Richard Daumas ABB Food and Beverage Beynost, France, richard.daumas@fr.abb.com
With their sheer scale and high production rates, it is little wonder modern food and beverage plants consume significant quantities of electrical power. Fortunately, the benefits of digitalization provide a way for these plants to optimize their energy usage. Digitalization allows detailed metering and monitoring of a plant’s entire electrical system and is the key to improving energy efficiency. With a digitalized system and ABB smart metering and monitoring in place [1], all relevant electrical parameters can be measured with high accuracy and devices can freely exchange information between themselves, the cloud, an energy management system and an asset performance management platform →01. As a further motivation to digitalize, it has become clear that up-and-coming standards will require high-accuracy monitoring of electrical parameters and power quality at many acquisition points.
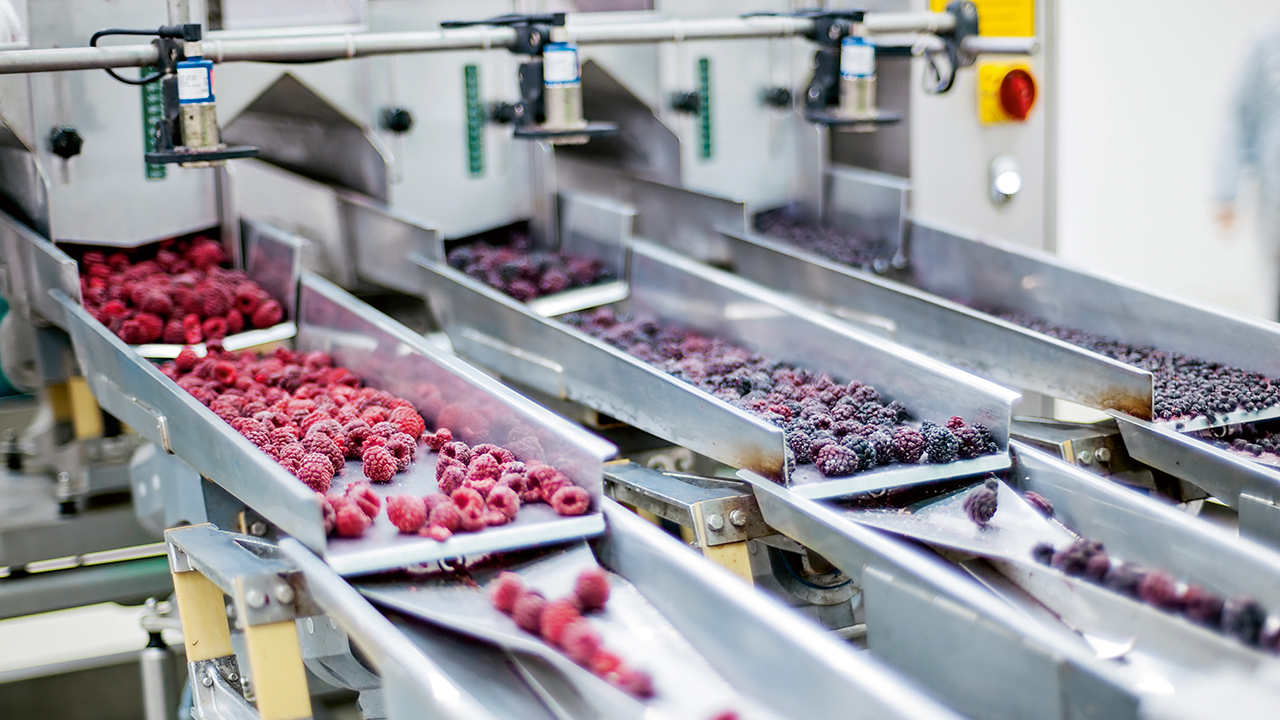
Detailed metering and monitoring can also guarantee the uninterrupted availability of electrical energy, which is business critical for food and beverage companies. Unplanned interruptions or disturbances in the power supply can incur significant costs related to product loss, production downtime, or supply chain interruption. This potential exposure to business disruption and financial loss is another reason why food and beverage companies give very careful thought to a site’s electrical distribution system and how it is monitored and managed.
Standards for energy management systems
International standards, such as ISO 50001 Energy Management Systems, make it easier for industries to integrate energy management into their quality and environmental efforts. The framework of requirements provided by ISO 50001 helps companies develop a policy for more efficient energy use, define ways to meet the policy and use data to make good decisions regarding the policy. ISO 50001 expands previous standards with new data-driven sections related to energy planning, operational control, measuring and monitoring. By adopting ISO 50001, companies can benefit from:
• Energy reduction, (of up to 10 percent within 12 months, in some cases).
• Reduced greenhouse gas (GHG) emissions and carbon footprint.
• Assistance in compliance with current and future voluntary and/or mandatory energy efficiency targets.
• Improved corporate image and credibility among customers, clients and stakeholders.
• Informed decision-making processes from system design to operation and maintenance.
• Increased energy usage awareness among staff members at all levels.
• Improved operational efficiencies and maintenance practices.
For low-voltage applications, metering requirements are set out in the IEC 60364-8-3 standard, which states that, for the incoming part of the facility, it is necessary to have detailed monitoring of all electrical parameters. This mandated supervision includes advanced power and power quality monitoring, and network performance analysis – a further incentive for food and beverage companies to digitalize.
Comprehensive products and connectivity
For the food and beverage industry, ABB has a full range of solutions, software, digital tools and devices that measure and analyze energy consumption in great detail, improving data-driven decisions and optimizing maintenance scheduling. ABB metering and monitoring products typically deliver a short payback time, a 7 percent improvement in energy efficiency [2] and ensured access to certification under LEED (Leadership in Energy and Environmental Design – the most widely used green building rating system in the world). Furthermore, these products enable authorized persons to connect a facility to the cloud in under a day and initiate monitoring of the entire electrical system. In fact, cloud connectivity is emerging as a necessity for compliance with newer international standards and regulations.
Thanks to the measurement accuracy of ABB metering and monitoring devices, the user can easily:
• Better identify any inefficiency within the electrical distribution system
• Better identify inefficiencies at a single component level
• Make the right decisions to improve energy efficiency and avoid unnecessary actions.
• Exploit predictive functions to anticipate and avert potential failures and issues in the electrical infrastructure. In this way, continuity of production is ensured, which is crucial in the food and beverage industry.
A full set of local monitoring and control tools
For local monitoring and control, ABB offers a full set of flexible solutions to fit all installation requirements. For instance, devices in the Tmax XT molded-case circuit-breaker (MCCB) family deliver information about current, voltage and operational parameters – eg, temperature, pressure and vibration – that can be digitalized at the device level and stored, analyzed, visualized or downloaded →02.
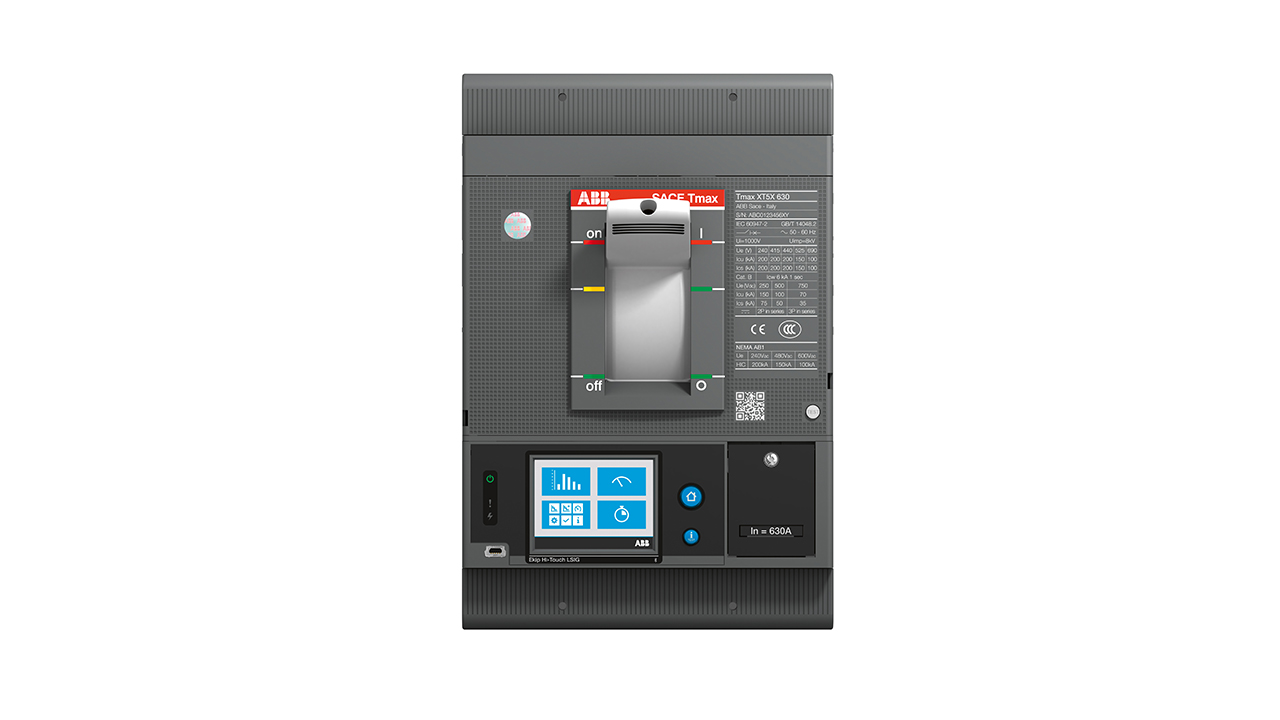
These digital breakers come equipped with a color touch screen and connect to smartphone and tablet-based apps that allow users to navigate menus of information about why a circuit has tripped. This is a huge improvement in terms of ease of use and value-added information available for customers.
Tmax XT MCCBs have embedded native communication protocols (Modbus RTU, Profibus DP, DeviceNet, Modbus TCP, Profinet, Ethernet/IP and IEC 61850) that allow interconnection between all relevant ABB and third-party devices. ABB’s range of Ekip communication modules further extends the Tmax XT’s capabilities →03.
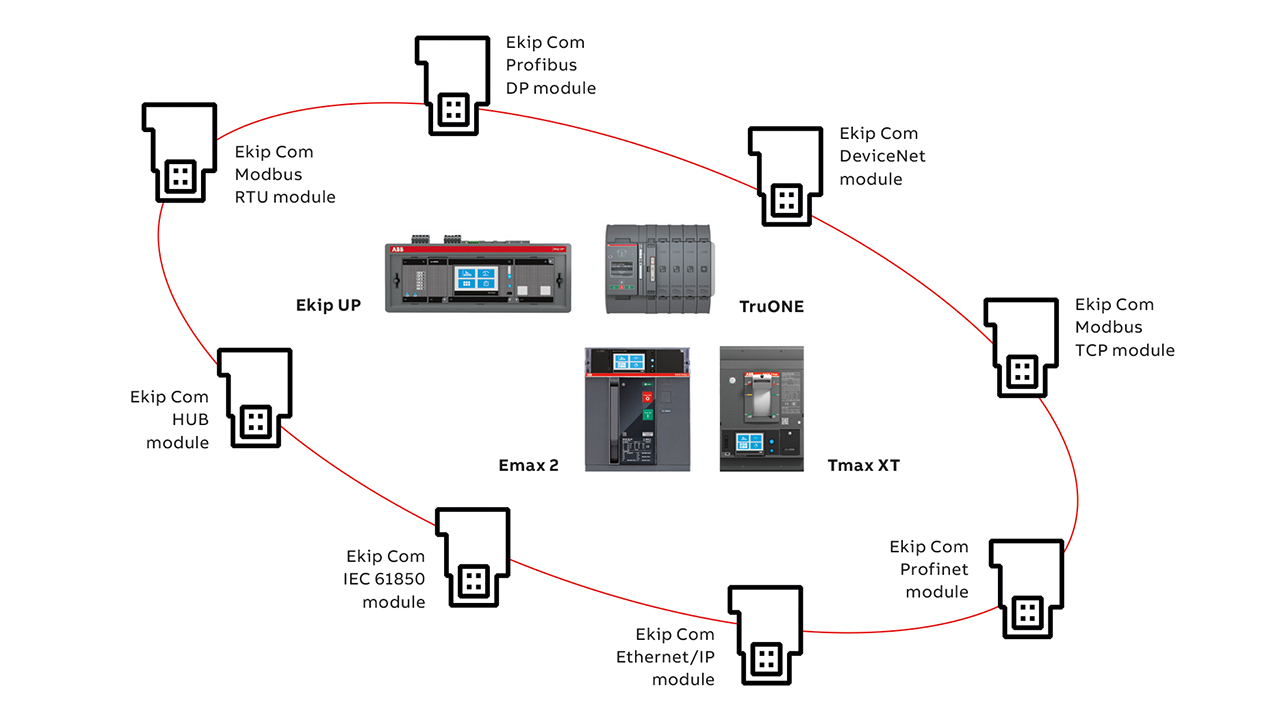
Bringing it all together
ABB Ability™ Energy Manager and ABB Ability Asset Manager are solutions that enable an on-premise or cloud approach to monitoring and analyzing site equipment. Together, these solutions allow managers to control an entire site’s electrical distribution system (and multiple energy sources). ABB Ability Energy Manager facilitates multi-utility monitoring, energy audits and cost management in a single, intuitive dashboard that helps organizations understand their energy consumption and identify areas for improvement – in one location or across multiple sites →04. ABB Ability Asset Manager alone can deliver a 30 percent savings in operating expenses.
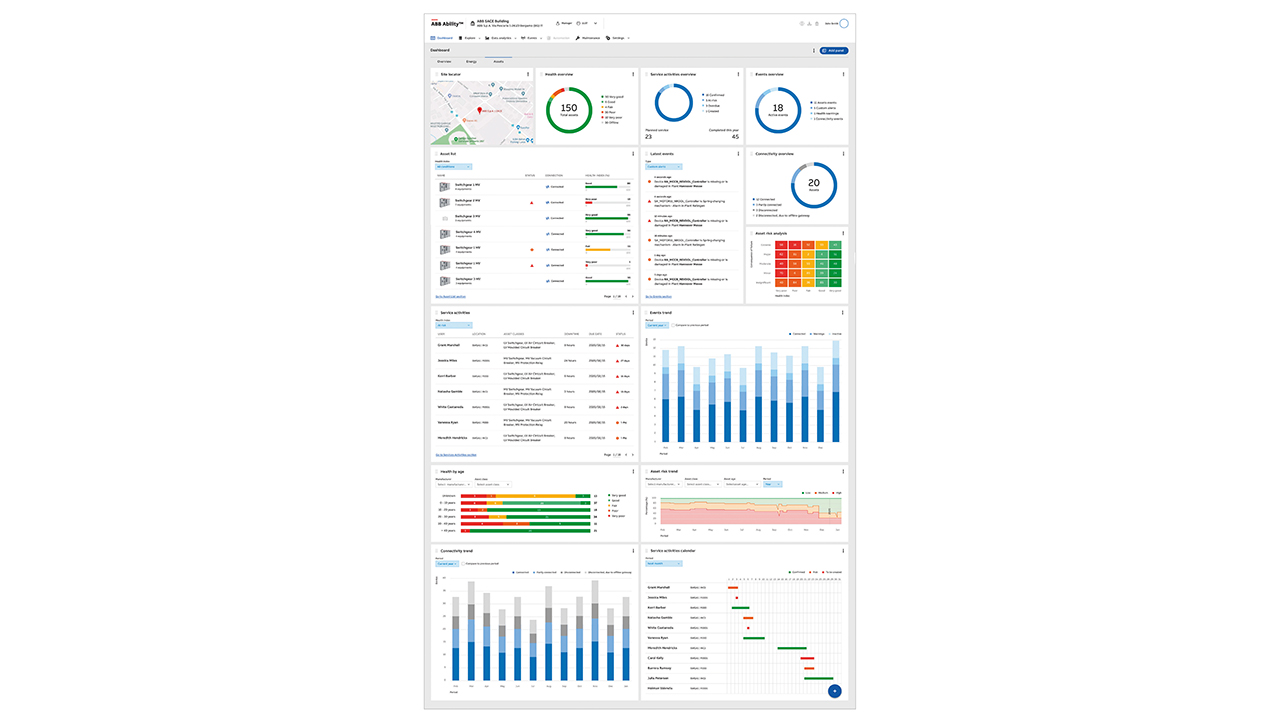
Across a range of facility types, including food and beverage plants, ABB Ability Energy Manager and ABB Ability Asset Manager provide not just device-level visibility, but empower insights at the system level. The associated cloud architecture was developed in partnership with Microsoft to guarantee world-class reliability and security from end to end.
One of the most valuable functions offered by ABB Ability Asset Manager is predictive maintenance, which allows the monitoring of the overall plant health condition through a smart visualization (traffic light display). With this visualization, the user can monitor the system at a glance and benefit from proactive alerts. Operation and maintenance cost savings are achieved thanks to optimized scheduling and spare parts management – customers know exactly what components they might need, avoiding unnecessary spare parts purchases and saving time.
Fiorentini feasts on energy savings
One of Europe’s leading manufacturers of crackers, cereals and rice cakes, Fiorentini, has specified ABB Ability Energy Manager to control the entire electrical power distribution across its new sustainable 56,000 m² production facility in Trofarello in Italy →05. The installation will support Fiorentini’s ambitious commitments to reduce energy consumption by 400,000 kWh each year.

Monitoring almost 100 intelligent devices across the factory, the ABB Ability Energy Manager provides a real-time digital twin to remotely monitor the status of all critical power distribution and consumption points, and the performance of critical assets on the factory floor. This total visibility across all assets allows Fiorentini to make informed decisions on production line performance and energy consumption, maximizing energy savings and making the factory as sustainable as possible.
Luca Perri, operations manager for the Fiorentini factory said: “With our new ABB digital platform we can set up the cost plan on a daily basis to quantify real-time energy consumption. This allows us to optimally allocate energy resources and assets, which will help us to achieve our ambitious energy saving targets.”
In an industrial setup, such as that at Fiorentini, the ABB Ability Energy Manager is not only able to monitor consumption at the main power distribution switches, but, in combination with ABB’s circuit monitoring system CMS-700 →06, is also able to track energy use all the way down to the lowest branch of the electrical system, such as the building’s lighting. Other ABB components, for example, open-air Emax 2 circuit breakers →07, as well as Tmax T4 and T5 MCCBs further assist customers in achieving their energy usage targets.
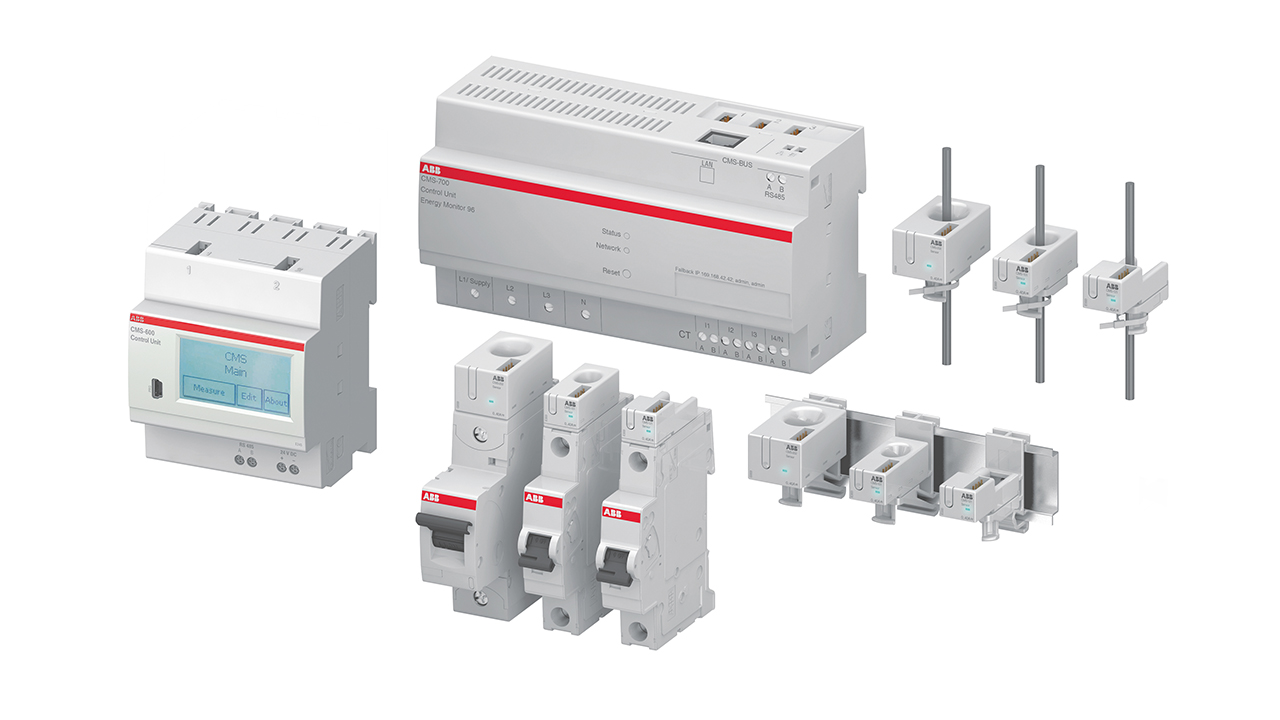
With its full range of smart metering and monitoring solutions, ABB is well placed to measure and analyze energy consumption throughout an entire food and beverage plant, or even across geographically separated plants [3]. In this way, food and beverage producers can not only optimize their energy consumption while complying with all relevant standards but also select the best maintenance strategy and eliminate unplanned downtime to ensure their plants keep delivering quality produce for their customers.
References
[1] ABB, “Smart Metering and Monitoring.” Available: https://new.abb.com/low-voltage/launches/smart-metering-and-monitoring. [Accessed February 16, 2022.]
[2] N. Kampelis and D. Kolokotsamar, Eds., “Smart Zero-energy Buildings and Communities for Smart Grids.” New Jersey: John Wiley & Sons, 2022.
[3] ABB, “Food & Beverage.” Available: https://new.abb.com/about/our-businesses/electrification/electrification-food-beverage. [Accessed February 16, 2022.]