Las tendencias tecnológicas, medioambientales y sociales están transformando el mundo. La industria minera, si bien tradicionalmente se encuentra en un nivel bajo en la curva de la Industria 4.0, está ganando posiciones rápidamente, principalmente a través de la electrificación de las minas. eMine™ de ABB y su sistema de trolleys asociado, así como sus accionamientos sin engranajes y su experiencia en la automatización de sistemas transportadores, están ayudando a los clientes de minería a electrificar sus equipos desde la mina hasta el puerto con soluciones idóneas.
ABB tiene amplia experiencia en todo el mundo suministrando grandes soluciones eléctricas y de control integradas a clientes de minería y minerales. Además, la empresa contribuye a que las empresas mineras den el paso hacia una mina totalmente eléctrica. La empresa se compromete a colaborar con clientes y proveedores para reducir sus emisiones anuales de CO₂ en al menos 100 megatones, lo que equivale a las emisiones anuales de 30 millones de coches de combustión, y lograr la neutralidad de carbono en sus propias operaciones en 2030. Actualmente, la minería es responsable de entre el 4 y el 7 % de las emisiones globales de gases de efecto invernadero (GEI), un área en la que los métodos actuales deben cambiar rápidamente para cumplir los objetivos, la normativa nacional y el Acuerdo de París.
Este artículo explora dos ejemplos en los que el camino hacia la mina totalmente eléctrica ya está en marcha. El primero examina la Copper Mountain Mining de Canadá, donde ABB ha instalado una infraestructura auxiliar de trolleys eléctricos. El segundo se refiere a la introducción del sistema transportador sin engranajes más potente del mundo, ubicado en la mina de cobre Chuquicamata en Chile.
Una transformación eléctrica en Canadá
Sin la extracción de materiales no habría móviles, ordenadores, baterías ni parques eólicos. La transición hacia una mina totalmente eléctrica, que permita extraer minerales con el menor impacto posible en el medio ambiente, requiere nuevas ideas, como pone de manifiesto eMine™ de ABB, un concepto recientemente lanzado, que ya está ayudando a los clientes de minería a electrificar sus equipos desde la mina hasta el puerto con soluciones adecuadas para satisfacer las demandas operativas. Esta solución está respaldada por muchas décadas de experiencia de ABB en electrificación, automatización y conexión digital de equipos y operaciones de minas para mejorar el uso energético y el rendimiento general.
Solución auxiliar completa de trolleys
Una de las soluciones clave de eMine es el ABB Ability™ eMine Trolley System →01[1], que ya se ha implantado en varios países. La solución permite que los vehículos circulen por una línea auxiliar de trolleys eléctricos en lugar de utilizar combustible diésel. Más recientemente, eMine se implantó en Columbia Británica, Canadá, donde ABB trabaja con Copper Mountain Mining →02 [2].
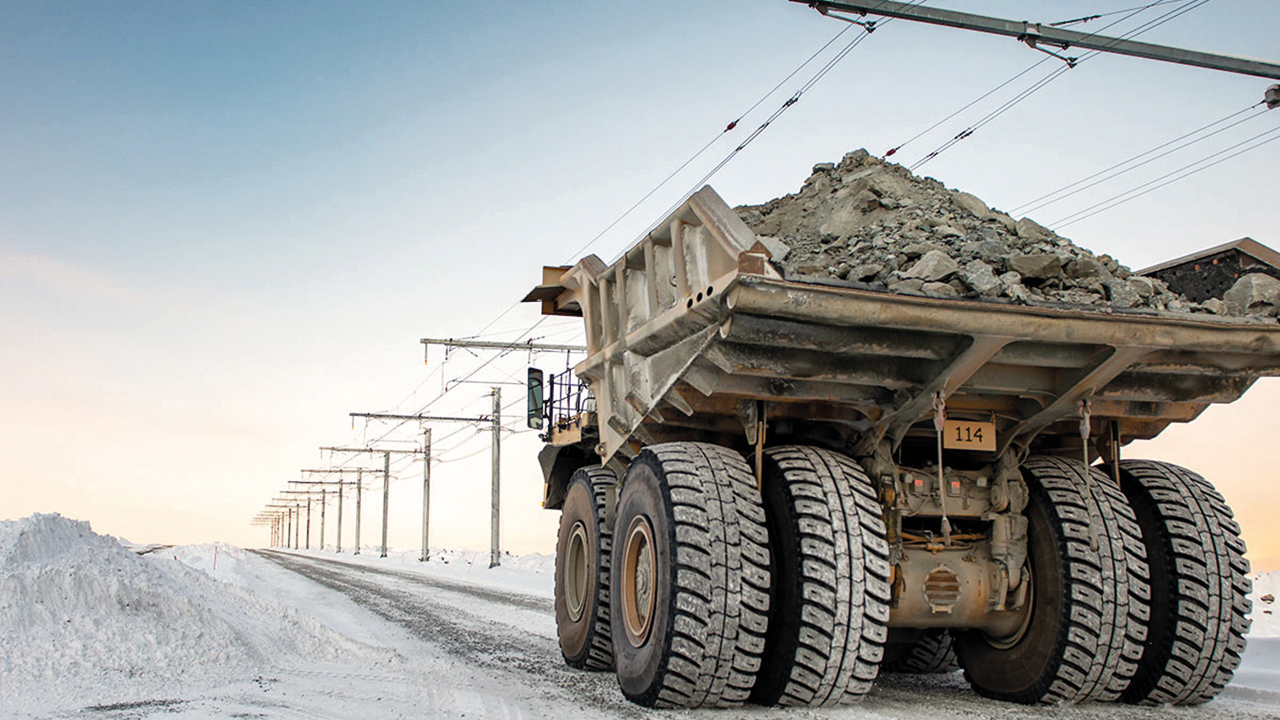
Aquí, donde una operación convencional a cielo abierto produce aproximadamente 45 000 toneladas métricas de equivalente de cobre al año, ABB ofrece una solución auxiliar completa de trolleys →03. ABB es responsable de toda la infraestructura auxiliar de trolleys sin camiones, incluido el diseño de un sistema de catenaria aérea (OCS) y una subestación rectificadora que proporciona más de 12 MW de energía de CC, así como de la gestión de ingeniería, proyectos y construcción, el suministro de equipos y la puesta en servicio del sistema.
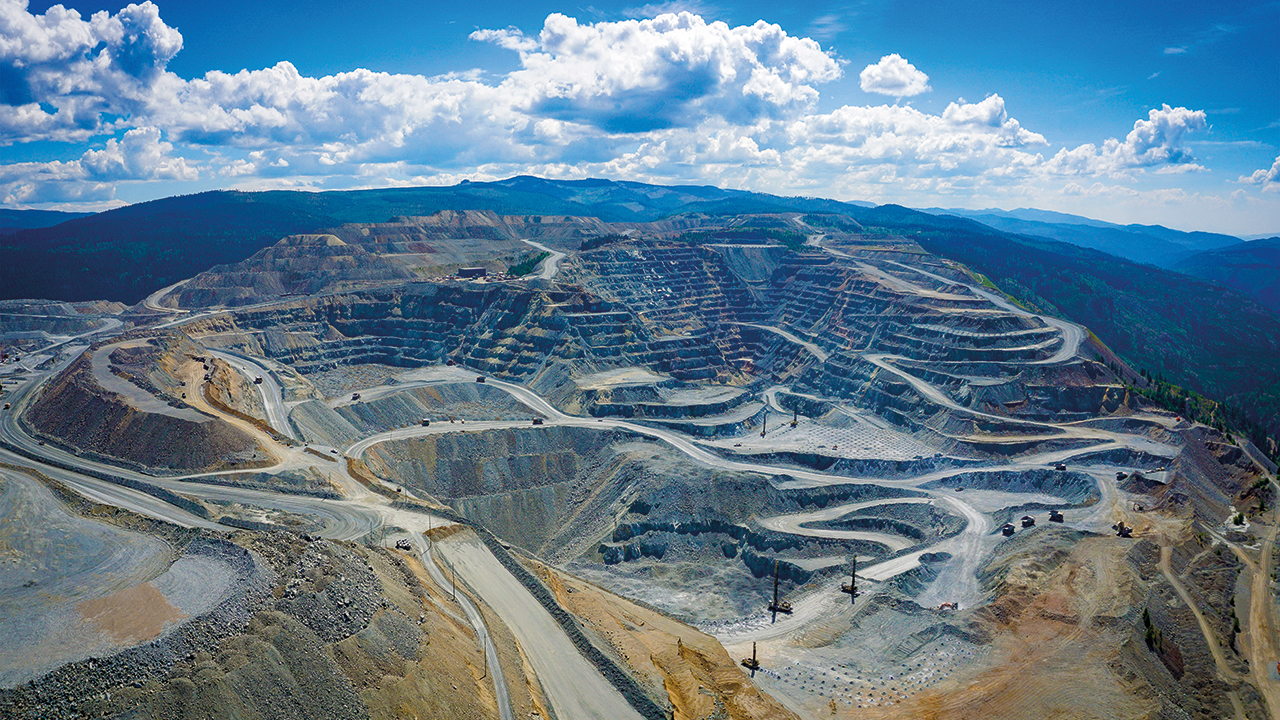
El sistema de control de trolleys puede proporcionar conectividad a la plataforma existente del sistema de control distribuido (DCS) ABB Ability™ 800xA, permitiendo una perfecta integración y supervisión de las operaciones de los trolleys y del consumo de energía. ABB también suministra componentes OCS personalizados para aplicaciones mineras.
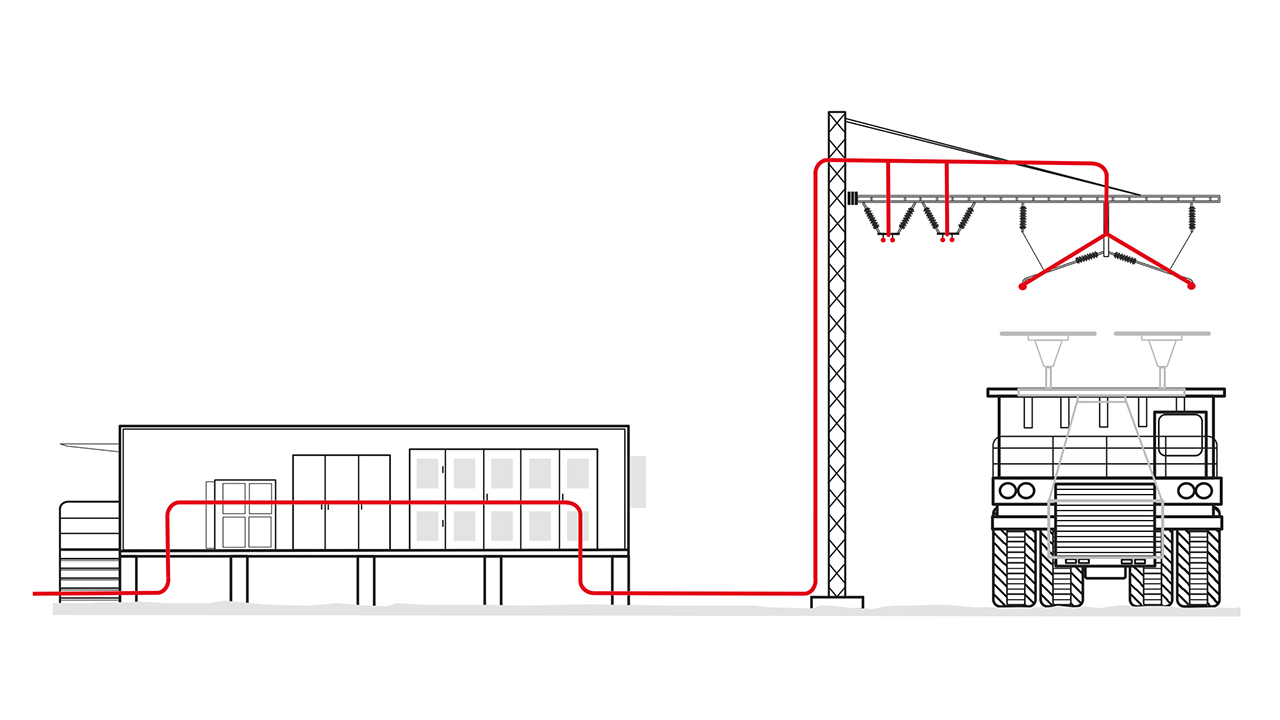
Se espera que Copper Mountain reduzca inicialmente las emisiones en un 7 % durante la primera fase del proyecto, y se ha fijado el objetivo de lograr una reducción de CO₂ del 50 % en el plazo de cinco a siete años. También se espera que el nuevo uso de trolleys mejore la eficiencia; por ejemplo, los camiones estarán equipados con un pantógrafo para recibir energía eléctrica externa, lo que les permitirá funcionar más rápido cuando se conecten al sistema de trolleys, al tiempo que consumen menos combustible y requieren menos mantenimiento. Como parte del concepto eMine™, ABB ha identificado seis elementos que serán esenciales para las operaciones totalmente eléctricas:
- Interoperabilidad: la capacidad de disponer de una infraestructura de carga versátil para todos los tipos de vehículos y fabricantes de equipos originales de vehículos eléctricos con batería (BEV)
- Movilidad/flexibilidad: la capacidad de implantar una infraestructura de punto de carga que permita a la mina adaptarse a medida que se desarrolla
- Gestión de la energía: la capacidad de combinar energía con control de procesos para minimizar los picos de carga y obtener un funcionamiento equilibrado
- Interfaz de conexión: la capacidad de operar con seguridad a altas intensidades gracias al uso de dispositivos de conexión automatizados resistentes para minas
- Tecnología de trolleys y carga: la capacidad de adaptar las infraestructuras de carga y trolleys a la capacidad de las baterías BEV para operaciones exigentes
- Proceso favorable y desarrollo de minas: la capacidad de utilizar enfoques alternativos para el desarrollo de las minas, tales como combinaciones de acarreo cuesta abajo y/o transportador o camión y grúa.
Los componentes anteriores, potenciados por ABB Ability™ MineOptimize [3], están diseñados para conseguir un diseño y unas operaciones óptimos mediante un uso equilibrado de la energía y los recursos.
IMPULSANDO UNA REVOLUCIÓN DE EFICIENCIA EN CHILE
En el remoto norte de Chile, ABB ha colaborado con la empresa industrial alemana TAKRAF en la mina Chuquicamata de Codelco, la mayor mina de cobre a cielo abierto del mundo. Allí, los accionamientos de transportadores sin engranajes (GCD) forman parte del sistema transportador más potente del mundo. También se han convertido en la solución preferida de muchos proyectos mineros a escala mundial.
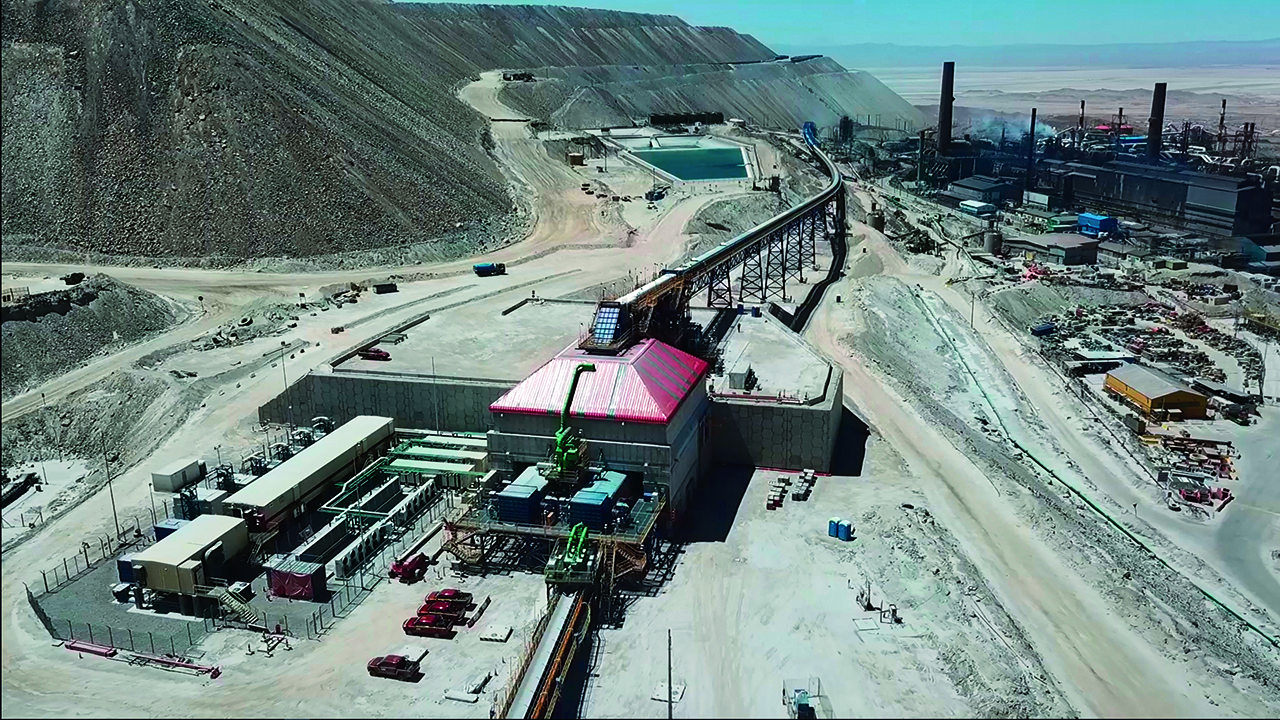
Desde el diseño técnico hasta los equipos eléctricos para el suministro eléctrico y la distribución de energía, las tecnologías de ABB y los conocimientos necesarios para integrarlas quedan patentes en toda la planta de Chuquicamata →04. Sin embargo, es en la automatización de un nuevo sistema transportador subterráneo y aéreo donde destacan las ventajas del GCD de ABB →05[4, 5, 6].
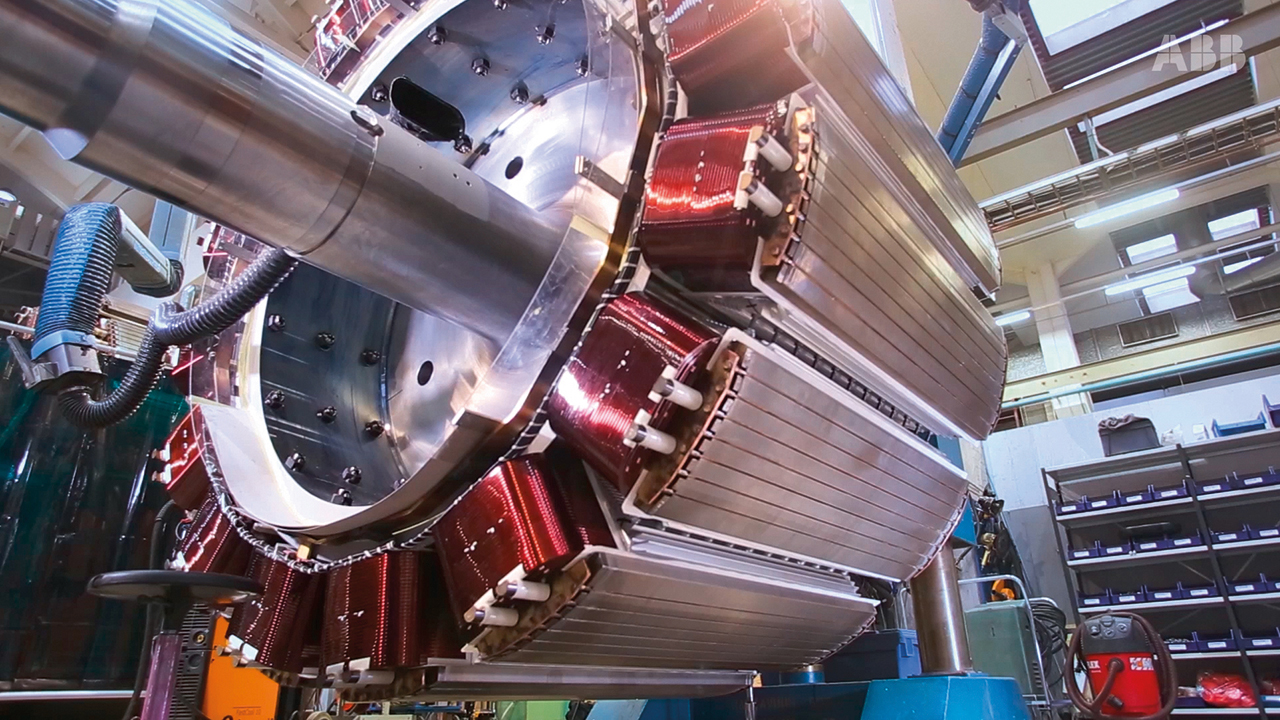
El sistema transportador de la mina debe funcionar a alta capacidad a 2850 metros sobre el nivel del mar en el desierto de la región de Antofagasta. El sistema transportador tiene una longitud de 13 km y conecta las operaciones subterráneas directamente con el concentrador del emplazamiento. Cada uno de los dos transportadores TAKRAF de 20 MW elevan 11 000 toneladas por hora (tph) de mineral a más de 600 metros para llegar a la superficie desde la mina subterránea. La elevación total es de aproximadamente 1,2 km, tras la cual el mineral pasa a un transportador aéreo de 15 MW.
Los GCD son aptos para proyectos mineros que requieren una gran potencia. Ayudan a aumentar la eficiencia de los sistemas de cintas de más capacidad, aumentando así el posible rendimiento del mineral, reduciendo el uso de energía, reduciendo el tiempo de inactividad de los equipos y minimizando los costes de mantenimiento →06. Son la única forma económicamente viable de proporcionar energía suficiente para operar los transportadores de 20 MW de la mina Chuquicamata. El límite de una caja de engranajes con piñón de entrada de un tranportador es 3-4 MW, por lo que el sistema de cintas de la mina habría requerido ocho motores asociados a una caja de engranajes con un eje de salida o varios transportadores con menor potencia nominal y múltiples estaciones de transferencia. Cualquiera de los dos escenarios habría requerido significativamente más materiales, espacio, cavidades e infraestructura para proporcionar la potencia necesaria. Por lo tanto, los GCD eran la forma más sencilla de conseguir la producción que el cliente necesitaba, con la ventaja añadida de una reducción del mantenimiento y un aumento significativo de la eficiencia.
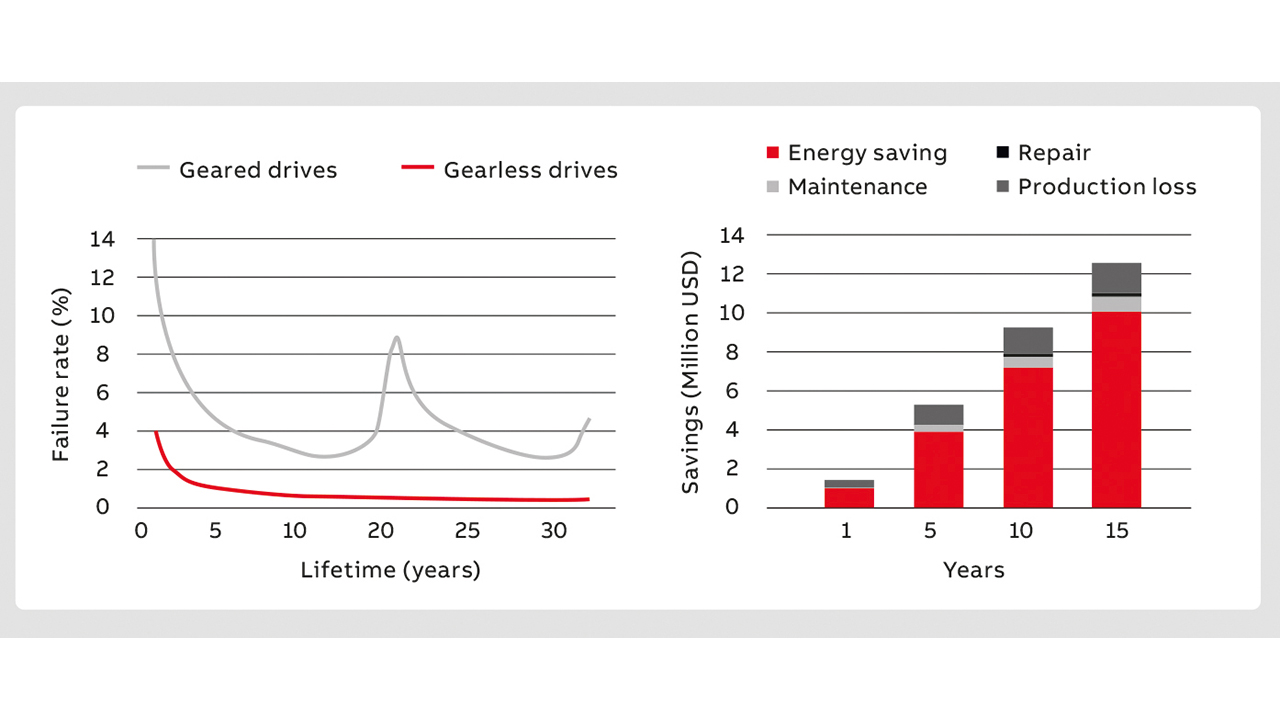
Teniendo en cuenta estos factores, ABB y TAKRAF implantaron el sistema GCD más potente del mundo. El sistema consta de 11 accionamientos con motores síncronos que funcionan a velocidades de 50-60 rpm y tienen una potencia nominal de 5 MW cada uno, lo que supone un par motor de unos 900 kNm. La potencia total instalada de todo el sistema, incluidos varios transportadores de alimentación, es de 58 MW.
Pasar de operaciones a cielo abierto con camiones y palas a operaciones subterráneas empleando el transportador TAKRAF con el GCD de ABB ayudará al propietario de la mina Codelco a ahorrar aproximadamente 130 millones de litros de gasolina al año →07. Esto se logrará eliminando la necesidad de 120 camiones grandes, reduciendo las emisiones de CO₂ de la mina de 340 000 t por año a 100 000 t, lo que supone un ahorro estimado de aproximadamente un 70 %.
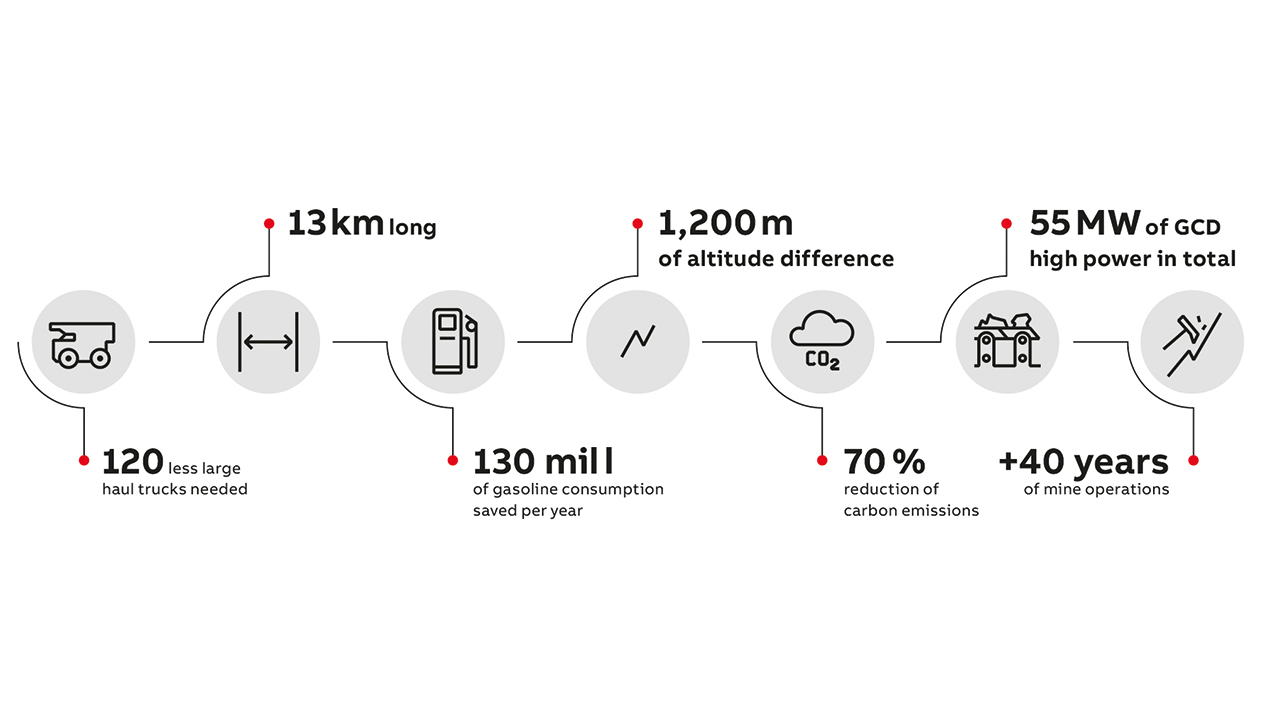
En Chuquicamata, la solución ABB/TAKRAF está conectada al sistema de control ABB Ability™ 800xA a efectos de la adquisición eficiente de datos, la evaluación de los equipos y la optimización de los procesos. El sistema 800xA supervisa y recopila datos de varios sensores integrados en el sistema de accionamiento del motor, detectando anomalías e identificando las necesidades de mantenimiento. Se espera que el proyecto amplíe sus operaciones a lo largo de los próximos 40 años.
Se espera que los requisitos de eficiencia para los GCD de potencia media en la gama de 1-10 MW (potencia total de transporte) aumenten en los próximos años. En vista de ello, ABB está respondiendo con tecnologías diseñadas para reducir el coste por tonelada de producción, ayudando así a los clientes a seguir siendo competitivos. En comparación con las soluciones con cajas de engranajes, los GCD son eficientes desde el punto de vista energético y producen menos ruido. Por otro lado, los accionamientos con cajas de engranajes tienen múltiples partes móviles girando a 1000 rpm o más y pueden ser muy ruidosos, con el riesgo de superar el límite de emisiones de ruido de 85 dB(A) (decibelios ponderados A) previsto por la UE.
Para evitar estos problemas, como parte de un proyecto de actualización en curso en la República Checa, ABB está instalando sus últimos GCD de media potencia. Al cambiar los accionamientos con engranajes montados en el eje de un sistema transportador existente equipado con GCD alimentados por motores síncronos de imán permanente, el propietario de la mina podrá cumplir los límites de emisión de ruido de la UE y evitar los fallos frecuentes de los accionamientos existentes por problemas de vibración. El uso de GCD a unas 50 rpm con refrigeradores de bajo nivel de ruido limita las emisiones de ruido de la unidad motriz a menos de 75 dBA, lo que proporciona a la mina todas las ventajas de los accionamientos sin engranajes y evita la necesidad de soluciones de encapsulamiento del ruido (carcasas alrededor de toda la unidad motriz) o paredes de protección contra el ruido a lo largo del sistema transportador. Estos GCD son un 5-8 % más eficientes energéticamente y tienen menos emisiones de CO2 que las soluciones con cajas de engranajes. Los GCD ofrecen también un mayor nivel de seguridad, ya que no necesitan combustibles ni líquidos peligrosos, como el aceite de la caja de engranajes, sino que utilizan un líquido refrigerante a base de agua.
Los GCD se utilizan en proyectos complejos y a menudo de categoría internacional. Pueden proporcionar muchos beneficios a los operadores de minas ayudándoles a aumentar la eficiencia y reducir el uso de energía, el tiempo de inactividad de los equipos, los costes de mantenimiento y el ruido. Junto con soluciones que incluyen aplicaciones de colaboración de realidad aumentada/mixta, análisis avanzado de datos, herramientas de IA y aprendizaje automático, las empresas de minería y sus socios tecnológicos están preparadas para aumentar aún más la eficiencia de las operaciones, por remotas o difíciles que sean.
Referencias
[1] ABB, Trolley-assist solution for Copper Mountain Mining sustainable development – Canada | ABB [Consultado el 11 de junio de 2021].[2] Copper Mountain Mining. The Copper Mountain mine, British Columbia, Canada. Disponible en: https://www.mining-technol-ogy.com/projects/copper-montain/ [Consultado el 11 de junio de 2021].[3] ABB, ABB Ability™ MineOptimize. Disponible en: https://new.abb.com/mining/mineoptimize [Consultado el 11 de junio de 2021].[4] ABB. ABB completes commissioning of the world’s most powerful conveyor system. Disponible en https://new.abb.com/news/detail/68172/abb-completescommissioning-of-theworlds-most-powerfulconveyor-system [Consultado el 8 de octubre de 2021].
[5] ABB. ABB gearless drives for TAKRAF’s most powerful mining conveyors in Chile. Disponible en https://new.abb.com/mining/reference-stories/underground-stories/takraf-underground-mining-conveyors-with-abb-gearless-drives-progressing-in-chile[Consultado el 8 de octubre de 2021].
[6] ABB. Video of the world’s most powerful Gearless Conveyor Drive system: https://youtu.be/tYHsqwo4TJU [Consultado el 19 de junio de 2021].