ABB aplicó los avances en software numérico a la tecnología de fabricación aditiva para crear soluciones potentes para el proceso de impresión 3D que optimizan y mejoran el diseño de componentes esenciales, a la vez que reducen los costes generales.
Lukasz Matysiak, Tomasz Nowak, Robert Sekula, Dariusz Bednarowski ABB Corporate Research Krakow, Poland, lukasz.matysiak@pl.abb.com, tomasz.nowak@pl.abb.com, robert.sekula@pl.abb.com, ariusz.bednarowski@pl.abb.com; Frederic Tholence, Erik X. Johansson ABB Corporate Research Västerås, Sweden, frederic.tholence@se.abb.com, erik.x.johansson@se.abb.com; Peter Schuster ABB Technology Center Uster, Switzerland, peter.schuster@ch.abb.com
En la última década se ha avanzado mucho enla tecnología de fabricación aditiva (AM) o impresión 3D: la fabricación de piezas por adición de material en un proceso de capa por capa [1]. Algunos procesos de AM fabrican piezas metálicas o poliméricas; utilizan diferentes combinaciones de formas de materiales ya existentes, ofrecen distintos materiales y emplean distintas fuentes de calor. La familia de procesos de extrusión de materiales (Modelado por Deposición Fundida o Fabricación de Filamentos Fundidos) es un ejemplo importante. Tomando como base la forma original del filamento, los objetos se construyen mediante la deposición selectiva de un polímero termoplástico fundido. Esto contrasta con los procesos basados en polvo (que utilizan polvo metálico o polimérico) en los que el polvo se extiende por la base del aparato antes de ser escaneado o se aplica directamente en la región afectada por el calor.
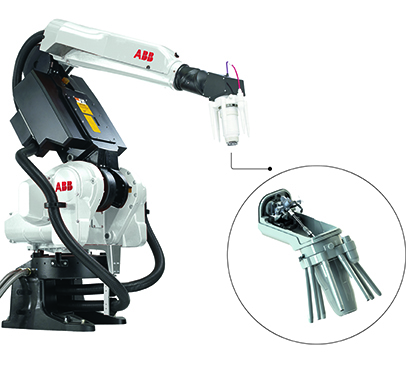
Gracias a estos avances, la AM proporciona a los fabricantes libertad de diseño y capacidad para construir (en impresión 3D) un conjunto compuesto de múltiples piezas integradas.
No obstante, los procesos intrínsecamente complejos plantean obstáculos que pueden impedir una aplicación más amplia de la AM. Por ejemplo, la geometría del producto y las estructuras de los materiales, que se definen durante el proceso de AM, plantean limitaciones complejas. Por otra parte, el propio proceso puede afectar al material depositado durante esta técnica de fabricación, según la cual una sola capa se "funde" sobre una capa anterior. Los efectos combinados de la rápida solidificación, el enfriamiento direccional y las transformaciones de fase inducidas por los ciclos térmicos repetidos pueden afectar negativamente a las microestructuras del material depositado. Además, es posible que las piezas fabricadas no cumplan los requisitos mecánicos debido a niveles de porosidad inaceptables. La naturaleza termomecánica del proceso puede dar lugar a imprecisiones dimensionales graves: el resultado de distorsiones y tensiones residuales inducidas térmicamente [2].
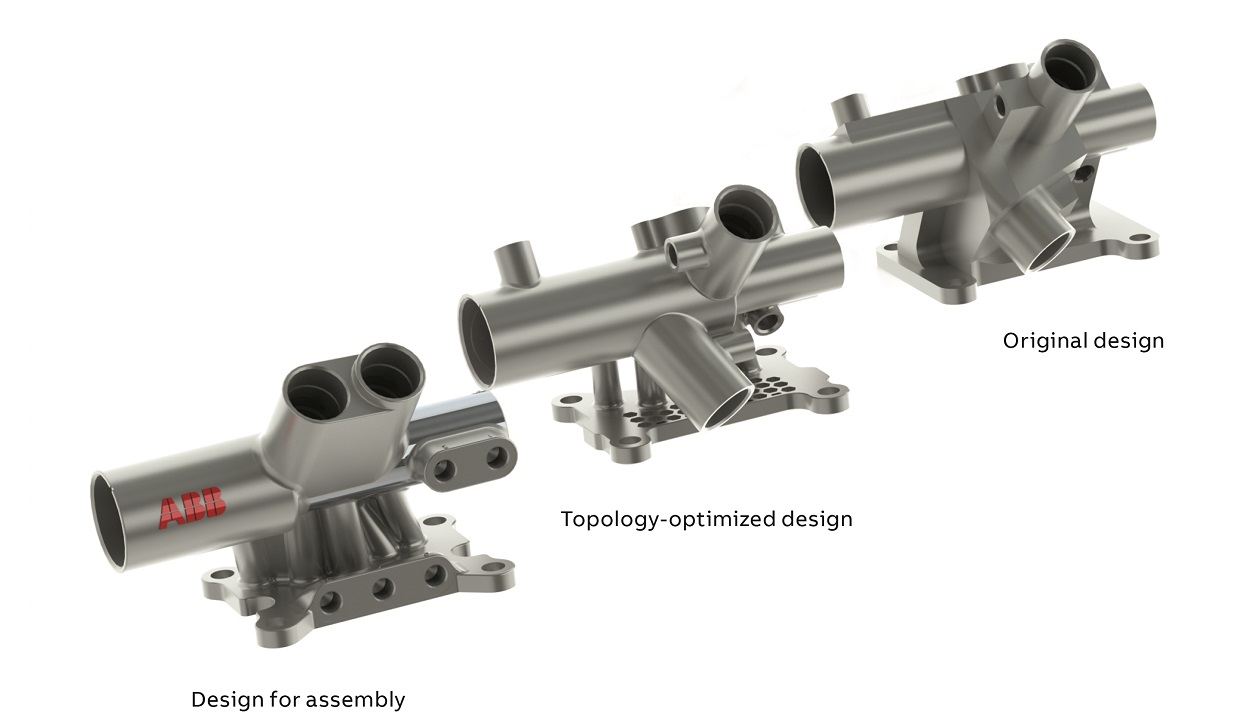
No es sorprendente que las herramientas de ingeniería numérica, por ejemplo, los paquetes de software de análisis de elementos finitos, revelen fenómenos físicos que son críticos. De este modo, los ingenieros pueden conocer el vínculo entre el diseño del producto, la configuración del proceso, la microestructura del material y las propiedades físicas de los productos impresos en 3D. Las herramientas numéricas también son muy eficaces en los métodos de optimización paramétrica y de topología, donde se trata de reducir el peso del componente y optimizar el tiempo de impresión.
Casos prácticos de ABB
ABB evaluó las simulaciones numéricas y herramientas de ingeniería en tres casos prácticos para establecer supuestos específicos en los que las aplicaciones AM ofrecen valor a los clientes, más allá de la ventaja de la libertad de diseño. Para ello, se abordaron los inconvenientes percibidos de la AM: largos tiempos de impresión y alto coste.
- Impresión 3D metálica de un conjunto colector de pintura.
- Optimización de la topología y la denominada fabricación híbrida de un demostrador de brazo robot.
- Herramientas basadas en AM para el moldeo por inyección.
Caso práctico del colector de pintura - impresión 3D metálica
En la robótica industrial, por ejemplo, en los robots depintura →1, las estructuras ligeras ahorrarían tiempo y coste y contribuirán a mejorar el tiempo de ciclo, la precisión, la carga útil y el consumo energético del robot. En particular, el módulo pulverizador de pintura situado en el extremo de un brazo robot de pintura se beneficiaría de una reducción de peso →1. Además, las técnicas de AM pueden ofrecer ventajas adicionales: facilidad de montaje, limpieza más fácil y mayor solidez de los componentes.
La función del colector de pintura es mezclar dos componentes de una pintura (resina y catalizador) justo antes de la pulverización →1.Tradicionalmente, el colector se fabrica a partir de un bloque de acero inoxidable mediante un mecanizado convencional CNC. Puesto que la parte interior del colector consta de una compleja red de tuberías, la producción del colector es costosa, requiere un largo plazo de tiempo y supone un importante nivel de materiales de desecho. En consecuencia, aproximadamente el 88% del bloque de acero inoxidable inicial se descarta.
Cualquier adición de material innecesaria en un componente AM aumentará el peso e incrementará el coste de la pieza final, por lo que es crucial imprimir estructuras ligeras. La optimización del peso suele conseguirse mediante la optimizaciónde la topología (TO). Inicialmente, se aplican cargas de servicio al componente. El motor de optimización obtiene la densidad de cada elemento que es necesaria para mantener la rigidez estructural del componente. El mapa de densidades resultante del componente puede utilizarse a continuación para fabricar una estructura biónica típica o una estructura reticular ligera.
ABB demostró con éxito que la AM es especialmente adecuada para fabricar este tipo de formas complejas. La versión más ligera del colector presenta características tanto biónicas como Honeycomb →2. El peso total se redujo en un espectacular 43 %, al tiempo que se conservaron la funcionalidad y la rigidez estructural.
A continuación, se rediseñó el colector para mejorar el proceso de impresión y facilitar el paso posterior de mecanizado CNC. Se utilizó un software informático específico para optimizar la orientación del componente durante el proceso deimpresión. Con el fin de mejorar la calidad y el coste de las piezas se evaluaron: el volumen de soporte (por ejemplo, material residual), el tiempo de impresión, la deformación, la cantidad y la facilidad de postprocesamiento y el número de piezas que encajan en una placa de construcción. El tiempo de impresión se redujo un 10 %, mientras que el volumen de soporte requerido se redujo en un extraordinario factor de seis.
A continuación, se modificó el diseño del colector para facilitar el montaje →2. A diferencia de las técnicas de fabricación tradicionales, que pueden limitar la forma de los canales internos a orificios rectos, la AM ofrece la posibilidad de fabricar canales curvos que se extienden libremente dentro de la estructura. El recorrido de los canales de aire podría entonces volver a trazarse libremente dentro del colector de manera que todas las válvulas del piloto de aire pudieran colocarse en el mismo lado del componente →3. El resultado es facilidad de montaje y un posterior mecanizado CNC más racional.
ABB empleó la técnica SLM para fabricar prototipos de esta nueva generación de colectores, lo que supuso una importante reducción del peso, mayor facilidad de montaje y una menor cantidad de materiales de desecho. El plazo de entrega de los componentes se redujo de tres meses a solo tres semanas. En general, este colector mejorado proporciona a los clientes de ABB un mejor diseño y pone a su disposición un rendimiento mejorado de sus robots.
Optimización de la topología de un brazo robot
Las principales ventajas de la tecnología AM (libertad de diseño, fácil fabricación de piezas complejas, impresión bajo demanda) se ven deterioradas durante la impresión 3D de los componentes de robots (por ejemplo, brazos de aluminio en los que hay un número limitado de materiales disponibles, pequeñas dimensiones de los componentes, alto coste de producción y largo tiempo de impresión). Por el contrario, los métodos clásicos, como la fundición, son muy eficientes y aplicables a una gama de componentes de dimensiones prácticamente ilimitadas. Por este motivo, ABB estudió una estrategia de fabricación híbrida. En primer lugar, el brazo inferior de un robot industrial se optimizó a nivel topológico [3,4], con el fin de discernir varias alternativas de diseño →4a,4b.
Image currently unavailable
Image currently unavailable
Image currently unavailable
Image currently unavailable
Image currently unavailable
Image currently unavailable
3a. Comparación de los canales interiores - diseño original. 3b. Comparación de los canales interiores - diseño de los componentes de montaje.
A partir de entonces, se fabricó el molde de arena mediante impresión 3D y a continuación se utilizó como herramienta en el posterior proceso de fabricación: fundición clásica. ABB desarrolló un concepto completamente nuevo del brazo robot inferior que supera las limitaciones anteriores de la tecnología AM.
Image currently unavailable
Image currently unavailable
Image currently unavailable
Image currently unavailable
Image currently unavailable
Image currently unavailable
Image currently unavailable
Image currently unavailable
Image currently unavailable
4a. Se muestran los resultados de varios conceptos de diseño. 4b. Simulación del proceso de llenado del molde. 4c. El demostrador resultante del brazo inferior de un robot industria.
El demostrador →4c fue el resultado de una combinación única de tres tecnologías diferentes: el diseño generativo, que ayuda a los ingenieros a proponer conceptos de formas libres; la fabricación aditiva, que fabrica el patrón (la herramienta) en lugar de la propia pieza; y la fundición de metal, que materializala idea del diseñador utilizando un molde impreso en 3D y una aleación metálica fuerte pero ligera.
De este modo, ABB demostró que puede ser más rentable fabricar una herramienta con tecnología AM y luego utilizar esta herramienta como ventaja durante los procesos de fabricación estándar.
Herramientas basadas en AM para el moldeo por inyección
La tecnología AM ha dado lugar a impresoras 3D de mayor resolución más rápidas y precisas que nunca, y al desarrollo de nuevos materiales para su uso en los procesos de inyección. En consecuencia, varios proveedores de AM propusieron la impresión directa en 3D de cavidades de moldeo por inyección [5,6], sin necesidad de un posterior mecanizado de las cavidades, es decir, listas para su adopción en un marco de molde metálico →5.
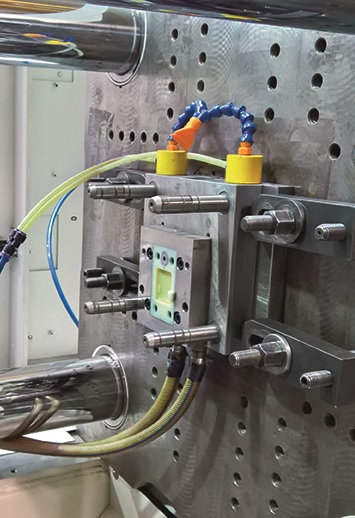
Las cavidades poliméricas de inyección impresas en 3D cuestan menos que las herramientas metálicas (generalmente un 50-70 % menos) y requieren una latencia mucho más corta (días). Lamentablemente, los moldes poliméricos impresos en 3D son más adecuados para trabajos de hasta 100 disparos (dependiendo del tipo de material y de la complejidad del molde) debido a las limitaciones tecnológicas actuales. Otras limitaciones incluyen: la gama de termoplásticos que pueden procesarse, el alto coste de la materia prima para la impresión 3D y el mayor tiempo de ciclo del moldeo por inyección (15 a 20 veces más que para las cavidades metálicas) gracias a la baja conductividad térmica de los polímeros utilizados para la impresión 3D. ABB propuso un enfoque completamente nuevo para superar estas limitaciones. La impresión en 3D se utiliza únicamente para fabricar una estructura de carcasa, que luego se llena con un material de mayor conductividad térmica. El espesor de la estructura de carcasa impresa en 3D es la consideración fundamentaldurante la fase de diseño cuando deben tenerse en cuenta las contradicciones de los requisitos: un espesor pequeño se asocia a un tiempo de ciclocorto mientras que un espesor grande asegura una buena estabilidad mecánica. Se evaluó el impacto del espesor de la carcasa en el tiempo de ciclo (eficiencia de enfriamiento) en la geometría mediante Ansys/Fluent →6.
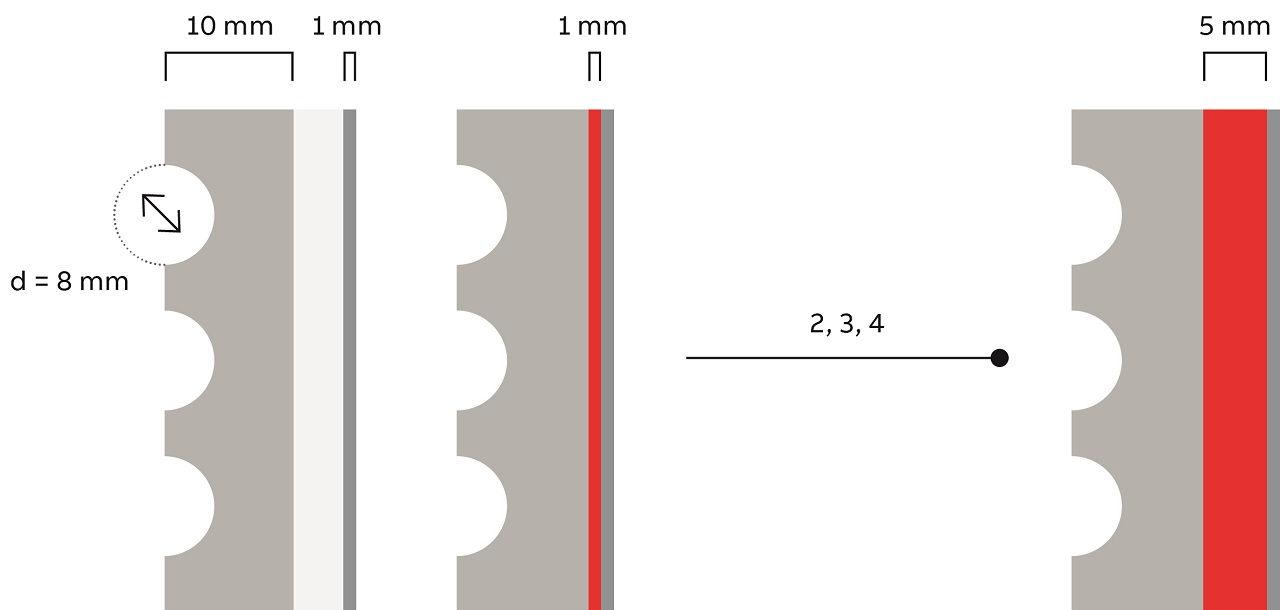
Se estudió el espesor tanto de la pared dela carcasa (de 1 a 5 mm) como de la estructura sólida (polímero y acero). Los resultados computacionales seleccionados de las temperaturas superficiales de las cavidades en los escenarios analizados durante el primer ciclo y los ciclos estables →7, muestran el extremo impacto que tiene el espesor de la carcasa en la eficiencia del enfriamiento, incluso durante el primer ciclo.
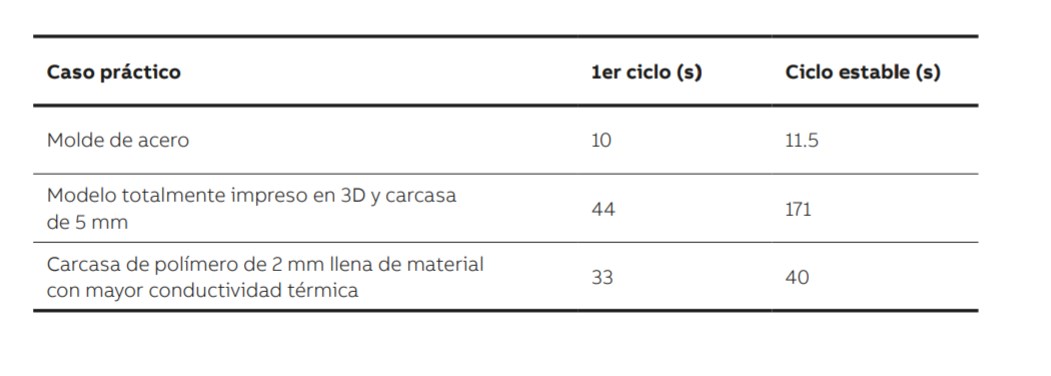
El tiempo de ciclo después de alcanzarcondiciones de procesamiento estables es aproximadamente 15 veces mayor para las cavidades depolímero sólido que para las cavidades de acero.Esta consideración final esencial y el diseño optimizado permiten reducir el tiempo de enfriamientoen un factor de cuatro a siete; esto se traduce en untiempo de ciclo que es solo de dos a tres veces máslargo que en el caso de los moldes de acero: unresultado excelente.
Perspectivas
La AM y todos sus beneficios tecnológicos están cambiando el modo de diseñar y fabricarlos productos. La AM ya es lo suficientemente madura como para competir con los procesos tradicionales de fabricación sustractiva o tecnologías de producción como el moldeo por inyección en términos de propiedades de materiales, dimensiones de geometrías, materiales y costes de procesos. Se espera que las empresas que desarrollan software de simulación, las máquinas AM y los proveedores de materiales sigan esforzándose para ofrecer a los clientes soluciones automatizadas que sean cada vez más fáciles de usar. Los clientes tendrán mayor libertad y flexibilidad en términos de geometría, lo que se traduce en estructuras ligeras y un excelente rendimiento mecánico en la integración funcional y en la consolidación de las piezas.
Actualmente, ABB está investigando otra tendencia, a saber, las simulaciones numéricas multifísicas del propio proceso de impresión; esto incluye interacciones termomecánicas entre las distintas partículas y capas del objeto impreso (de polvos metálicosy poliméricos). ABB presentará estos resultados desimulación cuando finalice las pruebas y los procedimientos intensivos de verificación.
Referencias
[1] Wohlers Report 2016, “3D Printing and Additive Manufacturing State of the Industry,” Wohlers Associates Inc. USA, 2016.
[2] B. Stucker, “Physics-Based Simulation: Accelerating Innovation in Additive Manufacturing.” 12th Intl. Conf. Additive Manufacturing and 3D Printing, Nottingham, UK, 2017.
[3] Y. Saadlaoui, J. Milan, J. Rossi, P. Chabrand, “Topology optimization and additive manufacturing: Comparison of conception methods using industrial codes.” J. Manufacturing Syst, vol. 43, Part 1, April 2017, pp. 178–186.
[4] M.K. Thompson, G. Moroni et.al., “Design for Additive Manufacturing: Trends, opportunities, considerations, and constraints.” Manufacturing Tech., vol. 65, Issue 2, 2016, pp. 737–760.
[5] R.A. Harris, H.A. Newlyn and P.M. Dickens, “Selection of mould design variables in direct stereolithography injection mould tooling.” Proc. Instit. Mech. Eng., Part B, J. Eng. Manufacture, vol 216 No. B4, 2002, pp. 499–505.
[6] G.V. Salmoria, F.V. Lafratta, M.M. Biava and P.Z. Ferreira, “Rapid manufacturing and rapid tooling of polymer miniaturized parts using Stereolithography”.
J. Brazilian Soc. Mech. Sci. and Eng., vol. 30, No. 1, 2008, pp. 7–10.