ABB will showcase its latest and most innovative solutions to help customers working with sheet metal increase flexibility and productivity at EuroBLECH from October 23-26, 2018 in Hannover, Germany. This includes digital solutions which are part of ABB’s vision for ‘Factory of the Future,’ which can flexibly adapt to constantly changing manufacturing demands as production shifts towards smaller lots of greater variety.
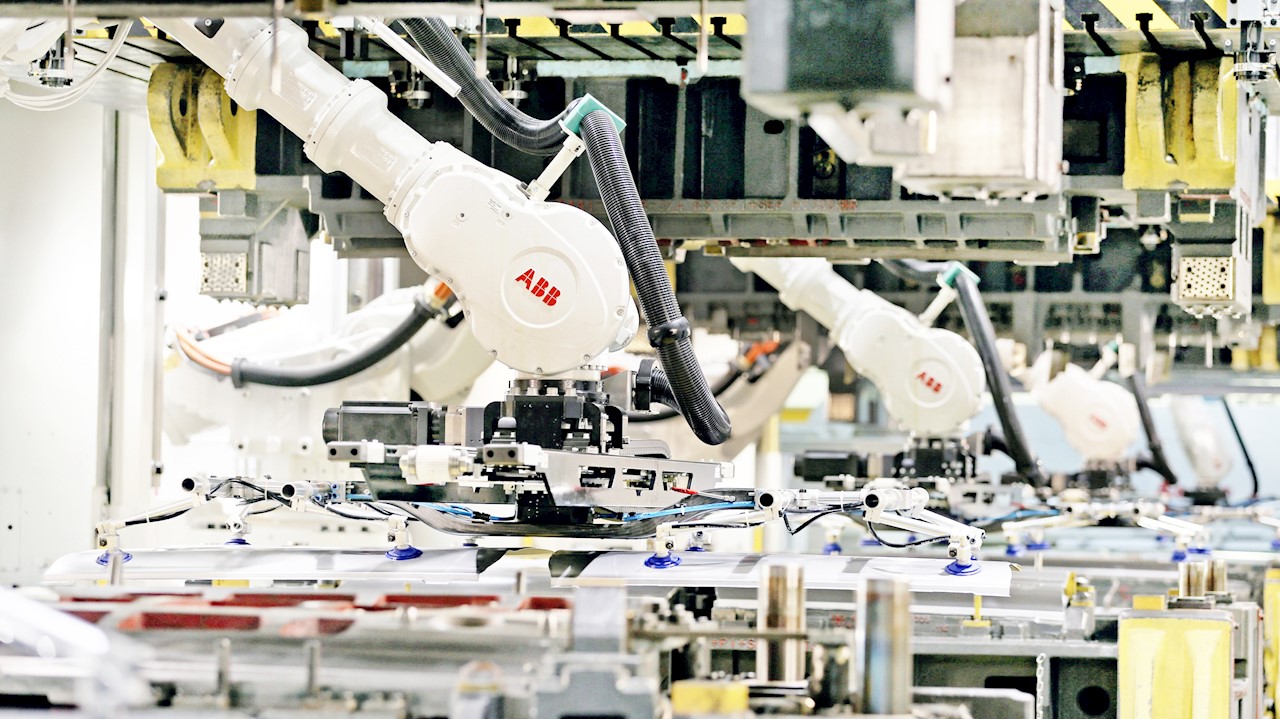
One challenge arising from this shift is the need to ramp up full production of new products with agility and efficiency. EuroBLECH visitors will be able to see how ABB’s RobotStudio can help reduce commissioning time and costly delays during installation.
Commissioning new press-lines has been always a time consuming process, including engineering and programming time as well as the coordination of presses, robots, dies, end-of-arm tooling and material flows. RobotStudio’s virtual commissioning tools can help simulate, optimize and trouble shoot these complex interactions offline, so current production is not disrupted and new production can be ramped up faster, and with less surprises.
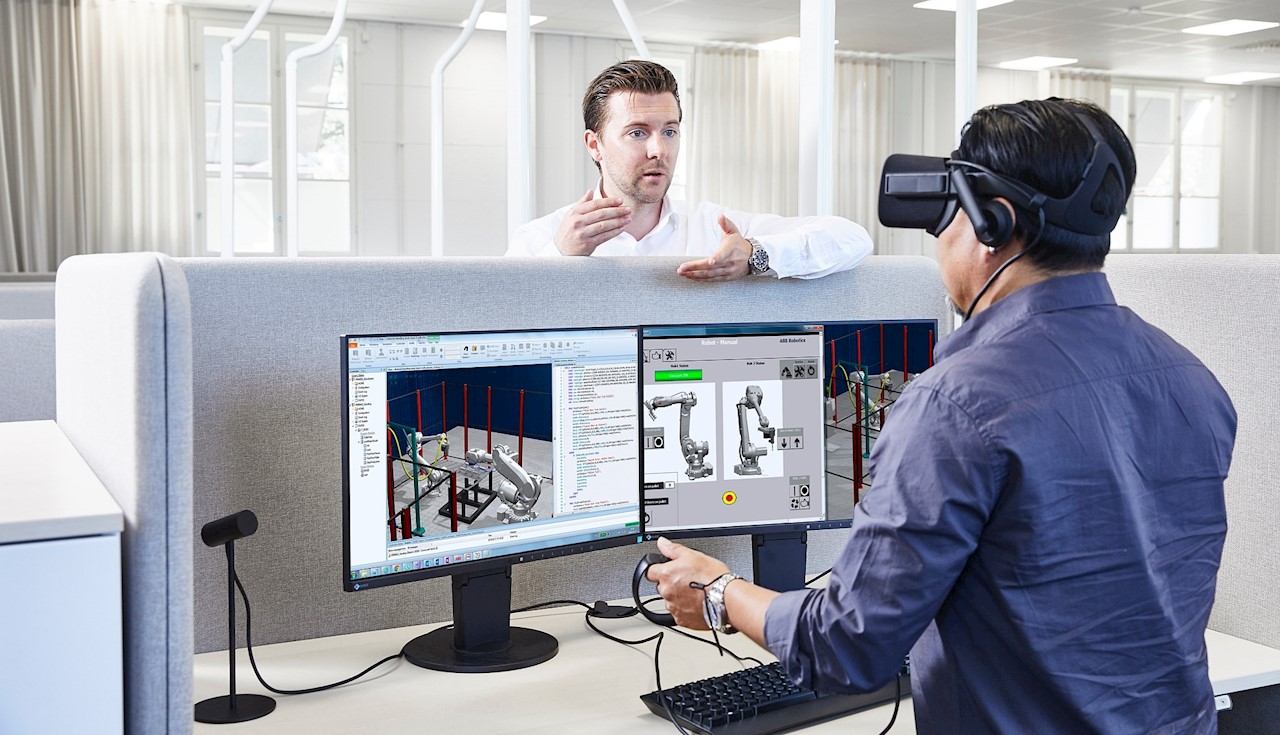
ABB also raises the bar in press automation with its IRB 760FX, a new generation of seven axis robots which offers customers more flexibility, 15-20 percent higher productivity and speeds of up to 14 parts per minute. The IRB 760FX’s linear axis structure uses reinforced carbon fiber for exceptional rigidity and a considerable reduction in weight. The result is a faster press automation robot with best-in-class repeatability, load capacity and flexibility.
The shift towards smaller lots of greater mix also challenges established quality control processes, which were primarily designed for inspecting large runs of the same product. ABB will present its 3DVM quality inspection system, which automates the previously manual and error-prone task of parts inspection.
3DVM uses advanced vision technology with high-precision structured white light to quickly and accurately measure manufactured parts and then compare them to their original CAD drawings.
This allows for every manufactured part to be individually inspected during production rather than relying on random samples after completion for statistical quality control - an approach which can allow undetected mistakes to continue being made until the error is detected.
This allows press operations to improve quality and productivity and reduce scrap. Digitizing the process also documents the quality, for example automotive suppliers can validate that their quality meets the high requirements of original equipment manufacturers.
ABB’s solutions are on display in Hall 27, Booth E128.
ABB (ABBN: SIX Swiss Ex) is a pioneering technology leader in power grids, electrification products, industrial automation and robotics and motion, serving customers in utilities, industry and transport & infrastructure globally. Continuing a history of innovation spanning more than 130 years, ABB today is writing the future of industrial digitalization with two clear value propositions: bringing electricity from any power plant to any plug and automating industries from natural resources to finished products. As title partner in ABB Formula E, the fully electric international FIA motorsport class, ABB is pushing the boundaries of e-mobility to contribute to a sustainable future. ABB operates in more than 100 countries with about 147,000 employees. www.abb.com
ABB Robotics is a pioneer in industrial and collaborative robots and advanced digital services. As one of the world’s leading robotics suppliers, we are active in 53 countries and over 100 locations and have shipped over 400,000 robot solutions in a diverse range of industries and applications. We help our customers to improve flexibility, efficiency, safety and reliability, while moving towards the connected and collaborative factory of the future. www.abb.com/robotics