindra@in.abb.com, suraj.s.kotian@in.abb.com, praveen.kc@in.abb.com, amitkumar.chakraborty@in.abb.com
With origins stretching back many centuries, steelmaking is one of the oldest industries still practiced. Technology has greatly changed – and is still changing – the steelmaking process, but the basic principles remain the same. In a modern steelmaking setup, the steel melt shop is the heart of the process. Here, feed materials are treated in a furnace and the resulting molten metal batch – typically weighing around 200 t and at about 1,600 °C – is poured into an empty refractory vessel (a “ladle”) so it can be moved to the next step in the steelmaking process →01. The production and handling of such quantities of molten metal is not only a very energy-intensive undertaking but also a potentially very dangerous one if performed incorrectly.
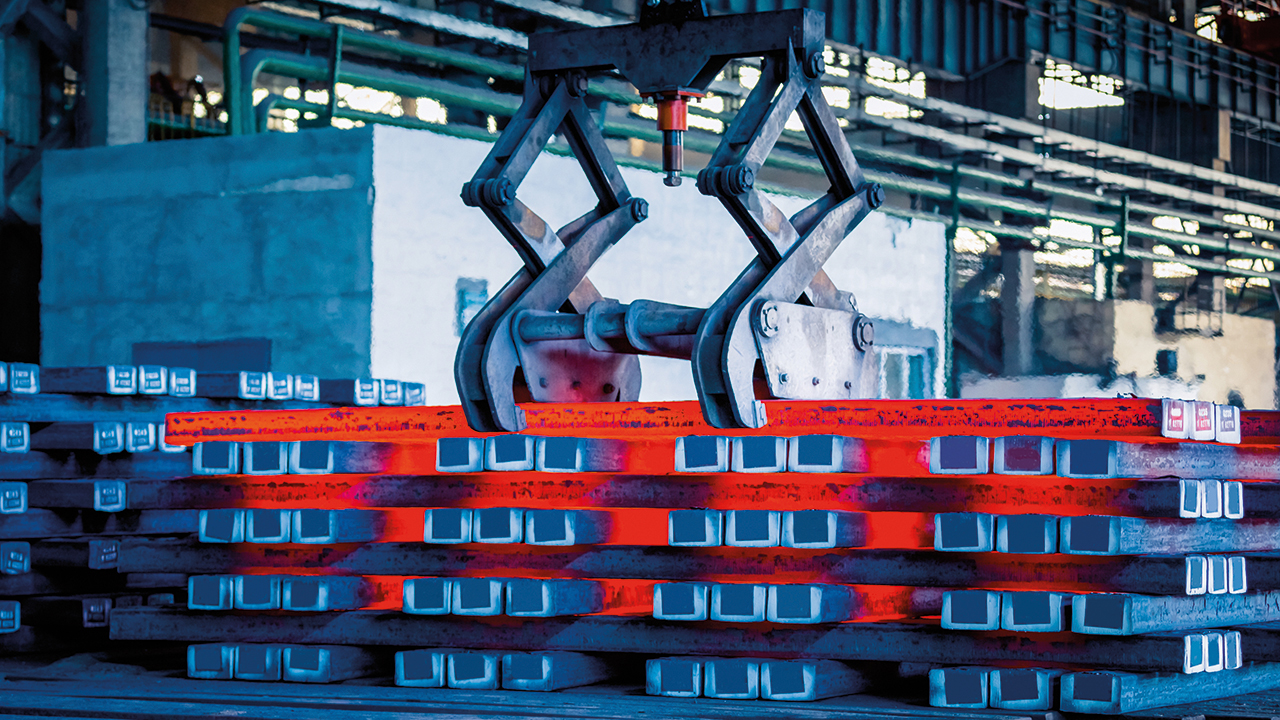
Once filled, the ladle containing the batch of molten metal is moved to the so-called ladle furnace (LF) on a rail-based transfer car or overhead crane. In the LF, the desired composition and temperature homogenization of the molten metal is achieved. Once LF processing is complete, the ladle is transported using overhead cranes to a continuous caster where the melt is formed into solid slabs, billets, etc. This transformation is achieved by draining the ladle’s liquid melt into a buffer vessel (a “tundish”) fixed at the top of the caster mold. The tundish then drains the liquid melt into the mold for continuous casting →02. After emptying all the liquid melt into the tundish of the given caster and subsequent deslagging in the dump yard, the empty ladle is moved, using overhead cranes, to a maintenance stand. After maintenance, the ladle is ready to take the next batch of molten metal.
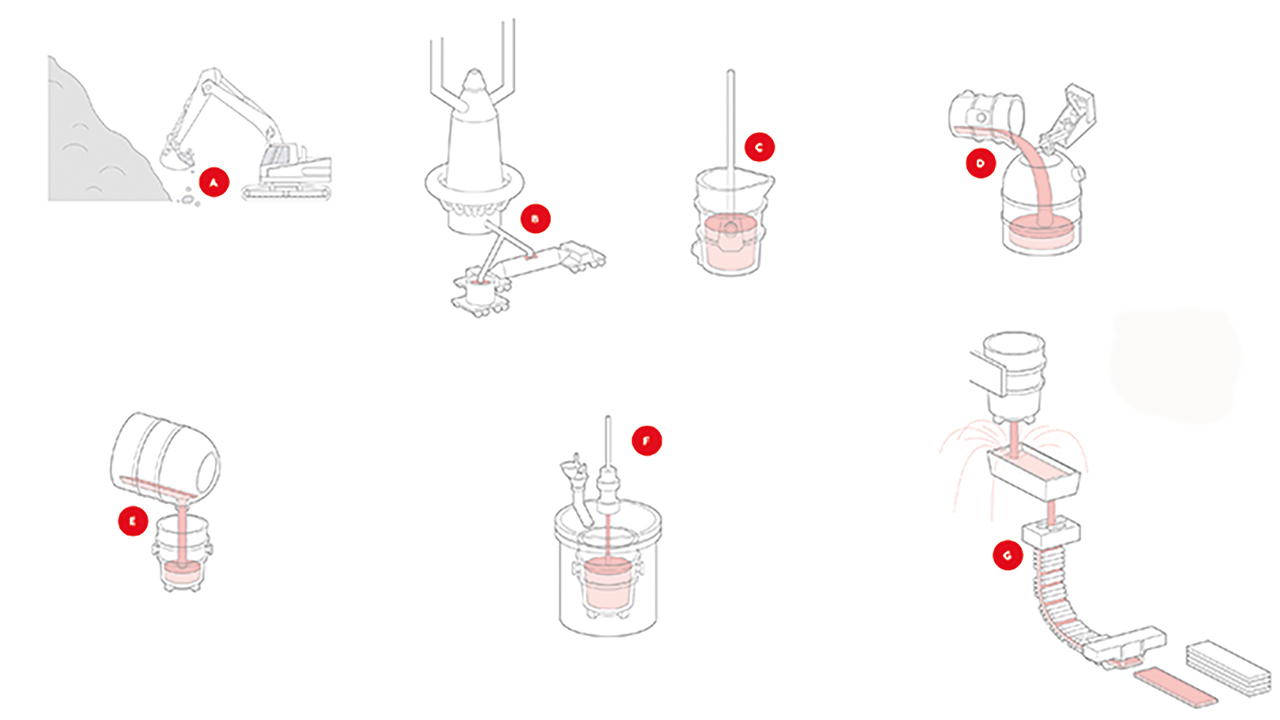
Opportunities for digitalization in the melt shop
A typical melt shop has a limited number of electric arc furnaces/convertors, LFs, continous casters, cranes, transfer cars and, in some plants, degassing equipment and other units for producing cleaner and special steels. It is, therefore, critical that these are utilized effectively. In most melt shops, equipment operation is directed by an operations team that tracks crane locations, unit availability and ongoing and upcoming jobs. Tracking of cranes, ladles, etc. in real time is done by the supervisor – or by dedicated personnel on the ground. These activities pose a major safety risk, considering that melt shop accidents can be fatal.
The supervisor must ensure the continuous availability of molten metal for casting at all the casters, as stoppage of the casting process is highly undesirable. However, the continuous casting step is preceded by the LF batch step. This combination of batch and continuous processes further complicates the supervisor’s real-time, manual decision-making task.
Here, ABB sees an opportunity for a digitized solution to help the supervisor run a safe and productive melt shop.
While productivity improvement has a bearing on revenue generation, equally important from an incurred-cost perspective is an energy-efficient operation of the melt shop. Of particular interest is the energy-intensive LF operation, in which the ladle’s liquid melt is raised to a high temperature. During the subsequent transfer to the caster, the melt will cool and perhaps fall below the appropriate temperature range, necessitating rework and reheating, leading to energy wastage, lowered production efficiency and possible equipment damage. Preemptive overheating to above the requisite temperature range leads to longer processing time and higher energy consumption.
ABB Ability™ Smart Melt Shop, a comprehensive digital solution for melt shops, addresses the issues of safety, productivity and energy efficiency discussed above by incorporating:
• A ladle tracking system for full melt shop visibility.
• A scheduling module for effective job management of cranes and processing equipment for high production efficiency.
• A thermal module for improved energy efficiency and productivity.
Visibility – ladle tracking system
In a melt shop, it is important to know the location and status of ladles and cranes at all times. While cranes may be located visually with ease, the precise location of ladles can be difficult to ascertain. Various ladle-location techniques have been tried – for example, by using radio-frequency identification (RFID) tags. All the techniques tried have limitations – for instance, an RFID tag can only be detected when near a base station and, despite a cooled housing, tags are still prone to failure. ABB AbilityTM Smart Melt Shop gets around these limitations by accurately tracking each ladle carrier in the melt shop. The principle of the method relies on the fact that a ladle can only be moved by a crane or transfer car. A ladle entering the active zone of the melt shop is identified by its ladle number using a camera. As the ladle moves, its location is continuously updated in the run-time database and the same details are displayed in the central monitoring displays →03 until another transfer carrier, such as a crane, comes to the same position and picks it up. Between actual monitoring points, the ladle position is inferred from the expected motion of the ladle carrier.
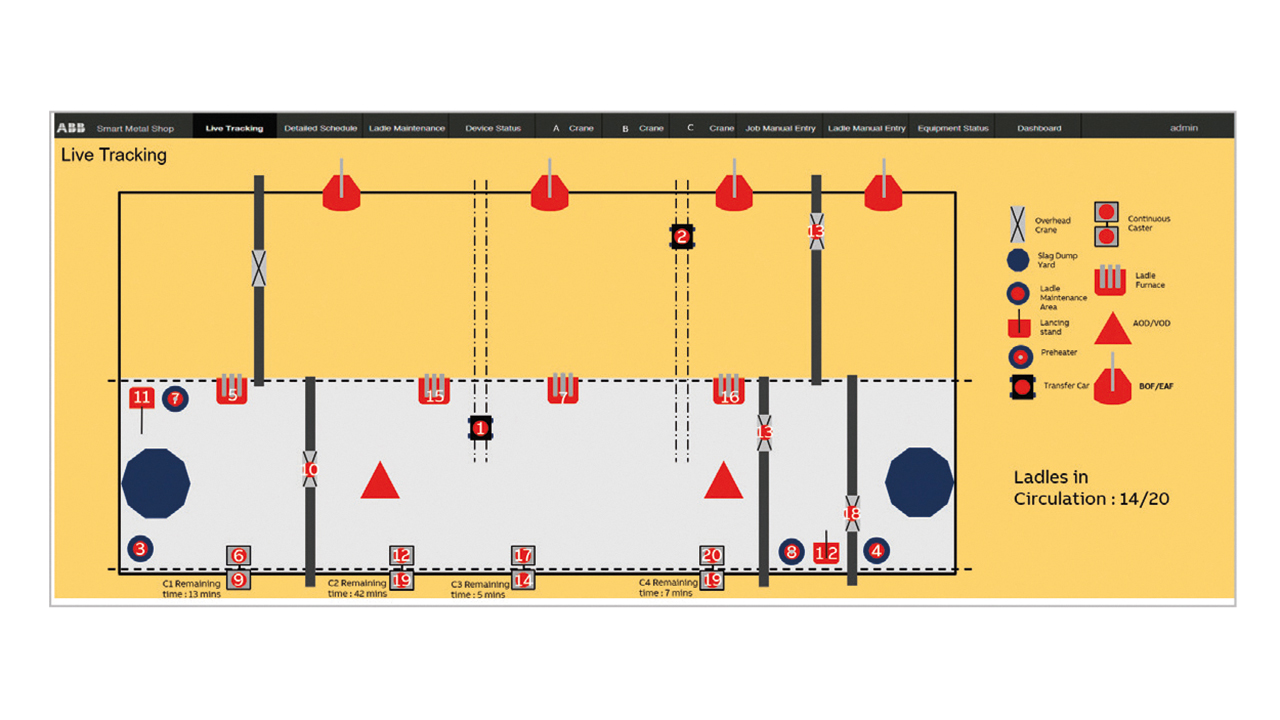
Scheduling module
The scheduling module ABB AbilityTM Smart Melt Shop uses the real-time information in the ladle tracking system to help plan future activities in the most productive and efficient way, up to a particular time horizon. As one schedule of activities draws to a close, the scheduler calculates the next. In generating a schedule for each horizon, the scheduling module:
• Collects information from each piece of processing equipment.
• Establishes where the ladles identified for pick-up need to be dropped off.
• Determines the cranes responsible for the ladle transfers.
• Calculates the precise times at which the ladles are to be picked up and dropped off at the respective equipment by the cranes.
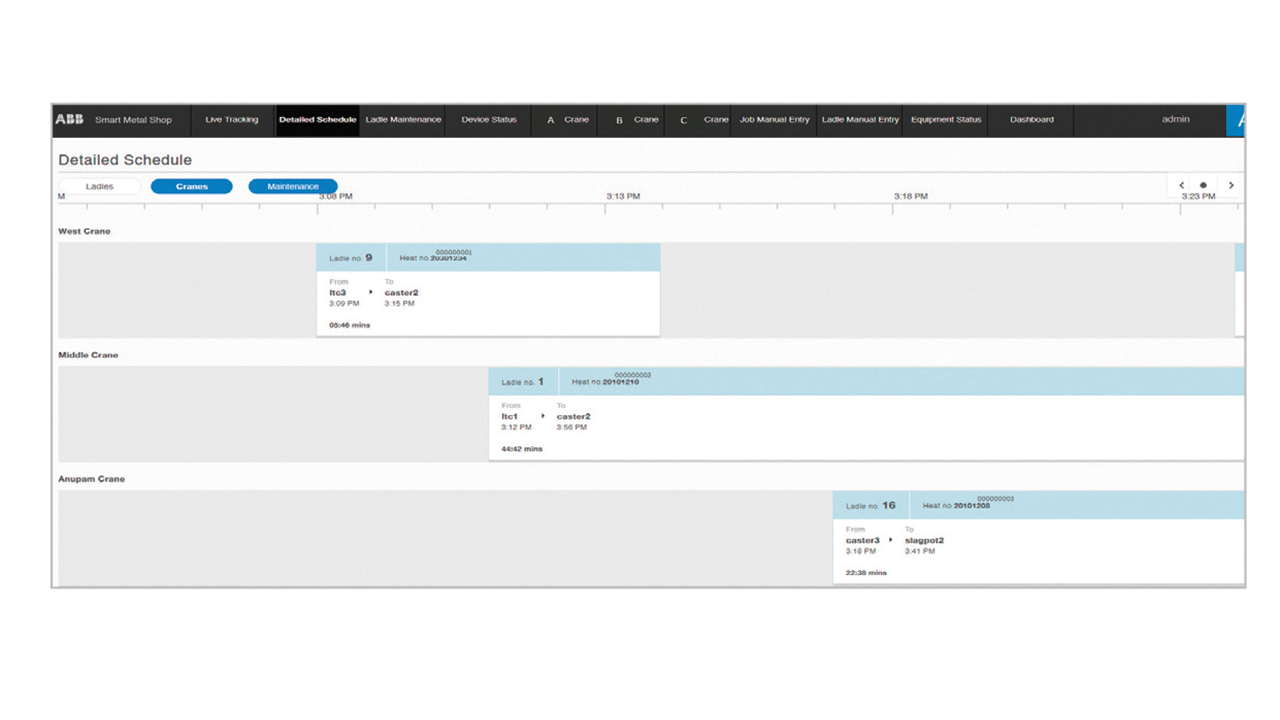
In making these calculations, it must be ensured that certain constraints inherent to melt shop operations are observed. For example, each ladle must follow a particular sequence of operations in a cycle and each ladle must remain at a piece of equipment for a designated period of time before it can be picked up. With these, and more, constraints incorporated, the module produces a schedule for centralized display and supervision →04. Further to the centralized display, a separate screen is made available to each crane operator in their cockpit that shows future scheduled activities specific to that particular crane. This crane-specific extract from the general schedule serves as instructions for the crane’s timely maneuvering →05. Finally, in addition to its utility as a guiding tool for productive operation, the output from the scheduling module also provides useful information to the thermal module.
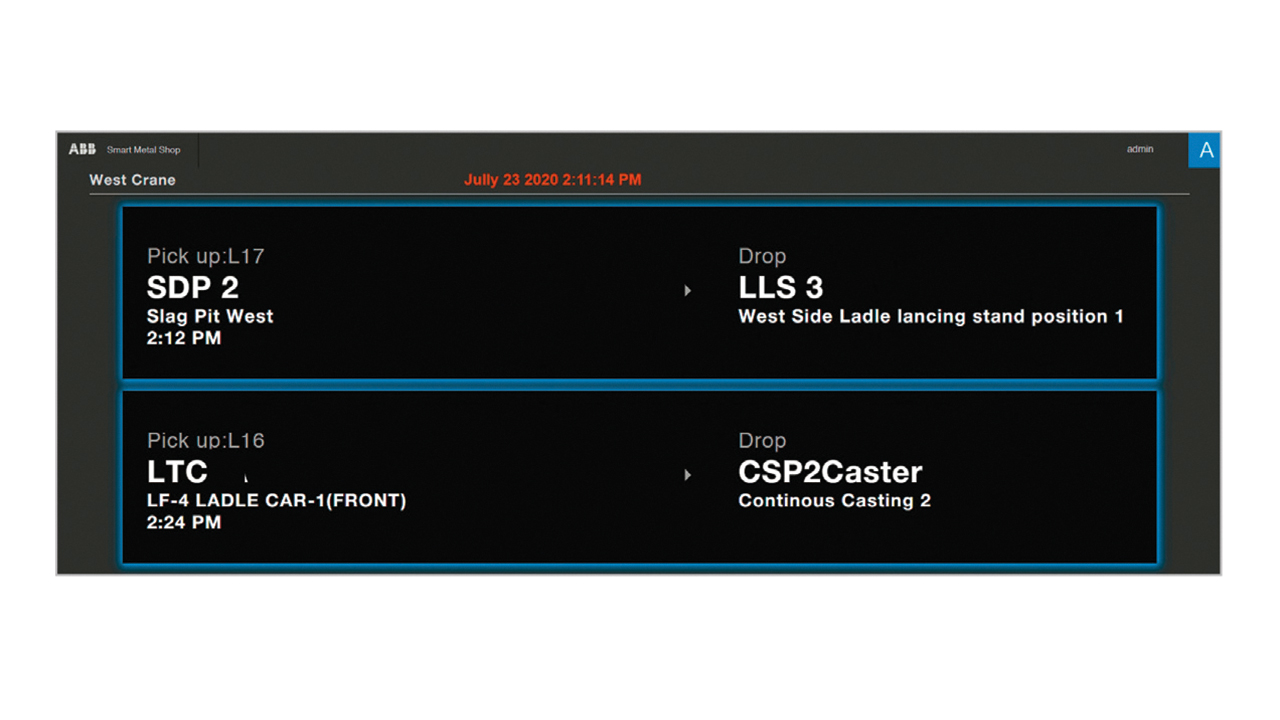
The thermal module
As mentioned earlier, the melt should be within a narrow window of temperature values when it arrives at the caster. However, heat is lost during holding, transfer and teeming (pouring of the melt for casting) →06 – 08.
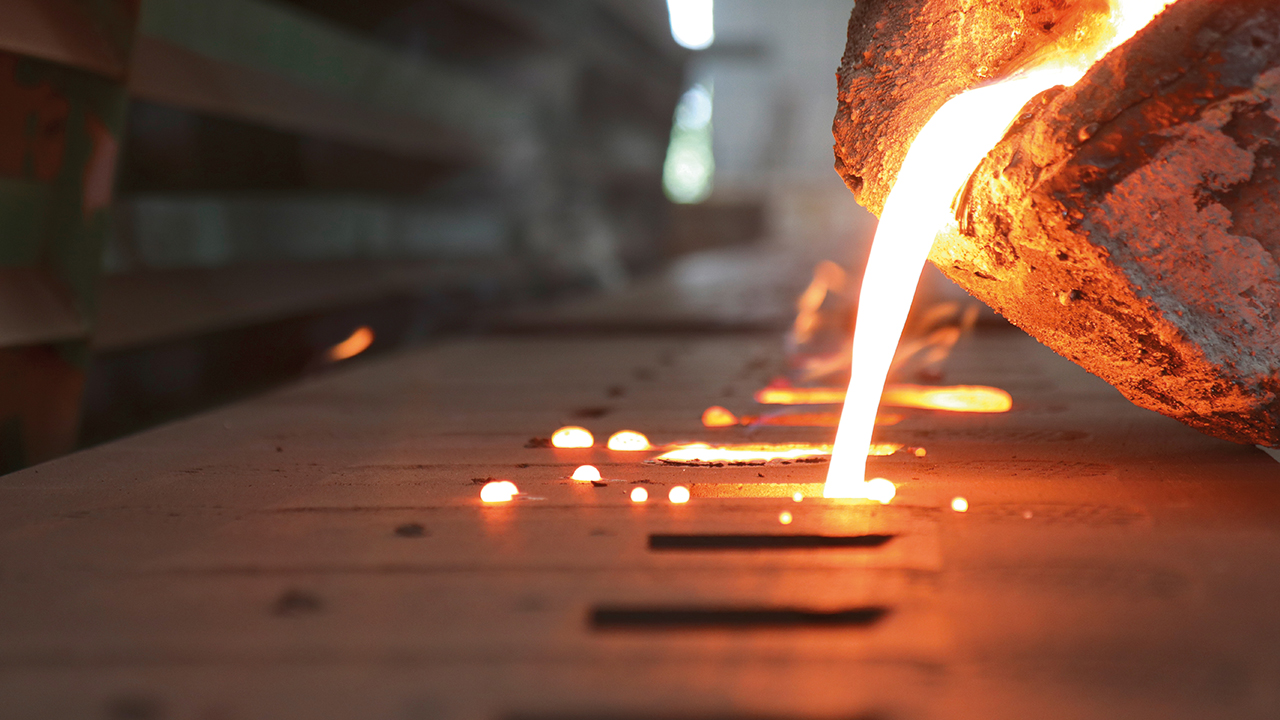
The melt heat loss depends on process variables such as melt properties, holding time, melt temperature, slag layer characteristics and casting type, as well as ladle properties like wall composition, erosion status of the ladle inner lining, ladle thermal history, etc. Since these features are bound to change with every melt load a ladle transfers, the heat loss and, hence, the temperature required at the end of LF operation are also different. The optimum temperature at the LF may vary between batches. In the plant where the model was first implemented (see next section), this variation was more than 40 °C.
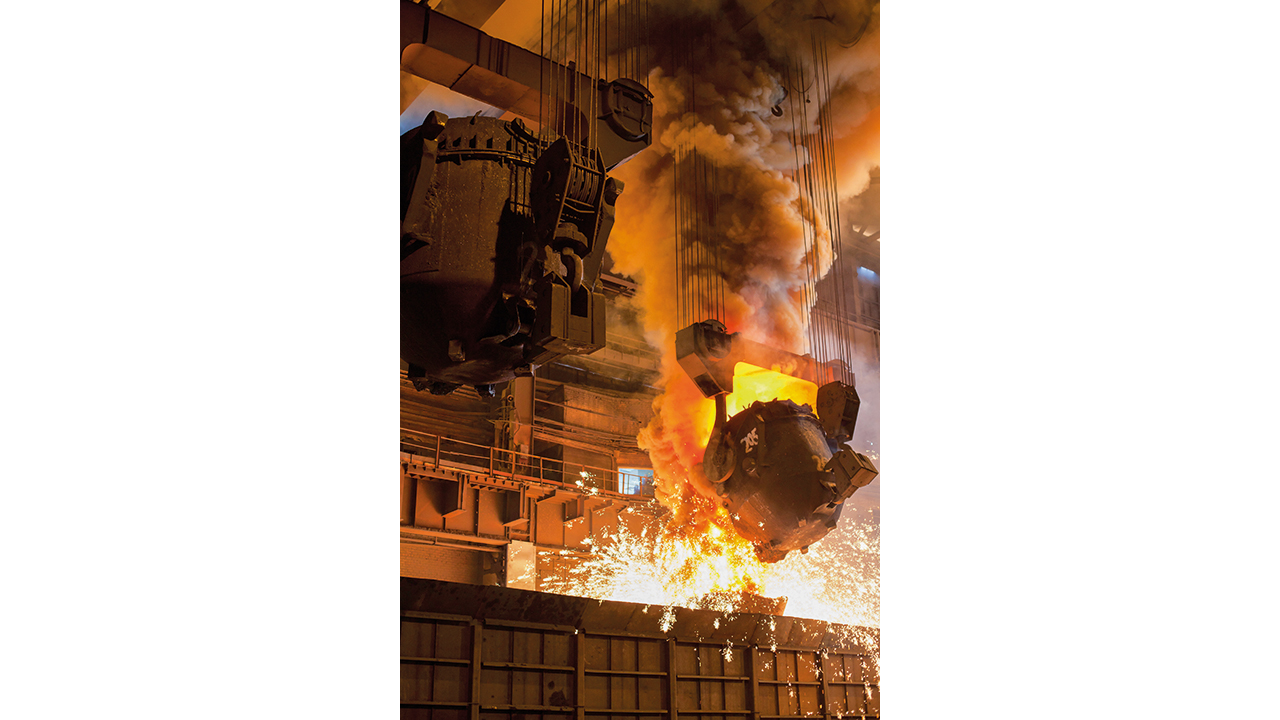
ABB AbilityTM Smart Melt Shop employs a thermal model to estimate this dynamic heat loss behavior and predict the end temperature required at the LF for successful casting. The model employs a discretization scheme and solves for heat transfer through the ladle wall as well as various other interfaces. Based on the heat loss thus calculated, a temperature setpoint is provided to the LF operator.
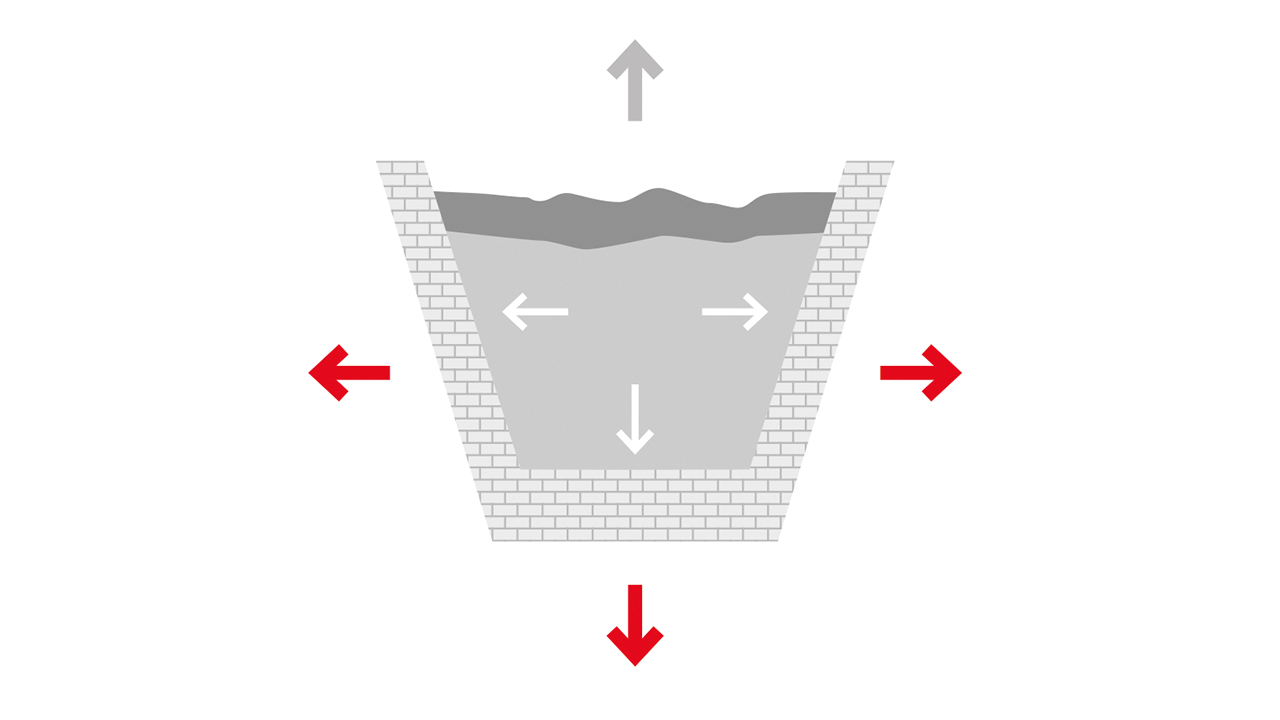
ABB AbilityTM Smart Melt Shop in a steelworks
The Performance Optimization for steel melt shops solution was implemented at a major steelmaker in India and has led to a smooth and efficient operation of the processing units in the melt shop. →09 illustrates the performance of the thermal model. All the batches were heated to a temperature of ±2 °C of the values dictated by the thermal model. All but one (batch 2) of the 16 batches were within the desired temperature range at the caster. By incorporating the model, an estimated yearly saving of 4,500 MWh can be achieved in the melt shop, which has an annual production capacity of four million tons. Side benefits are found in lower electrode consumption and lower ladle relining cost per batch of steel. At the same time, presenting a melt at an optimal temperature to the caster results in higher casting speed and better productivity.
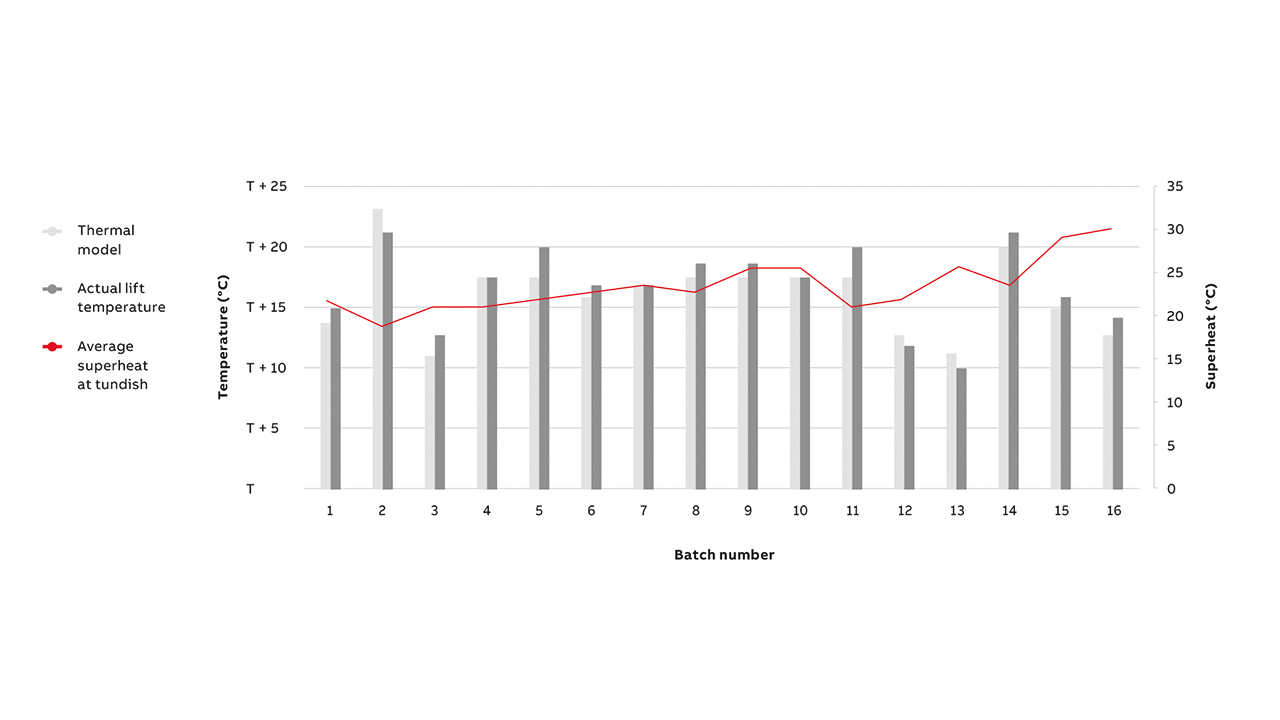
A milestone in steel melt shop autonomy
ABB AbilityTM Smart Melt Shop exemplifies how digitalization can bring about a radical change in manufacturing units with some of the most inhospitable, hazardous and dangerous conditions. The digitalized operation of Performance Optimization for steel melt shops improves productivity and energy efficiency and leads to higher operational safety. Given that many melt shops currently operate on a manual basis, there is broad scope for improvement and automation. ABB AbilityTM Smart Melt Shop sets a milestone on this path toward autonomous and efficient operation.