De Danske Gærfabrikker producerer gær til hele verden. ABB AbilityTM System 800xA er hjernen i den stadigt mere digitale og energioptimerede fabrik. Næste projekt er at anvende dataanalyse til at optimere køleprocessen.
Umiddelbart forbinder man ikke gær med højteknologi. Men hos De Danske Gærfabrikker i Grenå bevæger man sig i disse år hastigt mod Industri 4.0 og visionen om den digitale, integrerede fabrik. Ud over at fordoble produktionskapaciteten er teknisk chef Jack Domino og hans kolleger i færd med at energioptimere fabrikken; ligesom man til sommer bygger nye køletårne, som via brugen af dataanalyse skal optimere køleprocessen.
- Vi vil fordoble mængden af gærekstrakt, vi producerer, men uden store investeringer i nye produktionsanlæg. I stedet ønsker vi at øge kapaciteten ved at skabe et bedre flow gennem hele fabrikken, forklarer Jack Domino om optimeringsstrategien for fabrikken, der blandt andet skal øge antallet af fermenteringer pr. uge.
Bagegær kun en mindre del af forretningen
De Danske Gærfabrikker producerer det, man kan kalder basisgæren. Det vil sige basen for det, der senere bliver til produkter som bagegær, vingær og diverse smagsforstærkere til fødevareindustrien. 25.000 tons gær bliver det til om året.
Den velkendte 50-grams bagegærspakke med det kendte malteserkors har de fleste danskere et forhold til, men faktisk fylder bagegær til detailhandlen ikke særlig meget i virksomhedens samlede omsætning - kun cirka 20 pct.
På verdensmarkedet er der langt større efterspørgsel på gærstammer til eksempelvis bakterieproduktion, gærekstrakt samt fermenteringsbase til fødevarer og dyrefoder. Og det er baggrunden for De Danske Gærfabrikkers markante udvidelse i disse år.
Åbne systemer er vejen frem
Her spiller ABB AbilityTM System 800xA en afgørende rolle som fabrikkens digitale skelet, der sørger for, at samtlige ventiler, centrifuger og procesanlæg kan tale sammen.
- Det giver ellers ikke sig selv, forklarer Jack Domino. Fabrikken køber maskiner og udstyr fra forskellige leverandører, så derfor er det nødvendigt med et åbent styresystem, der kan integrere signaler fra eksempelvis PLC’er fra forskellige leverandører. Det er muligt takket være PLC connect-modulet i 800xA, der netop integrerer tredjeparts-udstyr.
- Åbne systemer er vejen frem. Vi har behov for at kunne købe en specialmaskine fra enhver leverandør, og så skal den bare virke fra dag ét, lyder det fra Jack Domino.
Energibesparelser på 25 pct.
800xA-systemet er også en vigtig del af De Danske Gærfabrikkers bestræbelser på at implementere en mere cirkulær, energibesparende produktion. Takket være en generel fintuning af samtlige anlæg samt genanvendelse af dampkondensat er det indtil videre lykkedes at reducere fabrikkens energiforbrug med 25 pct.
Fabrikken drives nemlig på damp, men det er først nu, at man er begyndt at genanvende dampkondensatet , så det igen kan blive til damp.
- Energi forsvinder jo ikke bare, men før i tiden kunne vi ikke spore energiens vej gennem systemet. Det kan vi i dag takket være System 800xA. Tidligere var det mere baseret på mavefornemmelser, men nu kan vi sætte ind præcist dér, hvor gevinsten er størst, forklarer Jack Domino.
Senest har De Danske Gærfabrikker investeret i en opdateret kedelcentral med nye styretavler og PLC’er - sidstnævnte leveret af ABB.
Første big data-projekt
Jack Dominos næste projekt bliver nye køletårne, der via brugen af for eksempel eksterne vejrdata fra DMI skal optimere processen. Blandt andet ved i højere grad at kunne planlægge kølelagre efter vejrforholdene.
- Vi vil gerne blive endnu bedre til at forholde os til omgivelserne, fx vejrsituationen. Hvis der er meget fugtigt vejr, er det nødvendigt at tørre luften inden den bruges til gærtørreprocesserne, forklarer Jack Domino. De nye køletårne bliver installeret til sommer og vil indeholde en række ABB-komponenter, fx controllere og motorer.
- Det bliver vores første rigtige big data-projekt. Og her bliver System 800xA på sin vis også hjernen i det hele, slutter den tekniske chef.
DE DANSKE GÆRFABRIKKER A/S
De Danske Gærfabrikker A/S udspringer af De Danske Spritfabrikker, som blev etableret i 1881. Helt frem til Danmarks tiltrædelse i EF i 1973 havde virksomheden monopol på at fremstille gær og spiritus i Danmark. Samme år byggede man den nuværende fabrik i Grenå. Virksomheden er i dag ejet af den canadiske fødevarevirksomhed Lallemand, der har hovedsæde i Montreal. Lallemand har 25 fabrikker over hele verden. De Danske Gærfabrikker producerer halvdelen af Lallemands vingær. 80 pct. af fabrikkens produktion går til eksport. Foruden fabrikken i Grenå ligger der en såkaldt blandingsfabrik i Fredericia. Her mikses de forskellige gærblandinger efter kundens ønsker.
Kilder: De Danske Gærfabrikker og Børsen
FÅ GRAM BLIVER TIL 100.000 KG GÆR
Hver gæring starter med ganske få gram gær, der opformeres i fire eller fem trin. Disse trin kaldes fedbatch-fermenteringer, hvor næringen tilsættes kontinuerligt til fermentoren. Hvert trin tager 16-20 timer. De få gram, der var startmaterialet, bliver i løbet af én uge til over 100.000 kg pakkegær, svarende til to millioner 50-grams pakker. Den flydende gær fyldes enten direkte på tankvogne og køres ud til industrikunderne eller forarbejdes til pakker til detailhandlen.
Kilde: www.danskgaer.dk
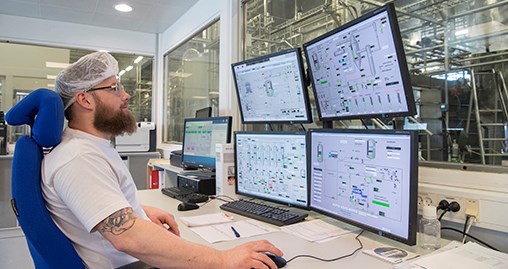