Subhashish Dasgupta ABB Corporate Research, Process Automation Bangalore, India subhashish.dasgupta@abb.in.com; Tuomas Kekki, Jukka Varis ABB, Marine & Ports Helsinki, Finland, tuomas.kekki@fi.abb.com, jukka.varis@fi.abb.com
With capability to sustain performance even under the harshest marine environments, ABB’s Azipod® propulsion system represents the best-in-class in propulsion technology on the market today. The performance of the sealing system is crucial to the reliable operation of this system. Recognizing this, ABB’s experts are working together to push the boundaries of seal performance beyond current limits. Azipod® experimental experts and multiphysics modeling research scientists embarked on a collaborative investigation to dive deeply into the complicated physics of the sealing system; this is the account and the results of their journey with a view to the future.
Azipod® propulsion: a history of innovation
Launched more than 30 years ago, ABB’s Azipod® propulsion system leads the global marine propulsion shipping market today. With the electric drive motor situated in a submerged pod outside the ship hull →01 – 2, the Azipod® system can rotate 360 degrees; this significantly increases the maneuverability and operating efficiency of a vessel and reduces fuel consumption by up to 20 percent compared to conventional shaft-line systems. Because both the pod motor and its shaft are located completely outside of the ship‘s hull, the pulling propeller receives a steady undisturbed wake field; there is practically no vibration during maneuvering, and both noise and vibration from a stern thruster are eliminated.
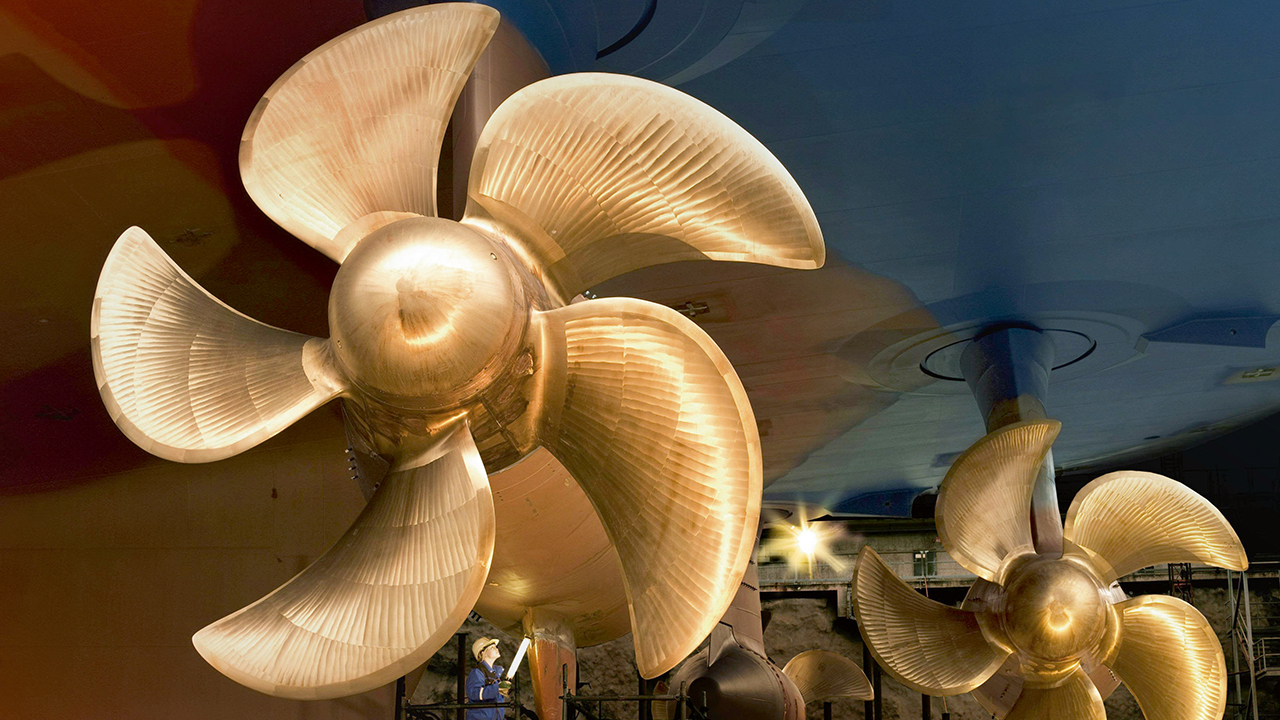
For example, the hybrid-electric exploration cruise vessel, Le Commandant Charcot fitted with two ABB’s Azipod® propulsion units →01 – 3, is not only the first exploration cruise vessel to reach the geographic North Pole, this vessel initiates a new era of sustainable and comfortable cruising in extreme environments, eg, icy waters. Eliminating noise and reducing vibrations, increases passenger comfort and safety; and thanks to the enhanced Azipod® system’s maneuverability, the vessel navigates smoothly, cruising in zero-emissions mode while exploring remote locations (here, the Azipod® propulsion system has a combined power of 34 megawatts).
Exemplary performance
To ensure the smooth performance of Azipod® systems, the condition of the sealing system requires regular intense scrutiny, as vibration can have an effect on the sealing system. The sealing system comprises a series of elastomer seals mounted on the propeller shaft, which contain sealing oil between adjacent seals; this ensures high quality lubrication and cooling of the sealing system – so necessary for superior performance.
Although the currently used sealing technology for ABB’s Azipod® propulsion system exhibits high performance even under adverse conditions, eg, during the vibration imposed by ice formations encountered by vessels, such as that experienced by ice-going vessels like Le Commandant Charcot and ice breakers, it is worthwhile to push the boundaries of safe and reliable performance to the highest possible limits. Given the ever-worsening and unpredictable climatic conditions observed [1], coupled with today’s stringent global norms [2], ABB believes this to be essential.
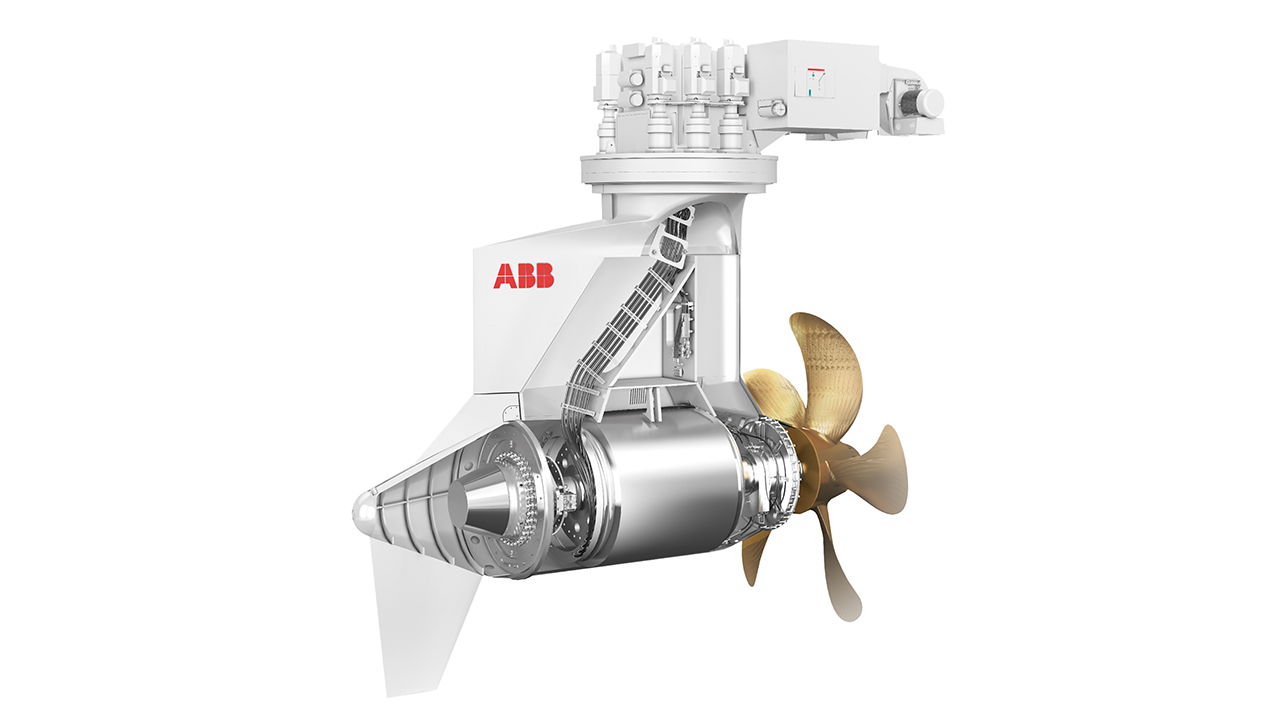
Innovative approach
Whereas much of ABB’s expertise concerning Azipod® sealing systems is based on experience, advanced computational techniques, eg, multiphysics modeling, can help garner insight into seal physics for improvement. In mid-2021, ABB began to delve into the advanced physics and functional aspects that underly the Azipod® sealing system. ABB set out to pinpoint the parameters that influence performance, through experimental tests and modeling, to understand the factors that impact operation of the current sealing system; to develop guidelines to optimize operational parameters and to improve the sealing system for the future.
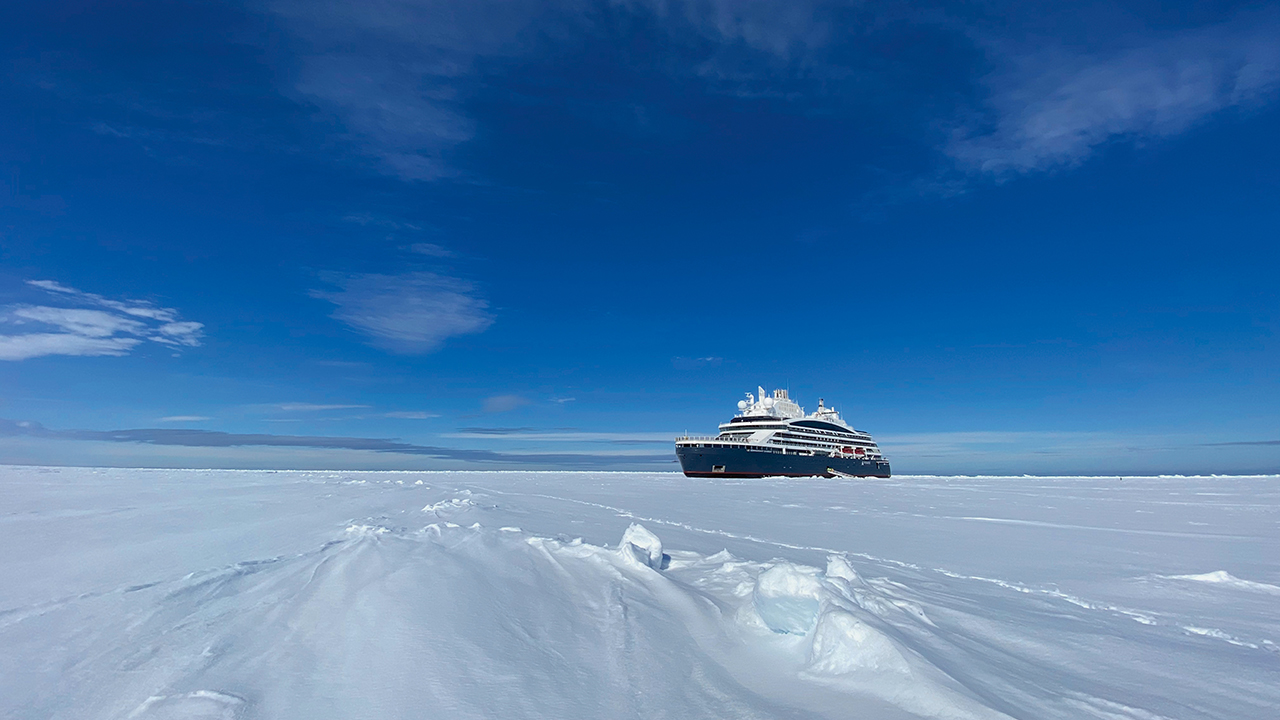
ABB’s holistic approach
Extensive tests were designed and performed on a sample Azipod® sealing system, housed in an ABB testing facility which would yield realistic information about the parameters that influence performance. In parallel, multiphysics models, which comprised a sequence of CFD (computational fluid dynamics) and structural dynamics modeling, were developed to simulate the performance of the sealing system under various, yet, specific conditions. In this way, ABB sought to bring forth a holistic view of critical parameters, such as oil flowrate, pressure, temperature and structural stresses. Critical analysis of the modeling results would yield invaluable knowledge regarding the complicated underlying physics of Azipod® to better equip ABB for future product upgrade efforts.
The models were initially validated using data from measurements; this established confidence in the modeling approach. Subsequently, the models were employed to evaluate several aspects of performance that were impossible to investigate using laboratory tests alone. In short, new insights into seal physics could be gleaned.
Tests, tests and more tests
Because experiments were integral to the project, tests were conducted rigorously: The sealing system was mounted on the rig and instrumented with temperature, pressure, vibration, and oil level sensors for an estimation of critical parameters. Analysis of these parameters provided a comprehensive understanding of system performance under diverse situations: Initial tests replicated normal operation of the sealing system while subsequent tests simulated challenging scenarios such as those that occur during shaft vibration (replicating the impact of icy conditions) to understand performance of the system.
Image currently unavailable
Image currently unavailable
Image currently unavailable
Image currently unavailable
Image currently unavailable
Image currently unavailable
Image currently unavailable
Image currently unavailable
Image currently unavailable
Image currently unavailable
Image currently unavailable
Image currently unavailable
04a Temperature measured at critical locations within the seal material and seal oil compartments. 04b Vibration level measured during vibration testing. 04c Oil pressure measured within the oil chambers in the sealing system. 04d Investigation at individual seal level. The seal was embedded with a temperature sensor and examined for possible wear after testing.
04 Experimental test results.
Temperature rise was measured at several positions and at varying shaft rotational speeds →04a within the seal material and in the oil chambers; this yielded valuable information about frictional heating effects at the seal-shaft contacts. The system was operated under normal- and vibrating conditions, to observe possible alteration in performance due to vibration. The level of vibration was monitored →04b at several shaft speeds, among other parameters, such as oil pressure →04c. The oil tank, (not shown here) which supplied oil to the seal, was monitored for level changes to detect possible oil leakage between adjacent chambers at the seal contact. Seals were individually examined for possible deterioration →04d by embedding sensors to measure temperature; and then by measuring the seal contact width to detect possible wear.
Multiphysics model-based investigations
To complement the extensive testing efforts, multiphysics modeling studies were performed to evaluate seal performance under conditions simulated in the tests. With the capability to compute critical parameters in three dimensional space and as a function of time, the modeling techniques, based on finite element and finite volume calculations, are considered, by far, to be the best models for multiphysics analysis. Initially, the models were compared with the test results for validation. With sufficient confidence in the modeling approach, the models were then extensively used to evaluate performance aspects impossible to evaluate by testing.
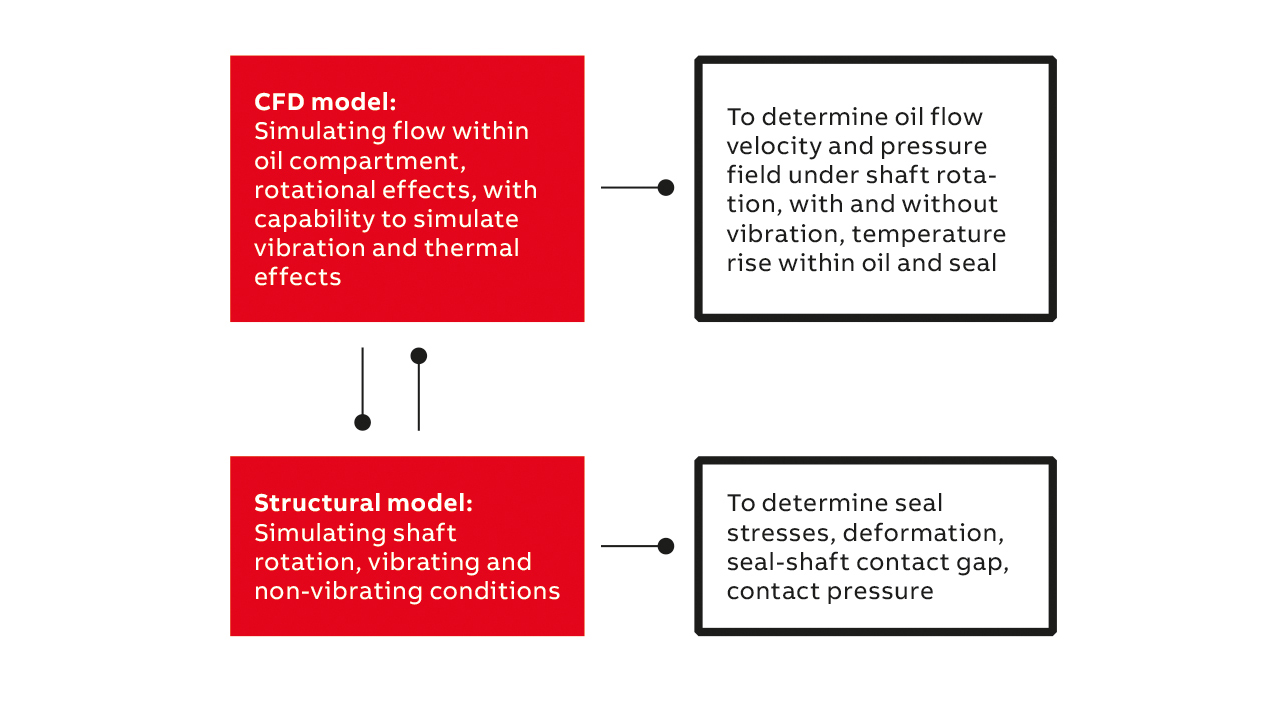
The modeling studies were performed in a specific sequence →05. CFD models were developed to understand fluid dynamics and thermal propagation within the oil space and seal structure, under various operating conditions, while structural dynamics models were used to analyze structural issues, eg, seal stress, deformation, and shaft-seal contact gap, and thus were useful in studying the impact of vibration. Depending on the particular investigation, structural dynamics modeling was conducted subsequent to CFD modeling or vice versa.
Image currently unavailable
Image currently unavailable
Image currently unavailable
Image currently unavailable
Image currently unavailable
Image currently unavailable
Image currently unavailable
Image currently unavailable
Image currently unavailable
06a Computational fluid dynamics (CFD) modeling domain to investigate oil dynamics during operation. Flow dynamics within oil space, including narrow contact gap computed by model in 3-dimensional space. 06b Pressure field within oil space computed by CFD model. 06c Temperature field within oil, seal and supporting structure computed by CFD/thermal model.
06 Computational model results.
Flow dynamics within the oil chambers, and within the narrow seal-shaft gap →06a, was simulated by the CFD models, as was the pressure field →06b. Flow dynamic calculations were used to estimate the rate of oil transfer from one chamber to the other, under a given set of operating conditions, eg, oil pressure and shaft speed, for a selected oil variety. By including the frictional heating load and enabling thermal calculations, the CFD model computed the temperature field within the oil and the seal material →06c.
Image currently unavailable
Image currently unavailable
Image currently unavailable
Image currently unavailable
Image currently unavailable
Image currently unavailable
07a Computational domain of structural dynamics model for analyzing structural issues during operation. 07b Discretization of computational domain.
07 Computational domain and discretization thereof is shown. Due to the software used, ANSYS, the resolution of the images is low.
Because the primary focus of the investigation was to determine the impact of shaft vibration on performance characteristics, structural dynamic models comprising the seal, shaft and garter spring were developed →07a. The input data to the models were primarily the oil pressure on the seal and the vibration frequency and amplitude prescribed to the shaft. Using advanced tools, the model was discretized →07b to solve the structural dynamic equations.
Image currently unavailable
Image currently unavailable
Image currently unavailable
Image currently unavailable
Image currently unavailable
Image currently unavailable
Image currently unavailable
Image currently unavailable
Image currently unavailable
08a Stress and deformation of seal during operation. Due to the software used, ANSYS, the resolution of the image is low. 08b Seal-shaft contact gap variation with shaft deflection computed by structural mode 08c Contact pressure as a function of shaft defection computed by structural model.
08 Primary outputs of the structural dynamics model used to quantify the vibrational conditions.
This resulted in the primary output of the structural dynamics model: seal stress and deformation →08a, the contact gap →08b and the seal contact pressure →08c as a function of shaft deflection – quantifying the vibrating condition.
Image currently unavailable
Image currently unavailable
Image currently unavailable
Image currently unavailable
Image currently unavailable
Image currently unavailable
09a Model reveals fluid pressure oscillation under shaft vibration, not seen during non- vibrating conditions. Confirms corresponding fluctuations observed during tests. 09b Oil dynamics within seal space, during shaft vibration computed by CFD model with moving boundary condition.
09 Comparisons were made of the observational test results and the models computed results, which agree.
An important purpose of the modeling approach was to confirm the test observations and therein the associated conclusions. For example, the fluctuation observed in oil pressure measurements during shaft vibration was confirmed by similar observations →09a in the results obtained from the CFD model →09b with a moving boundary simulation capability to evaluate vibration effects.
The conclusions based on the CFD and structural dynamics modeling results have contributed to a deep understanding of the operation of the current Azipod® sealing system, and have been instrumental in helping ABB derive guidelines to optimize operational parameters facillitating future sealing design modifications.
Looking forward
While experimental methods are able to successfully evaluate sealing system performance, thereby providing invaluable information for developing guidelines to upgrade current seal systems, synergizing experimental and high-end multiphysics modeling techniques have allowed ABB to glean new insights into sealing performance. Being able to go beyond what can be tested experimentally, the results of ABB’s collaborative efforts will help to propel the upgrade of ABB propulsion systems. ABB envisions that a knowledge-bank of seal performance physics will be an invaluable asset; one that will drive future endeavors to take Azipod® propulsion technology to the next level.
In this way, ABB’s Azipod® propulsion system will continue to be the preferred means of operating in sensitive and challenging marine environments, even as climate changes, and ABB demonstrates that their commitment to innovate is in good alignment with the current global call to promote sustainable performance.
References
[1] Johanna L. Miller “Ocean currents respond to climate change in unexpected ways”, Physics Today, Vol 70, No. 1, 2017, p. 17.
[2] DNV AS “Safeguard shaft seals and propeller shaft bearings – avoid costly failures”, 2022, Available: https://www.dnv.com/news/safeguard-shaft-seals-and-propeller-shaft-bearings-avoid-costly-failures-215171 [Accessed August 11, 2022].