Los equipos de la red eléctrica deben ser compactos y eficientes, pero también deben soportar esfuerzos térmicos extremos. Los métodos de diseño digital son indispensables para lograr este objetivo. Los recientes avances en simulación electrotérmica han convertido la técnica en una valiosa herramienta para el diseñador de equipos eléctricos.
Jörg Ostrowski, Andreas Blaszczyk ABB Corporate Research Baden-Dättwil, Switzerland, joerg.ostrowski@ch.abb.com, andreas.blaszczyk@ch.abb.com; Boguslaw Samul, Remigiusz Nowak ABB Corporate Research Krakow, Poland, boguslaw.samul@pl.abb.com, remigiusz.nowak@pl.abb.com; Michael Gatzsche ABB, High Voltage Products Zurich, Switzerland, michael.gatzsche@ch.abb.com; Valeri L. Oganezov ABB Electrification Products, Saint-Laurent, Quebec, Canada, valeri.l.oganezov@ca.abb.com
La presión por ser compactos y eficientes, y el exigente y variado panorama eléctrico en el que operan, convierten el esfuerzo térmico en una consideración crítica para el diseño de los equipos de red modernos. Para predecir el esfuerzo térmico en un dispositivo o sistema de potencia, podría parecer suficiente calcular el comportamiento electromagnético y las transferencias de calor.
Sin embargo, para lograr un cálculo completo y satisfactorio, deben considerarse y simularse muchos efectos físicos: una tarea que va más allá de los tradicionales enfoques heurísticos de diseño. Debe adoptarse un enfoque de diseño digital.
Nuevas herramientas para simulacióny cosimulación
Si bien las pérdidas resistivas e inductivas, y la conducción térmica, llevan años siendo computables, solo desde hace poco pueden predecirse con exactitud las importantes pérdidas en los contactos eléctricos o los mecanismos mixtos de transferencia de calor convectivo-turbulento-radiativo en las superficiesde dispositivos reales gracias a la cosimulación Maxwell-CFD (dinámica de fluidos computacional). Sofisticados algoritmos de mapeo, el refinamiento automático de la malla y el control de error constituyen importantes compañeros numéricos de estas simulaciones. Estas nuevas herramientas permiten predecir el esfuerzo térmico en los dispositivos eléctricos con una gran precisión y un esfuerzo comparativamente bajo.
La integración de grandes partes de estas simulaciones en un sistema CAD, como se consiguió con la Simulation Toolbox de ABB en los últimos años, permite ahora la ejecución relativamente sencilla de simulaciones complejas. Los modelos de simulación parametrizados integrados en CAD permiten el análisis rápido y preciso de una gran variedad de posibles variantes de producto con diferentes cargas. ABB ha sido pionera en estos gemelos de simulación basados en CAD, que se utilizarán en la ingeniería de la fábrica digital del futuro [1].
En particular, ABB ha sido pionera en métodos avanzados e integrales para cálculos electrotérmicos que son críticos para el correcto diseño de los equipos eléctricos modernos. Los diseñadores de producto de ABB ya utilizan algunos métodos de este tipo. La elección del método depende de la tarea de simulación, los tres ejemplos a continuación muestran la potencia y flexibilidad del enfoque.
Cosimulación Maxwell-CFD de un disyuntor de media tensión para exterior
Uno de los métodos más precisos y detallados para la computación de los procesos electrotérmicos se basa en la cosimulación Maxwell-CFD de acoplamiento de 2 vías. Aquí, las pérdidas de energía electromagnética se calculan mediante un solucionador numérico de elementos finitos de ecuaciones de Maxwell y la transferencia de calor se calcula mediante un solucionador numérico CFD. Los dos solucionadores numéricos intercambian información durante el cálculo para poder tener en cuenta todos los efectos electrotérmicos relevantes.
El uso de dos mallas diferentes para los dos dominios físicos distintos permite una resolución de fenómenos locales que de otro modo sería imposible. En el caso de la refrigeración convectiva, algunos ejemplos de estos fenómenos son los efectos peliculares que concentran las pérdidas de potencia cerca de la superficie de los conductores y las finas capas de contorno turbulentas en la superficie exterior de los sólidos que son decisivas para la transferencia de calor al medio ambiente.
Los investigadores de ABB han desarrollado herramientas computacionales eficaces para llevar a cabo este tipo de simulación tan compleja. A modo de ejemplo, puede utilizarse un análisis electrotérmico en 3D de un disyuntor de media tensión (MT) resistente al arco para exterior →1.
Image currently unavailable
Image currently unavailable
Image currently unavailable
Image currently unavailable
Image currently unavailable
Image currently unavailable
Image currently unavailable
Image currently unavailable
Image currently unavailable
01a Vista exterior. 01b. Componentes interiores. 01c. Modelo simplificado para el subanális térmico.
01. Disyuntor de MT resistente al arco para exterior.
Los disyuntores son uno de los componentes más importantes de las redes de distribución de potencia de MT, ya que garantizan una correcta conmutación de carga y protegen las cargas aguas abajo y las redes aguas arriba, incluidos elementos importantes como los transformadores de potencia.
El comportamiento térmico del disyuntor constituye un factor vital de su funcionamiento. El sobrecalentamiento durante el funcionamiento normal puede acortar su vida útil y dañar componentes principales. Las sobretemperaturas provocadas por las sobrecargas pueden dañar el aislamiento del disyuntor y provocar averías eléctricas.
Un desafío fue que durante la sobrecarga del disyuntor no se permite la refrigeración forzada, pero, no obstante, la unidad debe funcionar de forma fiable entre los -50 y +40 °C (de hecho, la unidad está diseñada para una sobrecarga de hasta el 60% a temperaturas extremadamente bajas). La carcasa aislada térmicamente –diseñada conforme a IP43– cuenta con rejillas de ventilación bien protegidas que limitan la circulación del aire y reducen así la eficacia de la refrigeración por convección. Este aspecto complica aún más el proceso de diseño y puede dar lugar a múltiples iteraciones y nuevas pruebas de diseño.
En dispositivos como los disyuntores automáticos se comprueba el comportamiento térmico mediante pruebas de aumento de la temperatura que requieren condiciones ambientales controladas, un modelo físico del dispositivo, una fuente de alimentación adecuada y una infraestructura de prueba (termopares, etc.).
Una prueba puede tardar muchas horas en alcanzar una temperatura estable. Por supuesto, este tipo de procedimiento de prueba es indispensable para la prueba tipo final de un dispositivo, pero es una forma cara de probar las primeras variantes de diseño, algunas de las cuales podrán descartarse en cualquier caso.
Por el contrario, las pruebas virtuales computarizadas de aumento de la temperatura permiten una validación muy rápida y relativamente barata de diferentes diseños de disyuntores con distintas cargas y condiciones ambientales. El modelo de simulación del disyuntor de media tensión en →2 incluye submodelos electromagnéticos y térmicos (CFD) que intercambian datos. En el modelo electromagnético, incluso si el dispositivo tiene una simetría geométrica, se tienen en cuenta las vías de corriente de las tres fases, habida cuenta de las cargas asimétricas de corriente y los efectos de proximidad. Se realizó una simulación de flujo térmico solo para la mitad del dispositivo, gracias a su simetría geométrica planar.
El proceso de simulación completo incluyó todos los efectos físicos que se producen durante el ensayo térmico estandarizado. En el caso de pérdidas eléctricas y efectos peliculares y de proximidad, se tuvieron en cuenta tanto la influencia de la temperatura en la resistividad de los materiales como las resistencias de contacto eléctrico. Para los cálculos térmicos, se tuvieron en cuenta los efectos de turbulencia en el fluido impulsado por flotabilidad y la radiación térmica. También se incluyeron otros detalles, como la influencia de las rejillas de ventilación en el intercambio de aire entre el interior del disyuntor y el medio ambiente.
La simulación acoplada es un proceso iterativo y se intercambiaron datos entre los dos solucionadores numéricos hasta alcanzar una temperatura estable (±5 %), lo que tardó cuatro iteraciones. Con unadesviación máxima de 5K, los resultados de lasimulación coincidieron casi a la perfección con los resultados de la prueba real de aumento de temperatura →3,4. Este ejemplo ilustra cómo la simulación puede ofrecer resultados fiables y reducir el número de iteraciones de prueba reales.
Image currently unavailable
Image currently unavailable
Image currently unavailable
Image currently unavailable
Image currently unavailable
Image currently unavailable
03. Distribución final de la temperatura dentro de un disyuntor de MT para exterior. 04. Precisión de la simulación: comparación con mediciones físicas.
Modelo de red de un transformador seco
No siempre se puede utilizar la cosimulación Maxwell-CFD, computacionalmente costosa, sobre todo en los grandes dispositivos complejos o si se busca la optimización automatizada del diseño. En estos casos, se utilizan descripciones analíticas simplificadas, por ejemplo, equivalentes térmicos a circuitos eléctricos: las redes térmicas. Estas redes no son necesariamente precisas, pero son computacionalmente mucho más eficientes.
Tradicionalmente, el enfoque de red térmica se ha utilizado para evaluar el aumento de la temperatura en los devanados de los transformadores [1].
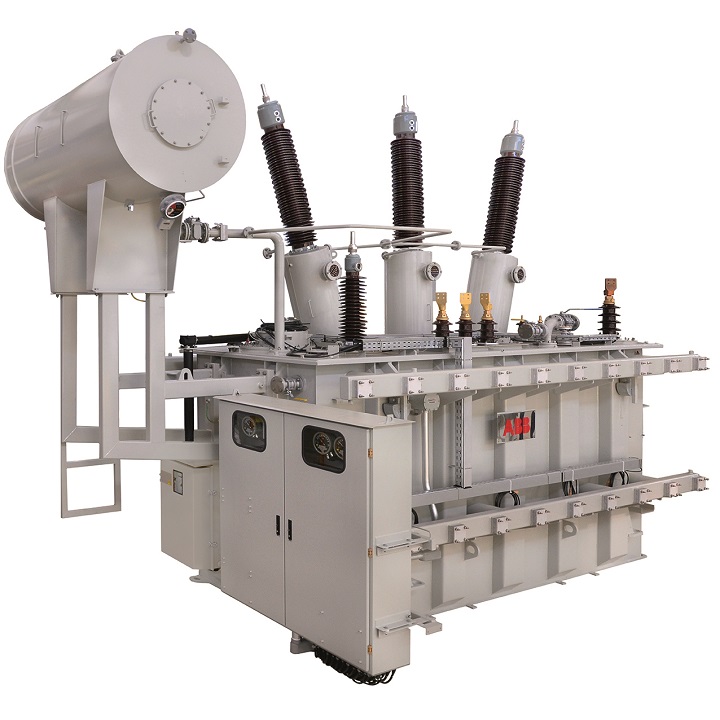
Recientemente, los desarrolladores de la herramienta de diseño de transformadores de ABB han ampliado el modelo de red y han permitido computaciones de todo el sistema de refrigeración [3] →5.
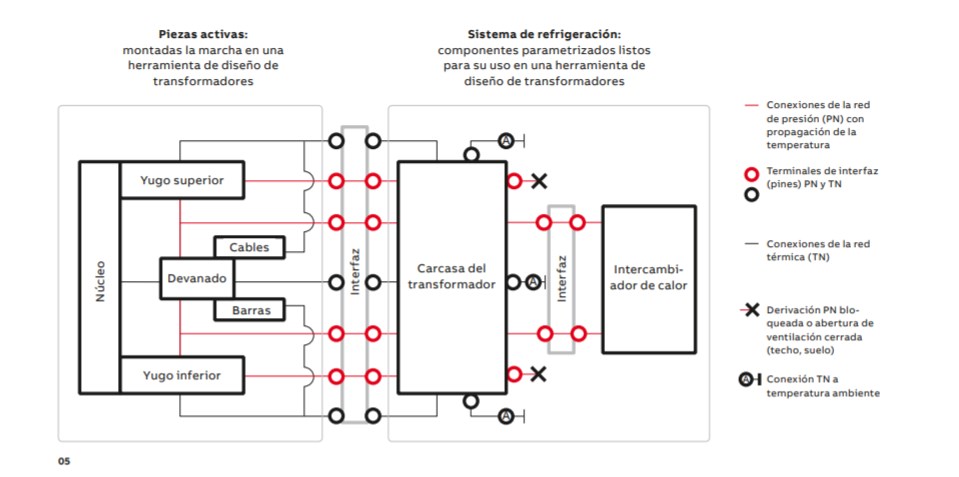
Las piezas activas que generan calor se conectan con el sistema de refrigeración a través de una interfaz predefinida que permite la transferencia de fluido y calor entre los componentes. El sistema de refrigeración incluye una carcasa así como un intercambiador de calor externo con otra interfaz entre ellos. Las interfaces permiten combinar todos los componentes de red implementados y definir una configuración arbitraria de acuerdo con las especificaciones del diseñador. El funcionamiento autónomo del transformador (sin carcasa) yla ventilación abierta (en lugar del intercambiador de calor) se incluyen como opciones disponibles.
Como ejemplo de implementación de los componentes, en →6,7 se muestra un modelo de red de presión de una carcasa de transformador seco. Para crear la topología de la red se han utilizado los flujos de aire identificados en una computación CFD. El resultado CFD se ha utilizado para validar la precisión del modelo de red dentro del rango de parámetros requerido.
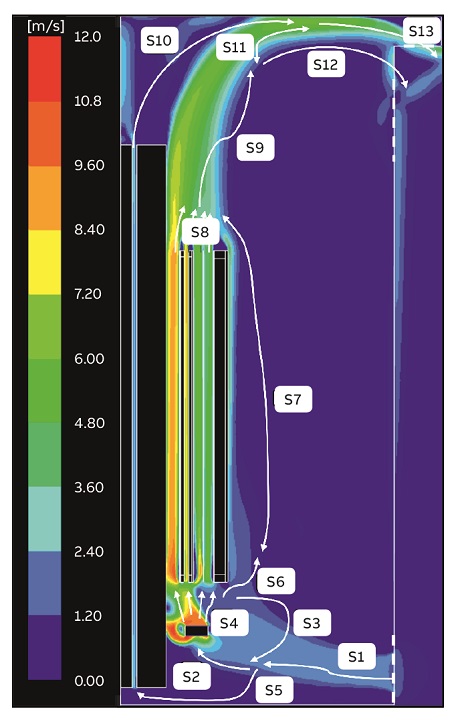
Los parámetros típicos son: dimensiones de la carcasa, datos del ventilador interno y resistencia al flujo de las rejillas de ventilación. El modelo de red puede reproducir los flujos circulares dentro de la carcasa.
![07. Red de presión con ramales de flujo de aire (flechas negras) correspondientes a los resultados CFD desde →6. No se
muestran los cables de propagación de la temperatura ni la red térmica (solo el acoplamiento PN/TN) [3].](https://resources.news.e.abb.com/images/2019/7/15/0/07.jpg)
El modelo completo puede calcular en cuestión de segundos el aumento de la temperatura en el devanado, teniendo en cuenta todos los detalles del bobinado, el núcleo y el sistema de refrigeración. Este enfoque permite a los diseñadores mantenerse dentro de los límites de temperatura requeridos y minimizar los costes de material.
Simulación de prueba de la corriente de corta duración de un seccionador de puesta a tierra
Las pruebas obligatorias de corriente de cortaduración (STC) conducen una alta corriente de corta duración (algunos segundos) a través de un dispositivo para emular un cortocircuito y probar así la resistencia del dispositivo. Dado que las pruebas de STC son complejas y costosas, se valoran las simulaciones STC que predicen de forma fiable el aumento de la temperatura en el dispositivo.
En este caso, un método de cosimulación Maxwell CFD sería exagerado, ya que el flujo de calor procedente del dispositivo a su entorno es bajo. De hecho, toda la parte CFD puede representarse como una mera conducción transitoria de calor en las partes sólidas del dispositivo. La modelización electromagnética adquiere una relevancia mucho mayor para las pruebas STC. Los principales efectos a tener en cuenta son:
- Pérdidas óhmicas en el volumen del dispositivo.
- Dependencia de la temperatura de la resistividad eléctrica.
- Pérdidas óhmicas debidas a resistencias de contacto eléctrico (ECR) en las interfaces del conductor.
Este último efecto es el más complicado y no se puede despreciar, ya que estas pérdidas pueden llegar a representar hasta el 50 % de las pérdidas totales. Además, en los seccionadores, las pérdidas se producen localmente en las superficies de los contactos eléctricos y no se distribuyen por todo el volumen (como es el caso de las pérdidas óhmicas dentro del material).
En consecuencia, las áreas más calientes y vulnerables se encuentran en las proximidades de los contactos eléctricos. La modelización de las ECR es un tema multifísico ampliamente estudiado en todo el mundo. En la simulación de un seccionador de puesta atierra de una subestación aisladas por gas (GIS), se asumió una resistencia de contacto constante, es decir, independiente de la temperatura [4]. Esta es la representación más sencilla de un contacto para el que la creciente resistividad eléctrica (material) durante el calentamiento se compensa con una disminución de la resistencia de contacto debido a una mayor área de contacto causada por el ablandamiento del material.
Se simularon y se realizaron en el laboratorio dos pruebas STC (en las que se condujeron corrientes RMS de 63 kA y 80 kA, respectivamente, por el seccionador de puesta a tierra durante 3 s) →8,9.
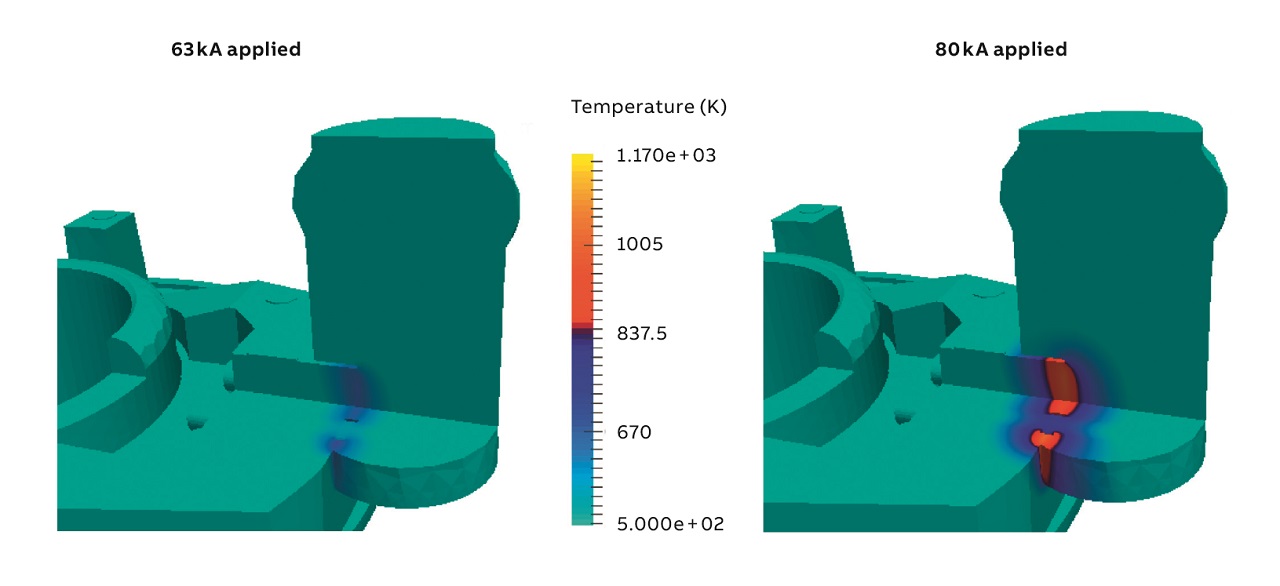
El prototipo real superó la prueba de 63 kA pero falló después de aproximadamente 2s en la pruebade 80 kA, reflejando fielmente los resultados de la simulación. Se desarrolló un nuevo diseño de 80 kA.
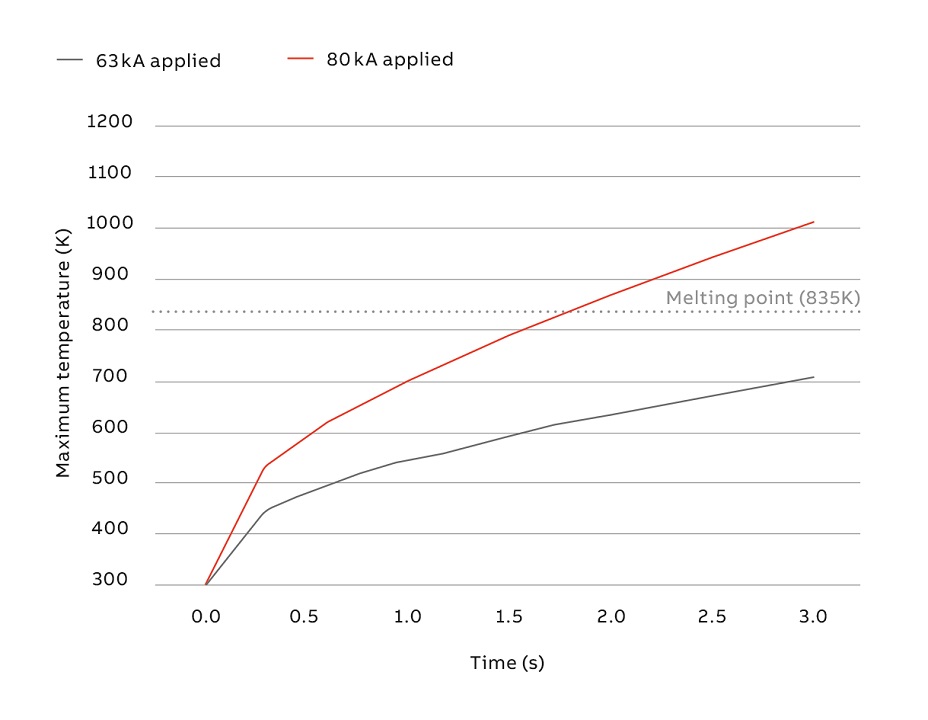
Modelizando el futuro
A medida que las herramientas de simulación electrotérmica mejoren aún más y la cosimulación sea más fácil y potente, se podrán conseguir mejores resoluciones de modelos y los modelos reproducirán la experiencia real de los dispositivos de forma aún más parecida. Los equipos eléctricos están atravesando un período de grandes cambios debido a tendencias como la digitalización, la generación distribuida, la transferencia interregional de energía y los efectos de renovables altamente variables. Las herramientas de simulación y cosimulación en desarrollo que sean más potentes y más sofisticadas resultarán muy útiles.
Referencias
[1] A. Blaszczyk et al., “Simulation Toolbox – Dielectric and thermal design of power devices,” ABB Review 3/2013, pp. 16–21.
[2] R. Nowak et al., “A 3D electro-thermal simulation of the outdoor medium voltage circuit breaker,” IEEE Transactions on Power Delivery (in review process).
[3] A. Cremasco et al., “Network modelling on dry-type transformer cooling systems,” COMPEL – The international journal for computation and mathematics in electrical and electronic engineering, Vol. 37, Issue 3, 2018.
[4] J. Ostrowski et al., “Simulation of short time current tests of industrial devices.” Accepted by SCEE 2018, Springer Series “Mathematics in Industry.”