INSTANT ACCESS TO PRODUCT DATA
In compliance with European Union Ecodesign requirements, ABB has introduced a QR code-based digital platform designed to provide easy access to information regarding ABB products.
Thanks to the new platform, technicians, commissioning engineers, customers and distribution partners can now use a handheld device such as a mobile phone to access a world of information from their ABB drives, motors and PLCs by simply scanning a device’s QR code. The key is ABB Access, a responsive web application that links users to product-specific information, such as manuals, installation guides, and step-by-step instructions regarding commissioning and troubleshooting. The responsive web application also allows users to rapidly and easily reach expert support from ABB to report and solve problems on-site.
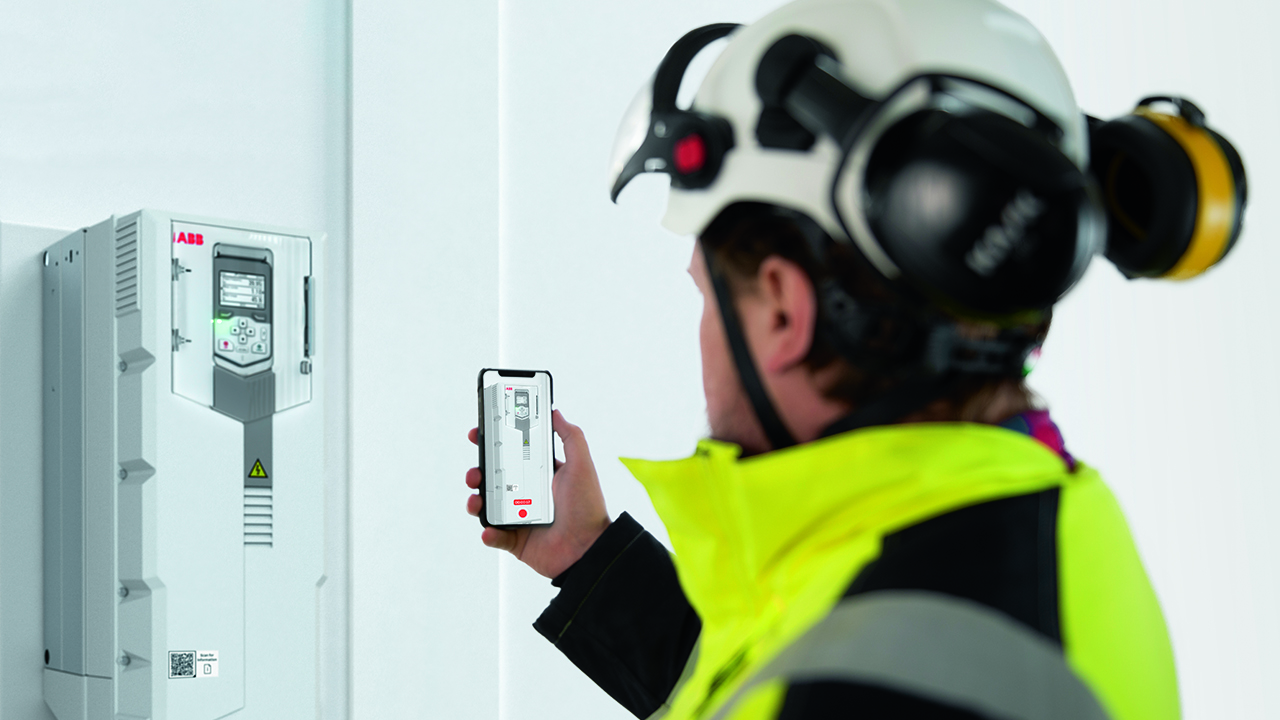
The result is faster troubleshooting, which results in higher uptime and lower downtime, as well as a unified user experience across a range of ABB products. As the web application facilitates self-service, troubleshooting can be performed by any user with basic knowledge, thus allowing more bandwidth for experts to handle challenging issues.
ABB Access architecture is based on a representational state transfer application programming interface (REST API) and microservice architecture policies in which data is communicated using frontend, backend and service layers. The platform draws data from ABB-approved data service providers, but, in compliance with standard security policies and principles, does not store any data. Instead, ABB Access uses an Auto ID redirection feature to access content from different products through its QR code scan feature.
Future enhancements of the web application will cover additional ABB products and will provide a wider range of information, including product maintenance history, warranty information, and additional information for special access users.
ABB Access complies with DIN SPEC standard 91406:2019-12, thus making it easier for OEMs and end users to read QR codes using commercially available hardware and software.
FAST, ACCURATE NATURAL GAS QUALITY MONITORING
Natural gas producers and distribution network operators are constantly on the lookout for excessive levels of contaminants in their gas streams. Monitored substances include water (H₂O), hydrogen sulfide (H₂S) and carbon dioxide (CO₂). Elevated levels of these substances can lead to accelerated infrastructure deterioration and even critical failures. In view of these risks, ABB has developed the GLA533-NG Sensi+™, an instrument based on a unique laser absorption technology called Off-Axis Integrated Cavity Output Spectroscopy (OA-ICOS) that is able to simultaneously monitor three types of contaminants in natural gas.
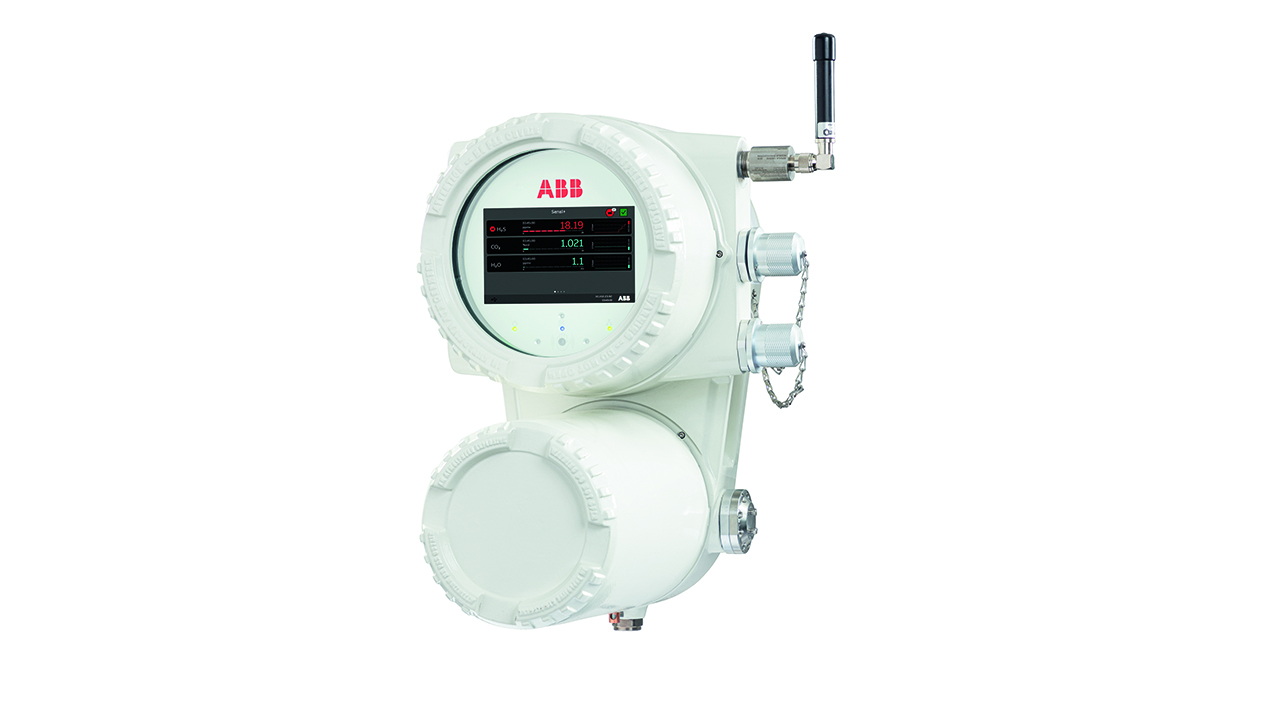
Patented by ABB, OA-ICOS, represents the latest advance in tunable diode laser absorption spectroscopy and delivers superior performance and reliability, yet is orders-of-magnitude less sensitive to internal alignment of components and to variations in local temperature and pressure than other methods. As a result, OA-ICOS is ideal for use in industrial instruments for even the most demanding applications in remote and/or hazardous locations.
Integrated in a customized explosion-proof enclosure, ABB’s GLA533-NG Sensi+ instrument is compact yet ensures ease of assembly and service. The modular character of the instrument’s gas manifold eliminates all internal piping, allowing critical components to be swapped rapidly without the need of special tools or advanced training. The instrument also benefits from a new ICOS electronic platform that offers a level for accuracy, precision and stability that provide outstanding measurement performance while minimizing cost of operation.
Among the many advantages of Sensi+, users will find the latest in cyber security, an excellent user interface, data exportability, and easy software upgradability. The instrument is designed to maximize response time while lowering the cost of ownership.
MINING THE BENEFITS OF AUTOMATED EV CHARGING
Mining environments are routinely referred to as rugged, harsh, or challenging. They are also places where safety must be maximized and human exposure minimized. With this in mind, ABB has developed a pilot version of an automated charging system that can be used by any electric haul truck without human intervention. Fast, flexible, and fully automated, the solution provides the highest power available on today’s market, thus minimizing mobile asset downtime. Known as eMine™ FastCharge, the system can be remotely monitored and controlled to optimize the charging process and energy usage in real time, hence reducing an operation’s environmental impact while improving its productivity.
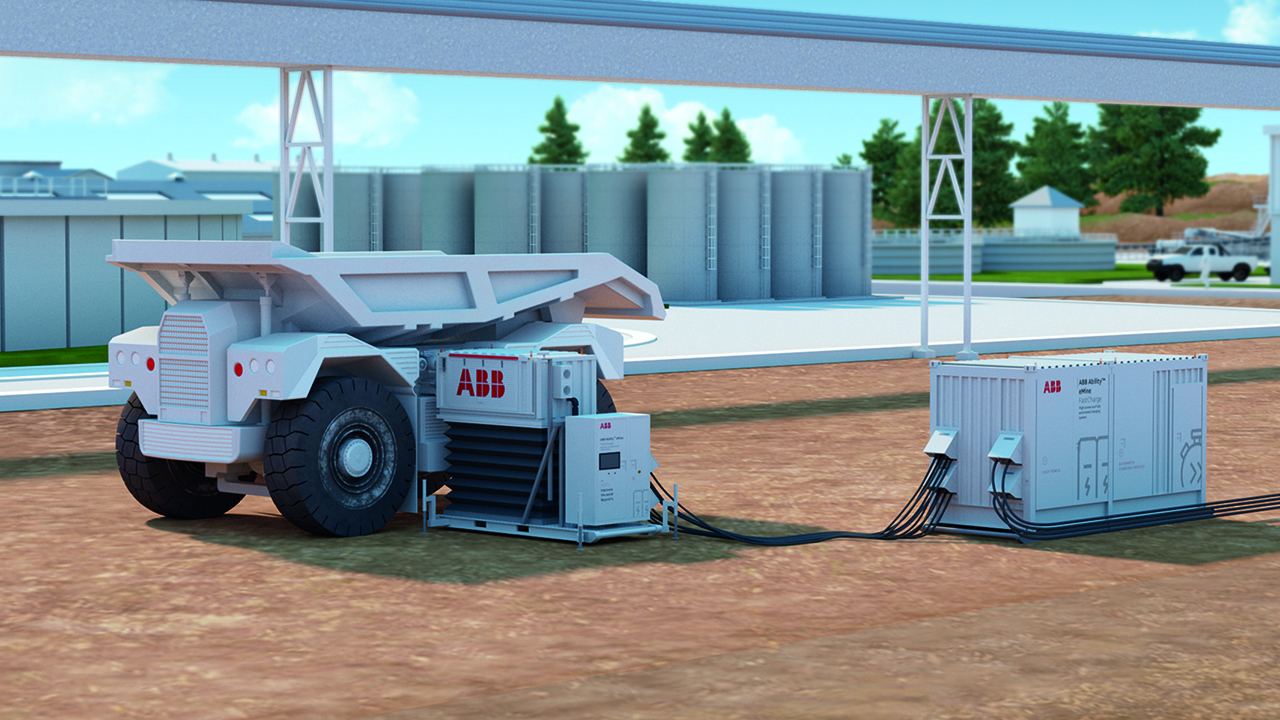
Based on widely adopted and open automotive industry standards that are interoperable and BEV OEM agnostic, eMine™ FastCharge does not require complex installation, thus lowering infrastructure costs and optimizing CAPEX/OPEX. Indeed, the entire charging station and its modules can be located separately, allowing the solution to seamlessly adapt as a mine’s configuration and requirements evolve.
Once up and running, the solution’s charging process is enhanced by a vehicle recognition camera system designed for maximum safety throughout the operation. Modular in design, eMine™ FastCharge’s building block configuration makes it easy to adapt to a mine’s operational and infrastructure needs, while making it future-ready for higher charging powers.
Thanks to an enclosure specifically designed to prevent ingress from dust and dirt, the solution is ready-made for the harshest environmental conditions prevailing in mining.
ABB ABILITY™ CYBER SECURITY WORKPLACE
With their complex IT and operational technology (OT) infrastructures, industrial plants can pose significant cyber security challenges.
Plant operators are, however, well aware of the risk from cyber attacks and usually implement a cyber security software solution for each system in the plant. However, because these solutions are typically from different vendors, maintaining them is not easy and any lapses can open the door to cyber attackers.
What is needed is a way to simplify security by consolidating tools, automating risk detection and remediating risks sooner. This is exactly what ABB Ability Cyber Security Workplace does.
Data from ABB and third-party cyber security solutions is collected by ABB Ability Cyber Security Workplace and forwarded to a consolidating native application, which presents it on a simple user interface. Operators can then monitor the status of all their security controls, perform maintenance activities to increase resilience and receive alerts with actionable insights to remediate threats and reduce risks.
Image currently unavailable
Image currently unavailable
Image currently unavailable
Image currently unavailable
Image currently unavailable
Image currently unavailable
Inbuilt risk root-cause analysis with remediation procedures evaluates any issue and suggests the steps required to fix it. Such inbuilt intelligence reduces the expertise needed to maintain cyber control systems. Further, these step-by-step guides cut remediation times, thus reducing operating costs and shortening the length of time the issue is present in the plant.
Moreover, ABB Ability Cyber Security Workplace installs patches against known exploits as quickly as they become available. Backup management is also included, as is the ability to isolate particular OT and IT environments to protect them from external intrusions. There is also a cyber asset inventory facility that monitors all the traffic on the network in real time, lists all assets based on an analysis of the traffic and informs users about newly added assets.
For more information, see: www.abb.com/cybersecurity/workplace
NEW DRIVE CONTROL PLATFORM IS BUILT FOR A DIGITAL FUTURE
Electric drives have come a long way since the days when their sole purpose was to deliver power from source to consumer. For instance, the growing computational performance of the processing units in today’s drives can be used to collect and analyze a steadily increasing quantity of information from the systems they are connected to. This ranges from more accurate estimates of torque and load characteristics to detailed information regarding the electrical grid.
However, as more and more interfaces are opened up to enable connectivity features, cyber security is becoming a key factor. With this in mind, ABB is about to introduce a next generation control platform for all its premium drives. The platform has been designed from the ground up to support critical security features such as authenticity and encryption of firmware, files, and applications.

The new platform is backwards compatible with ABB’s current generation of drives, making its introduction simple and familiar. To further enhance security and performance, drives can now also be equipped with an edge gateway capable of securely connecting to cloud backends and performing local analytics or process optimization from data collected from a drive or surrounding sensors.
The security features and high performance of ABB’s new control platform can also be harnessed by partners and customers. For instance, it is now possible for the first time to allow direct extension of the drive firmware via a software development kit. The kit allows development of latency-free applications directly in the drive using familiar technologies such as Matlab Simulink or even C++ programming. The applications are secured via authentication and encryption and utilize the latest hardware technologies to isolate them from the core firmware.
FASTER, EASIER AND BETTER WITH HIGH SPEED ALIGNMENT
With industry robots expected to perform ever more advanced tasks and interact with increasingly varied environments, it is essential to boost their performance as well as achieve rapid deployment and cycle times: In other words, the speed and accuracy of robots are essential. Following investigation of the challenges faced on high-precision assembly lines, ABB responded by offering its High Speed Alignment software.
In contrast to the conventional look-then-move approach, High Speed Alignment relies on sensors for an adaptive vision approach to achieve high accuracy and short cycle time, simultaneously. Thanks to the sensors and advanced motion control algorithm, the system controls the position of a robot’s device, or tool, relative to the workpiece in real-time. High Speed Alignment not only reduces the average cycle time by 70 percent, from ~5.6 s to ~1.7 s, it increases accuracy from 20 μ to 10 μ, or by 50 percent.

By paralleling the development of technical readiness prototypes and in-house customer cases with validation through real-world pilot studies, ABB achieved rapid market readiness. High Speed Alignment is the first software package in the market to provide visual servoing technology for 6-axis and 4-axis robots.
The inclusion of an auto-tuning feature, which automatically calculates the time delay of sensors, filter buffer length, control gain, delay of robot and dead zones etc., allows expert- and novice users alike to operate the system and reach their alignment goals. Ease of commissioning is ensured thanks to auto-calibration and tuning: Deployment time is reduced from an entire shift to just one hour.
Designed for the segment of the electronics industry that uses robotic alignment for high precision assembly and pick and place tasks, High Speed Alignment has many other potential applications, eg, consumer segments and service robots (CSSR), auto industry/tier 1, etc. In all these cases, the software ensures fast cycling time and phenomenal accuracy for better performance.
AUTOMATIC GENERATION OF COLLISION-FREE PROGRAMS
Boxes are stacking up, space is tight. Time is short. Wouldn’t it be nice to have a robot that could just be told what to do without any ifs, ands, or buts? In view of the fact that the integration and programming of robots represent a major part of any company’s investment in automation, ABB has introduced an innovation that allows its RobotStudio tool to automatically generate programs that guarantee collision-free motion of robots in a workspace.
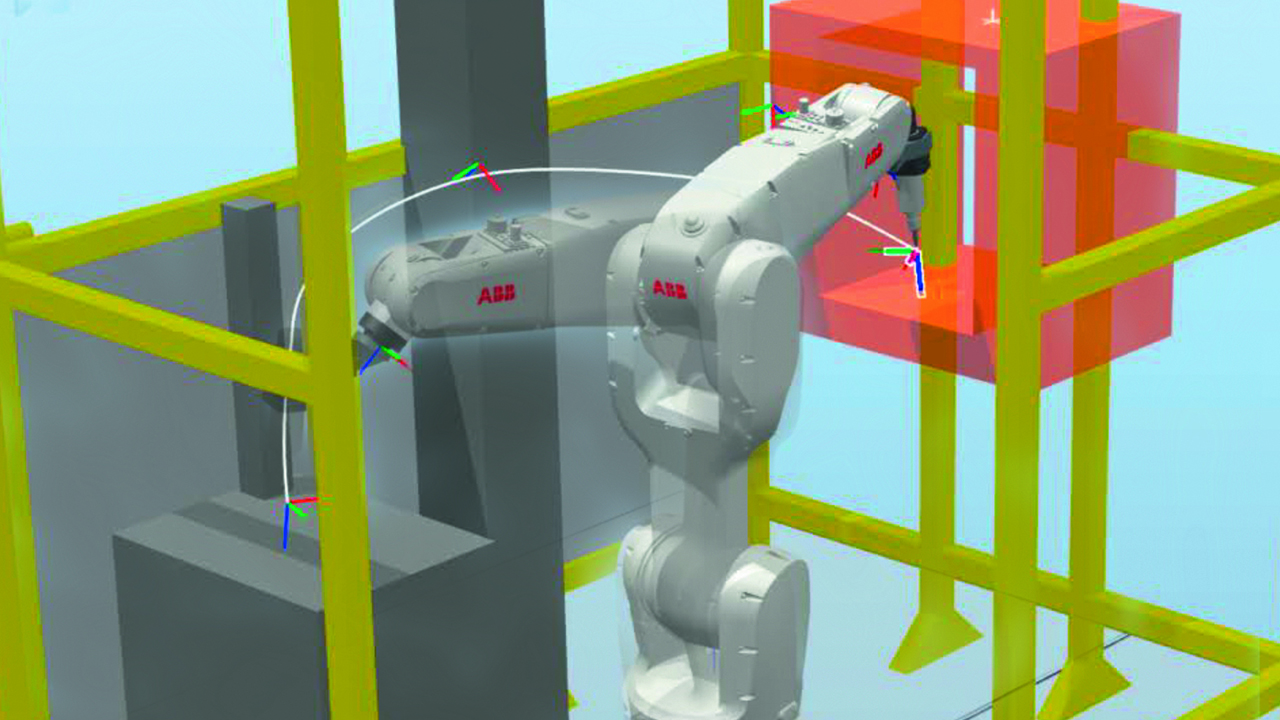
Automatically generated programs result in smoother and shorter movements compared to what an average user can achieve and require orders of magnitude less time to program. In addition, the resulting movement paths provide faster motion time and often reduce energy consumption.
In a preliminary internal study, an intermediate-level programmer spent up to 20 minutes to program a collision-free motion for a robot in a cluttered environment, while automatic generation needed only seconds.
RobotStudio’s innovation is the product of a combination of open source and in-house software, together with the virtual world in the tool itself. All in all, the innovation opens the door to a transformation of robotics in which systems become easier to use for non-experts.
TWO NEW FAMILIES OF LARGE ROBOTS
ABB has added two new robot families to its portfolio of large robots. Based on a new modular platform design, the IRB 5710 and 5720 are up to 25 percent faster than other large robots. The robots are more compact and robust, offer integrated process cabling, with higher uptime for multiple applications, including electric vehicle manufacturing.
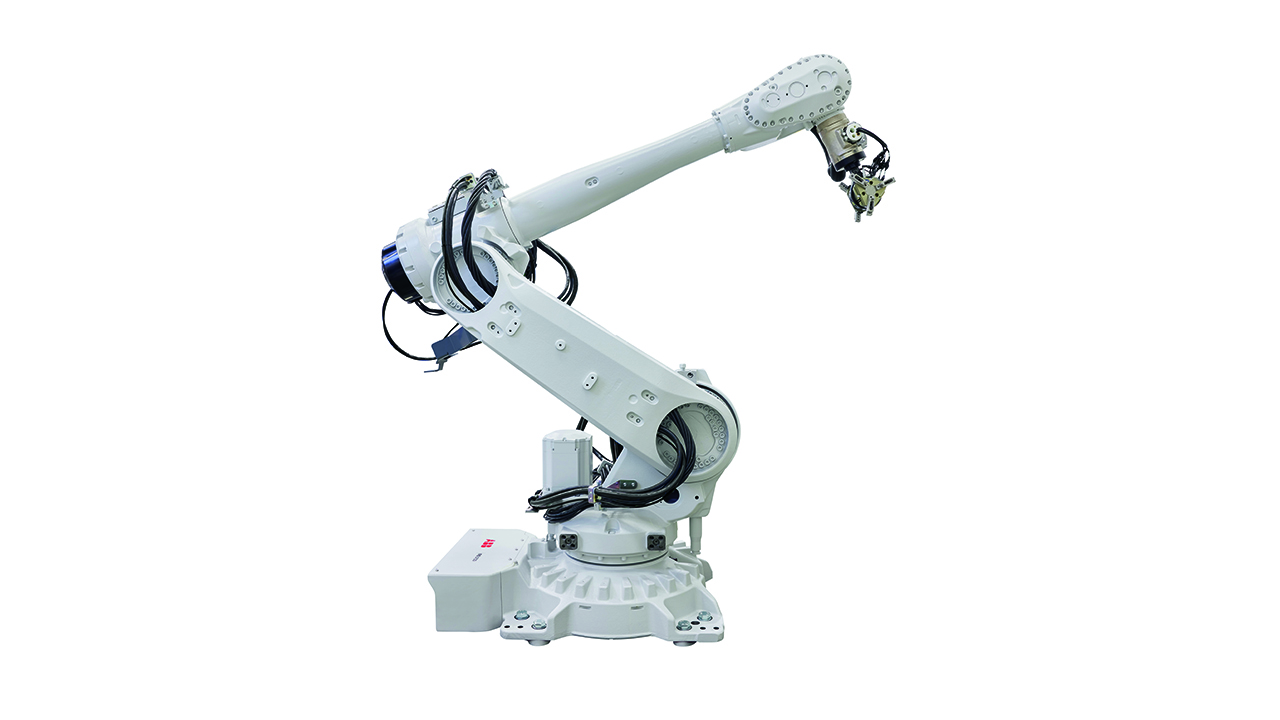
The robot families are suitable for a wide range of production tasks, including materials and parts handling, machine tending and assembly, and high-precision assembly. All variants have multiple mounting options and can operate hanging upside down. Payload options range from 70 kg to 180 kg and reaches from 2.3 m to 3 m.
The robots’ platform includes a new generation of motors and compact gearboxes. The former, together with smart brake release technology, enable reduced energy consumption.
Both robot families are powered by ABB’s new OmniCore™ controller V250XT. Featuring ABB’s TrueMove and QuickMove motion control technology, the OmniCore V250XT controller enables the IRB 5710 and IRB 5720 to offer class-leading speed and excellent position (≤0.05 mm) and path repeatability.
SUPPORTING THE SHIPPING INDUSTRY WITH OVERSEA
Bulit on ABB’s industrial software platform, ABB Ability™ Genix, Oversea is being developed by ABB and Wallenius Marine. This solution is being customized for the shipping industry to improve a vessel’s operational sustainability, efficiency and safety. This is accomplished by providing ship operators with a scalable system and services for centralized support, providing a fleet support center as a service.
This groundbreaking comprehensive digital solution, designed by ship masters, chief engineers and remote support experts, focuses on three areas that influence operational performance: technical-, environmental- and voyage performance. Oversea Digital Solution collects, transforms, aggregates and contextualizes data, and visualizes it in an actionable way. Data is turned into insights and insights into actions that can be applied to a single vessel or an entire fleet, thanks to the Oversea Support Center.
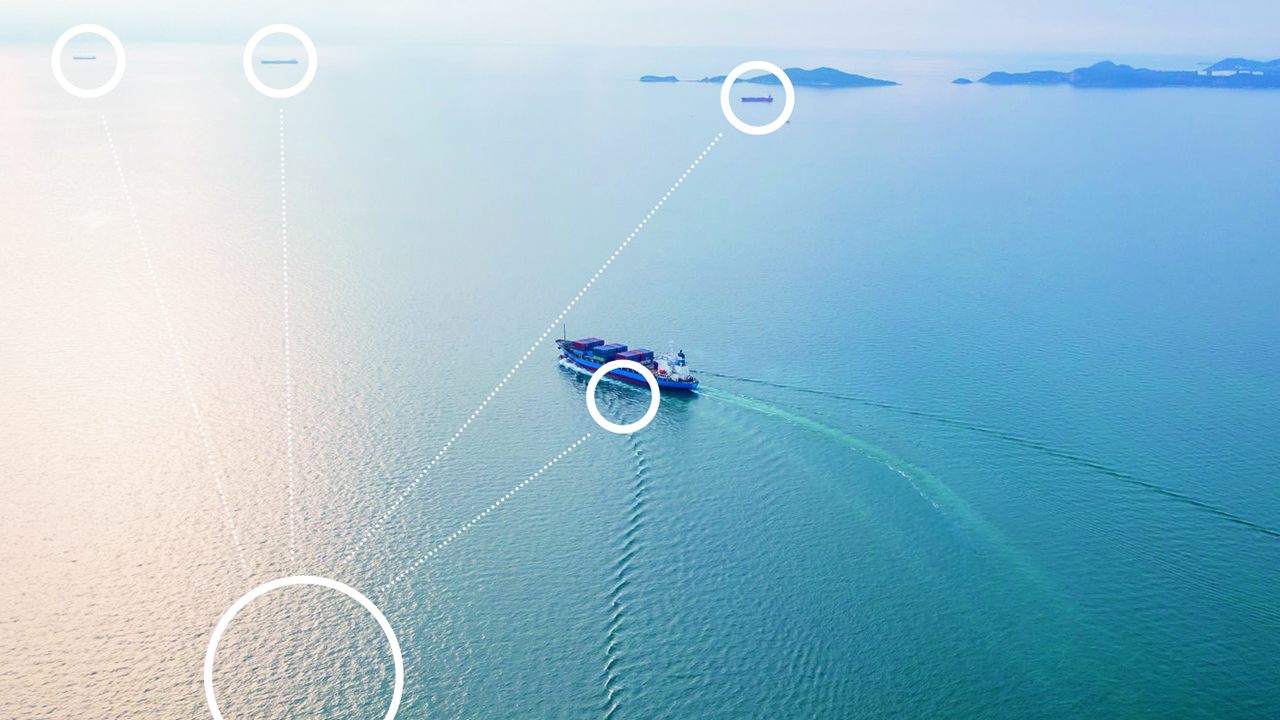
Collaborating with Wallenius Marine, ABB successfully completed an Oversea single vessel pilot study and is currently conducting an extended three-vessel pilot operation in a real-world environment. The user will test the functionalities that optimize technical performance, identify improvement areas using basic and advanced analytics, and ship-to-shore communication and workflows. The full-scope Oversea solution, under development, will include environmental- and voyage performance capabilities1).
Oversea’s underlying performance analysis enables a breakdown of the overall environmental performance into technical performance and voyage performance contributors; this enables the identification of under-performance and the appropriate corrective actions. Cutting-edge models, combining machine-learning and physics-based methods, are used to enable accurate results in all areas.
Ultimately, the Oversea Digital Solution will connect vessels, client office and the fleet support center to enable collaboration, provide insights and real-time recommendations to turn insights into actions. In this way, ABB and Wallenius Marine are enabling the shipping industry to achieve optimal operational performance while reducing emissions for a more efficient and sustainable future.
Footnote:
1) Two further releases of Oversea Digital Solution are planned for 2023.
ABB ABILITY™ SMART MASTER MAKES BETTER SERVICE DECISIONS FOR ABB MEASUREMENT DEVICES
The global installed base of field devices that perform sensing duties – such as flow meters, level meters, temperature sensors, pressure sensors and valve positioners – is enormous. ABB is a major supplier to this multi-billion dollar market.
Measurement accuracy, regulatory compliance, operational status and failure diagnosis and prediction are critical aspects of a field device’s performance. To manage these aspects in such a vast installed base, what is needed is a comprehensive asset performance management platform.
The ABB Ability Smart Master is just such a platform, designed specifically to cater to large installed bases of field devices.

Based on a prescribed schedule, Smart Master collects data remotely from field devices for condition monitoring purposes. Device health is verified and the device NAMUR status 1) is read to help the customer obtain an installed base overview. This knowledge enables ABB service-assisted clients and self-service customers to plan service operations, spare part orders and device replacement. If there is a pattern of device failures, a calendar view analysis and an analytical report provide more insight into the failure scenarios.
Smart Master provides a three-tier solution:
• On-premise: remote monitoring support. Collected data is managed within the customer network.
• Dedicated cloud: dedicated link to each customer for monitoring. Collected data is managed securely in ABB’s dedicated infrastructure for customers.
• Shared cloud: global link to all customers for monitoring. Collected data is managed securely in ABB’s common cloud infrastructure for all customers.
With remote access, costs are lowered as remote experts can carry out pre-compliance activities and, later, routine visits to site by an engineer are reduced.
Often, measurement devices are deployed in places where connection is difficult. In such cases, field device integration (FDI) technology connects the devices without additional wiring or disturbing operations. Smart Master can also connect via 3G/4G and NB-IoT.
Footnote
1) NAMUR is an international user association for automation technology and digitalization, and creator of associated standards.
ABB ROLLS OUT SERVO DRIVES R&D HUB IN NANJING
ABB servo products provide an extensive range of motion and machine control solutions for diverse industrial applications, such as packaging, textiles, printing, food and beverage, electronics and electrical. Such solutions help system integrators, OEMs and machine builders reduce energy consumption, increase their equipment uptime, and thus minimize maintenance costs while increasing productivity.
With a view to offering ever-more advanced servo products, as well as providing complete and more valuable motion control system solutions for the market, ABB opened a new R&D hub for servo products in Nanjing, China in 2020.
Image currently unavailable
Image currently unavailable
Image currently unavailable
Image currently unavailable
Image currently unavailable
Image currently unavailable
Image currently unavailable
Image currently unavailable
Image currently unavailable
The new R&D hub is a significant milestone for ABB on the road to becoming a key player in China’s growing servo business market. Its strategic significance for ABB and its customers is that the business will be close to local customers in the biggest market in China and will thus be able to provide faster delivery and response times than in the past.
What is more, by combining its new servo product line with research and development, the hub will be able to rapidly funnel customer input from ideas to implementation – a capability that can pay significant dividends in terms of recruiting from local universities and local competitors.
Since its inception, the R&D hub has expanded from 14 employees to 40 and has grown to offer services in areas such as hardware, firmware, testing and product management. The hub’s first products are expected to be released by the end of 2022.
BORDLINE® ESS MODULAR ENERGY STORAGE
Low-carbon drive systems with an embedded onboard energy storage system (ESS) are becoming an integral part of the rail industry’s transition to sustainable mobility. The increased adoption of these systems not only helps to decarbonize transport but also provides a variety of other benefits, such as lower total cost of ownership, more operational flexibility and improved vehicle performance.
Traction batteries for mass transportation must deliver the required performance with maximum reliability over long service periods. To address this market need, ABB has developed a portfolio of high-performance products called BORDLINE ESS.
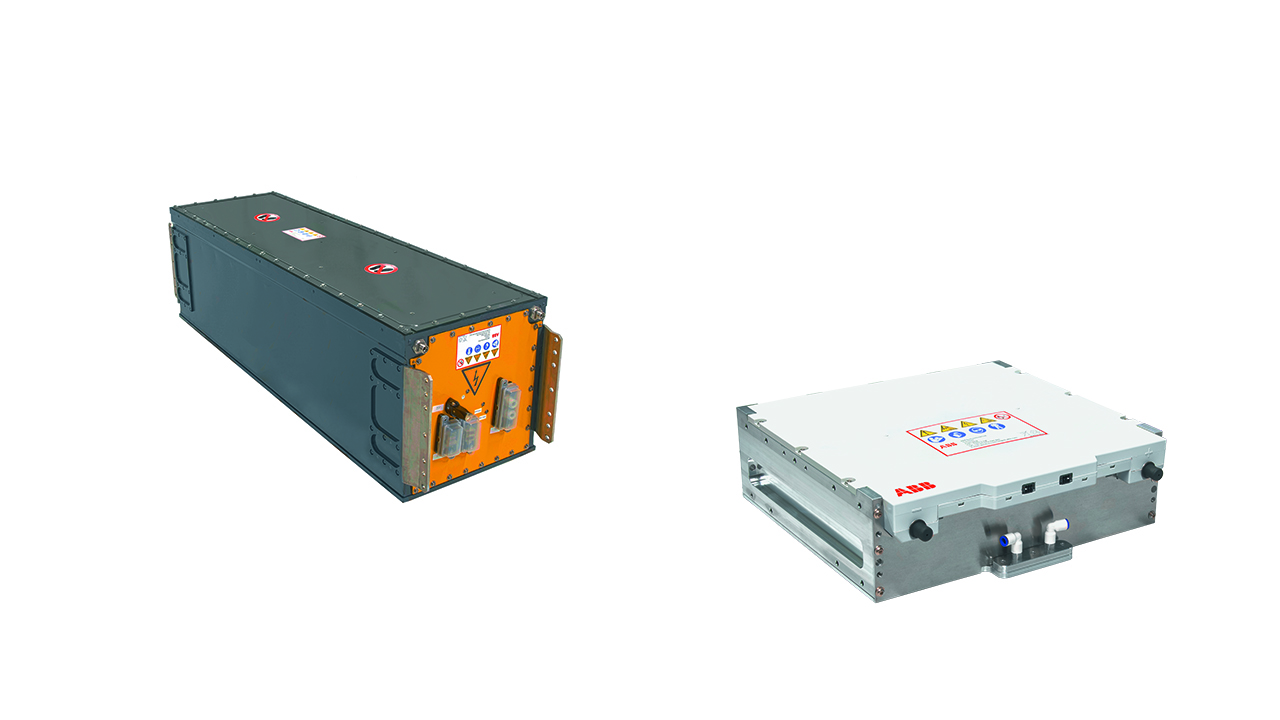
BORDLINE ESS battery packs have a modular architecture, which allows standardization at the subsystem level without compromising on the required flexibility at the product level. The modular design ensures easy scalability in terms of voltage and installed energy with a minimal set of module variants.
At the core of each battery pack are modules equipped with high-power prismatic lithium-ion cells that incorporate a lithium titanium oxide (LTO) anode. The Bordline ESS offers a high level of inherent safety (such as tolerance to abuse), a long cycle life, fast charging capability, excellent lifetime even at 35 °C and good low-temperature performance.
ABB has successfully delivered, or is in the process of delivering, high performance traction batteries to more than 700 vehicles with references in railway rolling stock, e-bus, trolleybus and mining vehicle segments.
RESEARCH TOWARDS AUTONOMOUS SOLUTIONS AT SEA
New technologies bring opportunities to look at familiar things with new perspectives. Consider ship navigation; a central task in navigation is lookout, keeping a close eye on the ship’s surroundings to be able to warn of and avoid any potential obstacles or danger. Another important task for navigation is determining distance to obstacles. Known as water clearance , this is particularly important when maneuvering in harbor or confined waters. These are both tasks that cameras and autonomous systems can very successfully help support the bridge crew with. So how does ABB go about developing such a system?
ABB is conducting research on vision systems for marine applications. Specifically, making added value from the information gathered from the myriad of cameras already installed onboard. Leveraging machine perception changes the way we look at things and can enable safer, more
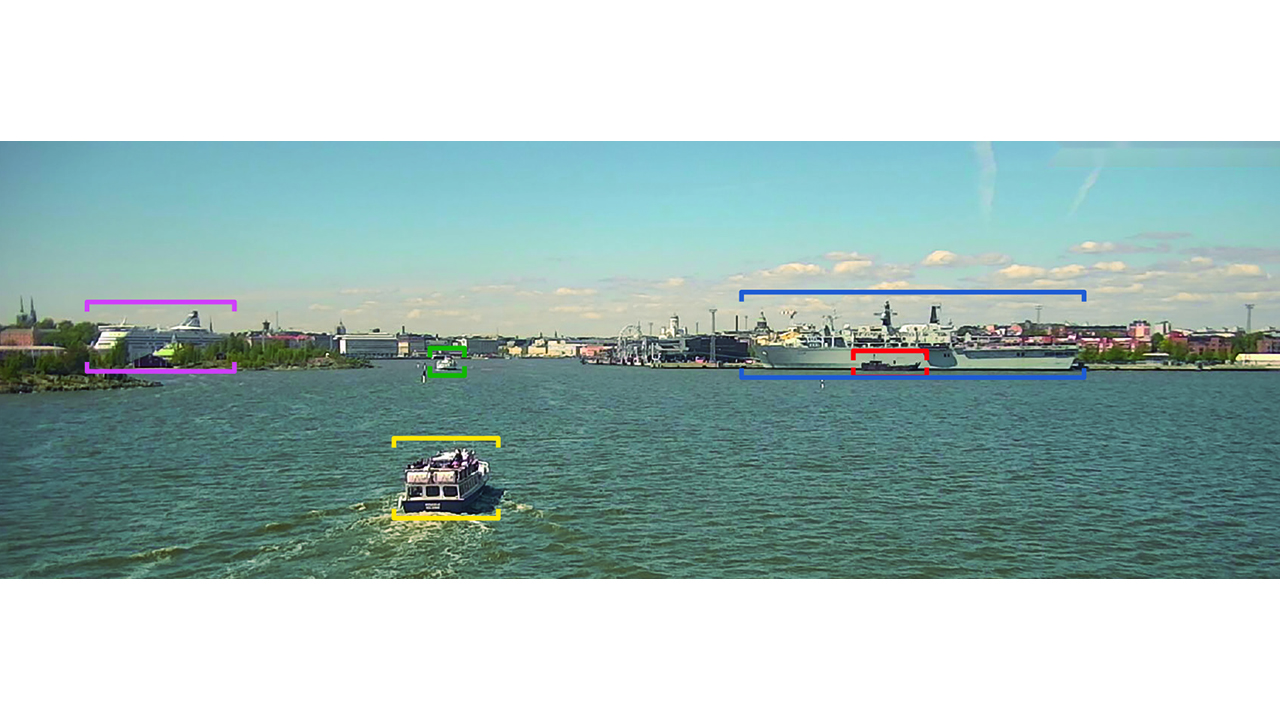
efficient, and more autonomous maritime operations. A system of cameras and machine perception algorithms can support the human lookout/ bridge crew by providing continuous, relentless, lookout, and accurate water clearance measurements, as well as covering blind spots not visible from the bridge. A camera-based system will also be able to detect small, non-metallic obstacles that might go unnoticed to radar.
The key technologies that enable machines to process image streams are object detection and semantic segmentation. The goal of object detection is to detect all instances of objects from one or more classes. To do this successfully the machine has to interpret every pixel of an image to the right class. The state-of-the-art of these technologies are models based on artificial neural networks.
ABB’s research is central to the development of more autonomous solutions for vessels, such as ABB Ability™ Marine Pilot Vision, which is part of ABB’s autonomous solutions portfolio for ships. The research shows the potential of vision-based solutions, in this case a monocular-vison system, and their benefits when integrated into the suite of marine safety systems.
A full article in an upcoming issue of ABB Review will dive deeper into the development of this technology, explaining how the vision-based system understands its surroundings and ultimately helps seafarers navigate more safely.
PERMANENT MAGNET TECHNOLOGY: THE ENERGY-EFFICIENT INNOVATION FOR SHAFT GENERATORS
Producing electrical power from a generator mounted directly onto a marine vessel’s main propulsion shaft is generally more efficient than running auxiliary gensets. To maximize such a shaft generator’s advantages, and especially to boost energy efficiency, its rotor can be designed with permanent magnets (PMs) in place of conventional rotor windings. Eliminating rotor windings and associated equipment removes factors that account for much of a generator’s total energy losses. Compared to conventional generators, the PM type achieves higher power density and efficiency at a smaller size. Energy savings are significant at full load but even greater (as much as 10 percent) in partial-load regimes (where vessels usually operate) compared to induction type shaft generators. Adding a variable-speed drive (VSD) enables the propulsion plant to run at the most efficient operation point.
For shipbuilders and system integrators, the beauty of PM shaft generators is their smaller and lighter construction, which enables quick and easy installation.

For owners and operators, there are savings in fuel consumption and maintenance expenses: Compared to previous solutions, a PM shaft generator should immediately cut fuel costs by up to 4 percent. Emissions are lowered, too and because a PM rotor has fewer components, maintenance and downtime costs are reduced.
PM shaft generators offer a choice of operating modes, bringing further flexibility, redundancy and safety. The generator mode – the one discussed so far – is called Power Take Off (PTO) mode. In Power Take In (PTI) mode, the generator works instead as a motor – delivering a temporary power boost to the propulsion shaft, which may allow downsizing of the main engine. Further, a Power Take Home (PTH) mode allows a vessel to return safely to port under electric power if the main engine fails.
ABB’s newest PM shaft generator, the AMZ 1400, will be fitted to a fleet of 12 Himalaya Shipping bulk carriers. The package includes ABB ACS880 VSDs, which will optimize the vessels’ performance in response to variations in speed, bulk freight weight and electrical load.
SYNCHRONOUS CONDENSERS PROVIDE INERTIA FOR GRID STABILIZATION
As renewable energy sources proliferate in power grids, the number of high-inertia generators, traditionally provided by fossil-fuel plants, decreases, both in actual numbers and as a share of the total power generating capacity. This reduction can have severe effects: Inertia is vital for compensating for sudden changes in the grid – such as when a generator trips and goes offline – to ensure grid frequency remains within tightly controlled limits.
How can a power grid’s inertia be maintained in the face of the removal of high-inertia generators? The answer lies with synchronous condensers.
A synchronous condenser is a large rotating device that stores physical inertia to deliver instantaneous support for grids, enabling them to maintain stability irrespective of the upstream network voltage or frequency.
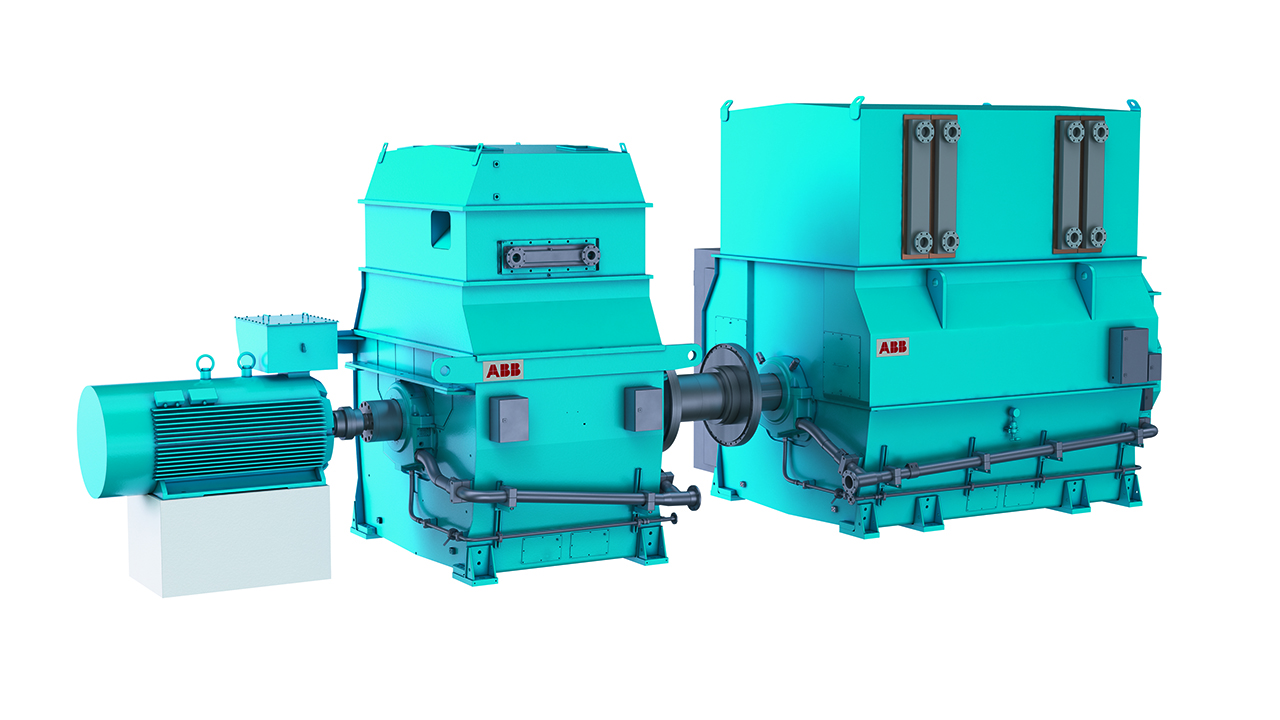
Fifty or more years ago, synchronous condensers were used widely but are now much less common as their former primary function – reactive power compensation – is now handled by a diversity of other solutions. However, this equipment cannot provide grid stability as well as a synchronous condenser, whose capabilities extend beyond reactive power compensation.
When additional inertia is needed in a system, an effective and economical approach is to add a flywheel to an existing synchronous condenser. This measure improves the potential to reduce losses compared to fulfilling the inertia requirement by installing a larger synchronous condenser.
ABB has chosen to upgrade its synchronous condenser flywheel with a patent-pending integrated safety device rather than relying on external protective functions.
The networks of the future will require decentralized solutions to maintain grid stability and resilience. Synchronous condensers are a well-proven solution that can be activated almost instantaneously to strengthen weak or compromised networks, even in remote areas.
For more information, see the article “Grid support” on pages 66-71 of this edition of ABB Review.