Sebastian Breisch, Arda Tüysüz ABB Industrial Automation, Corporate Research Ladenburg, Germany, sebastian.breisch@de.abb.com, arda.tueysuez@de.abb.com; Christian Simonidis ABB Electrification Division Smart Buildings Heidelberg, Germany, christian.simonidis@de.abb.com
There is no strict definition of “smart materials.” The worldwide community that investigates such materials and their application does, however, loosely define them as materials that can be used for actuation, sensing and energy harvesting without modifying the material itself.

The simplest and most widely used smart materials are those that exhibit piezoelectric properties, where an applied force causes a voltage to be generated and vice versa. Thermal shape memory alloys (SMAs) constitute another class of mature smart material. SMAs – alloys of nickel and titanium, for example – have two different crystal structures, which are temperature-dependent. At ambient temperature, the material is in its “cold” crystal structure. The SMA’s “warm” crystal structure can be trained by temperature cycling thousands of times. When, subsequently, mechanically deformed and then heated above the transition temperature at which the crystal re-orients its internal structure, the material “remembers” its trained shape, to which it then changes →02. The transition temperature for standard materials is around 60 °C.
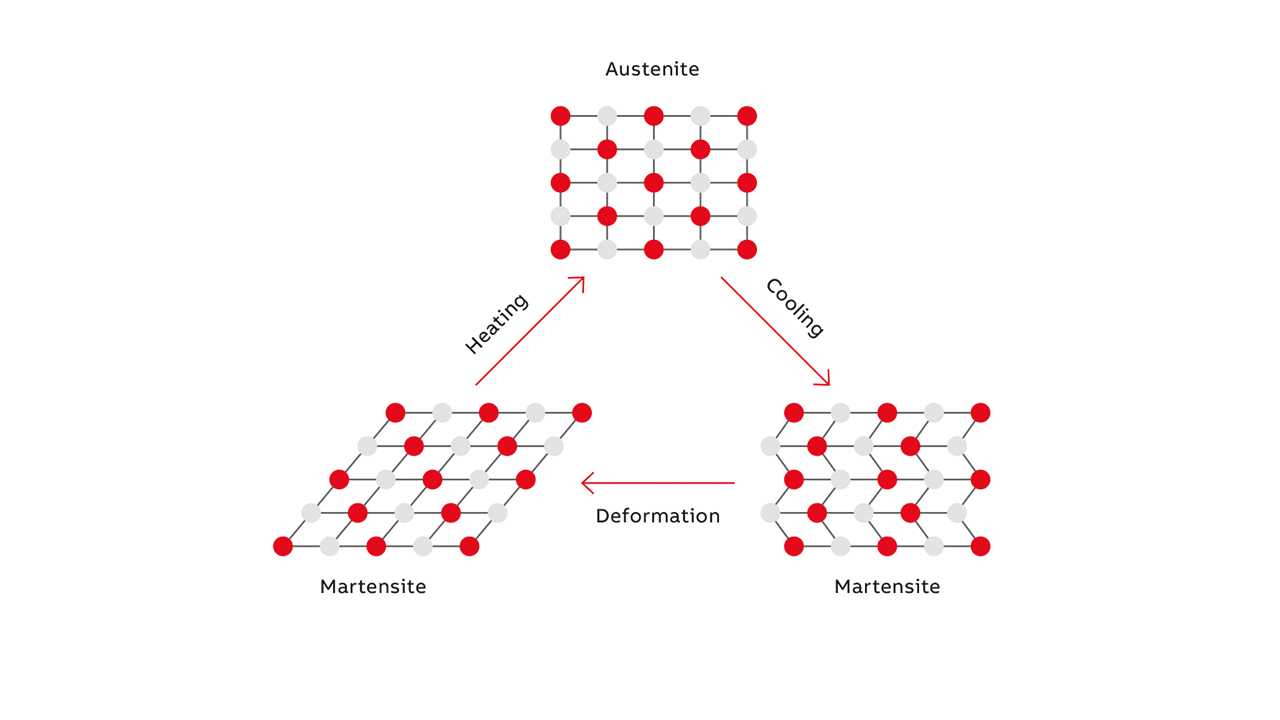
For industrial SMA actuators, a standard design is a simple wire that can be stretched and is then pulled back when heated. This structural change can exert high forces if a large cross-section is used. Commonly, the resetting is not done by gravity as suggested by →03, but via a resetting spring. The most straightforward active control is heating by passing an electric current through the wire.
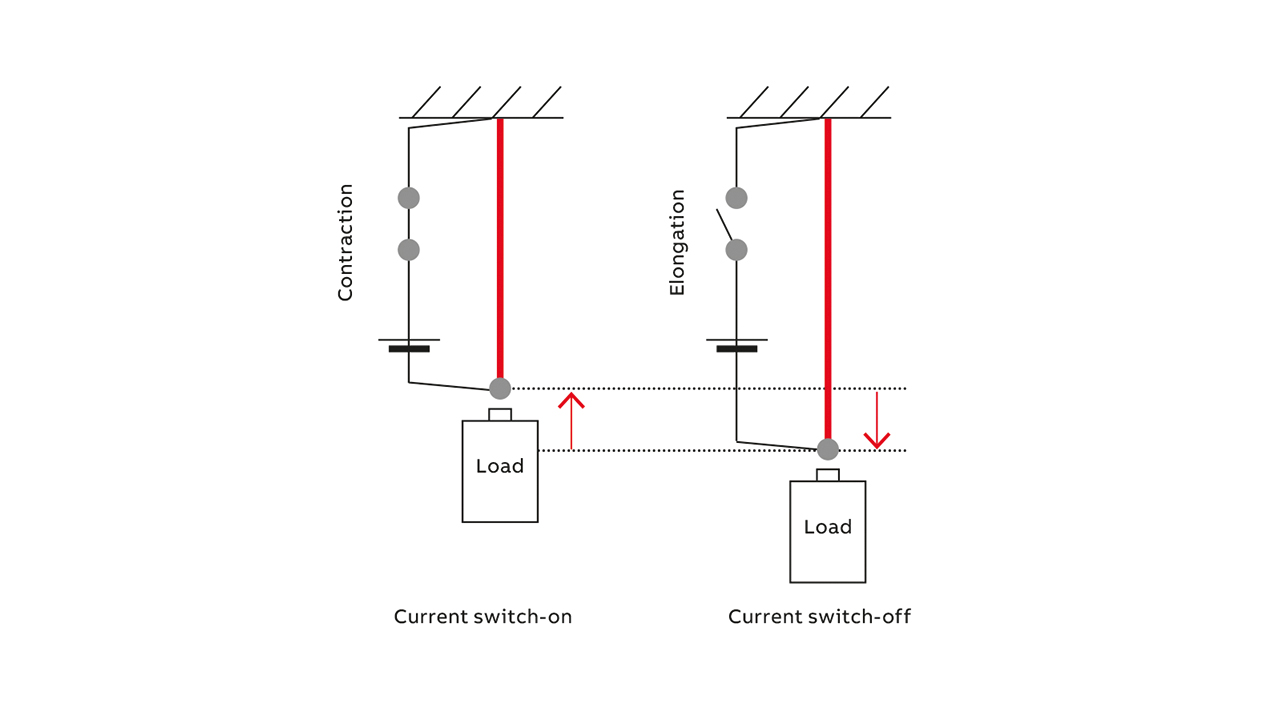
Smart materials that react to heat and magnetic fields
Similar to SMAs are magnetic shape memory alloys (MSMAs), which are composed of nickel, manganese and gallium. This class of smart material shows a dominant effect when exposed to a magnetic field but also reacts to temperature in the same way as SMAs. The material elongates when a perpendicular magnetic field is applied and thereby provides force and motion. A magnetic flux density of approximately 0.4 T is required to trigger this physical response. Full elongation is reached at approximately 1 T, depending on the load. Higher magnetic fields will have no added effect, but will not damage the materials, which is an advantage in some applications. Usually, an external force in the axial direction is used to reset the element.
MSMA performance characteristics fall into three categories:
• Force: Element cross-sectional area defines the forces.
• Stroke: Element length defines the stroke.
• General stress, strain and other properties: Defined by the element and its alloy composition.
As with thermal SMAs, the response to temperature is based on the change of the crystal structure by a phase transition between a martensite and an austenite structure – ie, between a body-centered cubic and face-centered cubic crystal arrangement →04. In general, the forces provided by the thermal actuation are approximately 20 times higher than by the magnetic actuation, whereas the stroke is comparable or slightly reduced.
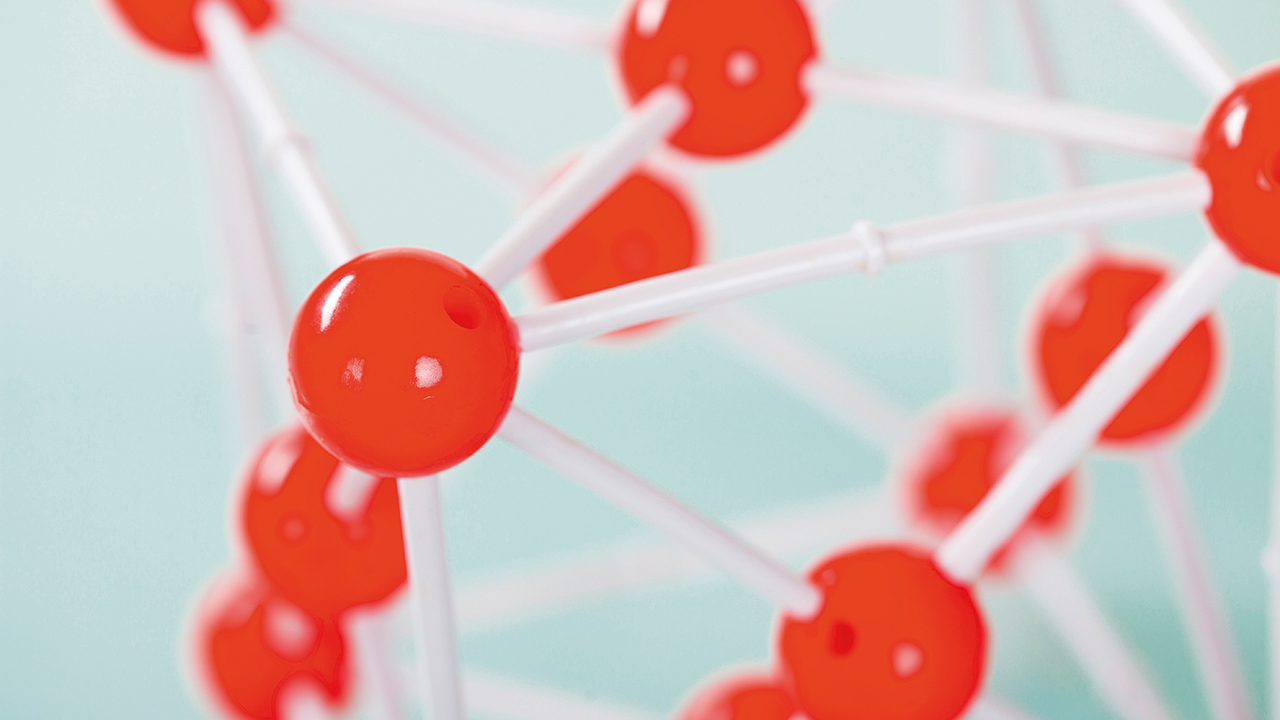
The manufacture of MSMAs is challenging because casting the required monocrystalline ingot is a complex process. Within this ingot, a polarized and folded magnetic crystal structure will evolve during solidification. The MSMA elements, called “sticks,” are cut out of the ingot in a beneficial orientation. It is the folded, magnetically polarized crystal structure within these sticks that allows them to deform when an external magnetic field is applied.
The combination of thermal and magnetic effects makes MSMAs ideal for applications where both a thermal and a magnetic response is required – for example, in a domestic miniature circuit breaker (MCB).
The MCB
An MCB is a protective device that breaks an electrical circuit in the event of a short circuit or thermal overload →05a. The latter occurs much more often than the former, but the MCB response to a short circuit must be much faster (1 ms) than to a thermal overload (several seconds). In conventional MCBs, separate actuators are installed for short circuit and thermal overload tripping functions – typically, a bimetallic strip and a solenoid, respectively →05b. The aim of the work described in this article is to replace these two actuators with one MSMA actuator. Such dual use of an MSMA actuator was described in a 2004 ABB patent application [1].
Image currently unavailable
Image currently unavailable
Image currently unavailable
Image currently unavailable
Image currently unavailable
Image currently unavailable
05a A typical MCB. 05b In a standard electrical installation, the main current always runs through the MCB from terminal to terminal.
05 MCBs are found in a multitude of electrical applications.
One MSMA actuator replaces two conventional ones
An additional benefit of MSMA technology is that the required tripping field can be achieved with a simple straight conductor surrounded by an iron core. Such a magnetic design is inherently more suitable for MCBs of higher nominal currents, where the conduction losses of conventional solenoids are more pronounced.
A parallel arrangement was chosen for the mechanism that transforms the linear motion of the MSMA into the linear mechanical motion of the plunger. Though this setup requires an additional linkage and has slightly more inertia, it is compact and provides the stroke required to eliminate arc re-ignition.
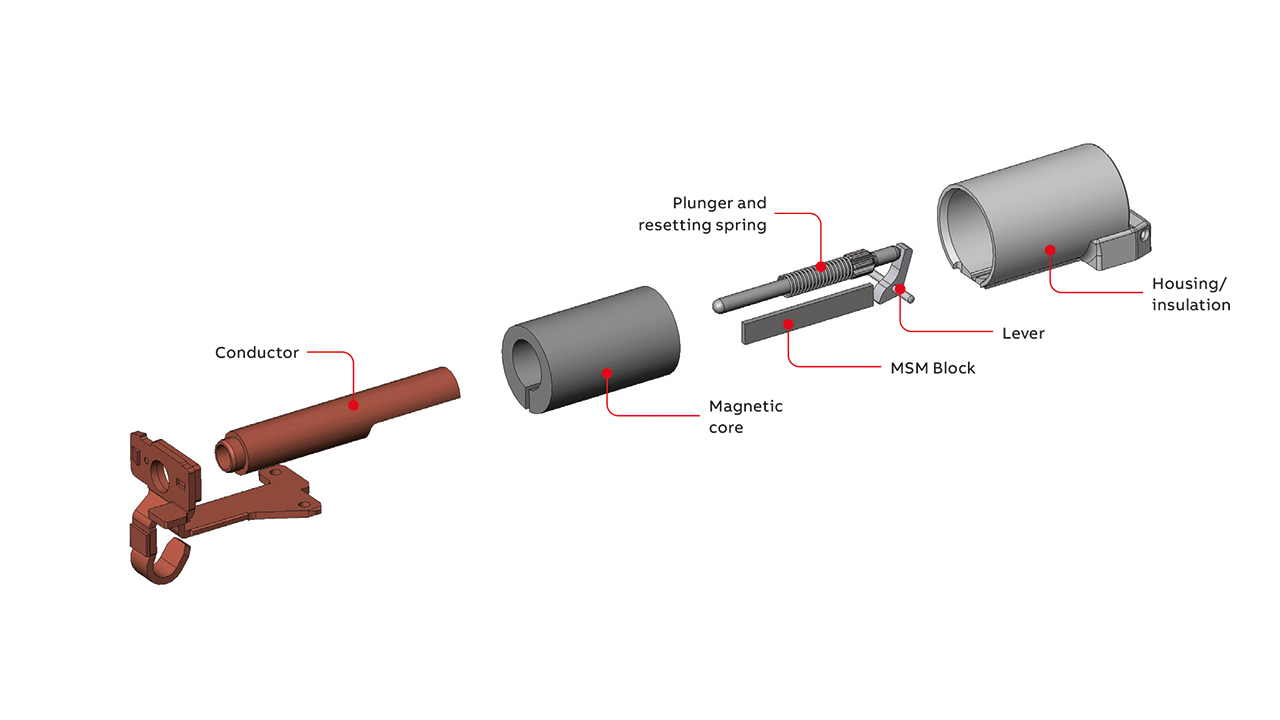
In iterative steps, a final technology demonstrator was developed that consists of a hollow straight conductor, in which the plunger as well as the resetting spring is integrated. A single-gap iron core surrounds the conductor and the MSMA element is placed in the air gap of the core. To adjust the MSMA element strain to the requirements of the MCB, a lever arm is used →06 – 07.
The fast actuation of the MCB when a short-circuit current occurs is ensured if a sufficiently high magnetic field intensity (H) can be applied to the MSMA at the required tripping currents. Therefore, the primary goal of the actuator’s geometric optimization is to maximize the H field on the MSMA while staying within the geometric space constraints defined by the MCB housing.
Electrical losses
A key performance indicator of the MSMA/MCB arrangement is the total (copper and core) losses at the rated current. As with any other electrical device, a primary design goal is to minimize such losses while maintaining the functionality required. On the other hand, the thermal overload trip requires some heat to be generated by the losses in the MCB. The approach taken was to focus on the short-circuit tripping first and design an actuator with the lowest possible losses and only then to take care of the thermal tripping and adjust the thermal budget accordingly (eg, by thermal insulation).
One of the key benefits of using MSMA technology is that the bimetallic strip heat source is eliminated. Also, the coil has a much higher energy efficiency since it consists only of a straight copper conductor instead of a coil. Thereby, the electrical losses can be reduced by around 75 percent →07.
Image currently unavailable
Image currently unavailable
Image currently unavailable
Image currently unavailable
Image currently unavailable
Image currently unavailable
07a An early actuator prototype. 07b Another prototype (silver cube) showing the scale of the device.
07 Hardware demonstrators.
Temperature rise tests in accordance with the IEC 60898-1 standard were carried out on the MCB itself at a 63 A nominal current. The temperature at the lower terminal on the MSMA MCB was found to be approximately 45 percent lower than on a conventional MCB. Thereby, it can be concluded that the temperatures inside the MCB in general and also the temperature on the contact surfaces itself are also much lower, which allows for a higher nominal current rating, with suitable dissipation of heat.
Magnetic tripping
Some MSMA MCBs were prepared to accommodate high-speed camera monitoring so that the moving contact could be tracked. Opening times comparable to conventional MCBs were observed but with less back-travel, which reduces the risk of arc re-ignition.
The MCB plunger is accelerated and impacts onto the beat lever after a short flight in the millimeter range. The effect of different plunger masses was investigated and a clear difference in plunger motion for different phase angles was observed. At the same time, repeatability was high. Higher plunger mass gives a higher impact force, but actuation time is lengthened due to increased inertia. Here, there is room for future optimization.
Thermal tripping
Thermal tripping using MSMA sticks with different thermal transition temperatures was explored. Today’s maximum transition temperature is approximately 60 °C. Initially, the MCB was manually switched on and, thereby, the current applied. The MCB trips after 40 s at 2.55 times nominal current (160 A) and thereby fulfills the requirement for tripping at ambient temperature. Temperature rise tests show that materials with a transition temperature of 85 °C are required to guarantee functionality at +55 °C.
An important further observation was that the performance of the first magnetic trip after a thermal transition was degraded. This phenomenon is being more fully explored.
Products within five years
Currently, MSMA technology is not implemented in any commercial product, so neither mature manufacturing processes nor quality processes exist. Hence, economic aspects are not addressed here. The forecast viability of MSMA technology, however, makes a continuation of the development imperative. The technical suitability of MSMAs for use in applications such as the MCB has been established [2 – 4]. Some work still needs to be done – for example, the development of materials with high (85 °C) transition temperatures as well as general optimization to facilitate production practicalities of the actuator mechanics. Further characterization of MSMA technology regarding lifetime, long-term stability, etc., also needs research, as does the reason why the first shot after a thermal transition is different.
That said, for an MCB, the combination of magnetic and thermal actuation integrated into one MSMA unit can improve performance, reduce costs for different actuators and associated individual adjustment processes, lower part count, simplify construction, eliminate potential hotspots and make the MCB substantially more energy-efficient. The first products exploiting the beneficial magnetic, thermal and physical properties of MSMAs are expected to be on the market within five years.
Acknowledgment
The work described in this article was performed under a publicly-funded joint project called MAREGA (Magnetic Actuators with Reduced Gallium fraction) [5]. ETO Magnetic GmbH – a medium-sized enterprise with a focus on MSMA materials and applications – had the consortia lead. The company is part of the ETO Group, a leading supplier of electromagnetic actuators and sensors for the automotive industry.
References
[1] ABB Patent GmbH, “Switching Equipment comprising a thermal and electromagnetic trip device,” WO 2006/056336 Al, 22 Nov, 2004.
[2] A. Tüysüz et al., “Linear Actuator Utilizing Magnetic Shape Memory Material,” 12th International Symposium on Linear Drives for Industry Applications, Neuchatel, Switzerland, 2019.
[3] S. Breisch et al., “Combined Thermal and Magnetic Tripping of MSM,” ACTUATOR 2018: 16th International Conference on New Actuators, Bremen, Germany, 2018.
[4] S. Breisch et al., “Combining thermal and magnetic tripping of MSM in next-generation miniature circuit breakers,” International Conference on Ferromagnetic Shape Memory Alloys Prague, 2019.
[5] Bundesministerium für Bildung und Forschung, “MAREGA: Ressourceneffiziente magnetische Formgedächtnismaterialien mit reduziertem Galliumbedarf.” Available: https://matressource.de/de/projekte/projekte-alphabetisch/marega/. [Accessed February 9, 2021].
Photo p. 45: ©Andrey Popov/stock.adobe.com