ABB has completed an £800,000 main drive control system upgrade for a wind tunnel used for aerodynamic test and simulation to optimise the take-off and landing performance of civil aircraft. The upgrade was funded as part of a project led by QinetiQ and Boeing and supported by the UK Government through the ATI Programme.
Built in the 1970s, QinetiQ’s wind tunnel facility, measuring 5 metres by 4.2 metres, continues to play an instrumental role in the design and development of commercial aircraft. The substantial upgrade reduces downtime and improves the efficiency of operation to enable all customers to take full advantage of the testing capability, which is unique in the UK.
"ABB’s solution introduces a modern and state-of-the-art digital system to control the wind tunnel’s AC and DC main fan drive motors and auxiliary systems," says Paul Simons, QinetiQ’s 5mWT Head of Electrical. "The success of the project was made possible by ABB’s feasibility study to determine the electrical and mechanical demands of upgrading the existing system and ensuring any alternative design could interface with the current layout of the facility. This not only included a full review of original documentation and visiting the site to see the system in use but also talking to the end-users. By understanding how the system was being used and applying the tools that a modern HMI based system could offer, ABB is able to design a system that not only meets all operational requirements but also enhances user experience."
A key upgrade is to the main fan drive which is speed controlled using a traditional method featuring an 11 MW slip-ring AC induction machine, piggy-backed with a 1.6 MW DC machine. The AC induction machine torque is controlled via a hydraulically actuated liquid rheostat on the rotor. The speed is then accurately regulated using the DC machine. ABB also replaced the motor control centre, DC drive and the 11 kV to 690 V transformer, using mechanical and electrical services contractor IME to perform the installation.
The wind tunnel’s existing control system has also been replaced with a state-of-the art automation system that determines the switching routine for the AC machine as well as finely trimming the DC machine‘s control and avoiding oscillations. It also interfaces with the existing safety system and the tunnel control system while offering better diagnostics, improved reliability and greater flexibility during tuning.
"Beyond the obvious benefits of installing a current, supportable and reliable system, this project allowed the introduction of an HMI," explains Simons. “From the operator's perspective, the new automation system brings a comprehensive view of the plant through a well-constructed user interface for starting, stopping and monitoring the fan, and its auxiliary systems. Where discrete steps were once required by the operator to start the system, this is now handled by an automatic sequencer that provides feedback on the state of the plant as it transitions through the different phases before starting the fan. The interlocks are managed through a trip and interlock cause and effect matrix that very quickly informs the user on the state of readiness to start and what has caused a trip condition."
The graphics pages are designed with the operator in mind, with user-friendly layouts providing a comprehensive overview of the state of the plant. These include detailed alarm and event handling through to bar graphs that advise on overload facilities available.
The introduction of modern technology, enables better analysis of the wind tunnel's performance. Since the restart of the wind tunnel, testing efficiency and reliability has greatly improved. Based on findings, QinetiQ is looking at introducing further performance improvements to the wind tunnel such as replacing the liquid rheostat hydraulic actuator with a fully-electric linear actuator, for even finer position control, improved stability and better system settling time.
"As a modernisation project, the challenges of such an enormous application were not unexpected for us," explains ABB’s John Dixon. "For example, the wind tunnel is pressurised and totally replacing the motors was cost-prohibitive as this would have entailed cutting away the tunnel ceiling and nacelle and then welding it back into place. For this reason, the approach was to retain the existing machines, as they were in good condition, and to install a new DC drive, while retaining the liquid rheostat."
Achieving the control stability required for aerodynamic tests and good response times was quite challenging given the dual motor system and dynamics of the liquid rheostat. "Attempting to replace the liquid rheostat would have meant we had to de-rate the AC machine," says Dixon. "However, the facility requires the full motor capacity plus occasional use of the overload limit, and so de-rating the machine was not an option. We therefore needed to retain the basic scheme and look at ways of modernising it.“
Due to the large operating window of the tunnel, in terms of speed and pressure, a significant amount of time was spent capturing data for comparison to give a performance baseline before the upgrade was undertaken. Models of most of the system components were built from this data and incorporated into the control system to improve the control performance.
"Often a customer does not fully realise how poorly the original system is operating until they see the impact of the modern upgrades and retrofits," concludes Dixon.
"QinetiQ worked closely with ABB throughout and we found their engineers to be engaging, supportive and always willing to spend time with the users to ensure the functionality of the new system was fully understood," adds Simons.
The ATI Programme is delivered in partnership by the Aerospace Technology Institute, the Department for Business, Energy and Industrial Strategy (BEIS) and Innovate UK.
Photographs copyright © QinetiQ.
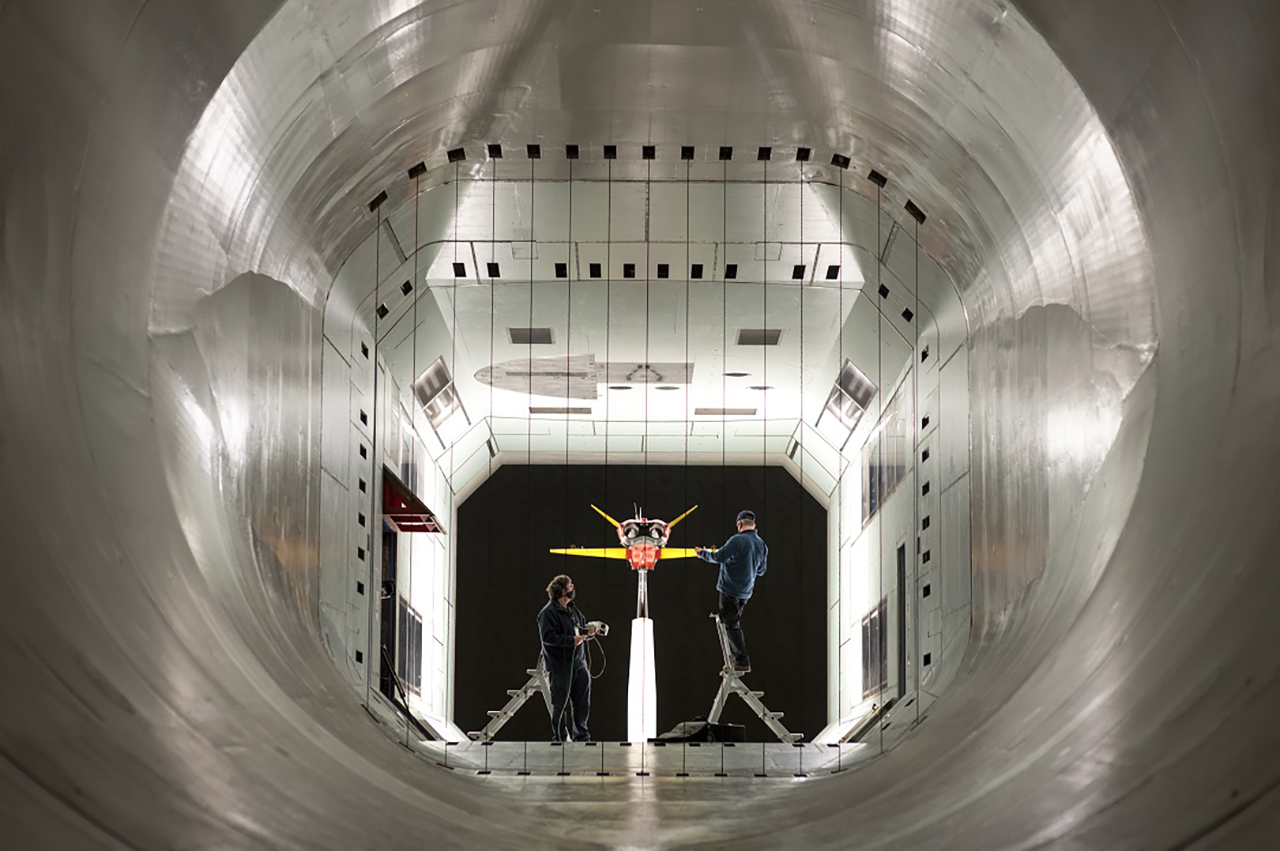