While college or military is the right pathway for some high school students, technical career paths may be more aligned to the interests and aptitudes of others. Studies done in our local communitites indicate many students have the aptitude for careers in manufacturing, but most don't have the interest.
But we understand we are up against two primary challenges in driving that interest. We hide what we do behind brick walls with no windows, and we wait until high school before we tell students and their parents what we do. So we are taking a variety of steps to overcome those challenges.
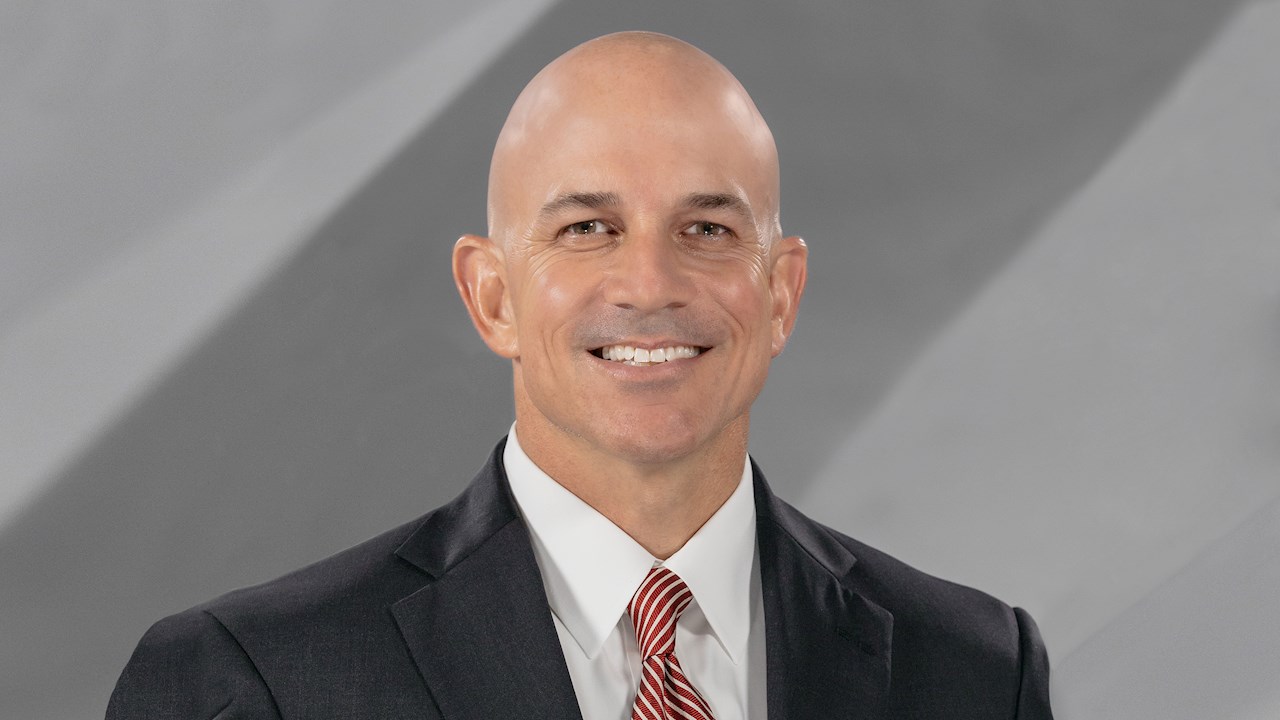
Partnerships
We value our relationships with national organizations such as The Manufacturing Institute, Girl Scouts, FIRST Robotics, and EdgeFactor. Each offers engaging, hands-on, STEAM-related content and activities designed specifically for K-12 students.
We encourage local employees to partner with their local schools to participate on curriculum advisory boards, communicate needed skills, and speak in classrooms. We also host plant tours so students, parents and counselors can see behind our doors and get a clear view of career pathways in manufacturing.
Externships
In one location, multiple manufacturing companies and high schools recently came together for an externship program. This program immerses educators in one businesses for a week, during which time they receive an overview of the work the business does, shadow various jobs, see the skills needed in manufacturing, and become aware of the financial impact manufacturing has on the local economy. We see the true benefit of investing in this program is it allows teachers to talk to their students about more career options than they could have before the program.
Community relationships
Sometimes the success of an entire community is based on the jobs that are available and the security they offer. One facility recently became part of a newly formed alliance with the chamber of commerce, local university and other businesses in town in an effort to connect skilled workers with employers.
The partnership is visible in many ways. The members present together at local career fairs, they offer paid positions for college interns, and they are offering permanent positions to those graduating from those internships. Offering well-paying jobs and developing students into dependable local manufacturing employees is good for the sustainability of the overall community. All of our communities are different based on size, complexity, and manufacturing base, so no single model works across them all, but best practices can always be scaled and adapted.
Other opportunities
How can other businesses grow awareness of manufacturing careers and improve their own local talent pipeline? There are many ways, but these are the two easiest ways to start: First, be visible in your community and the schools closest to you. Encourage members of your team to become active participants in the schools programs that are most needed by your business. Second, open your doors on a regular basis to students, parents and educators.
If we want to be smart about keeping manufacturing jobs in the US and in our communities, more of us must be engaged in sharing the vision, actively talking about career pathways, and hiring the next generation of manufacturers.