Manuel Oriol, Der-Yeuan Yu ABB Motion, Motors and Generators Baden, Switzerland, manuel.oriol@ch.abb.com, der-yeuan.yu@ch.abb.com; Maciej Orman ABB Business Services Sp. z o.o. Motion, Motors and Generators Krakow, Poland, maciej.orman@pl.abb.com; Neethu Tp ABB Global Industries and Services Private Limited, Motion, Motors and Generators, Bangalore, India, neethu.tp@in.abb.com; Geir Svoen ABB AS Industrial Automation, Energy Industries Oslo, Norway, geir.svoen@no.abb.com; Philipp Sommer, Gerd Schlottig, Alexey Sokolov, Ștefan Stănciulescu, Felix Sutton ABB Corporate Research Baden-Dättwil, Switzerland, philipp.sommer@ch.abb.com, gerd.schlottig@ch.abb.com, alexey.sokolov@ch.abb.com, stefan.stanciulescu@ch.abb.com, felix.sutton@ch.abb.com
En la última década, ABB ha presentado varios sensores inteligentes integrados, como WiMon100, el ABB Ability Smart Sensor para motores, el ABB Ability Smart Sensor para bombas y el ABB Ability Smart Sensor para cojinetes y engranajes montados.
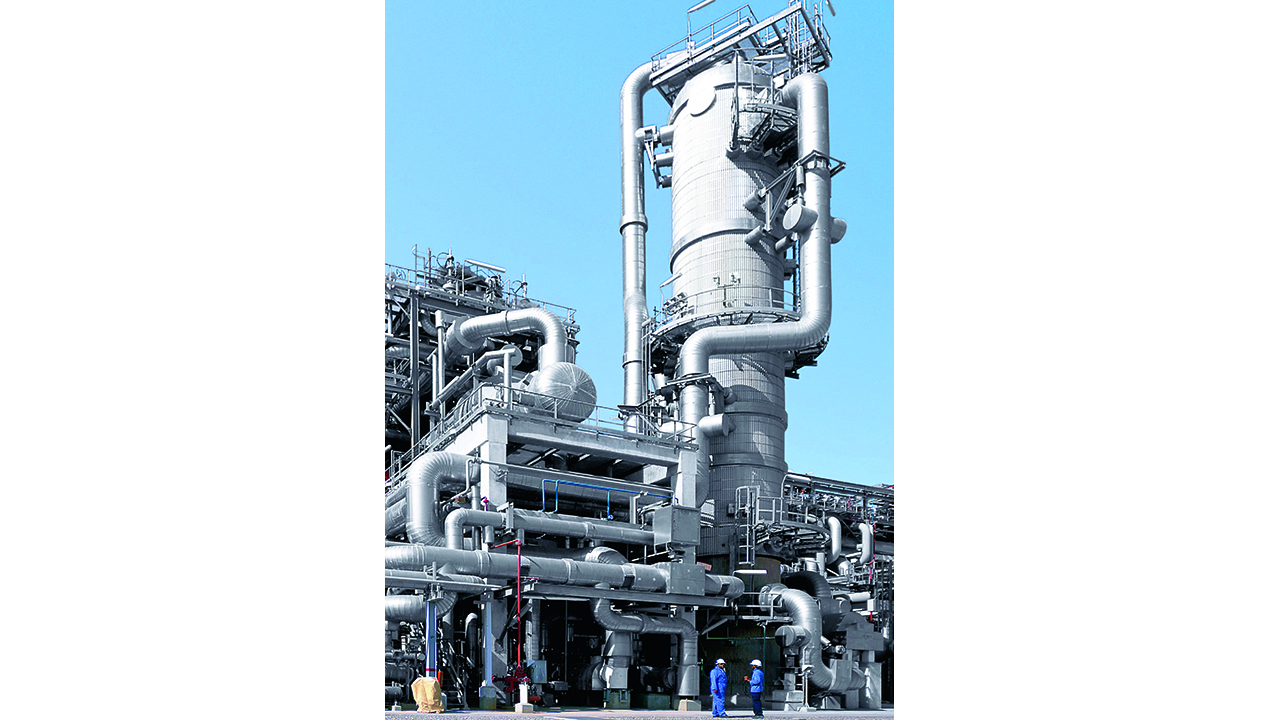
Presentada en 2016, la familia ABB Ability Smart Sensor se encuentra ahora en miles de aplicaciones de clientes en todo el mundo; sin embargo, faltaba una versión eficiente del producto para máquinas rotativas que operan en áreas peligrosas. Para llenar este vacío, ABB ha diseñado una nueva generación desensores ABB Ability Smart que pueden utilizarse en equipos que trabajan en atmósferas explosivas. Garantizar que el nuevo sensor sobreviviría cómodamente en estos entornos, y supondría una mejora respecto de los sensores de ABB existentes, impuso al dispositivo exigencias extremas de diseño, el cual tendría que:
• Medir vibraciones de alta frecuencia.
• Demostrar resiliencia física frente a condicionesambientales duras y peligrosas.
• Tener una vida útil que coincida con la de la mayoría de los equipos supervisados, con una batería, no recargable y no reemplazable.
• Utilizar una arquitectura de firmware flexible para adaptarse a las distintas necesidades deproducto en el futuro →01–02.
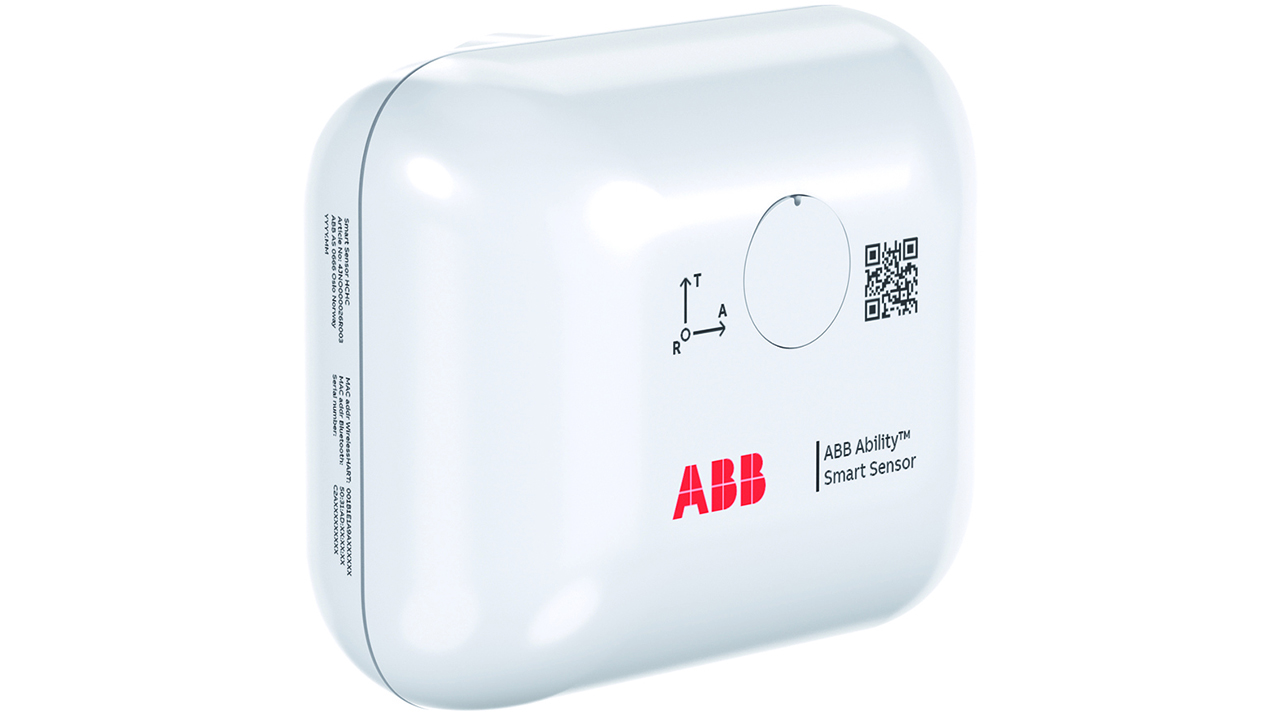
Reto 1: medir la vibración
Mientras que la mayoría de los sensores equivalentes del mercado solo miden vibraciones y temperatura, ABB Ability Smart Sensor mide vibraciones, campo magnético, temperatura y acústica. En consecuencia, el sensor puede medir la velocidad de rotación de los motores con una precisión muy alta.
Los sensores de vibración se están convirtiendo en algo habitual en la electrónica de consumo y la automatización industrial; sin embargo, crear un sensor de vibración de alta calidad no es tarea fácil. Por ejemplo, es fundamental evitar que las resonancias que se producen en cualquier parte del cuerpo del sensor afecten a los transductores que captan vibraciones de la máquina que se está supervisando. Muchos aspectos hacen que el problema sea más difícil de resolver: posicionamiento, soportes de montaje y método de fijación, por citar algunos. Y hacerlo además con el menor coste posible supone un reto difícil de abordar.
El primer enfoque de ABB hacia el nuevo sensor consistió en colocar una gran chapa de acero prensado en la parte inferior del sensor para transmitir las vibraciones del activo supervisado de la forma más directa posible. El sensor tenía dos placas electrónicas: unapegada a la chapa metálica (directamente atornillada al activo) y otra conectada a la chapa y dicha placautilizando únicamente un cable flexible →03.
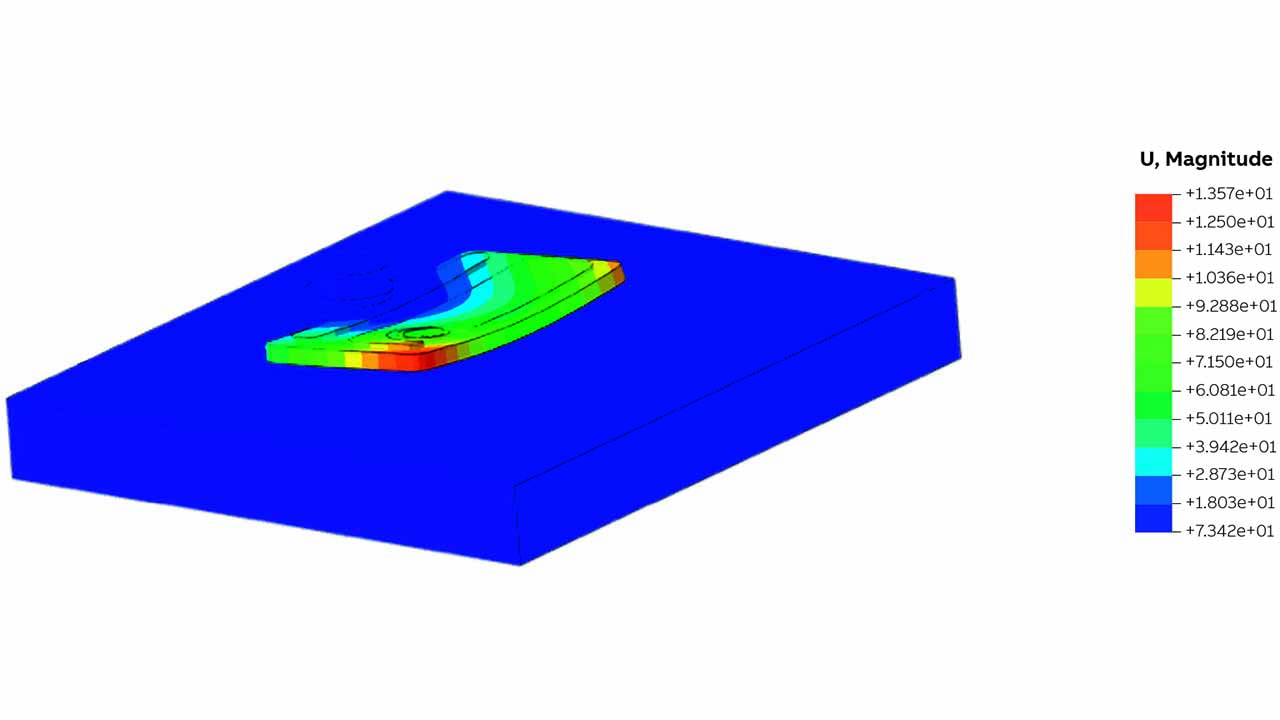
Esta primera versión de la chapa metálica consiguió un rendimiento deficiente con respecto a la autorresonancia: Las fuerzas de resonancia desde el cuerpo del sensor se propagaron hasta la base metálica prensada y fueron captadas por los transductores de vibración. Sin embargo, al utilizar un modelo detallado del sensor y la chapa metálica, se simularon muchas alternativas, lo que dio lugar a una chapa metálica que no solo está completamente pegada a la máquina sin propagar fuerzas de vibración desde el cuerpo del sensor hasta la ubicación de los transductores de vibración, sino que también mantiene los objetivos de coste →04.
04a. Base del sensor y orejeta de la chapa, vista oblicua. 04b Base del sensor y orejeta de la chapa, vista lateral.
04. Modelo 3D de la chapa metálica.
Reto 2: crear un sensor para áreas de peligro
Los sensores certificados para áreas de peligro disponibles a escala mundial deben cumplir una amplia gama de requisitos detallados establecidos en varias normas. Algunas condiciones esenciales son:
• Un cortocircuito interno en la batería no provocará un calentamiento que pueda inflamar gas.
• El hardware interno no provocará calor ni una chispa que pueda inflamar gas.
• Si la envuelta está comprometida y el sensor está relleno de material conductor, no debe producirse calentamiento ni chispas que puedan inflamar gas.
• El sensor debe soportar las tensiones derivadas de su entorno.
La primera condición se suele abordar comprobando la temperatura que se puede alcanzar en las condiciones más extremas. En el caso de un sensor alimentado por baterías, estas condiciones se comprueban haciendo cortocircuitar las baterías y manteniendo las temperaturas resultantes por debajo del límite máximo definido por la norma,135 °C (clase de temperatura T4). En el diseño denuestro sensor inteligente para zonas peligrosas se cumple este criterio de temperatura. El calor también se dirige al resto de la estructura mecánica y es absorbido por los plásticos de la carcasa.
La última condición de la lista anterior es asegurarse de que el sensor es capaz de sobrevivir incluso en las condiciones ambientales más extremas. Para nuestro sensor inteligente, el intervalo de funcionamiento objetivo fue de -40 a +85 °C, que es el intervalo típico de la mayoría de los componentes electrónicos industriales. Se realizaron pruebas de vida altamente aceleradas (HALT) para probar la resistencia del sensor fuera de la ventana operativa nominal, mediante ciclos de alta y baja temperaturas y mediante una combinación de altas vibraciones y temperaturas extremas. Los resultados de las pruebas HALT demostraron que el sensor sobrevive a intervalos de temperaturas de -70 a 130 °C, muy por encima del objetivo original →05.
05a. Ciclos de temperatura. 05b. Detalle del sensor sometido a prueba montado en su placa.
05. Sometido apruebas HALT.
Reto 3: construir un sensor inalámbrico alimentado por batería con una larga vida útil
La vida útil de la batería del ABB Ability Smart Sensor para áreas de peligro es hasta tres veces más larga que la de la mayoría de los diseños de la competencia y puede adaptarse a la vida útil de los equipos supervisados. También se beneficia de más autonomía gracias al protocolo Bluetooth 5. La batería principal no puede reemplazarse ni recargarse. Las baterías recargables o reemplazables no son deseables porque:
• Las baterías reemplazables pueden aumentar el coste del sensor hasta el punto de que sea más rentable simplemente cambiar todo el sensor, y de paso incorporar nuevos componentes electrónicos con un mayor rendimiento.
• Existe el riesgo de que el usuario ponga en peligro el estado de protección del área peligrosa al insertar incorrectamente las nuevas baterías.
• La protección contra la entrada de polvo y agua también podría verse comprometida si las baterías no se sustituyen correctamente.
El objetivo combinado de diseñar un sistema integrado con una vida útil de diseño de hasta 15 años al tiempo que se proporciona una indicación fiable de la vida útil restante de la batería es complicado, debido como mínimo a tres razones:
• Para limitar la corriente de fuga interna de la batería, la temperatura experimentada por la batería debe ser moderada.
• Para evitar que las almohadillas soldadas se rompan, las fuerzas de vibración de la batería y el sensor no deben propagarse a la interfaz entre ambos.
• El consumo de energía del sensor debe mantenersebajo, incluso con una gran batería instalada.
En el nuevo sensor inteligente, la batería y susalmohadillas soldadas están recogidas en un soporte de batería que está separado de las fuentes de calor primarias por un entrehierro, que la protegen del calor procedente del activo supervisado →06.
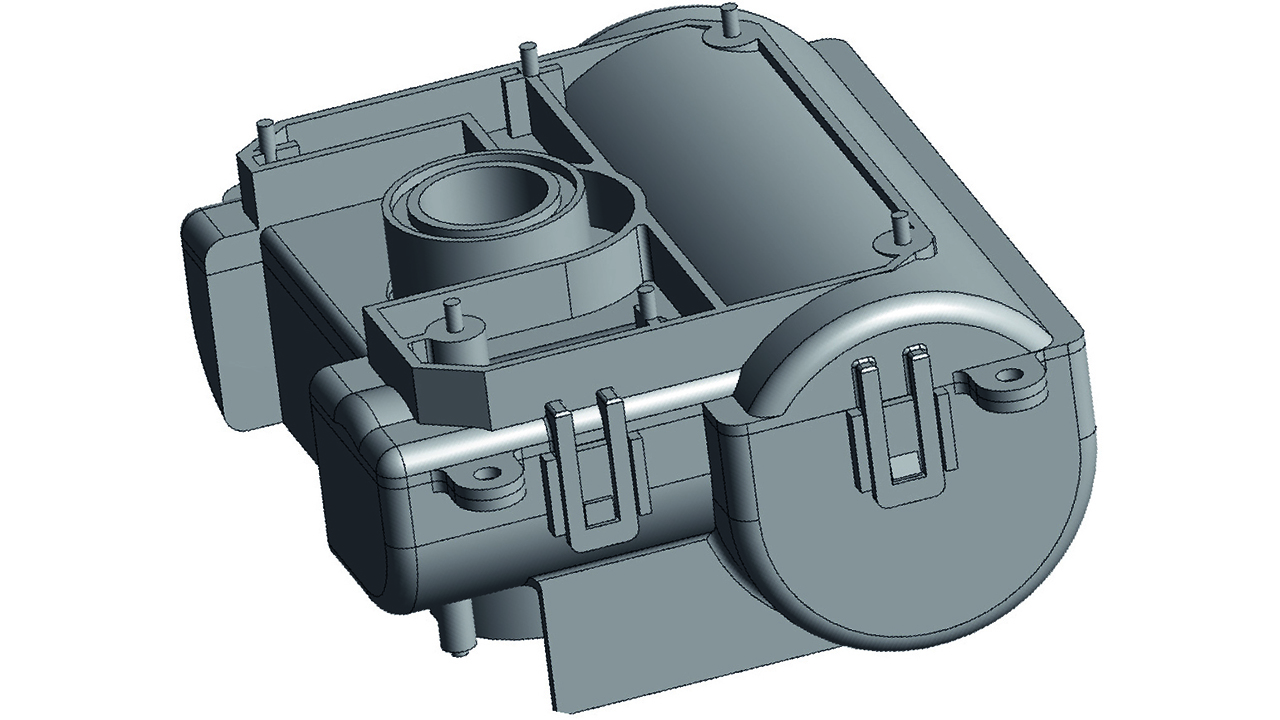
Para evaluar la corriente de fuga dependiente de la temperatura de la batería, el sensor mide la temperatura de la batería durante su funcionamiento y calcula la corriente de fuga correspondiente basándose en un modelo de batería probado.
En otra táctica de medición de la carga de la batería, el firmware utiliza un sistema de puntos para calcular la carga consumida por el funcionamiento normal del sensor. La mayoría de las veces, el sensor está en sueño profundo y consume muy poca energía, pero cuando el sensor se despierta, su consumo aumenta.El sensor registra cuánto tiempo tarda cada operación que consume batería, por ejemplo, la duración de una actividad de chip Bluetooth. A partir de las duraciones y curvas de potencia de las operaciones, se calcula la carga consumida y se resta de la capacidad inicial de la batería. Sobre la base de un valor medio continuo del consumo, se estima y publica la vida restante. Este enfoque capta el uso real de la batería en lugar de basarse en la vida útil predefinida de la batería y unos niveles de consumo de energía asumidos, que a menudo son inexactos.
Reto 4: firmware y software a prueba de futuro
El nuevo firmware y software de Smart Sensor tiene dos objetivos principales: promover la creación de diferentes tipos de sensores en el futuro y permitir la reconfiguración de un sensor instalado para supervisar distintos tipos de activos. Como ejemplo de este último objetivo, un nuevo sensor podría reconfigurarse sobre la marcha para ser utilizado como sensor de motor o sensor de bomba, o en cualquier otro tipo de activo, mediante la selección de perfiles de máquina predefinidos o personalizados. El firmware del sensor puede adaptarse fácilmente a los nuevos requisitos gracias a su arquitectura de software flexible que permite desacoplar los componentes individuales de la plataforma del hardware/sistema operativo. Estos componentes se comunican mediante un middleware de publicar-suscribir. En general, el firmware está organizado como una línea de producto de software, lo que lo hace a prueba de futuro y, por tanto, apto para la creación de nuevas variantes de sensores basados en la misma plataforma subyacente.
Las pruebas de estas múltiples configuraciones y características avanzadas requieren pruebas automáticas, las cuales deben ser rastreadas y administradas. Para ello, ABB ha encargado una serie de pruebas de integración continua que garantiza que la recogida de datos funciona según lo previsto, que se detectan todos los bugs introducidos mediante reconfiguraciones o cambios de firmware, que se prueban rigurosamente las actualizaciones de los algoritmos y que el firmware cumple los requisitos relativos al bajo consumo de energía.
Basándose en una mayor sensibilización en materia de protección de datos, ABB también ha desarrollado funciones integrales de ciberseguridad para satisfacer las necesidades de los clientes. Estas incluyen el intercambio seguro de claves para la comunicación Bluetooth con conexión fuera de banda, cifrado Bluetooth, autenticación del usuario, control de accesos basado en roles y actualización segura del firmware.
Inteligente de cara al futuro
El nuevo sensor inteligente es un éxito tecnológico que mide las vibraciones con una precisión superior a la de todos los sensores inteligentes anteriores. Es tesensor extremadamente robusto está certificadopara zonas peligrosas (ATEX e IECEx: Zona 0, Zona 20,Clase I División I y Clase 2 División I). Además, el sensor se ha beneficiado de un esfuerzo de diseño que introduce ciertas características que mejoran significativamente la experiencia del operador: puesta en servicio del sensor fácil de usar mediante la activación NFC (comunicación de campo cercano), mejor diseño de la antena para una comunicacióninalámbrica óptima y mayor duración de la batería.
En resumen, nuestro último sensor ofrece funciones integrales de ciberseguridad, plataforma de firmware flexible, rendimiento optimizado y control y evaluación del consumo de energía en el mundo real. Estas mejoras aportan aún más valor a los clientes y hacen del nuevo ABB Ability Smart Sensor para entornos peligrosos el estándar de facto para la supervisión del estado de los equipos rotativos.