Jinendra Gugaliya Former ABB employee; Will Leonard ABB Energy Industries Cambridge, United Kingdom, will.leonard@gb.abb.com; Peter Damer ABB Energy Industries St Neots, United Kingdom, peter.damer@gb.abb.com; Maurizio Barabino ABB Energy Industries Genoa, Italy, maurizio.barabino@it.abb.com
Las industrias de procesos, como las refinerías, las cementeras y las centrales eléctricas, etc., dependen de una multitud de equipos cruciales, como motores, bombas, ventiladores, compresores, turbinas, etc., que funcionan 24 horas al día para garantizar una buena producción. Mantener estas máquinas en el mejor estado es fundamental, ya que el desgaste es inevitable y las averías no son deseables. Normalmente esto se consigue con un mantenimiento planificado, en el que se sustituyen algunas piezas y se aplica lubricante a piezas giratorias, etc., según un calendario establecido, o con un mantenimiento reactivo o no planificado, en el que las máquinas solo se reparan cuando fallan, una labor muy cara [1,2]. De hecho, un estudio reciente de la ARC reveló que las empresas pierden entre el 3 y el 5 % de su producción debido a tiempos de inactividad imprevistos [2]. Aumentar el uso de los activos solo un 1 % podría fácilmente traducirse en varios millones de dólares de ingresos adicionales [2]. Además, las empresas energéticas dedican alrededor del 40 % de sus gastos operativos al mantenimiento planificado y no planificado pero solo cubren el 20 % de sus activos [2]. El mantenimiento planificado tiene ventajas sobre el mantenimiento reactivo, porque el uso de las máquinas hasta que fallen no solo puede dar lugar a una parada no planificada de la planta, sino que también puede comprometer seriamente la seguridad del personal, los equipos y el medio ambiente [3,4].
Con la aparición de la Industria 4.0, los avances en tecnología digital, aprendizaje automático (ML) y computación en la nube y en el borde, está surgiendo un nuevo paradigma para el mantenimiento del buen estado de los activos y ABB está a la vanguardia de esta génesis. En la actualidad, los activos están muy digitalizados, de manera que las mediciones críticas de los sensores generan grandes flujos de datos. Los análisis avanzados pueden utilizarse para averiguar el momento exacto en que el activo requiere mantenimiento. Adoptar este enfoque basado en datos sensibles para el mantenimiento de activos, el del mantenimiento predictivo, abre todo un mundo de rentabilidad al basarse en el estado efectivo de los activos en tiempo real. La industria ya no debe elegir entre usar una máquina hasta que falle o sustituir piezas que estén en perfectas condiciones: el mantenimiento puede pronosticarse y optimizarse.
Mantenimiento predictivo: los fines y los resultados
El mantenimiento predictivo puede añadir valor a los procesos de producción mejorando la eficiencia y reduciendo la necesidad de mantenimiento no planificado y la redundancia, y con ello reduciendo los costes [1]. En las industrias de procesos, el uso de este enfoque puede reducir el tiempo de inactividad entre un 30 % y un 50 % y prolongar la vida útil de los equipos entre un 20 % y un 40 % [1].
Para adoptar una estrategia de mantenimiento predictivo con éxito, la detección e identificación temprana de fallos incipientes es imprescindible. Esto exige una inspección del equipo y alertas tempranas para investigar las posibles causas de los fallos que puedan producirse.
Pronosticar el mantenimiento no es algo sencillo. Para programar eficazmente el mantenimiento, es necesario predecir cómo de probable es que el estado anormal detectado se desarrolle en el futuro. Solo entonces se podrá obtener información valiosa sobre las probables consecuencias futuras [1]. Por lo tanto, el correcto mantenimiento predictivo requiere un proceso de tres vertientes:
- Vigilancia del estado que permita la detección temprana de fallos;
- Identificación de modos de fallo específicos relacionados con la detección de fallos:
- Cuantificación del alcance del desarrollo de los fallos para contribuir a la planificación del mantenimiento.
A pesar de que existen varios enfoques de ML populares para el desarrollo de modelos para controlar el estado de los activos, como el análisis de componentes principales (PCA), los k vecinos más cercanos (KNN), el factor atípico local (LOF), la máquina de soporte vectorial de una clase (OCSVM), etc. [5], los enfoques de ML son enfoques de caja negra y dependen totalmente de datos de los activos: no hacen ninguna suposición por lo que respecta al activo o a sus modos de fallo. En la práctica, la experiencia industrial indica que este tipo de enfoque no siempre tiene éxito y a menudo da lugar a varios tipos y/o varias instancias del mismo tipo de falsos positivos; y falsos negativos. Dar una alarma cuando el activo está en perfectas condiciones o viceversa puede aumentar los costes imprevistos y redundantes y reducir la viabilidad [6].
Para evitar estas consecuencias no deseadas, ABB propone el uso de un robusto enfoque híbrido que utiliza modelos de ML y análisis de modos de fallo y efectos (FMEA) de los activos para proporcionar una información precisa sobre su estado real.
El innovador enfoque híbrido de ABB
El enfoque híbrido de ABB se basa en los datos históricos y los modelos de ingeniería de un activo para permitir el mantenimiento predictivo. Aquí, la supervisión online del estado, combinada con la ciencia de datos, utiliza una de estas dos técnicas:
- Detección de anomalías cuando las mediciones online se desvían del comportamiento operativo normal.
- Identificación de las características conocidas del fallo cuando las mediciones online se asemejan mucho a una «firma de fallo».
Ambas técnicas utilizan un modelo de datos: la primera representa el «estado correcto» y la segunda refleja la «firma de datos» de las condiciones de fallo. Dado que estas dos técnicas son esencialmente el corolario la una de la otra, es natural concluir que pueden ser igualmente útiles. En la práctica, sin embargo, la primera es a menudo el mejor enfoque porque casi siempre hay suficientes datos históricos disponibles que representan el estado correcto. Estos datos de estado permiten entrenar al modelo. Por el contrario, normalmente no hay datos disponibles, o no hay datos suficientes, para representar todas las posibles condiciones de fallo, lo que impide entrenar al modelo. Además, este último modelo se basa en las características del equipo, según se observan en los datos, y estas dependen de las condiciones de instalación y funcionamiento. Por lo tanto, los datos que se refieren a una máquina específica suelen ser insuficientes para el entrenamiento de un modelo de fallos preciso.
Con el enfoque híbrido, un modelo de ingeniería permite cuantificar el alcance de la desviación de las mediciones online procedentes respecto del modelo de estado. Se utiliza un modelo de análisis del modo de fallo. Esta técnica, comúnmente conocida como análisis de modos de fallo y efectos (FMEA), es un elemento fundamental de los programas de mantenimiento centrado en la fiabilidad (RCM). Dado que ya existen modelos para los equipos y sistemas más comunes, esta técnica resulta ventajosa. El FMEA incorpora los medios (a través de la observación) para definir la posible detección e identificación de un fallo. Cuando esta detección es posible por la medición online de sensores, puede predecirse el fallo.
Tres pasos para el éxito: el proceso del enfoque híbrido
Los científicos de ABB han propuesto un nuevo proceso en tres pasos para configurar el estado de los activos:
- Definir el modelo de ingeniería estableciendo los modos de fallo y las mediciones asociadas.
- Entrenar al modelo de datos con datos históricos.
- Desplegar el modelo
En el paso 1, la asociación entre los modos de fallo y las mediciones asociadas se refleja como un conjunto de variables. Una variable distinta de cero indica que el fallo es observable en valores anómalos de la medición, y la magnitud de la variable refleja la fuerza asociada de la observación en relación con el resto de mediciones →01.
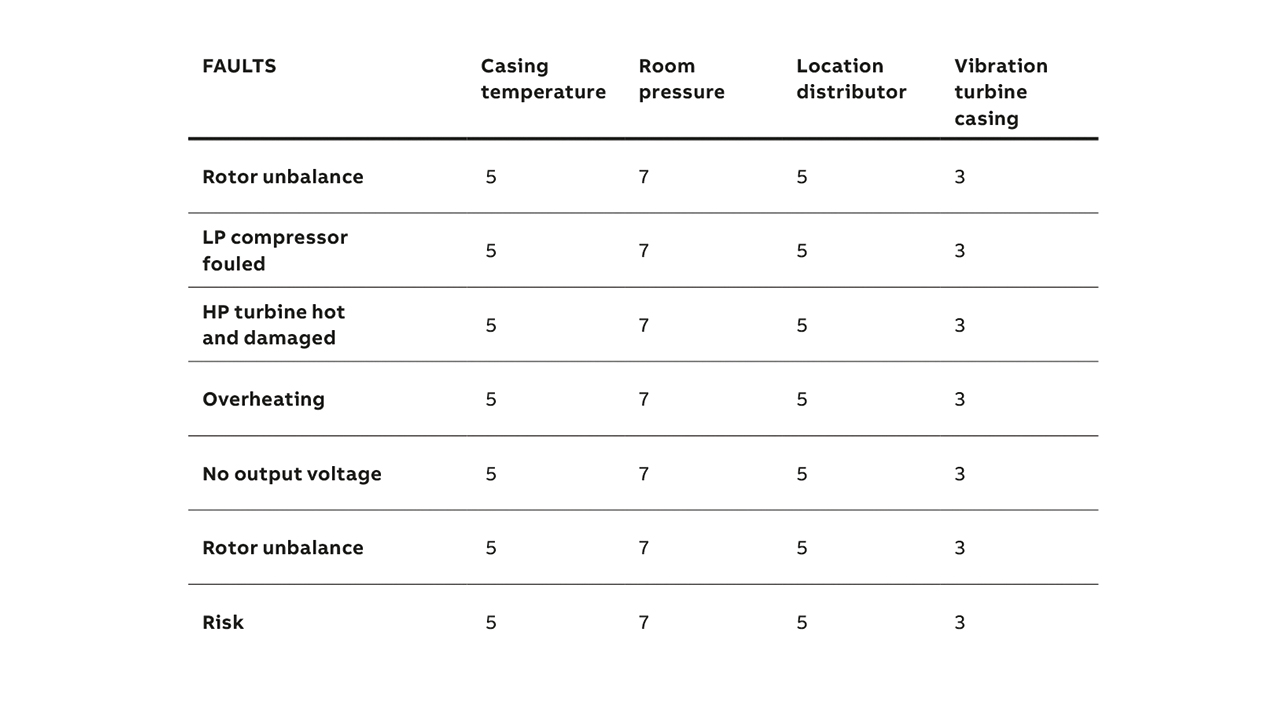
En el paso 2 se utilizan los datos históricos para entrenar al modelo de datos de estado. Los datos seleccionados reflejan el estado correcto del equipo en todas las condiciones de funcionamiento. Para el entrenamiento se utilizan varios métodos estadísticos y de ML para obtener un modelo comprimido adecuado para el cálculo en tiempo real.
A continuación, en el paso 3, se despliegan los modelos entrenados. Estos modelos toman datos del activo a intervalos regulares, por ejemplo, un minuto, y proporcionan información sobre el estado del activo; por ejemplo, la probabilidad de que la condición dé lugar a un modo de fallo.
¿Cómo funciona el modelo híbrido?
Basándose en modelos de análisis de datos y de fallos, el enfoque híbrido genera indicadores para el mantenimiento predictivo: Indicador clave de diagnóstico (KDI) →02 e indicadores de fallo. En primer lugar, para cada medición en cada modelo se calcula un KDI comparando la desviación del valor medido con respecto al valor de referencia «esperado». El valor de referencia se obtiene buscando todos los datos de la correspondencia más cercana a las condiciones actuales. Se utiliza un algoritmo de ML como KNN para calcular de forma eficiente el vecino más cercano.
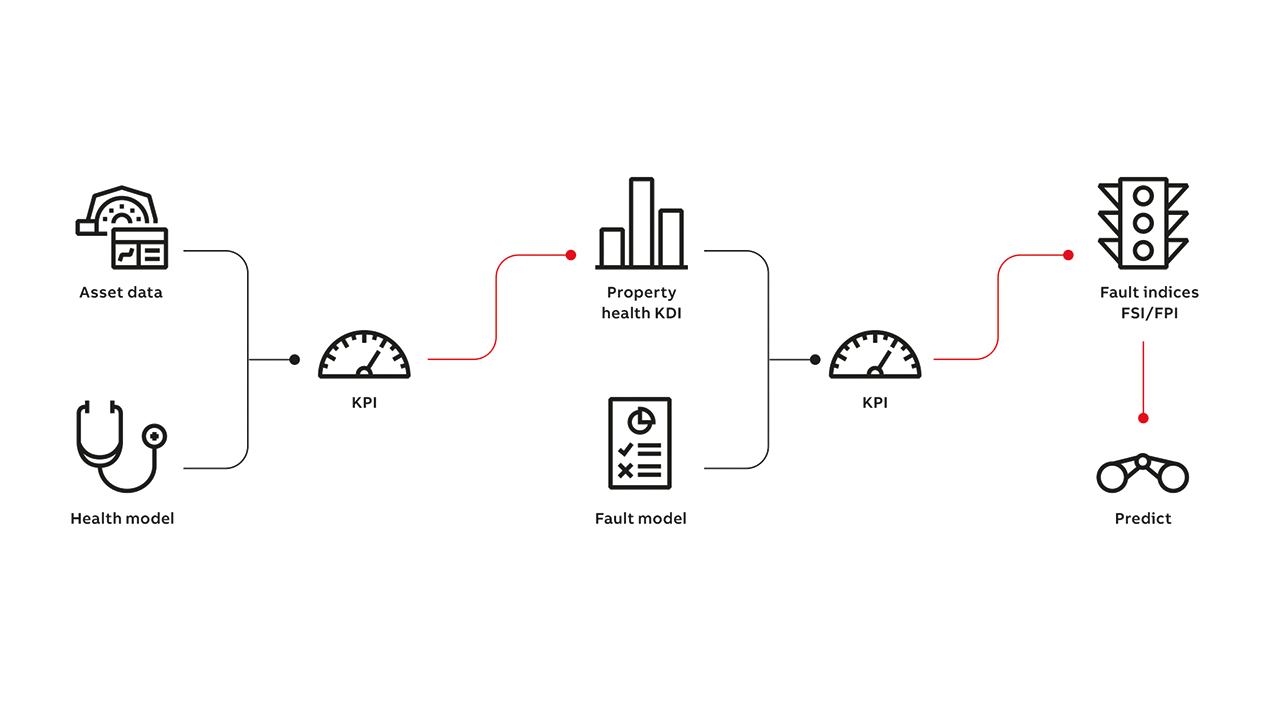
Todos los KDI se expresan como porcentaje, lo que permite al usuario interpretar fácilmente el valor, independientemente del modelo, la cantidad medida o el rango. Cabe destacar que, aunque se trata de un valor singular, el cálculo del KDI utiliza una técnica multivariable de modo que la correspondencia más cercana tiene en cuenta todas las mediciones definidas para el modelo →02 – 03.
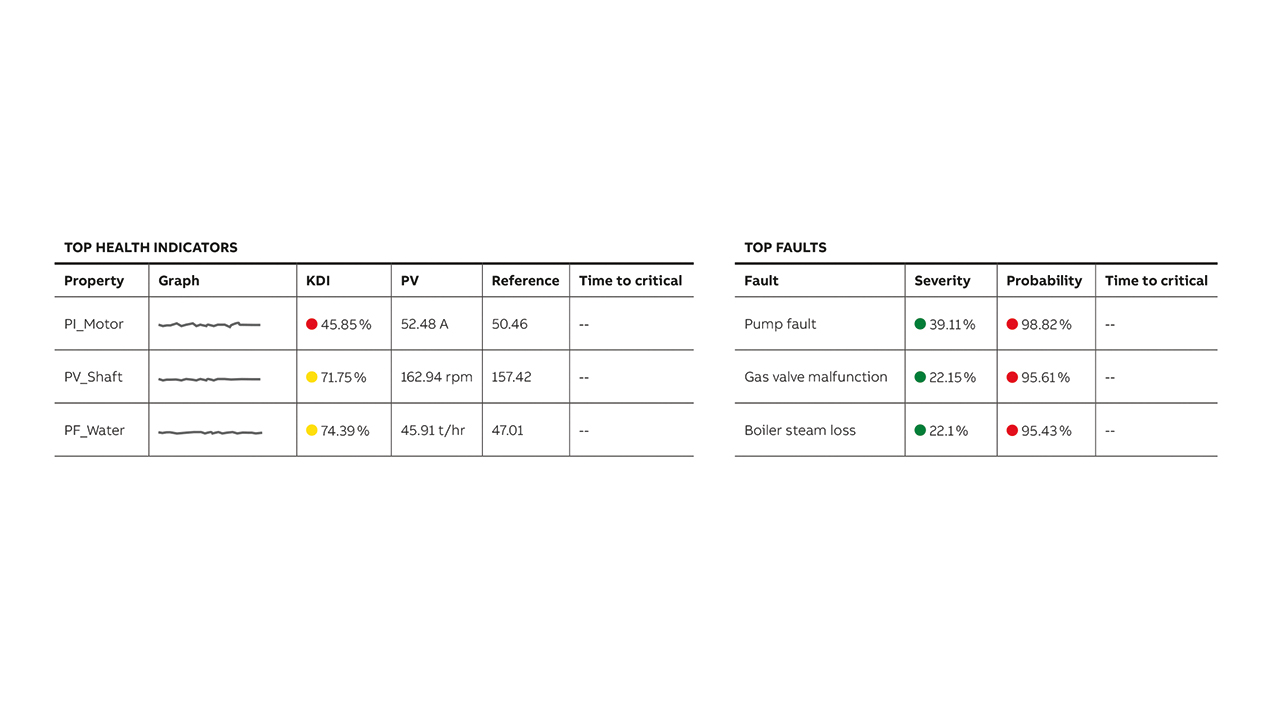
En segundo lugar, los indicadores de fallos →02: para cada fallo se calculan el indicador de probabilidad de fallo (FPI) y el indicador de gravedad del fallo (FSI) →03. El cálculo representa una agregación de las desviaciones de todas las medidas ponderadas. El cálculo de la agregación difiere para establecer una distinción entre gravedad y probabilidad basada en la distribución relativa de la desviación en todas las mediciones →03.
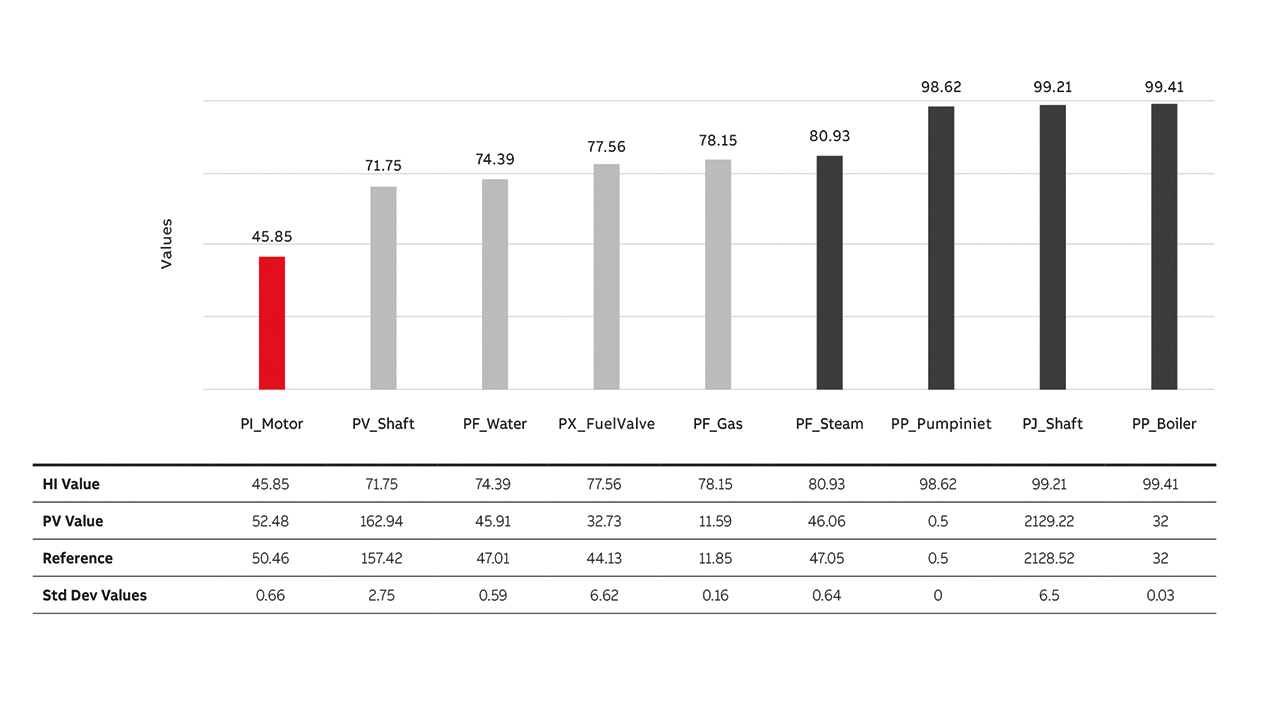
Además de ver la información de resumen de los KDI y los fallos, los usuarios pueden ver todos los indicadores →04 ordenados por puntuación. Para cada fallo, los usuarios pueden acceder a la información del KDI subyacente →05. Para los valores extraídos del modelo de datos, el valor de desviación estándar se calcula utilizando un algoritmo KNN. Este valor se utiliza para calcular la puntuación del KDI y proporciona a un usuario experimentado información sobre el cálculo subyacente.
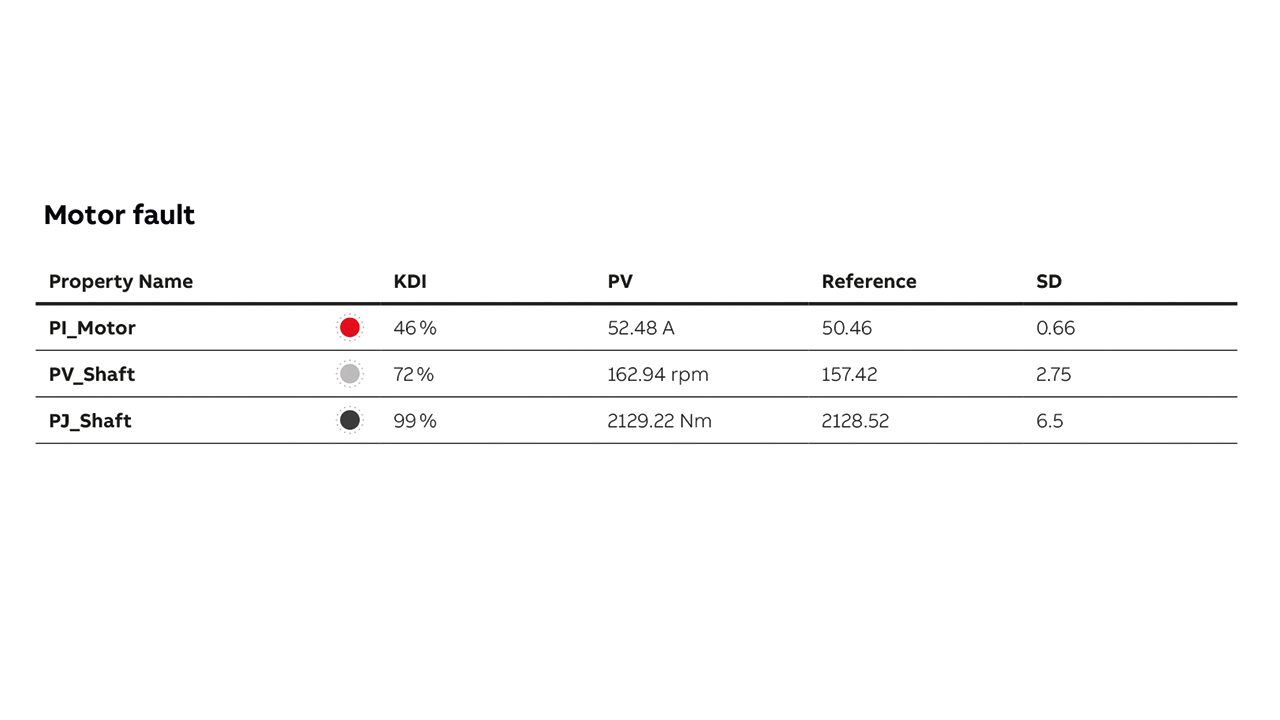
Si bien los indicadores mencionados se refieren al estado actual de los equipos, para proporcionar la base del mantenimiento predictivo →06 es necesario prever las condiciones futuras. En primer lugar, se proporcionan al usuario tendencias históricas que permiten el análisis manual →07; esto se consigue facilitando las tendencias históricas de cada uno de los indicadores clave.
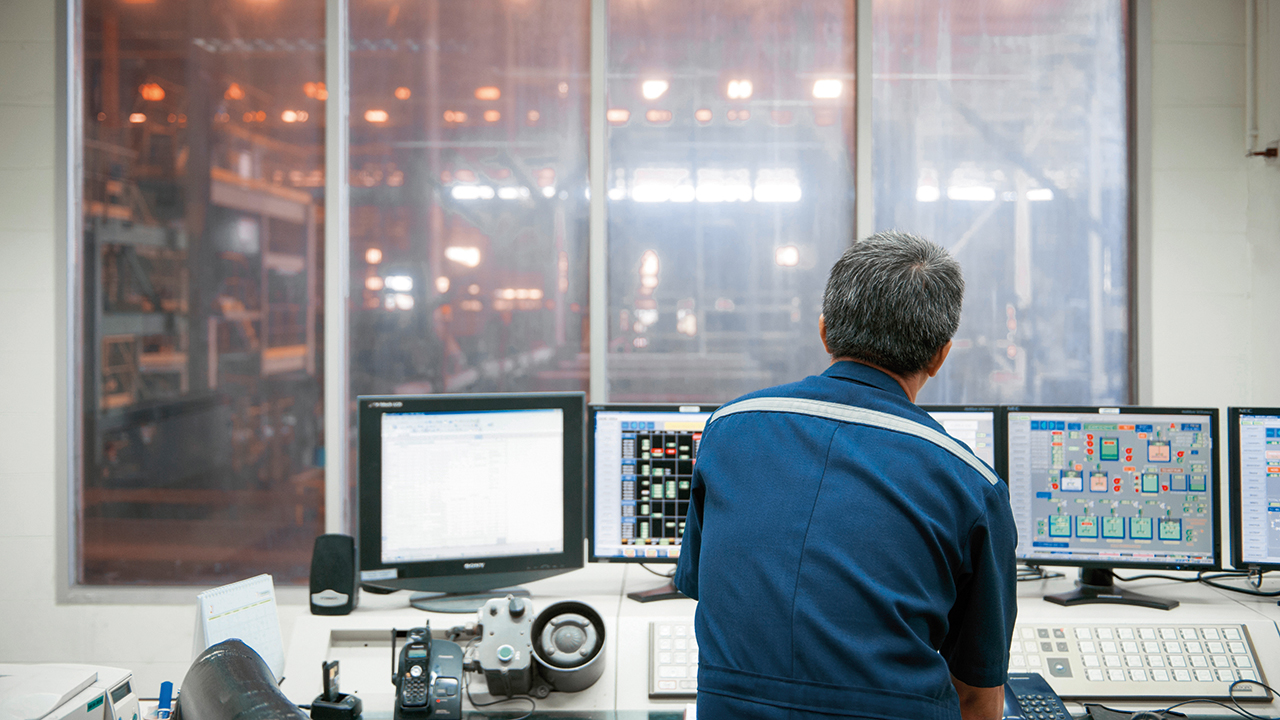
En segundo lugar, se proporciona un perfil de previsión de los indicadores con cierto horizonte futuro. Esto se calcula (y se visualiza) utilizando la técnica de regresión Auto Regressive Integrated Moving Average model (ARIMA).

El modelo de fallos ofrece información adicional relacionada con el análisis de la causa y las acciones correctivas, que se visualizan fácilmente →08. Se proporciona un flujo de trabajo totalmente automatizado integrando los valores de los indicadores de fallo y la información de los fallos con un sistema de gestión del mantenimiento informatizado (CMMS). Estos sistemas suelen organizar las actividades de mantenimiento en función de la prioridad y la disponibilidad de recursos.

Arquitectura del enfoque híbrido propuesto
ABB ha definido una arquitectura típica para su uso con el enfoque híbrido de modelos →09. Aquí, el modelo se entrena con los datos históricos almacenados del activo. Los datos históricos y el motor de cálculo de la aplicación propuesta son la plataforma CPM patentada de ABB. los datos de la aplicación se almacenan con la base de datos MS SQL y los modelos se entrenan y desarrollan con una plataforma R de código abierto. Se utiliza un servidor web para presentar los resultados y un cliente web de intranet para acceder y ver los resultados.
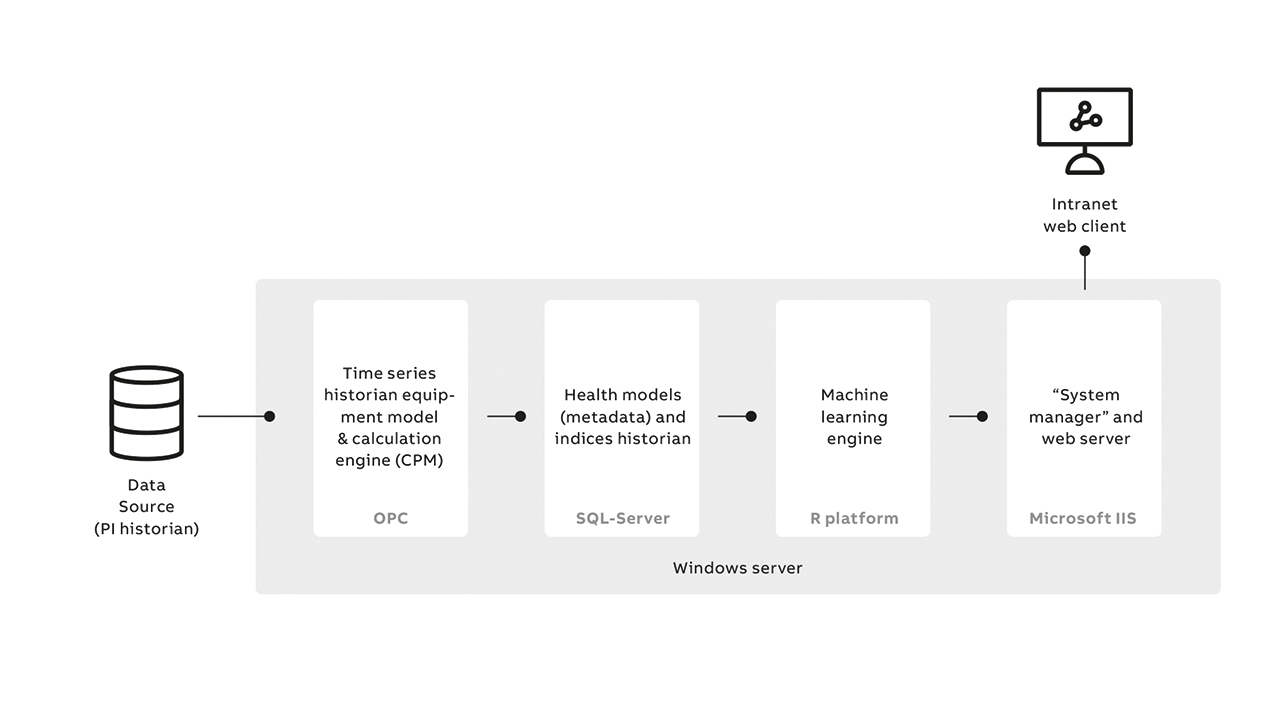
Pruebas en centrales hidroeléctricas
A mediados de 2020, Enel Green instaló con éxito el software resultante en 33 centrales hidroeléctricas. Actualmente, se está llevando a cabo una supervisión en tiempo real del estado de varios activos, como hidroturbinas, bombas, motores, generadores, etc., con una finalización prevista del proyecto para 2022. En general, los resultados se presentan en una vista jerárquica y combinada, fácilmente consultable por los usuarios, lo que supone una ventaja importante. Inicialmente, los activos se combinan lógicamente según la subsección de la planta; a continuación, se combinan lógicamente para representar toda la planta. Puede verse el número de activos que están en buen estado (verde), en el límite (amarillo) o en mal estado (rojo) a nivel de planta. El usuario puede entonces profundizar hasta diferentes niveles; puede accederse a una sección de la planta o incluso a un activo específico para consultar la información correcta necesaria.
Basándose en el éxito inicial del proyecto piloto, ABB tiene previsto ampliar el uso de este enfoque híbrido para el mantenimiento predictivo en diferentes sectores verticales, como las centrales eléctricas convencionales, las refinerías, las fábricas de cemento, la industria del petróleo y el gas, etc. Esto es posible porque, a diferencia de la modelización de primeros principios que requiere un conocimiento exacto de los equipos y procesos específicos del sector, la modelización de ML y FMA es completamente genérica por naturaleza y, por tanto, no es específica de la industria: un enfoque transformador.
Al anteponer las necesidades de la industria, ABB está desarrollando los medios para utilizar los flujos masivos de datos generados y los análisis avanzados para hacer que el mantenimiento predictivo sea verdaderamente predictivo; garantizando así que las industrias de procesos obtengan valor al mejorar la producción y maximizar el retorno de la inversión de sus equipos.
Referencias
01 Un ejemplo del primer paso del proceso de configuración del estado del activo que ilustra la relación de la medición de fallos a través de variables. Cada variable se calcula como la proporción de la suma del total.
02 El enfoque de modelo híbrido propuesto se muestra ilustrando cómo se utilizan modelos de análisis de datos y fallos para generar los indicadores del mantenimiento predictivo.
03 Se muestran los indicadores clave de diagnóstico (KDI) y los fallos. La tabla del lado inferior izquierdo muestra la información de resumen que se muestra para los tres KDI con menos puntuación de un activo. Además, a la derecha, se presenta un resumen de los fallos. Las abreviaturas de los parámetros (P) se establecen según la notación estándar ISA S5.1.
04 Se muestra un ejemplo de indicadores de estado con los valores de referencia correspondientes. Las abreviaturas de los parámetros (P) se establecen según la notación estándar ISA S5.1.
05 Resultados de ejemplo de un motor en los que se indican el valor de los KDI subyacentes. Las abreviaturas de los parámetros (P) se establecen según la notación estándar ISA S5.1.
06 Dado que los usuarios no solo tienen que consultar los indicadores de estado de corriente del equipo, el innovador enfoque híbrido de ABB les facilita la base para predecir estados futuros.
07 Ejemplos de predicción de tendencias futuras de los indicadores de estado.
08 Se muestran varios fallos y las probabilidades de que ocurran.
09 Se ilustra la arquitectura del enfoque híbrido propuesto.