Tim Gartner Hoisting Electrical Montreal, Canada, tim.gartner@ca.abb.com; Magnus Uddman Advanced Services Västeräs, Sweden, magnus.x.uddman@se.abb.com
ABB, one of the world’s largest suppliers of complete mine hoists, and the only company that manufactures and supplies both associated electrical and mechanical systems, has introduced a newly developed platform of mine hoist safety products. Known as ABB Ability™ Safety Plus for hoists [1], the platform is composed of three solutions: Safety Plus Hoist Monitor (SPHM), Safety Plus Hoist Protector (SPHP), and Safety Plus Brake System (SPBS), which includes Safety Brake Hydraulics (SBH).
Mine hoist brake systems are the most safety-critical sub-components of a mine hoist. With this in mind, ABB designed SPBS to include both hydraulic and PLC-based Safety Integrity Level (SIL) 3 brake control sub-systems, thus ensuring seamless integration while maximizing the performance of the complete brake system. In order to be assigned a SIL rating, a hoist control and safety system needs to be designed from the ground up according to IEC62061 functional safety standards. For more on SIL, see insert →01.
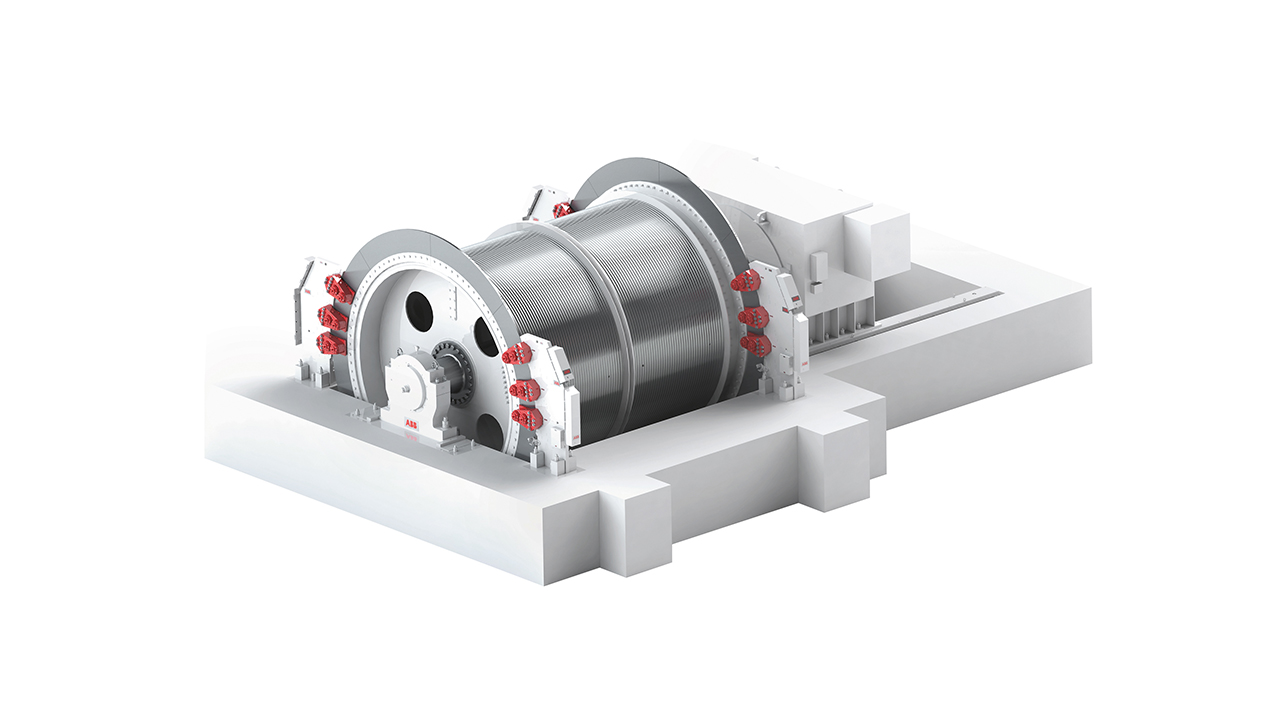
For completely new ABB mine hoists, the Safety Plus platform can be designed into a system from the start. This means the resulting mine hoist will be fully SIL 3 certified, including the brake system as well as hoist protections. Furthermore, enhanced shaft and infrastructure protection, such as shaft gates, cage doors, remote emergency stop buttons, and more, can be provided by SPHP. Of course, the Safety Plus platform can also be implemented on new mine hoists manufactured by other OEMs.
ABB Ability™ Safety Plus for hoists includes a number of advanced self-testing and diagnostic functions that, in the case of degradation of performance of a safety feature, will either correct performance automatically or flag operations and maintenance personnel early on if potential maintenance issues arise. These functions occur automatically and while equipment is in operation, thus reducing downtime for equipment testing.
The platform can also be used to transfer performance data and test results to ABB Ability™ Performance Optimization for hoists →02, an analytics suite. There, field data regarding speed, position, brake pressure, temperature, time, and actuator position, is sensed and subjected to analysis to allow site engineers to identify discrepancies and take remedial actions.
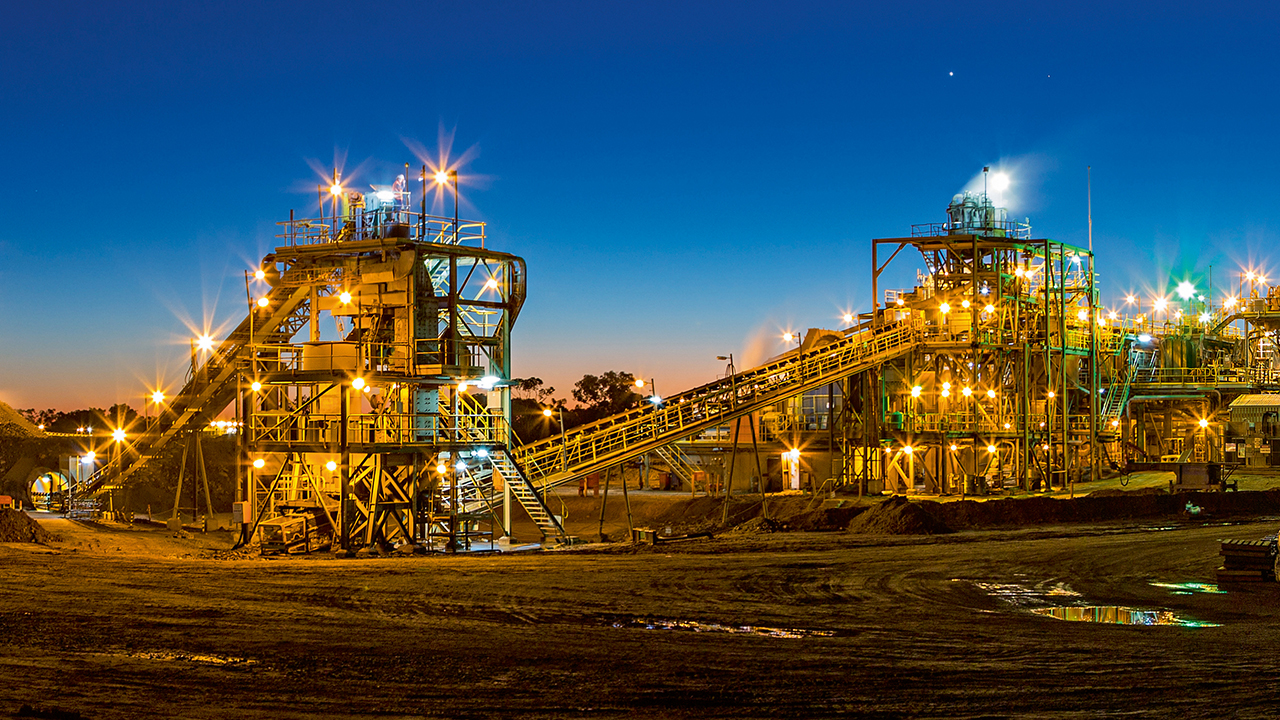
The first fully SIL 3-independently certified platform for mine hoist solutions, ABB Ability™ Safety Plus for hoists offers a range of customer benefits, including best-in-class reliability, and easy (plug and play) integration into existing hoist systems →03.
Redefining mine hoist control and automation
In addition, seamlessly integrated with ABB Ability™ Safety Plus for hoists, as well as ABB Ability™ Performance Optimization for hoists, is the soon-to-be-released, ABB Ability™ NGX Hoist Control Platform.
Designed to comply with all regional- and country-based mine hoist regulations and legislation, the new NGX platform will help large, global mining clients because, regardless of their location, the hoist control system delivered by ABB will be the same, thus providing numerous operational and maintenance advantages.
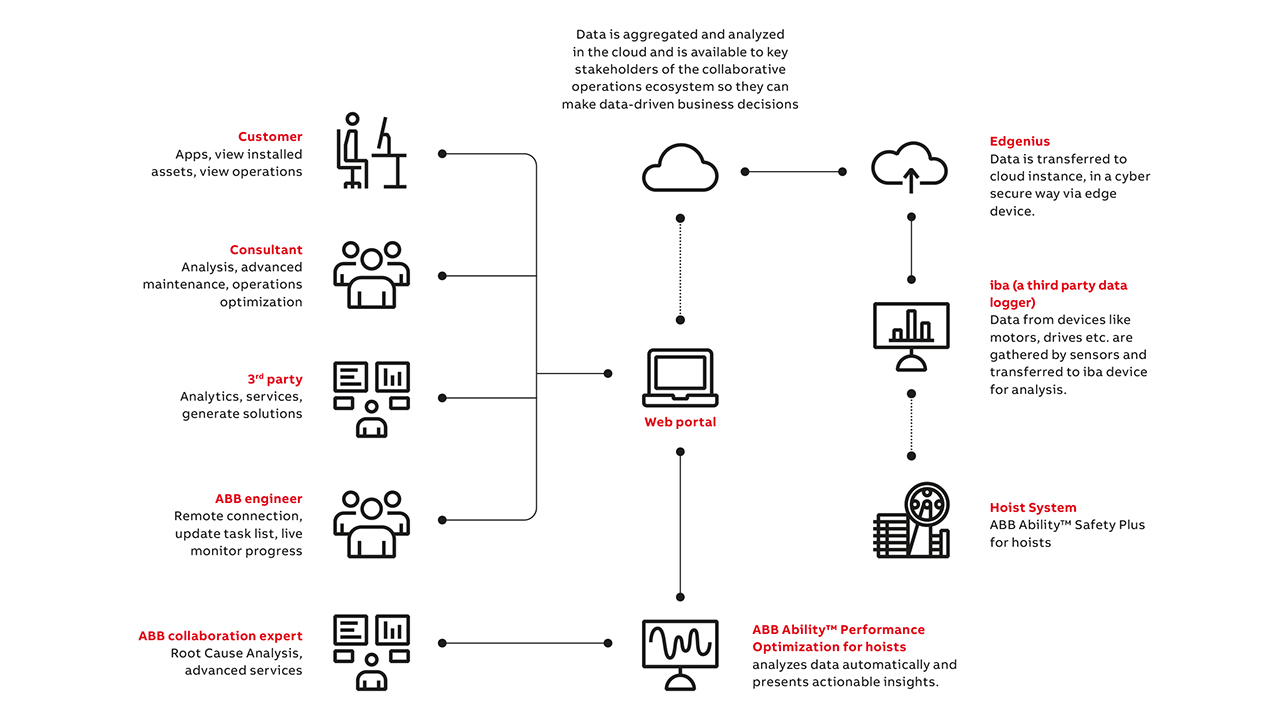
The design of the new platform builds on years of ABB experience and expertise in designing mine hoist control systems. In addition to providing the highest level of standard hoist control functionality, the modular features of NGX provide a platform for optional performance-enhancing software applications →04, including:
• Demand Driven Control
• Automatic Rope Oscillation Control
• Automatic Controlled Rollback.
As new mine hoist performance-enhancing software applications are developed, they can be easily integrated with the NGX Platform.
A second advantage associated with its modular features is that the NGX platform can be economically installed on mine hoists ranging from the smallest to the largest. It is also designed for use on all mine hoist types, such as friction, drum, and Blair multi-rope hoists, and can be operated in conjunction with all mine hoist applications, such as service, production, auxiliary or shaft sinking.
Last but not least, the NGX Hoist Control Platform uses ABB’s latest PLC and HMI systems and technology. Its operator stations →05 and graphical screens are based on human factors engineering concepts, thus providing hoist operators with intuitive and easy-to-understand menus and graphic screens for the operation and control of mine hoists.
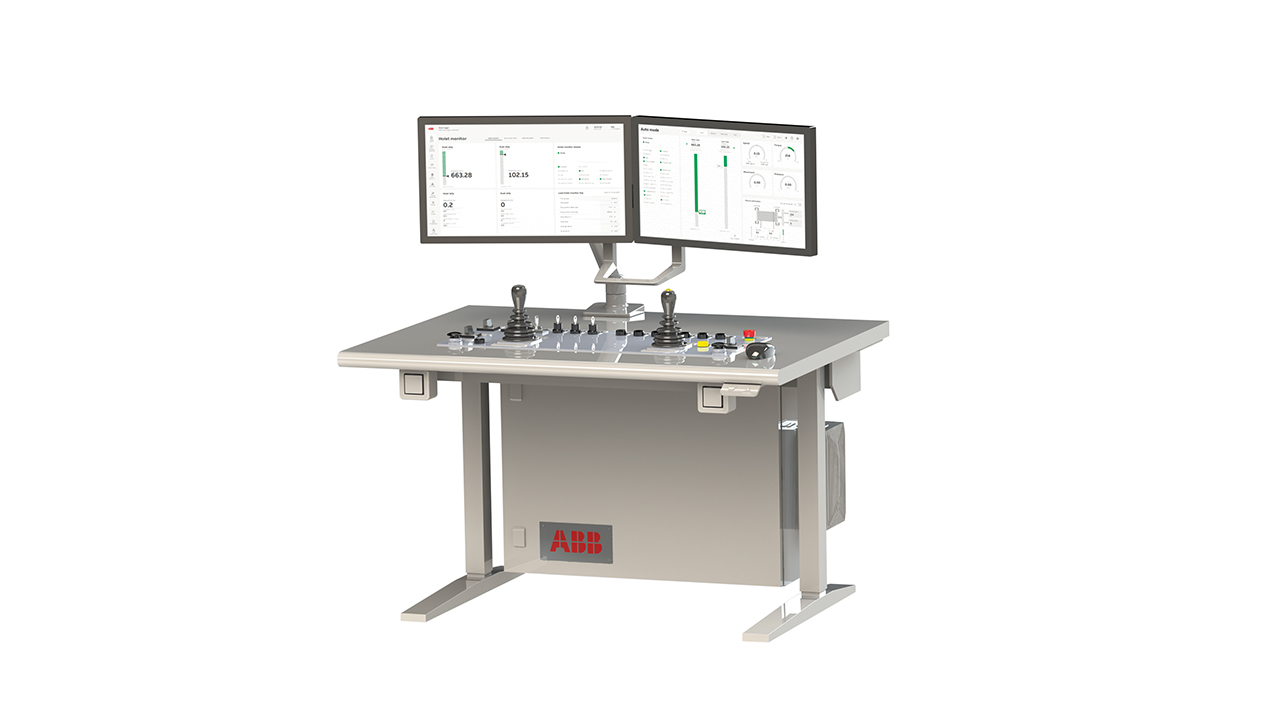
All in all, ABB mine hoist solutions can provide the lowest possible life cycle cost, the highest possible reliability and system availability, short project execution time, and a single source of supply for complete systems, including service and spare parts.
ABB has more than 130 years of experience in hoisting and more than 1,000 hoisting solutions installed worldwide. Digitally connected with
ABB Ability Performance Optimization for hoists, ABB hoisting solutions provide the highest availability and productivity.
References
[1] ABB Ability™ Safety Plus for hoists portfolio. Available: new.abb.com/mining/underground-mining/mine-hoist-systems/abb-ability-safety-plus-for-hoists [Accessed January 18, 2022].
[2] ABB Ability™ Edgenius dashboard application. Available: https://new.abb.com/process-automation/edgenius/abb-ability-edgenius-dashboard-visualize-your-needs-and-realize-your-opportunities [Accessed January 18 2022].
[3] ABB Ability™ collaborative operations for mining. Available: https://new.abb.com/mining/digital-transformation-in-mining-industry/abb-ability-collaborative-operations [Accessed January 18, 2022].
SIL IN A NUTSHELL
SIL (Safety Integrity Level) is a term used by International Functional Safety Standards including IEC61508 and IEC62061. Simply put, it quantifies the relative safety of a system with a unitless number ranging from 1 to 4. The higher the number (SIL level), the higher the level of safety. ABB Ability™ Safety Plus for hoists uses SIL 3 components in all instances where they are available. These components include PLCs, encoders, relays, switches, etc. and since they are SIL 3-rated, they are generally more reliable and come with published reliability data.
The higher the level of safety integrity, the lower the probability that the safety-related system will fail to carry out its required safety functions. At the component level, more and more electrical/electronic components, such as PLCs, speed encoders, switches, relays, etc. are available at SIL 2 and SIL 3 levels, meaning that these subcomponents provide the highest level of hardware safety and reliability available.
REMOTE SUPPORT FOR HOISTS WORLDWIDE
ABB Ability™ Performance Optimization for hoists is a digital service designed to improve the uptime, availability, performance, and productivity of mine hoists by providing actionable information on key performance indicators (KPIs) →02a. Hosted on the ABB Ability™ Edgenius Dashboard application [2] – a cloud-based solution that offers a digitized way of working with reports while enhancing transparency – it enables quick analysis and insights into any plant’s operation.
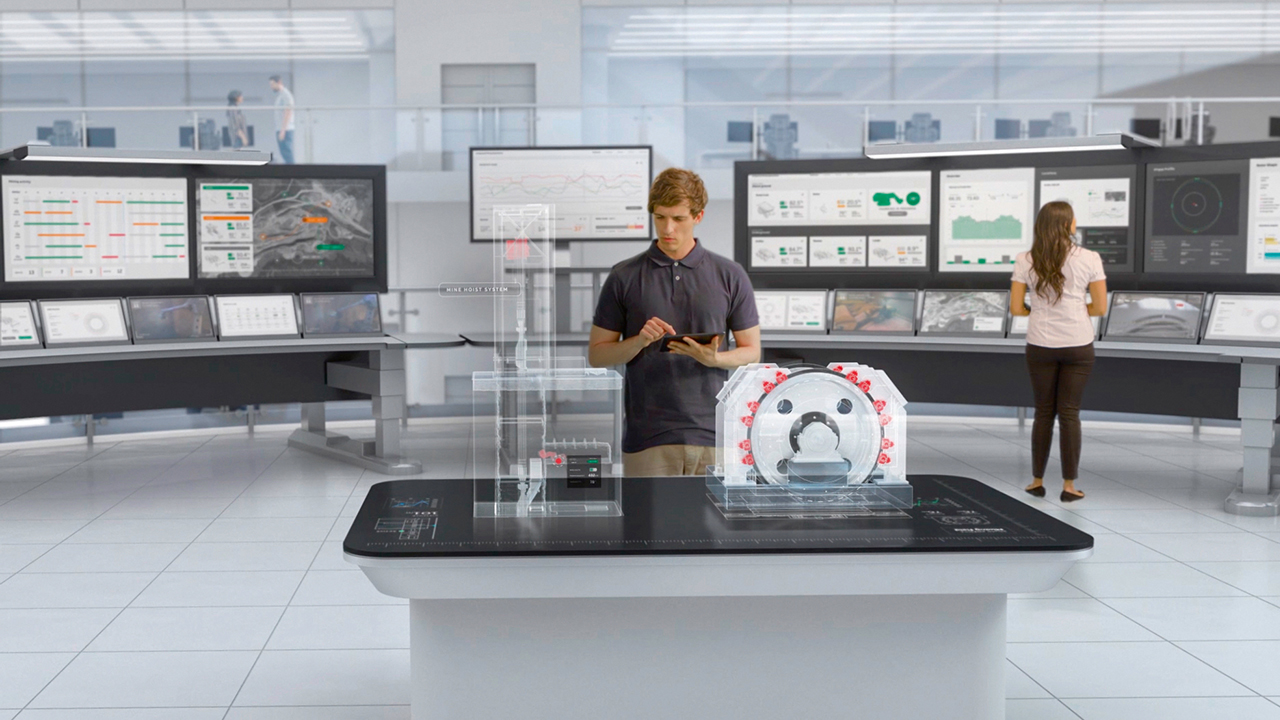
The dashboard shows crucial, customer-requested information from hoists with KPIs organized into the categories of performance, supervision, and safety. Additionally, the platform is flexible, scalable and meets the highest levels of cybersecurity.
Predictive analysis of a mine hoist’s condition prevents unexpected, time-consuming and costly shutdowns, and opens the door to uninterrupted condition-based monitoring. Data is automatically collected, categorized, and managed, then securely monitored and analyzed to generate actionable insights that can increase production performance, identify safety hazards, and provide optimized maintenance scheduling.
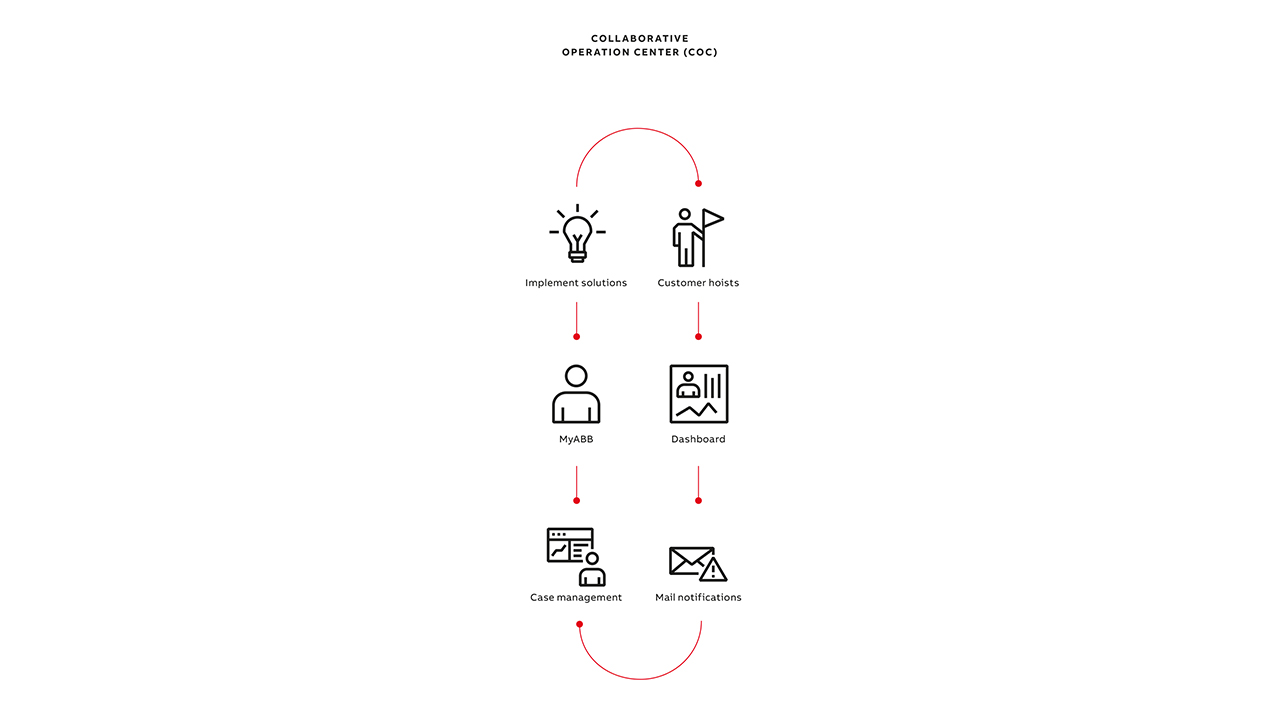
ABB’s Performance Optimization service connects customers’ mine hoists enterprise-wide with experts located remotely in ABB’s Collaborative Operations Centers →02b [3], or on site. Mine hoists are monitored 24/7, meaning that potential problems are identified before they can cause damage, and necessary actions can be taken at the right time. This improves the availability of equipment and the overall safety of mining operations.
The ABB Ability Edgenius Dashboard is available and secured within the ABB Ability™ cloud. Customers can follow ABB actions as they happen, collaborate, and learn from events onsite or remotely. This reduces the requirement for in-person maintenance visits and travel, saving time and lowering ABB’s carbon footprint.
The Dashboard creates a cyber-secure bridge between a mine hoist customer’s information technology (IT) and operational technology (OT) elements. This helps to establish an increasingly connected infrastructure, more collaborative relationships, and greater transparency in terms of real-time data reporting and actions. The backbone of this service is in its infrastructure →02c, where all data transferred to and from site is handled in the most cyber secure way. Fault tracing and solution investigation are possible only through a secure VPN connection. The raw hoist data is stored on the premises, where it is easily accessible for both customer and ABB experts for deeper analysis if needed.
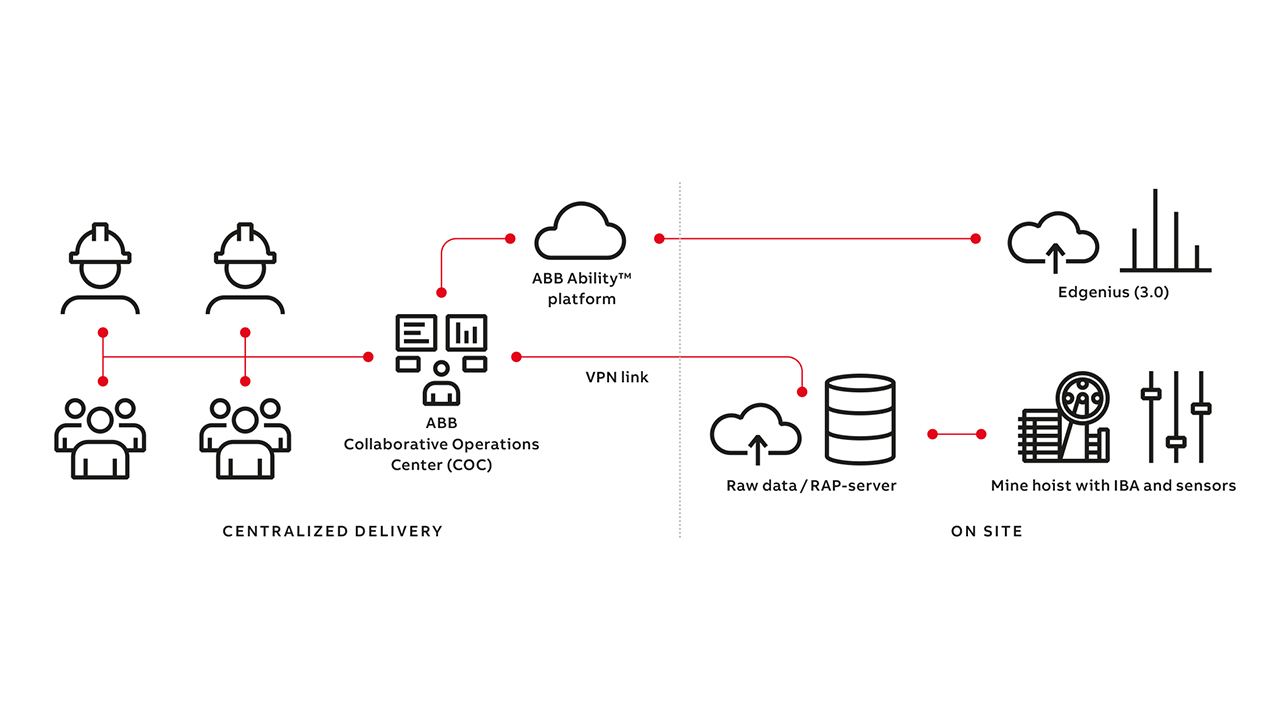
Furthermore, ABB Ability Performance Optimization for hoists improves accessibility, performance, and productivity for mine hoists by collecting and analyzing data from various operating points and KPIs, such as mine hoist cycle time, filling and dumping time, as well as the safety brake system and supervision of hoist protections. The results can be used as a basis for optimizing the hoist’s availability, which can offer opportunities for further increasing production.