ABB’s Pointe-Claire facility has developed solid expertise in plastic injection molding, used in a series of electrical solutions for the Canadian market. In addition, its vertical integration efforts have helped optimize production.
Image currently unavailable
Image currently unavailable
Image currently unavailable
Image currently unavailable
Image currently unavailable
Image currently unavailable
Image currently unavailable
Image currently unavailable
Image currently unavailable
Image currently unavailable
Image currently unavailable
Image currently unavailable
Image currently unavailable
Image currently unavailable
Image currently unavailable
Georges Maisonneuve - Production supervisor Oskar Baivel - Shift leader Jeanifa Larue - Shift leader Jagdish Kaur - Assembler Parveen Bath - Quality and Operational Excellence technician
Known as the “T-Can” facility due to its location on the Trans-Canada Highway, this facility has a rich history. Previously owned and operated by Thomas & Betts, and now ABB, it currently produces three Canadian legacy brands including: the Marrette® wire connector, developed by Bill Marr in 1914, and its various models; the NuTek® series of non-metallic thermoplastic boxes used exclusively in wood frame residential construction, once produced by a British Columbia firm of the same name; and Snap-it®plastic fittings. These products account for nearly two-thirds of the facility’s output, with another third dedicated to a range of Carlon® PVC products for the North American market. The facility also produces components for emergency lighting housings and signs, Microlectric® meter bases, and others parts that are vertically integrated into these products manufactured at other Quebec-based ABB facilities.
Image currently unavailable
Image currently unavailable
Image currently unavailable
Image currently unavailable
Image currently unavailable
Image currently unavailable
Image currently unavailable
Image currently unavailable
Image currently unavailable
Image currently unavailable
Image currently unavailable
Image currently unavailable
Image currently unavailable
Image currently unavailable
Image currently unavailable
Image currently unavailable
Image currently unavailable
Image currently unavailable
Marrette PRO-BLU 933® wire connector Marrette PRO-BLU 933® wire connector Marrette PRO-BLU 933® wire connector NuTek® non-metallic thermoplastic boxes Snap-it® non-metallic fitting Emergi-lite Premier™ series thermoplastic battery unit and EXIT sign
At a time when ABB had the opportunity to move plastic molding production elsewhere, it decided to invest in the T-Can facility and keep the manufacture of these products in Canada. The decision was the result of a focus on continuous improvement that reaped the benefits of a loyal and knowledgeable local workforce, as many of its members had decades of service. Strategic planning and operational investments in the early 2000s, moved production to the more spacious and better adapted facility. These elements made further investment in the T-Can facility a logical next step.
“Thanks to automation, improvements in our processes and very tight scheduling tools, we didn’t need more space to fit more production on the same factory footprint,” says Jean-Sebastien Ouimet, operations manager for the facility. “We were able to move presses from another location and optimize their use, enabling us to further our expertise in plastic injection molding—and increase our output.”
A process used for mass production, plastic injection molding involves feeding an injection press with plastic granules that melt as they are pushed through a large screw forcing them into a mold. The plastic is then shaped into the desired product, ranging from Marrette® wire connectors to plastic housings for EXIT signs.
“Having this solid expertise allows our facility to contribute concretely to brands that are made in Canada for Canadians. Producing components that are shipped to other ABB facilities for integration allows us to capitalize on an expertise in its native environment, thereby increasing efficiencies across other ABB product lines and locations,” explains Eric Deschenes, Country Manager and Head Electrification Business, ABB Canada.
Image currently unavailable
Image currently unavailable
Image currently unavailable
Image currently unavailable
Image currently unavailable
Image currently unavailable
Image currently unavailable
Image currently unavailable
Image currently unavailable
Image currently unavailable
Image currently unavailable
Image currently unavailable
Image currently unavailable
Image currently unavailable
Image currently unavailable
Image currently unavailable
Image currently unavailable
Image currently unavailable
Interior of Pointe-Claire's plastic injection molding facility End-of-line packaging of PVC fitting products Carlon PVC fittings awaiting packaging Copper coils used for Marrette® 833 wire connector Technician setting up and testing plastic molding injection press for production of PVC conduit clamp Assembly of plastic components for the Emergi-lite Premier™ series thermoplastic battery unit and EXIT sign
The combination of expertise and automation made it possible for the facility to double its production over the past three years. An increase in production also meant an opportunity to grow the team by 70%. This mix of technology and talented people provided the necessary capacity to respond to construction growth, largely due to increased home renovations during the pandemic.
Set-up technician and team lead Billy Michaud, who has been with the organization for the past 14 years, recognizes the T-Can facility’s accomplishments. “With these recent investments in technology, we pushed the boundaries of production. A great part of it has to do with ABB’s ability to elevate its employees,” he points out. “Here, it doesn’t matter where you’re from or what your gender is. If you can do the job, you get the job. People get credit for the work they do.”
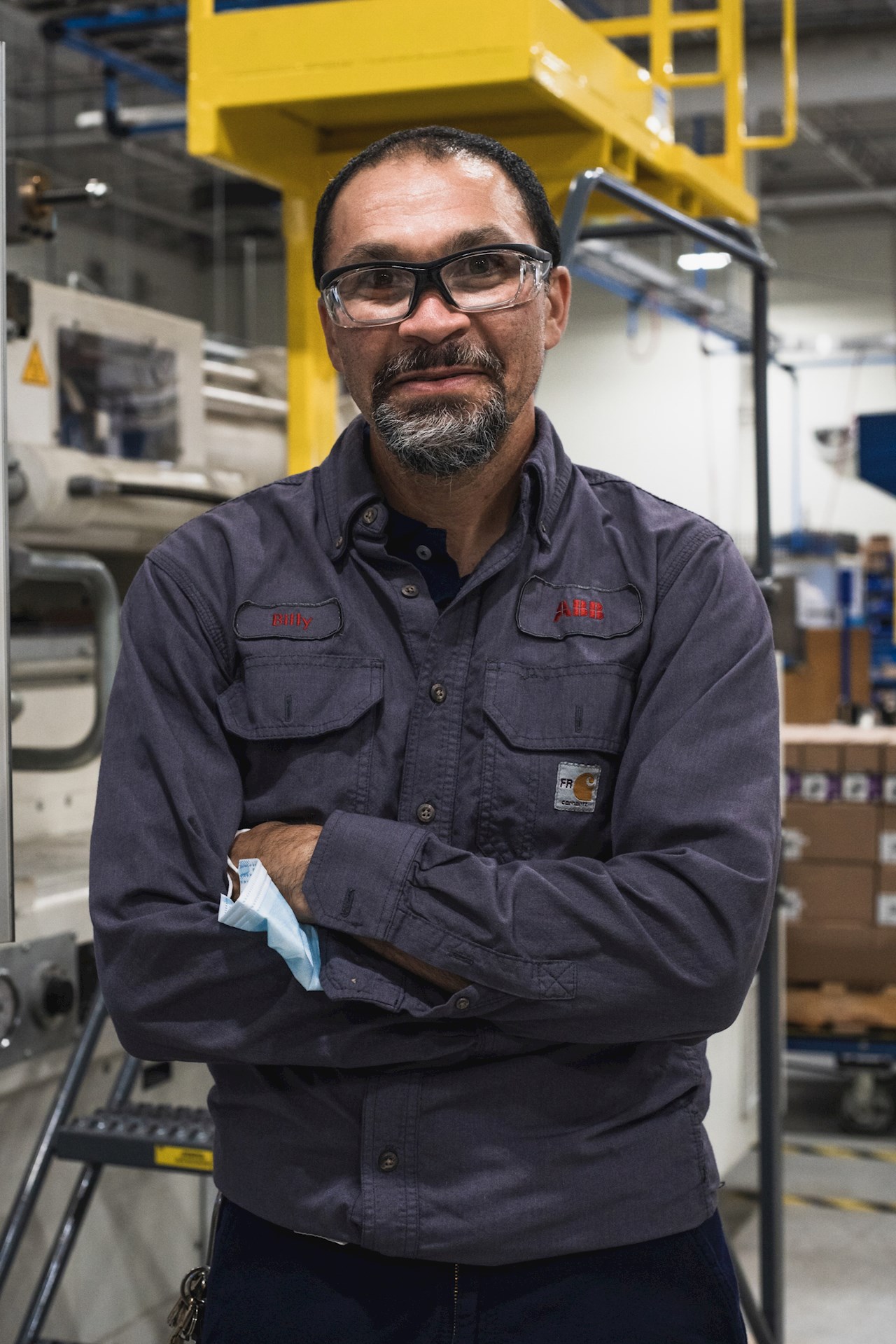
Facility manager Ouimet acknowledges the recipe for success in his operation: people, adaptability, and respect. “This facility is testimony to the high-performing but flexible environment we’ve created—an inclusive team of experts from very diverse backgrounds that has worked hard to optimize production and takes pride in making unique products for the Canadian market,” says Ouimet.
Through focused investment in the T-Can facility and its team, ABB has developed an expertise in plastic injection molding that has facilitated production of a number of Canadian products. Building on ABB’s proven history and commitment to innovation, these products continue to evolve to help make people’s lives easier and safer and contribute in a meaningful way to the Canadian economy.