Technological, environmental and social trends are transforming the world. The mining industry, while traditionally low on the Industry 4.0 curve, is catching up fast – primarily through mine electrification. ABB’s eMine™ and its associated Trolley System, as well as its gearless conveyor drives and its expertise in the automation of conveyor systems, are helping mining customers to electrify their equipment from pit to port with fit-for-purpose solutions.
Mehrzad Ashnagaran Mine Electrification and Composite Plant Zurich, Switzerland, mehrzad.ashnagaran@ch.abb.com
ABB has considerable experience around the world supplying large, integrated electrical and control solutions to mining and minerals customers. In addition, the company is enabling miners to transition toward the all-electric mine. The company is committed to partnering with customers and suppliers to reduce their annual CO₂ emissions by at least 100 megatons, equivalent to the annual emissions of 30 million combustion cars, and to achieve carbon neutrality in its own operations by 2030. Mining is currently responsible for around four to seven percent of global greenhouse gas (GHG) emissions – an area in which current methods must change rapidly to meet targets, national regulations and the Paris Agreement.
This article explores two examples in which the journey toward the all-electric mine is already underway. The first examines Canada’s Copper Mountain Mining, where ABB is installing an electric haul truck trolley assist infrastructure. The second reports on the introduction of the world’s most powerful gearless conveyor system, which is located at the Chuquicamata copper mine in Chile.
An electric transformation in Canada
Without newly mined materials there would be no cellphones, computers, batteries or wind farms. Transitioning to an all-electric mine, which allows extraction of ores with the lowest
possible impact on the environment, requires new thinking, as exemplified by ABB’s eMine™, a recently launched concept, which is already helping mining customers to electrify their equipment from pit to port with fit-for-purpose solutions to meet operational demands. It is backed by ABB’s many decades of real-world experience in electrifying, automating and digitally connecting mine equipment and operations to improve energy usage and overall performance.
Complete trolley assist solution
One of eMine’s key solutions is the ABB Ability™ eMine Trolley System →01[1], which has already been implemented in a number of countries. The solution enables vehicles to run on an electric trolley assist line instead of using diesel fuel. Most recently, eMine was implemented in British Columbia, Canada, where ABB is working with Copper Mountain Mining →02 [2].
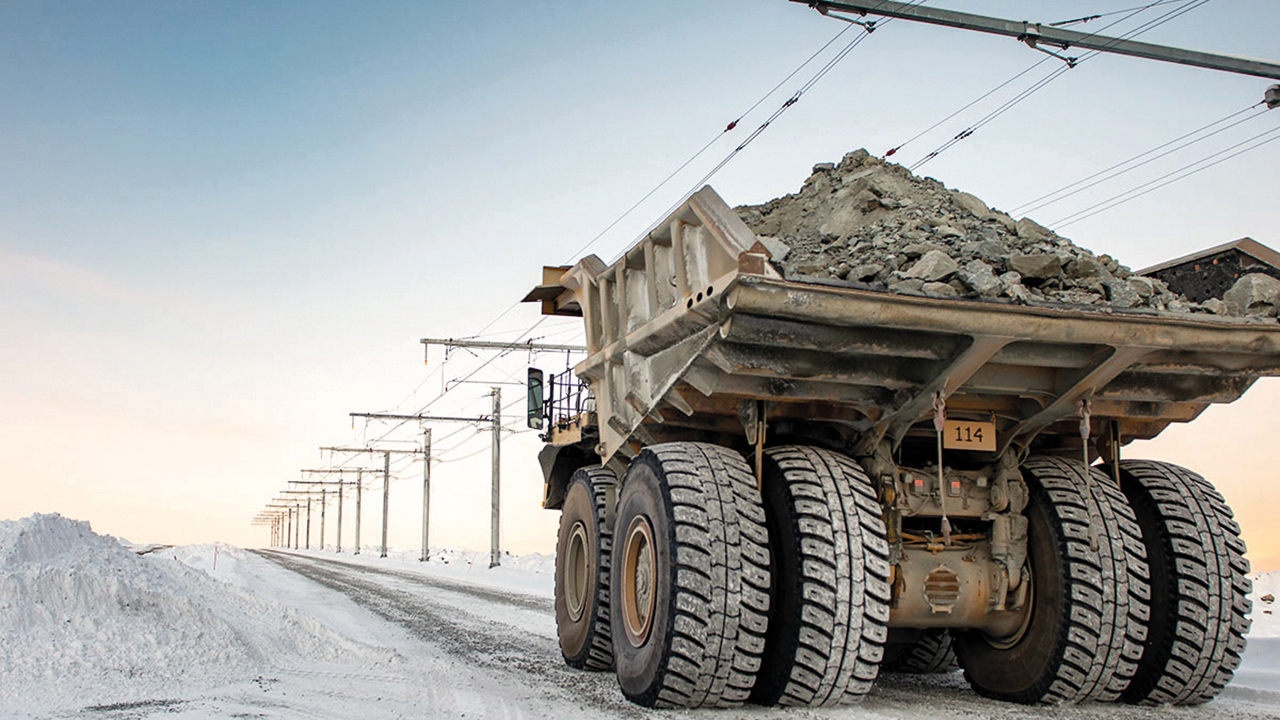
Here, where a conventional open-pit operation produces approximately 45,000 metric tons of copper equivalent per year, ABB is providing a complete trolley assist solution →03. ABB is responsible for all the off-truck trolley assist infrastructure, including an overhead catenary system (OCS) design and a rectifier substation providing more than 12 MW of DC power – as well as engineering, project and construction management, equipment supply and system commissioning.
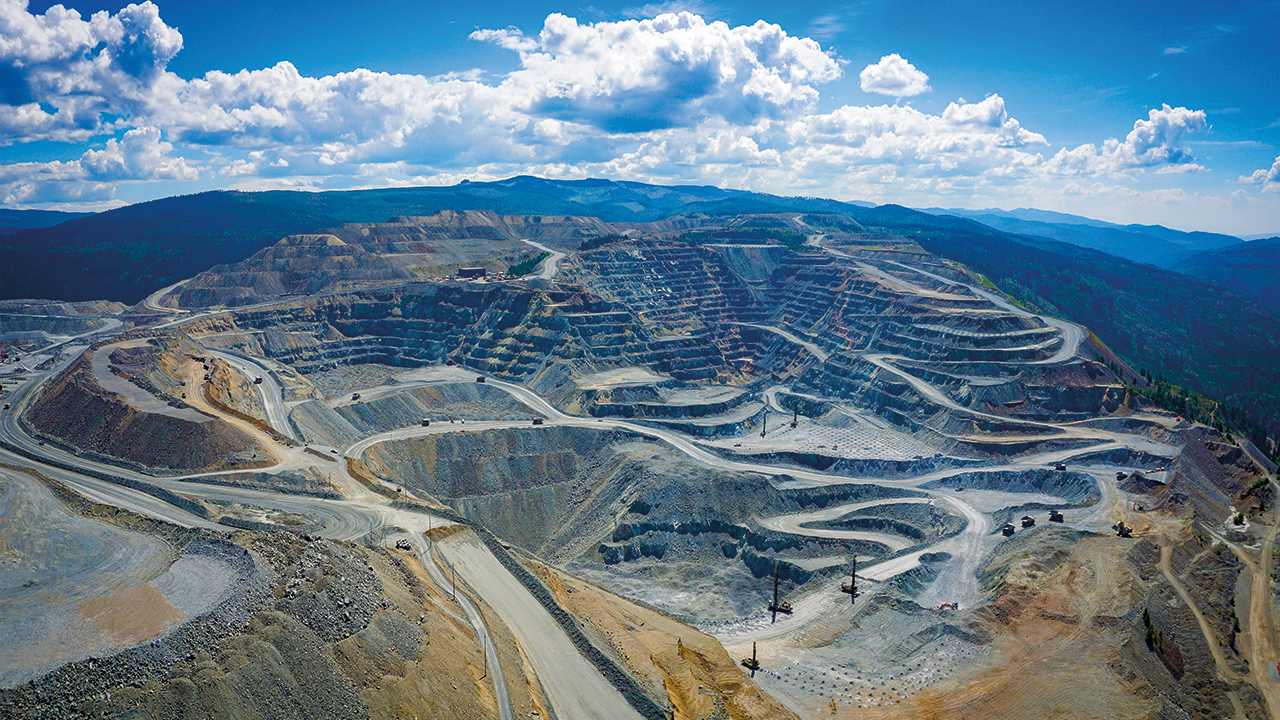
The trolley control system can provide connectivity to the existing ABB Ability™ 800xA distributed control system (DCS) platform, allowing for seamless integration and monitoring of trolley operations and energy consumption. ABB is also providing OCS components customized for mining applications.
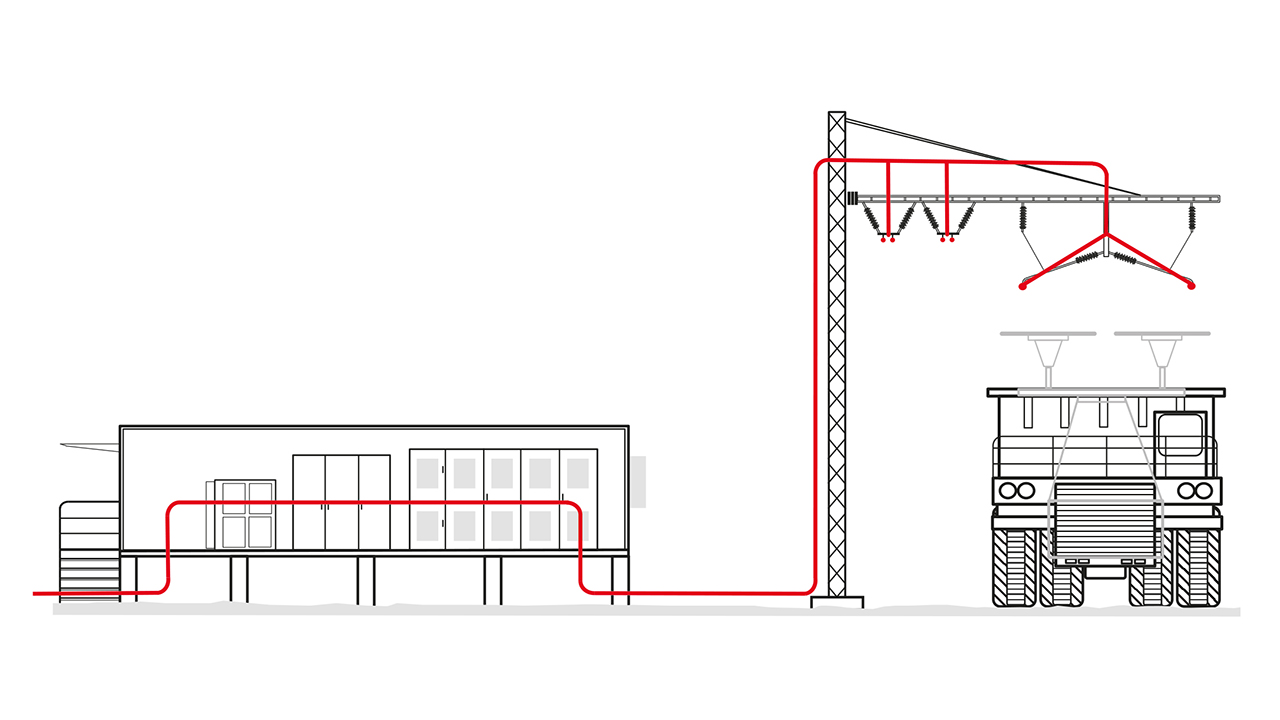
Copper Mountain is expected to initially reduce emissions by seven percent during the first phase of the project, and has set a goal of achieving a 50 percent reduction in CO₂ over five to seven years. The new trolley operation is also expected to improve efficiency; for instance, trucks will be fitted with a pantograph to receive external electric power, thus allowing them to run faster when connected to the trolley system, while using less fuel and requiring less maintenance.
As part of the eMine™ concept, ABB has identified six ingredients that will be essential for all-electric operations:
• Interoperability: the ability to have a versatile charging infrastructure application across battery-electric vehicle (BEV) original equipment manufacturers and vehicle types
• Mobility/Flexibility: the ability to implement a point-of-charge infrastructure that allows a mine to adapt as it develops
• Energy Management: the ability to combine power with process control to minimize load peaks and create balanced operation
• Connection Interface: the ability to operate safely at high currents thanks to the use of ruggedized, mine-applicable automated connection devices
• Trolley and Charger Technology: the ability to match charging and trolley infrastructures to the capability of BEV batteries for demanding operations
• Favorable Process and Mine Development: the ability to use alternative mine development approaches such as downhill hauling and/or conveyor, truck and hoist combinations.
The above ingredients, which are empowered by ABB Ability™ MineOptimize [3], are designed to achieve optimal design and operations through the balanced use of energy and resources.
References
[1] ABB, Trolley-assist solution for Copper Mountain Mining sustainable development – Canada | ABB [Accessed June 11, 2021].
[2] Copper Mountain Mining. The Copper Mountain mine, British Columbia, Canada. Available at: https://www.mining-technology.com/projects/copper-montain/ [Accessed June 11, 2021].
[3] ABB, ABB Ability™ MineOptimize. Available at: https://new.abb.com/mining/mineoptimize [Accessed June 11, 2021].
Driving an efficiency revolution in Chile
Ulf Richter ABB Belt Conveyor Systems Cottbus, Germany, ulf.richter@de.abb.com
In remote northern Chile, ABB has been working with German industrial company TAKRAF at Codelco’s Chuquicamata mine – the world’s largest open-pit copper mine. There, gearless conveyor drives (GCDs) are part of the most powerful belt conveyor system anywhere. They have also become the preferred solution in many mining projects globally.
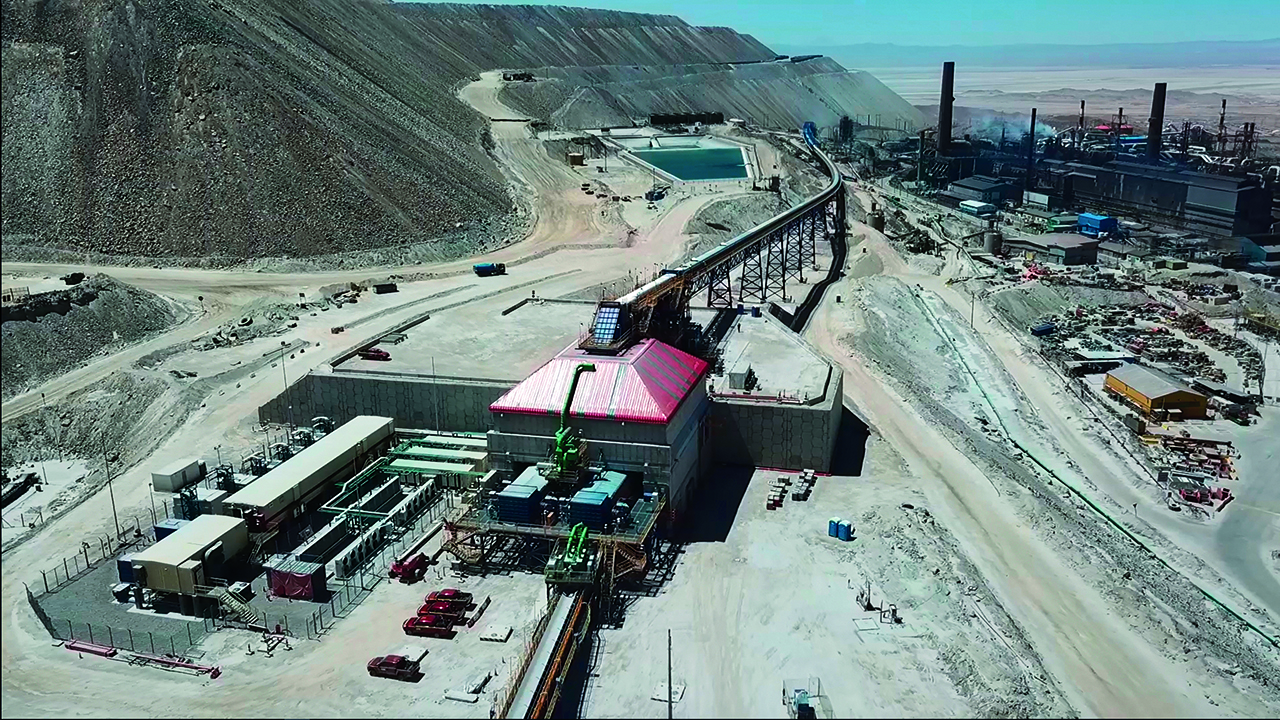
From engineering design to electrical equipment for power supply and energy distribution, ABB technologies and the expertise needed to integrate them, are evident across the Chuquicamata site →04. However, it is in the automation of a new underground and overland conveyor system that ABB’s GCD →05 strengths are highlighted [4, 5, 6].
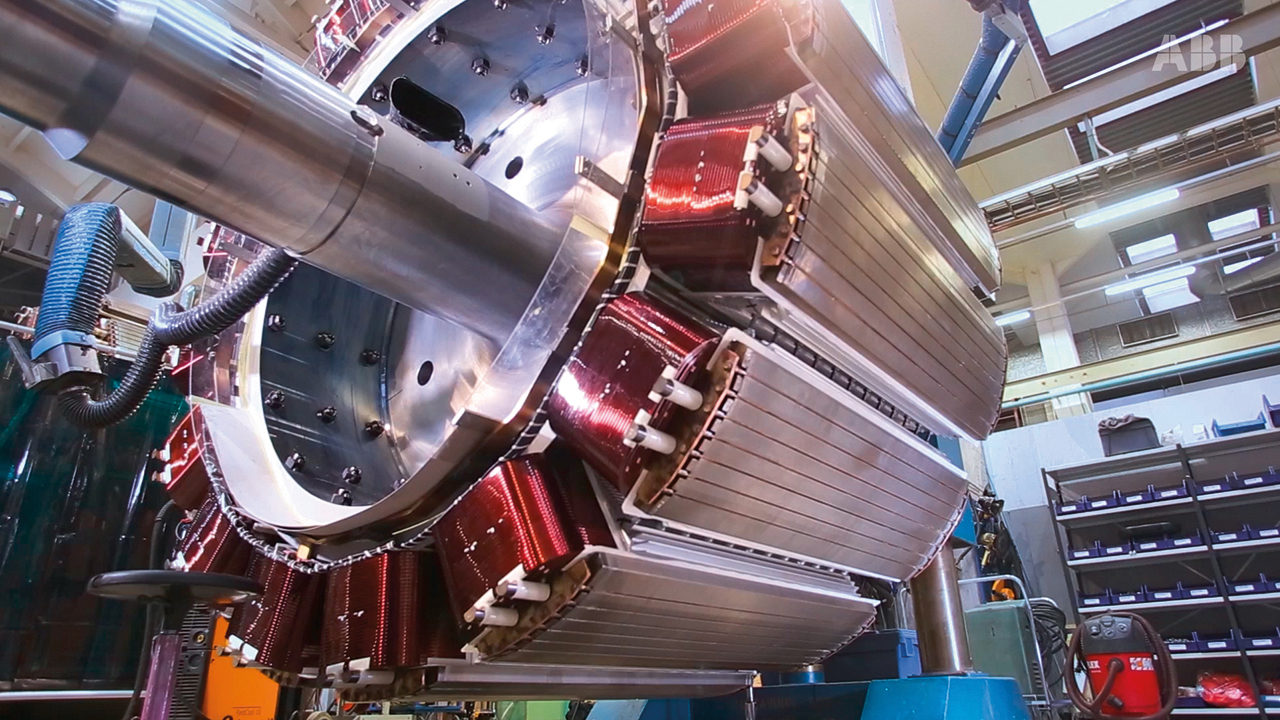
The mine’s belt conveyor system has to perform at high capacity 2,850 meters above sea level in the high desert of the Antofagasta region. The conveyor system is 13 km long and connects underground operations directly to the site’s concentrator. Two 20 MW TAKRAF conveyors each lift 11,000 tons per hour (tph) of ore more than 600 meters to reach the surface from the underground mine. The total lift is about 1.2 km, after which the ore is fed to a 15 MW overland conveyor.
GCDs are suited to mining projects that require high drive power. They help to boost the efficiency of higher-capacity belt systems, thus increasing the possible ore throughput, reducing energy usage, cutting equipment downtime and minimizing maintenance costs →06. They are the only economically feasible way to provide enough power to run the Chuquicamata mine’s 20 MW conveyors. The limit for an input pinion gearbox on a conveyor is 3-4 MW, so the belt system at the mine would have either required eight motors driving into a gearbox with an output shaft or multiple conveyors with lower power ratings and multiple transfer stations. Either scenario would have required substantially more materials, space, caverns and infrastructure to deliver the requisite power. GCDs were therefore the simplest way to achieve the production output that the customer wanted, with the added benefit of reduced maintenance while driving significant efficiency gains.
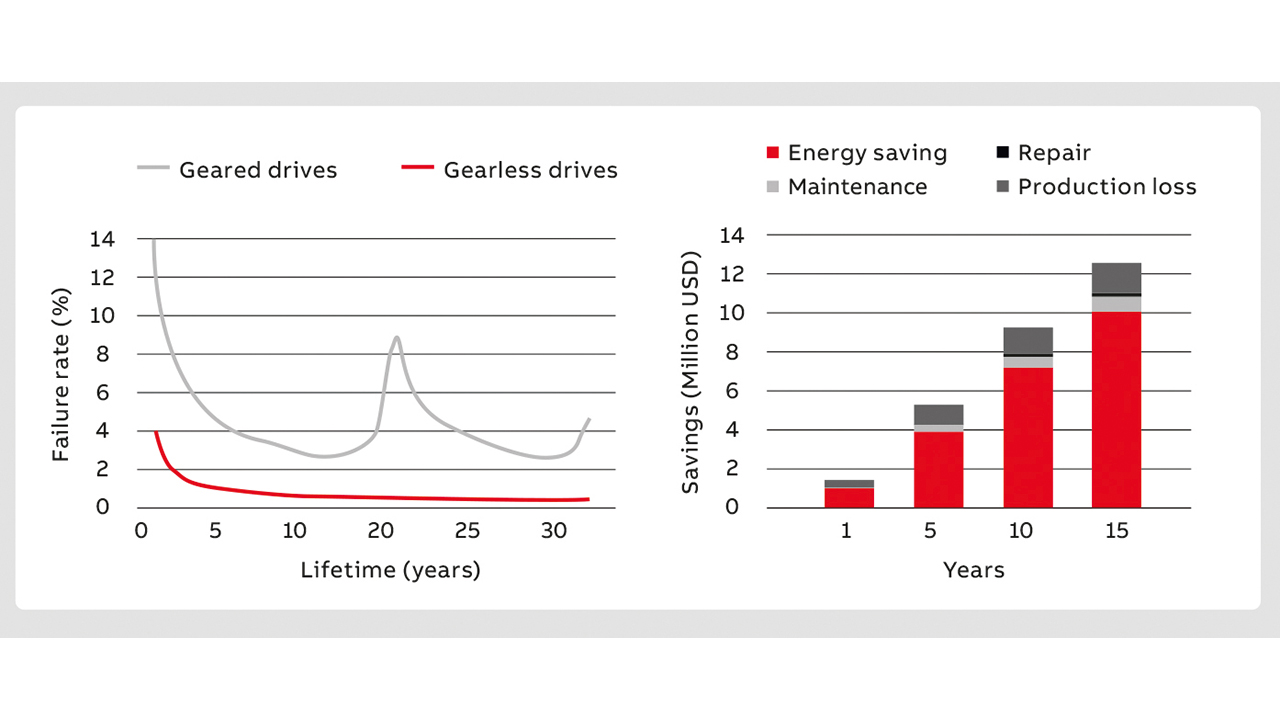
With these factors in mind, ABB and TAKRAF commissioned the most powerful GCD system in the world. The system comprises 11 drives with synchronous motors running at speeds of 50-60 rpm, and with a rated power of 5 MW each, resulting in a motor shaft torque of roughly 900 kNm. The total installed drive power for the entire system, including multiple feeder conveyors, is 58 MW.
Switching from open-pit, truck-and-shovel operations to underground operations using the TAKRAF conveyor with ABB GCDs will help mine owner Codelco save roughly 130 million liters of gasoline per year →07. This will be achieved by eliminating the need for 120 large-haul trucks, reducing the mine’s CO₂ emissions from 340,000 t per annum to 100,000 t – an estimated saving of approximately 70 percent.
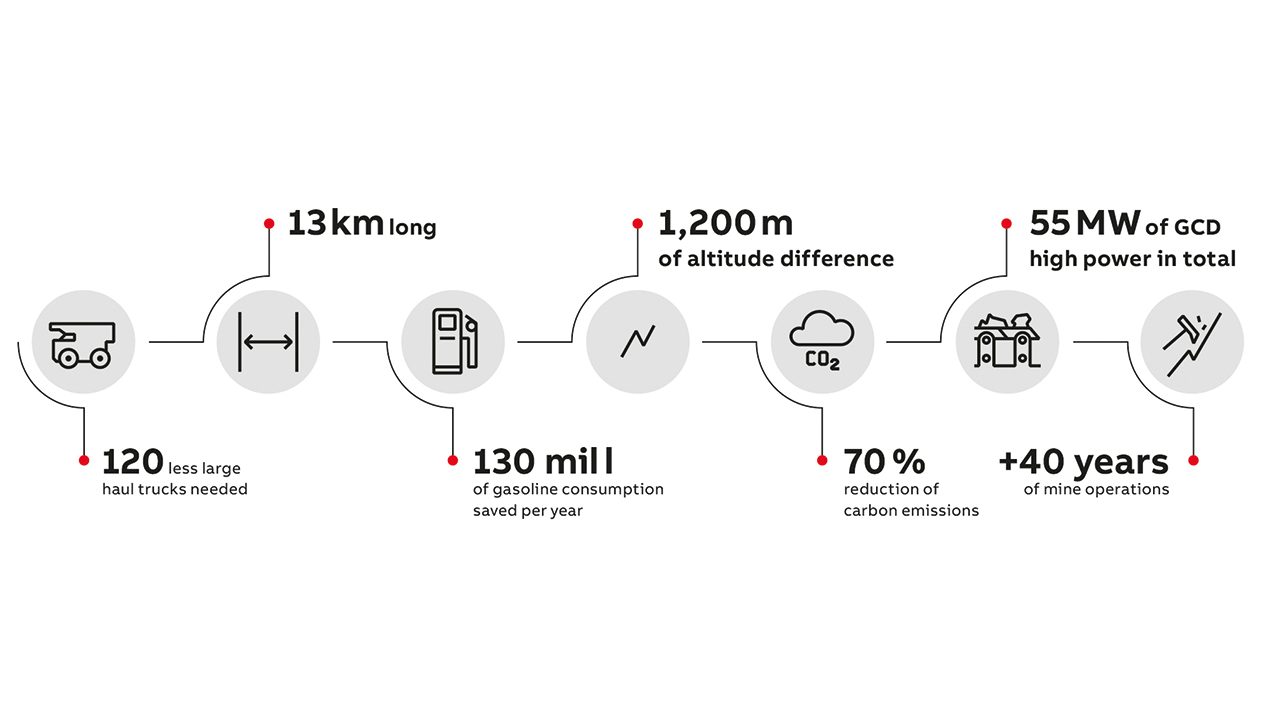
At Chuquicamata, the ABB/TAKRAF solution is connected to the ABB Ability™ 800xA control system for efficient data acquisition, equipment assessment and process optimization. System 800xA monitors and collects data from multiple sensors embedded in the motor drive system, searching for anomalies and identifying maintenance needs. The project is expected to extend operations for the next 40 years.
Efficiency requirements for medium power GCDs in the 1-10 MW range (total conveying power) are expected to increase in coming years. In view of this, ABB is responding with technologies designed to reduce the cost per ton of production, thus helping customers stay competitive. Compared with gearbox-led solutions, GCDs are energy efficient and produce less noise. On the other hand, drives containing gearboxes with multiple moving parts turning at 1,000 rpm or higher can be very loud and run the risk of exceeding the EU’s noise emissions limit of 85 dB(A) (A-weighted decibels).
To avoid such problems, as part of an ongoing upgrade project in the Czech Republic, ABB is utilizing its latest medium power GCDs. By updating shaft mounted geared drives on an existing conveyor system equipped with GCDs powered by synchronous permanent magnet motors, the mine owner will be able to meet EU noise emission limits, as well as prevent frequent failures of the existing drives due to vibration issues. Using GCDs at around 50 rpm with low noise coolers limits noise emissions from the drive unit to less than 75 dBA, giving the mine all the benefits of gearless drives while negating the need for noise encapsulation (housing around the whole geared drive unit) or noise protection walls along the conveyor system. Such GCDs are 5-8 percent more energy efficient and have lower CO₂ emissions than gearbox-led solutions. GCDs also offer a higher level of safety as they require no combustibles or hazardous liquids such as gearbox oil, but instead use a water-based cooling liquid.
GCDs are being deployed in complex and often world-class projects. They can provide many benefits for mine operators by helping to increase efficiency and reduce energy usage, equipment downtime, maintenance costs and noise. Together with solutions including augmented/mixed reality collaboration applications, advanced data analytics, AI tools and machine learning, mining companies and their technology partners are set to further increase the efficiency of operations, however remote or challenging.
References
[4] ABB. ABB completes commissioning of the world’s most powerful conveyor system. Available at: https://new.abb.com/news/detail/68172/abb-completes-commissioning-of-the-worlds-most-powerful-conveyor-system [Accessed October 8, 2021].
[5] ABB. ABB gearless drives for TAKRAF’s most powerful mining conveyors in Chile. Available at: https://new.abb.com/mining/reference-stories/underground-stories/takraf-underground-mining-conveyors-with-abb-gearless-drives-progressing-in-chile [Accessed October 8, 2021].
[6] ABB. Video of the world’s most powerful Gearless Conveyor Drive system: https:// youtu.be/tYHsqwo4TJU [Accessed June 19, 2021].