Gunnar T. Zank ABB Electrification, Distribution Solutions Heidelberg, Germany, gunnar.t.zank@de.abb.com
In an increasingly electrified world, switchgear plays a critical role in delivering constant, reliable electric power to almost every application imaginable. The task of switchgear is to transfer electricity safely and effectively from the medium-voltage (MV) – up to 40.5 kV – supply coming from power plants and utility networks to low-voltage (LV) – up to 690 V – distribution networks. Switchgear encompasses a number of electrical devices, such as circuit breakers, power monitors, motor and feeder controls, and protection devices.
The hidden cost of traditional switchgear technology
There are many hidden costs of traditional switchgear that can add up over the lifetime of the switchgear to significant totals, for example:
• The initial cost of device implementation and correct parameter value-setting, which can be time-consuming if the necessary information is hard to find.
• Coordination friction between the engineering and commissioning team when the design does not fully match on-site reality.
• Switchgear testing, including manual operational data collection and report creation, which can require costly and time-consuming coordination between the buyer, operator and manufacturer.
Operational costs are also a significant overhead in traditional switchgear. These expenditures include regular visual inspection, function checks and maintenance that is conducted on a preventative rather than an as-needed basis. Even worse, lack of insight into a device’s condition means operators are often forced to perform reactive maintenance, retain a collection of expensive spare parts or keep a trained maintenance team available in case of device failure. Despite being more expensive and disruptive, reactive maintenance is still far more common than preventative maintenance.
Further, switchgear has an average lifetime of 30 years. As power demands change over that time, it can be difficult for operators to calculate whether there is sufficient electrical and thermal capacity in the existing switchgear to support new components. This can lead to new equipment being purchased unnecessarily.
Unlocking data unlocks cost savings
Electrical infrastructure already produces data. For example, protection relays count operation and trip cycles and this data can then be used to estimate contact wear and other breaker conditions. Motor controllers – employed in everything from industrial operations to air conditioning – can collect data on motor load conditions that helps the operator detect problems in motors or attached machines. However, the data these smart devices create is only as useful as the user’s ability to collect, access and take action on it.
In many cases, data remains where it is due to the lack of the specialized knowledge needed to set up and program the smart devices, fieldbuses and Ethernet communications required to access it. However, if accessed and incorporated into a single system, this data could be used to identify the right threshold settings, monitor ongoing performance and help drive cost-effective predictive switchgear maintenance based on actual condition information, which is far preferable to waiting for a costly failure to occur.
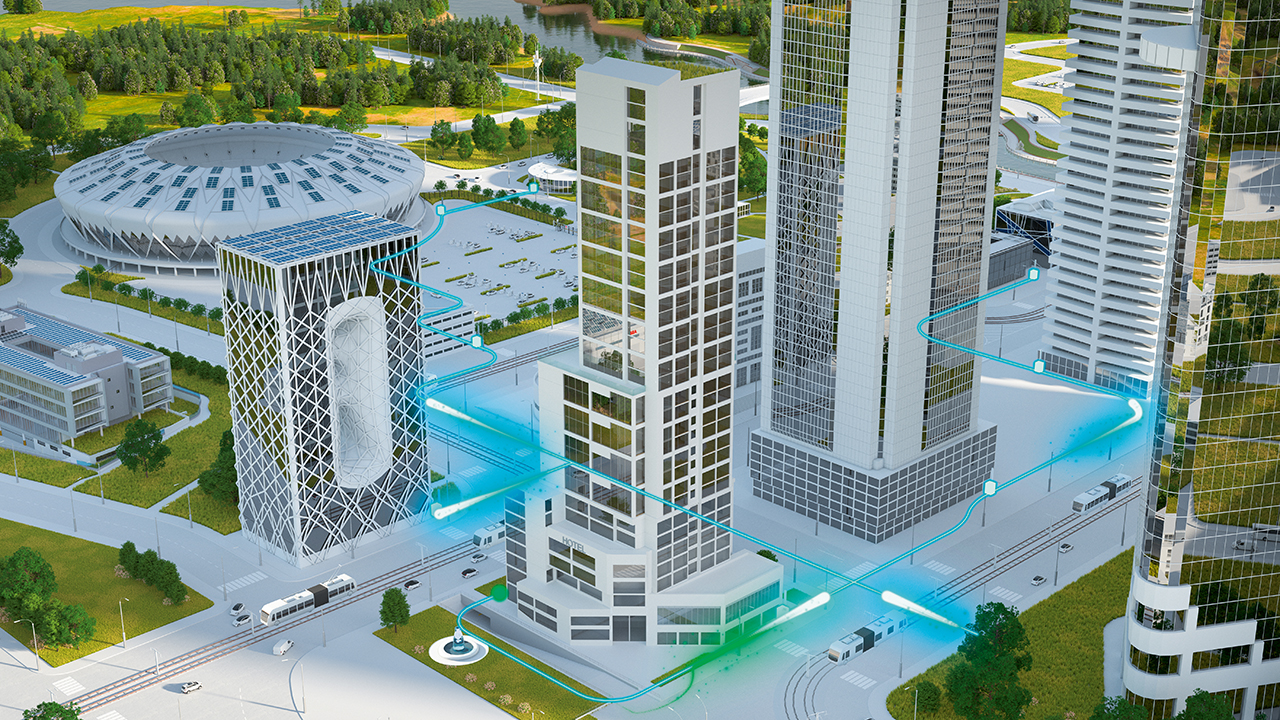
Digital switchgear massively simplifies the task of liberating data from device silos to make it available for analysis, enabling cost-saving actions to be identified →01.
The advantages of digital switchgear
With a digital switchgear solution, the operator can not only collect data automatically, but also store and analyze it to facilitate data-driven decisions while applying lifetime analytics for further value creation. This data can be used, for example, to provide condition monitoring that can:
• Verify switchgear function and performance before a factory acceptance test
• Demonstrate the switchgear’s condition with a condition report during factory acceptance tests and commissioning
• Identify elements that need repair before they fail during operation
• Analyze performance data to determine condition-based maintenance requirements
• Better plan maintenance in advance and shift from preventive to predictive maintenance
Moreover, with on-site data collection throughout the switchgear’s lifetime, digital switchgear solutions provide the basis for asset management solutions that better estimate the remaining useful life of electrical equipment and the probability of failures.
An even more effective approach is to add comprehensive condition monitoring to the switchgear or the site’s entire electrical assembly – eg, with ABB Ability™ solutions. These solutions uses sophisticated data analysis and algorithms to automatically and continuously convert data from the devices into actionable insights that are easily accessible to maintenance personnel via a dashboard. Together with past lifetime data such as commissioning date, maintenance dates and performed maintenance, this data will become actionable information that drives decisions.
Switchgear digitalization is not only for new installations – any switchgear can be digitalized by adding smart devices and sensors as desired.
Smart communications, devices and sensors for digital switchgear
Digitalization of switchgear involves an array of technology. For example, for monitoring purposes, digital MV and LV switchgear is connected via Ethernet-based digital communication links, including the widely used IEC 61850 and Modbus TCP or OPC UA →02. These communication protocols are commonly found in Industrial Internet of Things (IIoT) platforms.
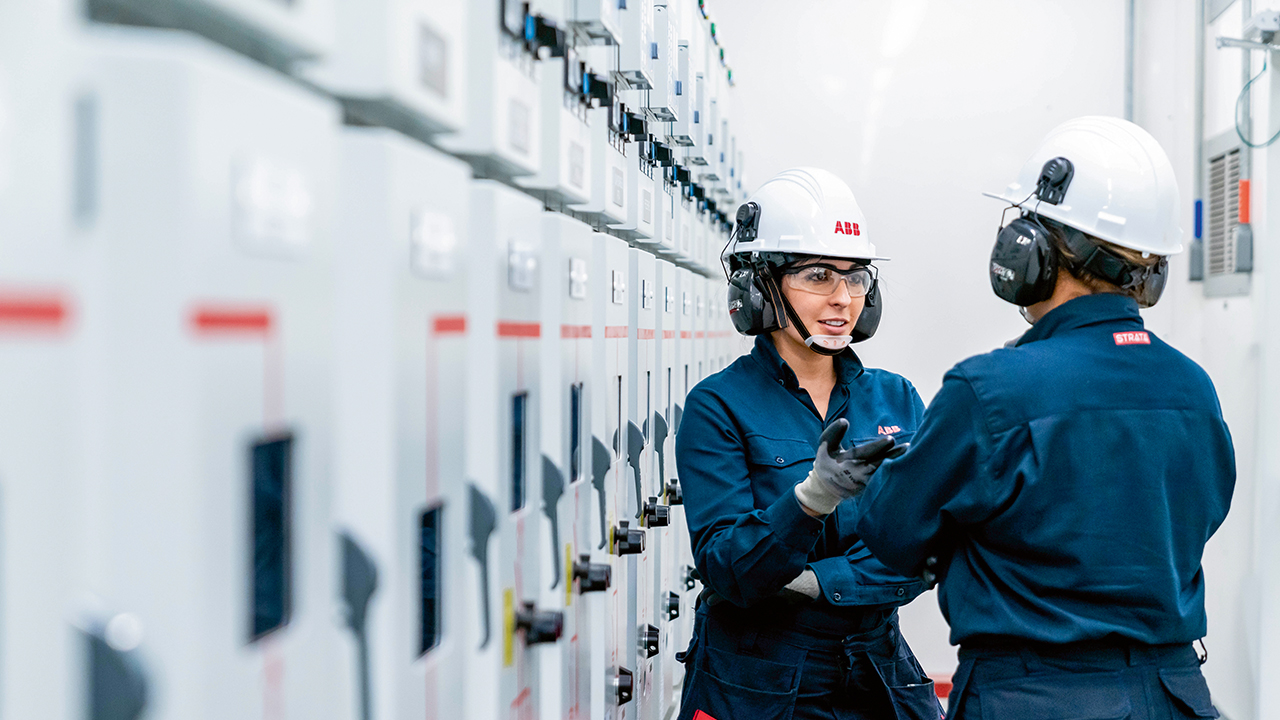
Circuit breakers, together with intelligent electronic devices (IEDs), such as ABB’s Relion® relays or Ekip control and protection units for LV breakers are core elements of switchgear digitalization. IEDs not only perform control and protection functions but include a feature for circuit breaker condition monitoring that provides an operator with data that can be analyzed and used for scheduling circuit breaker maintenance or functional testing. At the same time, a runtime counter enables the scheduling of time-based maintenance for the connected motor or transformer. Data collected includes:
• Electrical parameters such as current, voltage and power
• Time-stamped alarms and events
• Circuit breaker condition data with real-time counter and values
• Changes in load levels
With more sensing technologies becoming available, the circuit breaker itself becomes more digitalized and can provide more accurate information about its condition. Moreover, collection and monitoring of data from other switchgear assembly components and sensors – such as earthing switches, disconnectors and door lock position indicators – provides further insights into the electrical and mechanical status of the assembly without the need to be present in the switch room, thus enhancing overall safety for the operation and maintenance teams.
Thermal aspects
With MV and LV switchgear section or panel condition monitoring, temperature and humidity data can be collected from the switch room and inside the switchgear →03 – 04. This data provides an understanding of the operating conditions and their potential impact on the switchgear over its lifetime. Further, constant monitoring of critical electrical connections eliminates manual maintenance tasks and ensures that data is continuously recorded and analyzed. In MV switchgear, monitoring the insulation and partial discharge occurrences provides even more information.
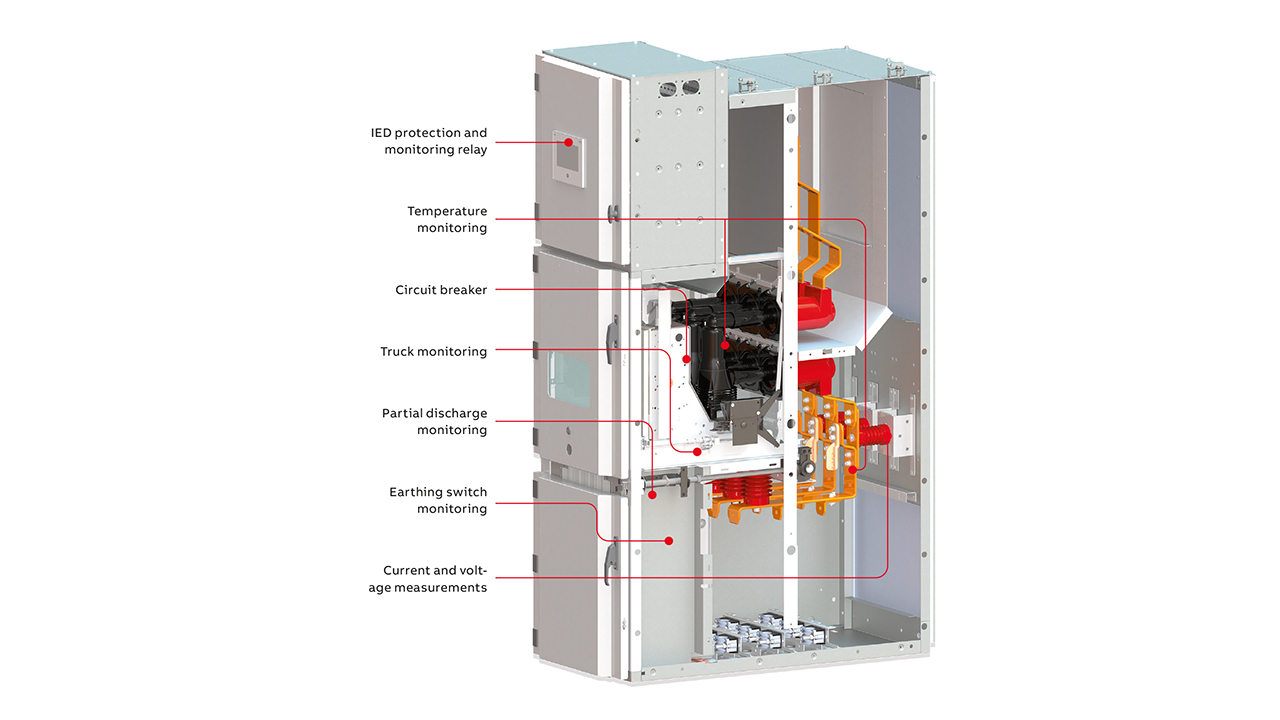
LV switchgear is mainly used to distribute energy to hundreds of loads such as motors or sub-distribution panels. Located in various areas of a building or plant, LV switchgear is often exposed to temperature and humidity changes and extremes. Although switchgear is designed to cope with these external influences while accommodating a certain level of internal heat generation, extending the demands on the equipment can result in further heat generation. Traditionally, an operator calculates how much extra load can be added without exceeding the thermal and electrical capacity of the switchgear under the expected ambient temperature and humidity conditions. This undertaking is prone to error. However, digital switchgear can provide valuable historical and current data to help operators and planners make the right decisions for extension planning.
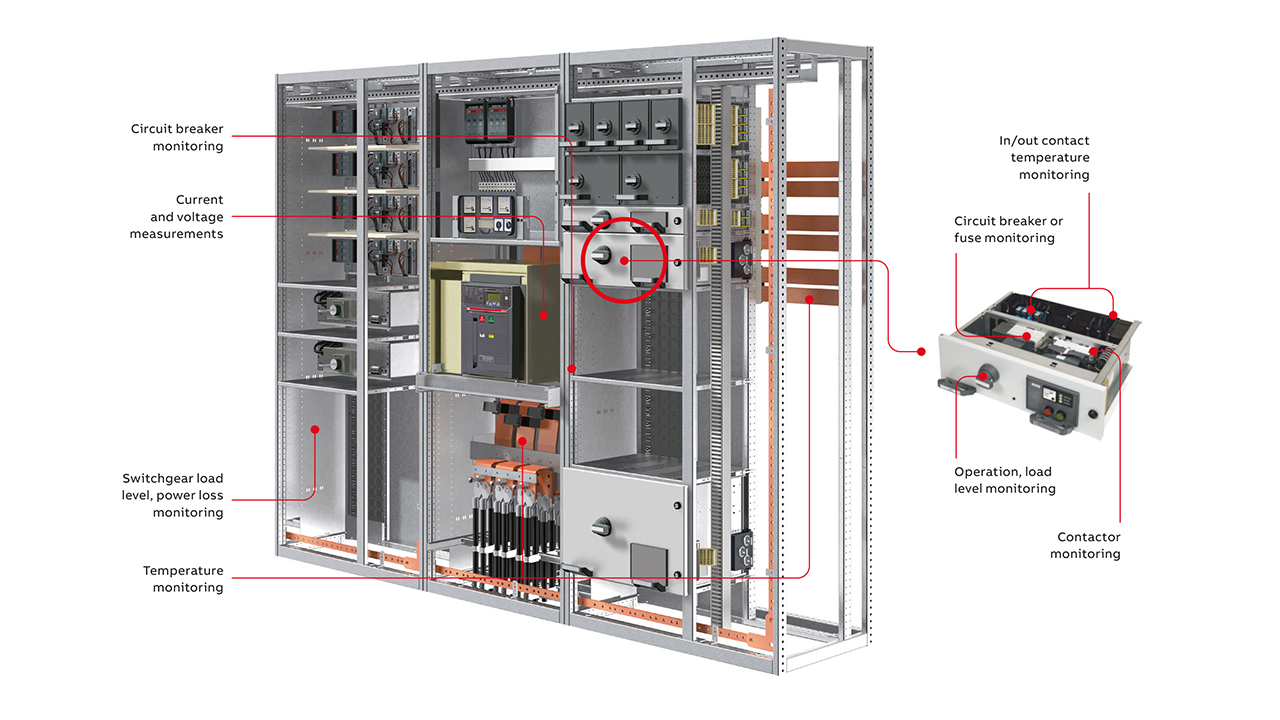
Monitoring LV digital switchgear modules
LV switchgear also has various types of modules that feed motors or external loads. This is another area where maintenance, although regularly required, is sometimes overlooked. For example, removable modules use specially designed contact systems for power connections that withstand a certain number of operations. These contact systems require maintenance such as greasing, which is traditionally conducted in maintenance cycles that may not align with the actual maintenance needs of the component. For this example and other situations, data relating to a digital switchgear module can be provided by smart devices such as a power meter and motor controller. This equipment monitors various parameters to better understand conditions. Maintenance cycles can be calculated and maintenance effort is minimized by working only on those modules in need, avoiding total switchgear shutdowns.
Motor controllers
Smart LV motor controllers comprise another group of devices whose digital capabilities are often underutilized. While the primary function of these devices is motor control and protection, they are capable of collecting additional valuable data, such as:
•Motor current levels and imbalances
•Thermal loading levels •Operating and condition data
•Temperature, humidity and other data using additional sensors.
Abnormal motor current levels and imbalances can indicate issues with a motor or connected machine. With this data, the user can go beyond switchgear monitoring and monitor the complete power train.
To the edge and beyond
For digital switchgear to deliver its many benefits to electrical systems, careful analysis of the data generated and collected is required. Any analysis on-premise is generally limited to local data, while situations and experiences from other sites are not considered. Should all the data be sent to a data center (ie, the cloud) for further analytics, machine learning and the application of artificial intelligence? Not necessarily. Data may also be processed in real-time on a local computer, server, or even the device that collects it – so-called edge computing.
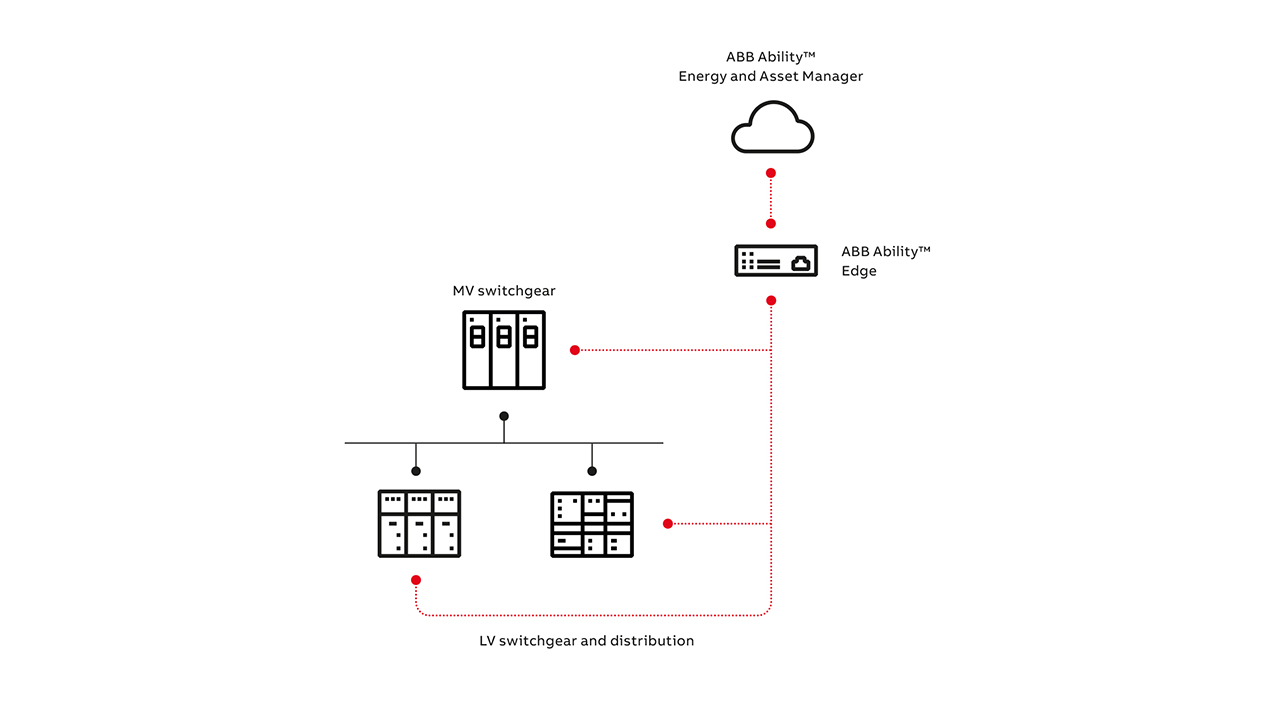
ABB Ability gives the best of both worlds. ABB Ability is a set of ABB industrial solutions that use digital technology. ABB is digitalizing its complete range of products and services and uses a cloud-based platform built on technology from Microsoft Azure to offer a broad range of analytics and services →05. Because ABB Ability solutions are also installed on edge devices, the user has the option to connect to on-site systems or cloud-based solutions for maintenance management.
An edge device is relatively inexpensive to install and operate while still providing a suitable level of on-site calculation power and data storage, making it an effective solution whether used solely on-premise or connected to the cloud. Many users of digital switchgear adopt edge computing as a crucial part of their hybrid data architecture thanks to its ability to vastly reduce latency, reduce the need for data centers and cut down on costly bandwidth requirements. And with connectivity to ABB Ability™ cloud-based solutions, the user can extend predictive capabilities that help understand probabilities of failure across multiple sites and switchgear, enabling further operational cost reduction while making switchgear capable for the future needs of Industry 4.0.