Stefan Bollmeyer ABB Measurement & Analytics Minden, Germany, stefan.bollmeyer@de.abb.com; Francisco Mendoza ABB Process Automation Ladenburg, Germany, francisco.mendoza@de.abb.com
Over the past decade, Ethernet-based networking technologies have been increasingly adopted in industrial automation settings. Despite this, their adoption in process automation is still constrained [1], mainly due to their limitations in hazardous-location applications. Relying on 4–20 mA analog, 4–20 mA + HART or fieldbus technology, this important sector has had to sacrifice high bandwidth and communication speed for safety.
Significantly, the vast data collected at the field sensor level is, as a result, restricted – or unavailable, generally, for use across the entire enterprise from internal systems to the cloud. Since data and its transmission is the enabler of Industry 4.0 and the Industrial Internet of Things (IIoT), any data network communication dam prevents enterprises in the process industries from achieving the full value potential inherent in data availability and transfer.
For this reason, ABB joined a consortium of 11 other market leaders and three communications standards development organizations to develop the Advanced Physical Layer (APL) standard to make field-level Ethernet a reality for process automation industries even in hazardous areas [1]. The Ethernet-APL technology developed is simple, practical, compatible, easy-to-use and brings bandwidth and communication speed to a level that allows process industries to reap the rewards associated with digitalization such as asset management and condition monitoring applications. Concurrently, ABB has worked to expand the benefits possible through use of Ethernet-APL through their research on IIoT devices. Available prototypes demonstrate that it is possible to bring modern protocols, like OPC UA, with cyber security and information modeling capabilities that are suitable for bridging IT/OT boundaries into small resource-constrained field devices [2]. With the technology introduction in June 2021, such products, combined with Ethernet-APL, will allow process industries to leverage data across the value chain from the field-level device to the control system, the cloud and everywhere in between [2].
Extending Ethernet to process industry
Communication and networking technologies developed rapidly over the past decades →01. Today, Ethernet is the widely accepted standard for wired digital technologies in the great majority of industries and business applications, with its huge set of standardized tools for installation, troubleshooting, and diagnostics, as well as high bandwidth and communication speed. Still, its adoption is comparatively limited in process industry [1,3]. Why is this so? Two reasons stand out: the simplicity and cost-effectiveness, thus dominance, of legacy communication technologies installed and the hazardous nature of many process industry environments [3]. Cost, suitability and practicality make the extension of Ethernet-level technology to the field challenging.
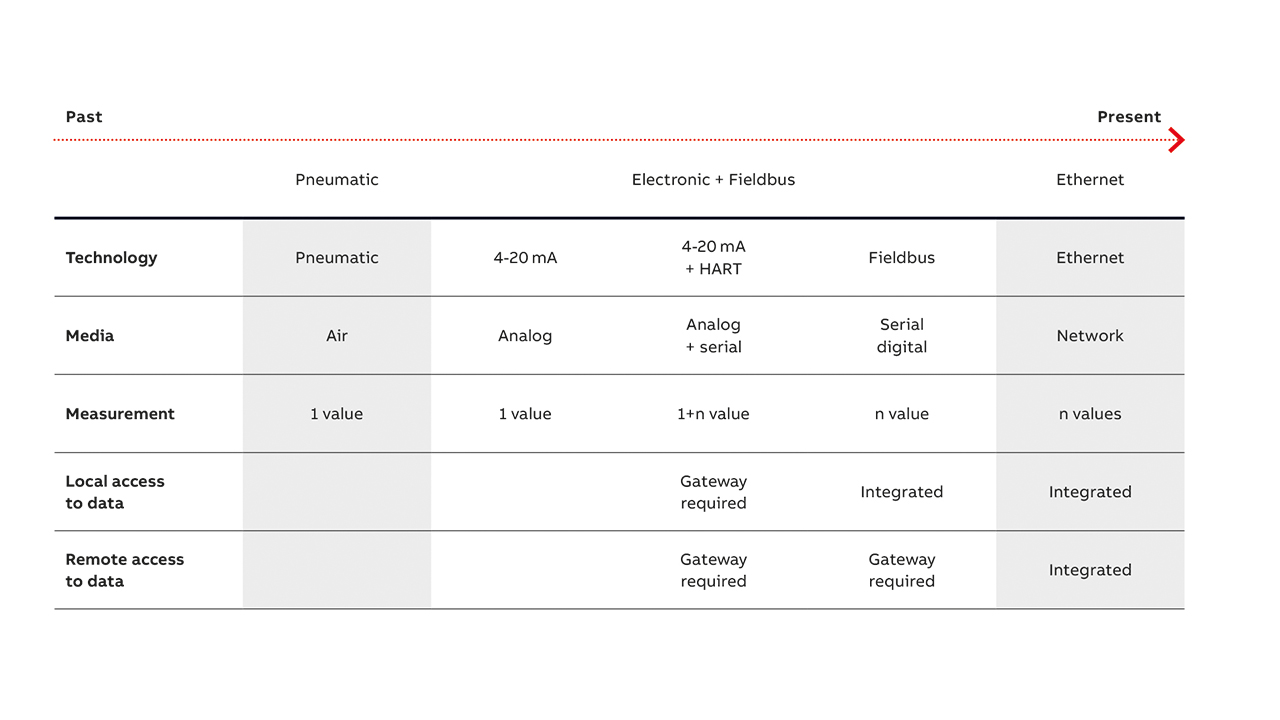
Data transfer technology over time
Early on, the predominant way to connect field instruments to distributed control systems (DCSs) to measure process values relied on simple wiring to convert analog measurements to 4-20 mA analog signals [3]. HART technology later introduced digital communication on the top of the analog signal, thus maintaining the beneficial simplicity of conventional wiring. Nonetheless, bandwidth and communication speed, albeit digital, were extremely low (1200 Bps) →01 – 02. Not surprisingly, this technology still makes up the largest segment of the market in terms of installed base and greenfield plant design and construction [3].
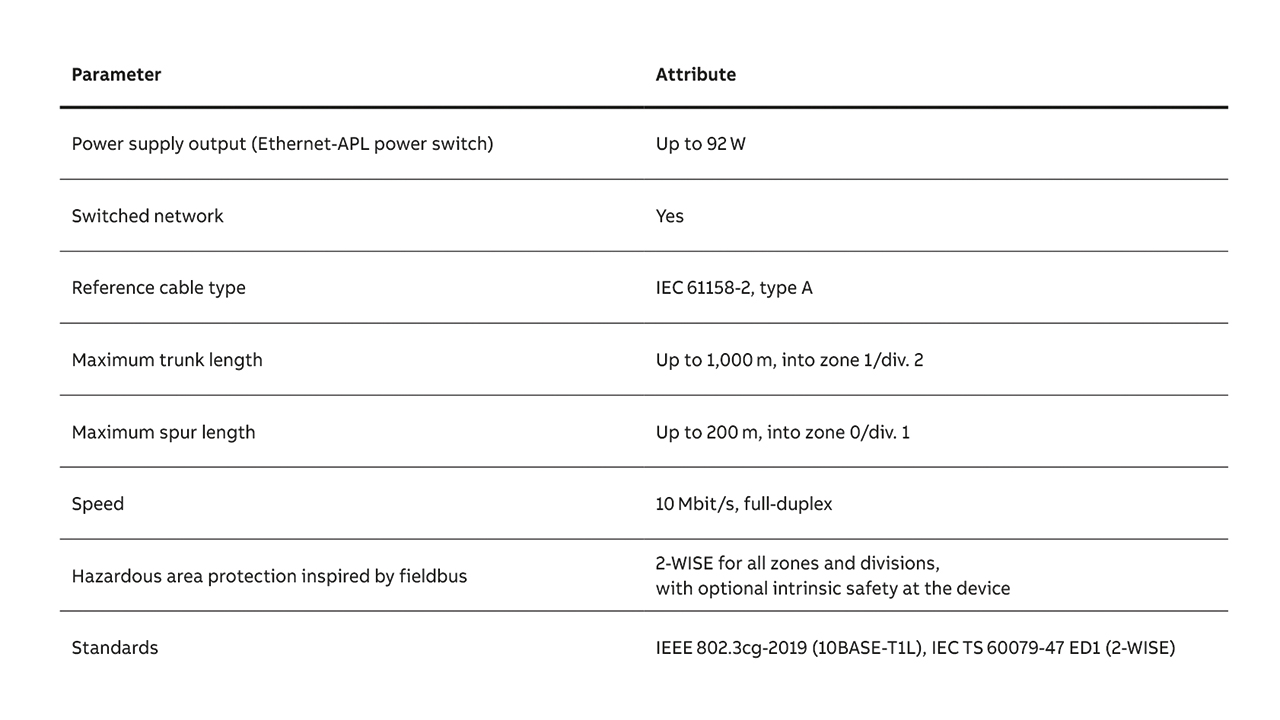
Another technology, the fully digital serial fieldbus technology, introduced in the 1990s, became the technology-of-choice in the early years of the second millennium. With improved bandwidth (31.25 Kbps) →02, this technology requires gateways and has proven too complex in engineering, operations and maintenance to truly satisfy process industry vendors. What process industry needs for a fully digital future is a technology with an Ethernet-level bandwidth and communication speed that is as simple to engineer, operate and maintain as the 2-wire, 4-20 mA solution, yet extends to the field device and operates in hazardous areas.
Collaboration: key to an Ethernet-level solution
Establishing an Ethernet-type communication technology that fulfills the aforementioned demands is a tall order. Challenges abound: short cable reach (100 m), complex wiring (Ethernet twisted-pair cables) and lack of safety for use in hazardous areas. Rigorous research and development efforts as well as strong cooperation between the process automation leaders and standards organizations are fundamental to resolve these difficulties. Recognizing the need to establish fully digitalized plants and enable Industry 4.0 applications for the future of process industries in 2010, key industry leaders established the critical importance of extending Ethernet connectivity to the field-level [3]. In 2015, a group consisting of leading suppliers of process automation; ABB, Emerson, Endress+Hauser, Krohne, Pepperl + Fuchs, Phoenix Contact, R. Stahl, Rockwell Automation, Samson, Siemens, Vega, and Yokogawa with backing from leading standards development organizations (SDOs): FieldComm Group, ODVA and PROFIBUS & PROFINET International initialized the Advanced Physical Layer (APL) project [3]. They established in 2018 that any solution to be sustainable should be fully compatible and embrace the IEEE 802.3 Ethernet standard and satisfy specific criteria [3]:
• Two-wire cable
• Long cable runs
• Power and communication on the same cable
• Support of all explosion protection techniques including intrinsic safety
• Simple installation technology
• Reuse of existing fieldbus cable type ‘A’, which reduces cost and provides easy migration strategies from fieldbus to Ethernet-APL
• Resilience to electro-magnetic interference
• Support of surge protection
Ethernet-APL
Ethernet-APL, the culmination of a nearly decade long journey to extend Ethernet to the field, is an offshoot of the original 802.3 Ethernet standard with the recently published IEEE 802.3cg-2019 standard [4]. The 10 BASE-T1L variant of this standard simplifies the network architecture and vastly increases the available bandwidth for digital instrument communications (300 times faster than FOUNDATION Fieldbus H1 or PROFIBUS PA, and more than 8,000 times faster than the early HART protocol) →02, thus achieving the aforementioned criteria issued by the APL project [1]. Ethernet-APL is an enhanced physical layer that enables single pair Ethernet (SPE) communication over a distance of 1,000 m with the provision of power to devices as an option [3] →02. By defining Port Profiles matching different explosion protection classes, APL enables the extension of 10BASE-T1L for use in hazardous areas – an essential technical achievement for the process industries. Additionally, the soon-to-be released IEC technical specification, Two-wire Intrinsically Safe Ethernet (2-WISE), sets the guidelines for intrinsic safety (without the need for calculations) for loop-powered and separately powered instruments in hazardous areas up to Zone 0, 1, and 2 / Division 1 and 2 →03, [4]. With an expected release in 2021, 2-WISE, based on Fieldbus Intrinsically Safe Concept (FISCO), will simplify the engineering and verification of this technology [4].
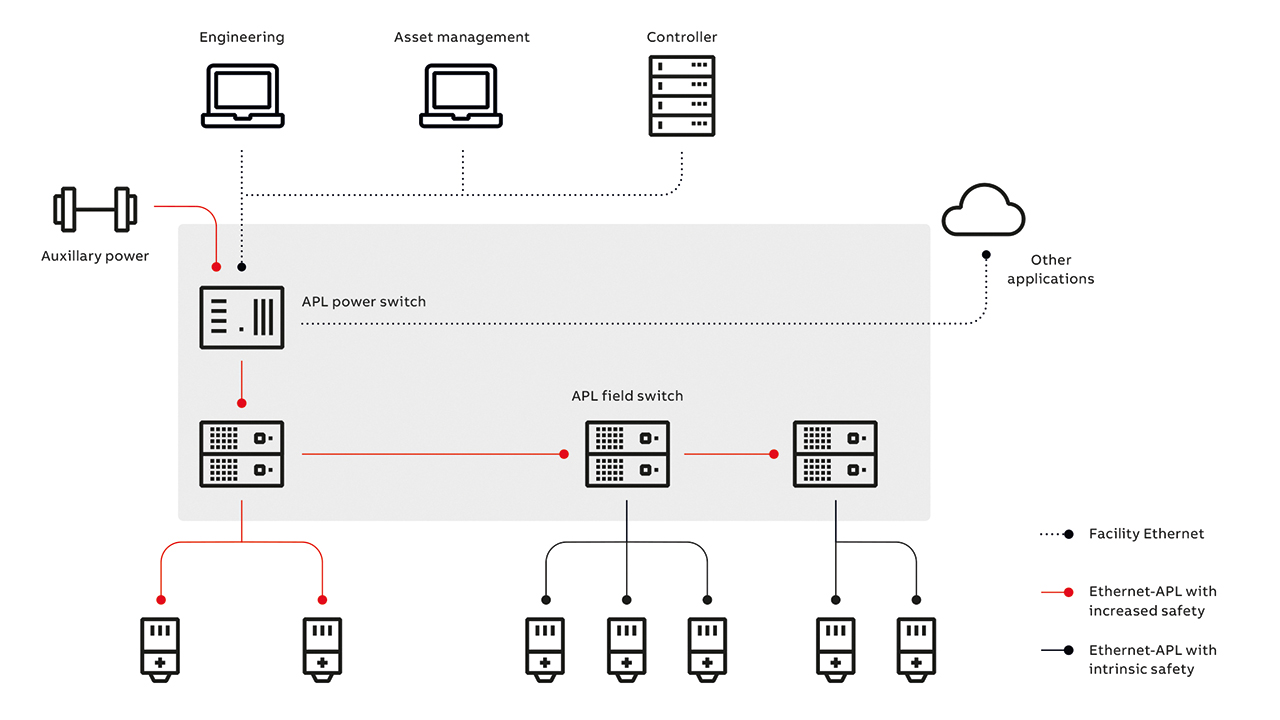
Supporting topologies
Ethernet-APL is designed to support various installation topologies, with optional redundancy or resiliency concepts and trunk-and-spur. The trunk provides high power and signal levels for long cable lengths, up to 1,000 m. Whereas, the spur carries lower power with optional intrinsic safety for lengths up to 200 m. Ethernet-APL explicitly specifies point-to-point connections only with each connection between communications partners constituting a segment. Ethernet-APL switches thus isolate communications between segments.
Ethernet-APL success: rooted in protocol compatibility
Despite the promise of success, adoption of Ethernet-APL technology will take time [3]. With analog 4-20 mA + HART technology still dominant, process industries will need convincing reasons to revamp their engineering and systems to employ APL. Reluctance to shift away from legacy technology can only be overcome if the value proposition to incorporate APL technology is clear.
Since Ethernet-APL supports EtherNet/IP, HART-IP, OPC UA, PROFINET, and other higher-level protocols, this business shift is realistic. Nowadays, many process industries utilize DCS systems that already support PROFINET and/or Ethernet/IP protocols, and so will be able to easily adopt Ethernet-APL [1]. And, because APL eliminates the need for gateways or other protocol conversions, industries should swiftly recognize the added value achieved through reduced complexity, lower cost of ownership, improved usability and robustness as compared to conventional fieldbus systems or the analog 4-20 mA + HART systems.
Significantly, modern protocols can run over APL too [1]. ABB has been investigating one protocol in particular – Open Platform Communication Unified Architecture (OPC UA). Ethernet-APL allows OPC UA to be deployed directly in field devices for easier integration with IT and OT applications of Industry 4.0.
Extending Ethernet-APL to the field level with OPC UA integrated devices
Around 2016, the customer organization Standardization Association for Measurement and Control in Chemical Industries (NAMUR) released a position paper (finally resulting in NAMUR Recommendation NE 168 in 2018 [5,6]), pointing out that any Ethernet solution for devices must overcome the limitations of fieldbus systems – in other words, vendors should avoid making mistakes inherent in previous generations of fieldbuses [5,6]. Seizing on this, ABB focused on removing existing barriers that interfere with information communication, such as the massive conversions and data description that traditional fieldbuses require to make data useful in a process plant, eg for control, monitoring, optimization and maintenance. In particular, OPC UA technology provides data with semantic information and according to ABB could eliminate, if properly deployed, the inconvenience of fieldbus-type barriers. Beginning from 2017, ABB developed a series of prototypes to demonstrate that OPC UA is suitable for transferring device data securely with sufficient performance and low memory footprint, which is suitable for resource constrained devices. Prior to this, OPC UA was only used for interchanging information between more powerful devices like PC servers or controllers.
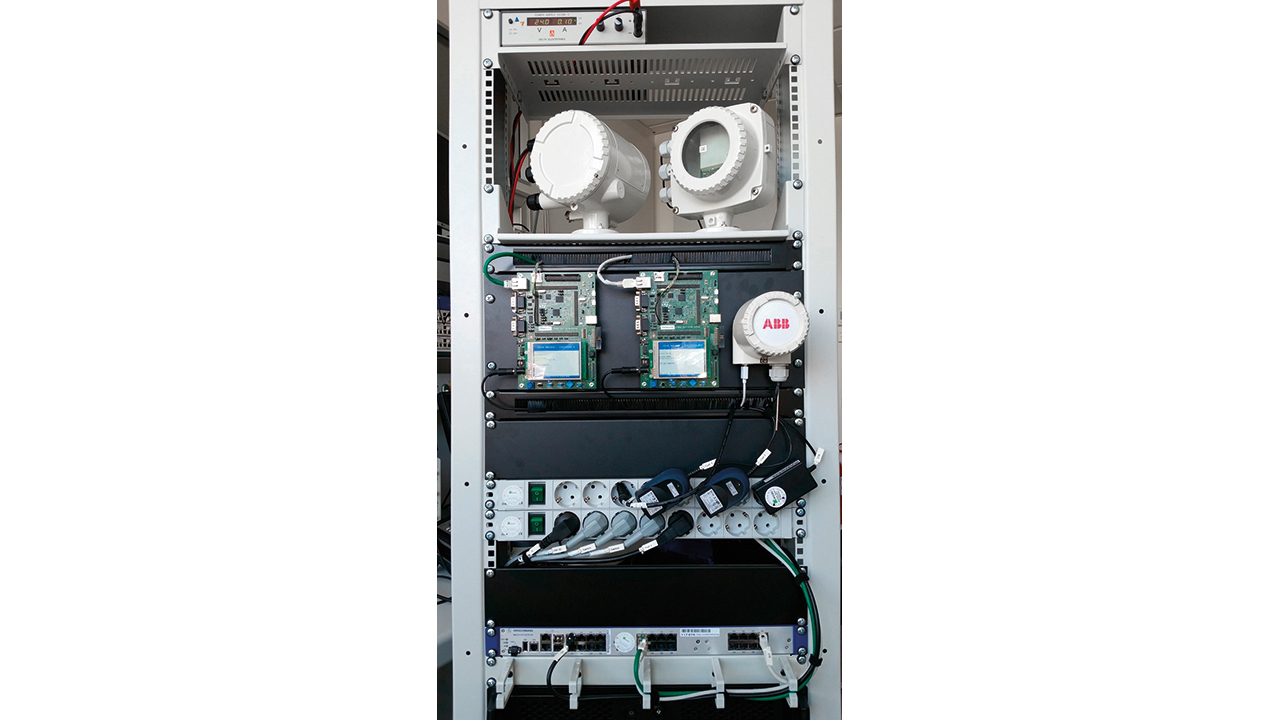
Initially, ABB evaluated the applicability of OPC UA to 4-wire flow meters (power and communication on separate wires). Relying on an Ethernet adapter that converted the HART protocol from the device into an OPC UA server, ABB achieved sufficient performance; hence, it was possible to access hundreds of device parameters via OPC UA easily, without the need of additional device descriptions →04. Furthermore, ABB investigated the applicability of OPC UA to lower-footprint devices such as level transmitters, with low-power consumption requirements →05. Choosing a newly available OPC UA communication stack that targets embedded devices (high performance and low memory footprint), ABB could use an Ethernet platform that natively integrates OPC UA together with the full device functionality into this prototype. Hence, power consumption and memory footprint could be further reduced while maintaining update rates.
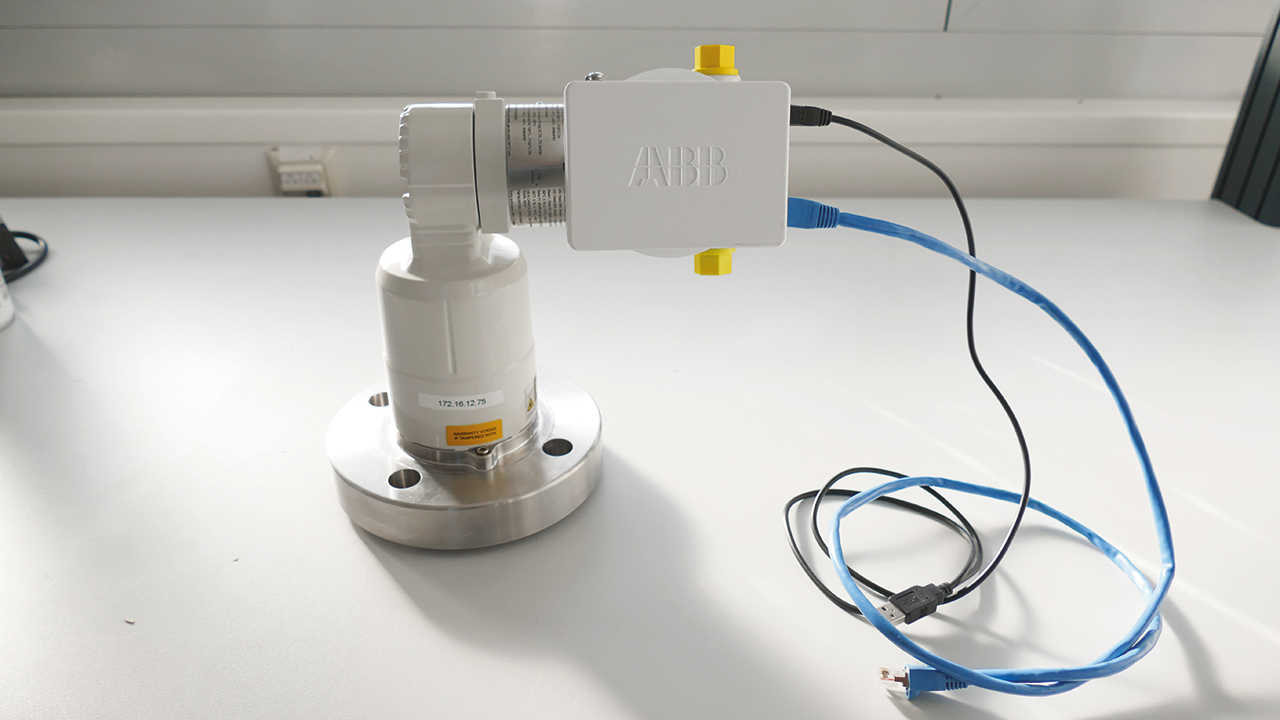
Understanding that the result matched the performance and power budget, which can be provided with Ethernet-APL, ABB then implemented a native OPC UA device with power and communication over Ethernet-APL. Here, the level transmitter application was successfully ported to evaluation boards, developed by the Ethernet-APL consortium →06. Next, the ABB team successfully evaluated the ability of OPC UA to be ported and integrated to a pressure transmitter prototype that requires one of the fastest update rates (2 ms) encountered for process instruments.
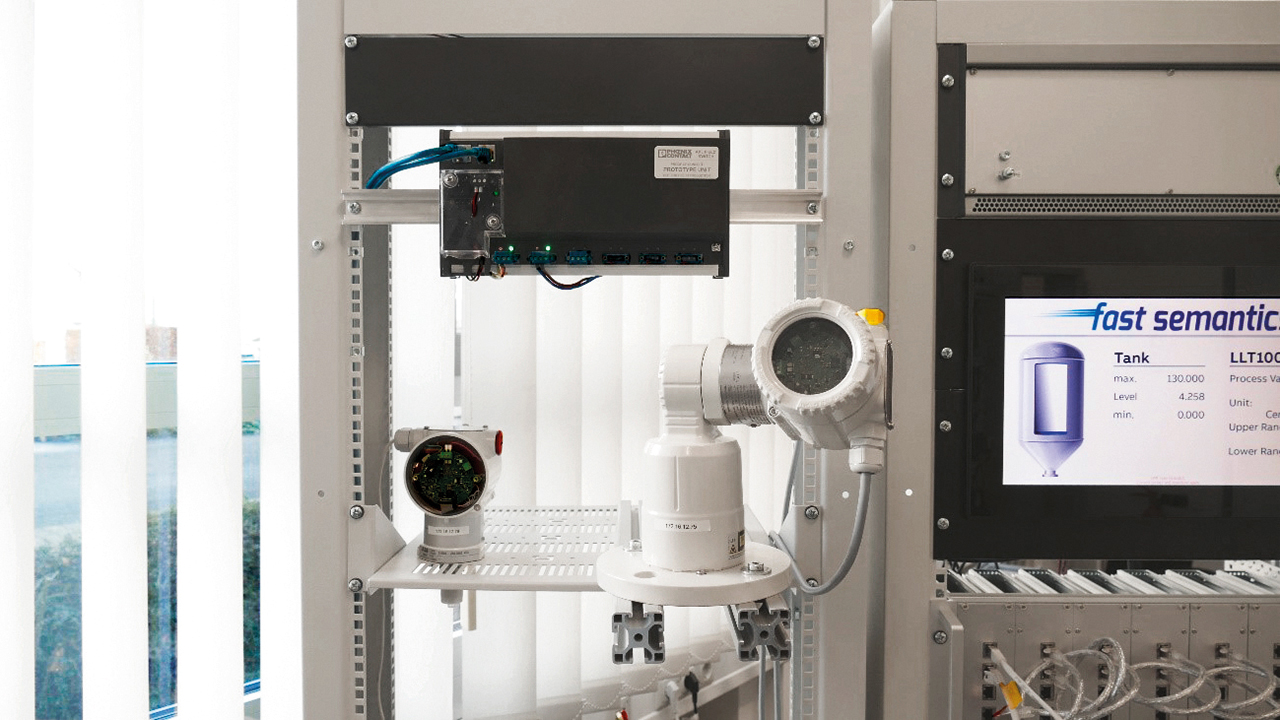
Currently, these ABB device prototypes are used by selected customers in their first Ethernet-APL testbeds and they demonstrate full interoperability at a multi-vendor Ethernet-APL network. Thus, ABB is not only implementing Ethernet-APL devices, it is driving the standardization of OPC UA-based devices together with the OPC Foundation and FieldComm Group standard organizations.
Based on these test cases, customers can be confident that once OPC UA field devices are commercially available, Ethernet bandwidth and speed will be possible with two-wire power consumption and communication, and unproblematic fast update rates →07. With information models embedded in the device that incorporate semantics in the information being transmitted, these devices do not need additional descriptions and can be easily integrated with different applications.
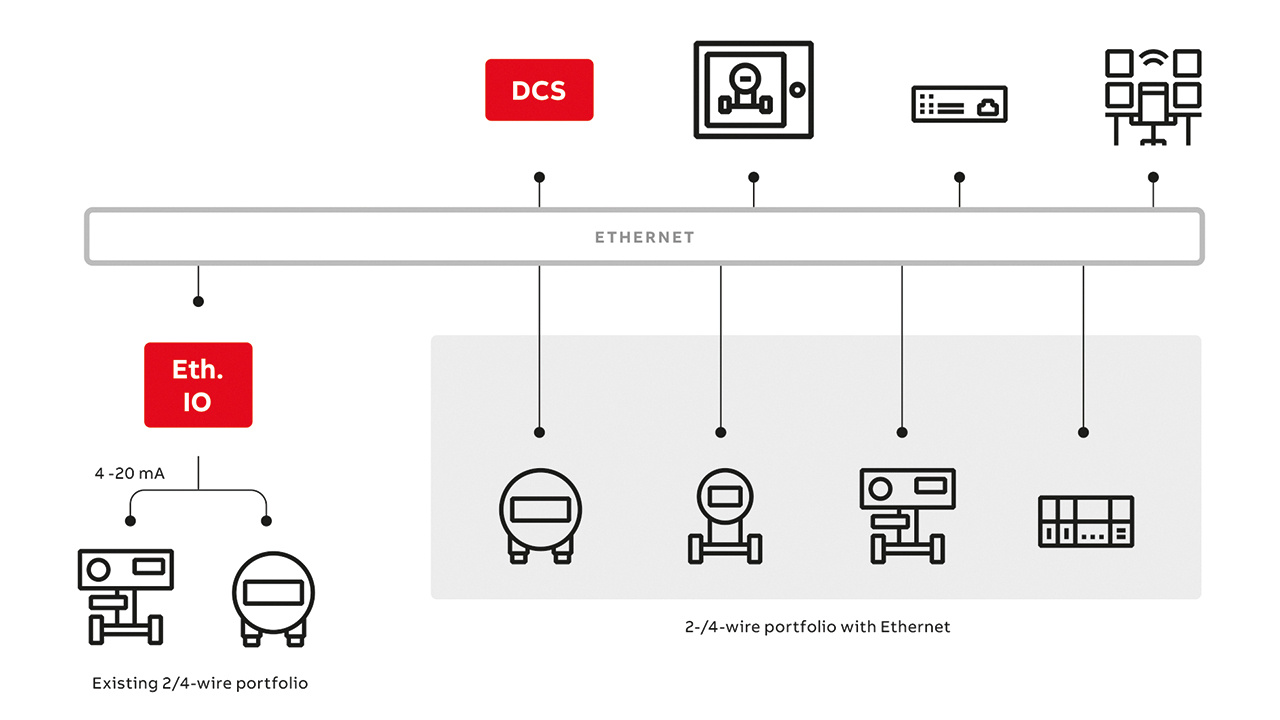
Creating value from the field to the enterprise
With a simple network architecture and no need for protocol conversion, Ethernet-APL is highly compatible and easy to use. With a speed of 10 Mbps Ethernet-APL exhibits the simplicity of the 4-20 mA communication protocol, but with a Ethernet-level bandwidth suitable for instrument communication and multi-protocol support. By enabling connectivity with broadly distributed two-wire loop powered field instruments in hazardous location areas, Ethernet-APL enables improved communication performance without sacrificing safety →08. By integrating OPC UA technology, with Ethernet-APL, ABB makes this universally applicable and modern communication protocol available for field devices. The resultant semantics and information models remove the need for descriptions and will help bridge the gap between Operation Technology (OT) and Information Technology (IT).
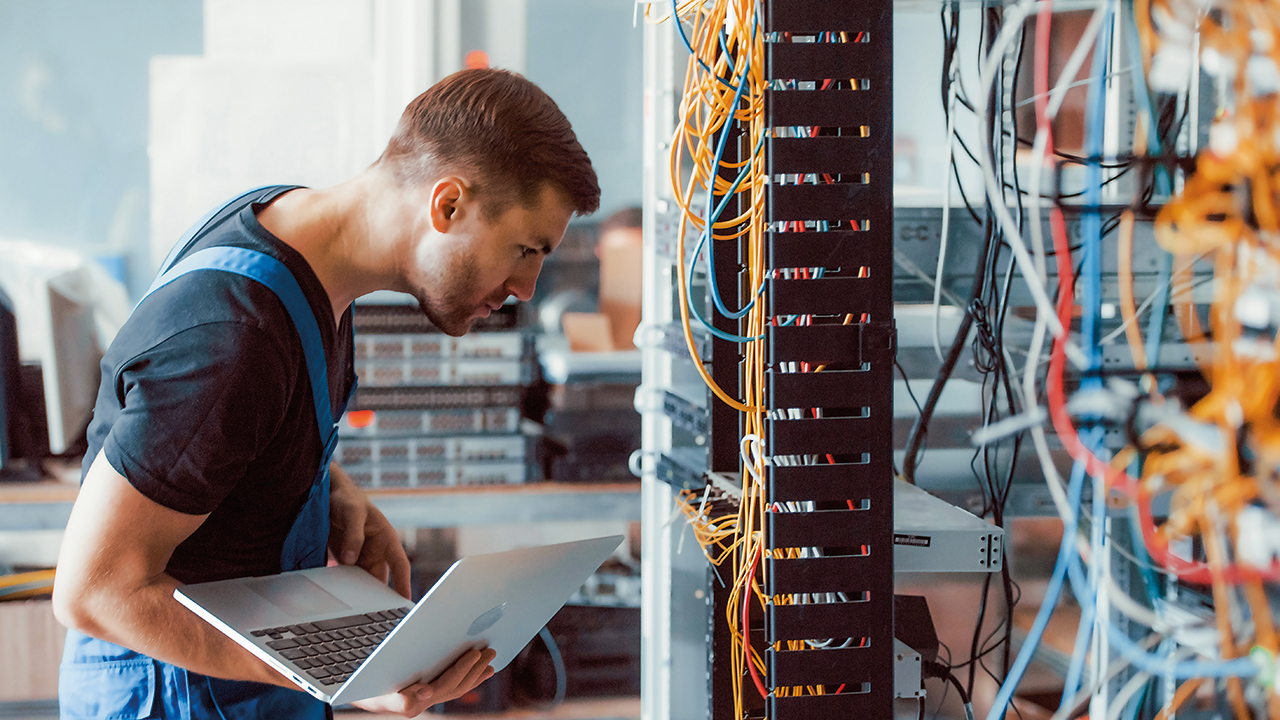
Prior to the launch of Ethernet-APL in the third quarter of 2021, ABB together with other automation suppliers successfully introduced the first Ethernet-APL products at the ACHEMA Pulse virtual trade show in June. Thus, the decade long journey to expand Ethernet to field-level communication for process automation plants is completed; thereby initiating a safe, secure, and practical communication from the field to the entire enterprise and the cloud.
Acknowledgements
This article would not have been possible without the ideas, work and dedication from many people at ABB. Special thanks are extended to: Roland Braun, Philipp Bauer, Alexander Gogolev, Alexander Nahrwold, Peter Ude and Tilo Merlin.
References
[1] K. Larson, “The Last Mile-APL Standard to Make Field-level Ethernet a Practical Reality”, Control, June 2020, pp. 24 – 28.
[2] A. Gogolev, “OPC UA and TSN: enabling Industry 4.0 for end devices”, ABB Review 4/2020, pp. 30 – 35.
[3] APL Project Group, “Ethernet to the Field”, White paper , internal report, 2020, pp. 1 – 17.
[4] Profinews, “Moving Forward: Advanced Physical Layer for Industrial Ethernet”, Profinews, November 30, 2019, [Online]. Available: https://profinews.com/2019/11/moving-forward-advanced-physical-layer-for-industrial-ethernet [Accessed July 1, 2021].
[5] Plauky, Ethernet-Kommunikation, Position Paper NAMUR Hauptsitzung, 2016.
[6] NAMUR Arbeitskreis, Anforderungen an ein Ethernet-Kommunikation fuer die Feldebene, NAMUR Arbeitskreis AK 2.6 Digital Prozesskommunikation, Nov. 22, 2018, pp. 1 – 9.