A manutenção preditiva não é, e nem pode ser, algo para a indústria do futuro. A notícia de que ela é uma aliada da gestão de recursos e ativos, assim como promissora candidata para redução de custos operacionais, já correu o suficiente para se tornar um tanto velha. Resta agora às indústrias do setor de energia colocar em prática o que vem sendo discutido e apresentado para finalmente usufruir de seus benefícios.
A manutenção preditiva é, por si só, um benefício da digitalização dos processos industriais. Uma vez automatizados e digitalizados os fluxos da operação, a empresa é munida de dados importantes sobre a condição e comportamento dos ativos. E esses dados têm no mínimo uma finalidade importante: informar e basear análises em prol da saúde do negócio. Neste ponto, as decisões informadas a respeito de quando parar o ativo para manutenção já são o segundo ganho dessa cadeia de benefícios iniciada com a digitalização.
No segmento de energia, parar ou não parar é muito mais que uma questão filosófica, é uma questão de competitividade, inclusive de sobrevivência do negócio. Parar uma operação pode custar milhões, daí a importância de se trabalhar com dados de qualidade para pausar ativos somente quando houver sinais claros de que eles vão apresentar uma falha, que por sua vez é possível ser corrigida antes mesmo de acontecer.
Para se ter uma ideia do que poderia ser perdido, uso o exemplo da Refinaria de Capuava da Petrobras em São Paulo, que recentemente anunciou uma parada programada para manutenção com um investimento de R$160 milhões. A Recap tem capacidade para produzir 10.000 m3/dia (62,8 mil barris) e responde por cerca de 30% do volume de combustível comercializado na Grande São Paulo. Uma parada não planejada poderia acarretar uma perda muito superior ao investido na pausa programada para manutenção. Agora, escale esse problema para operações que produzem, por exemplo, 100 mil barris por dia.
Com dados de qualidade e análises claras da condição dos ativos, a manutenção preditiva entra em ação baseada em um histórico que indica quando ela é necessária. Isso é possível graças a sistemas de automação e digitais que possibilitam a extração, visualização e análise de grandes volumes de dados. Um exemplo dessa união de automação e digital é o 800xA, cérebro da automação da ABB porque integra informações em tempo real e fornece visualizações sobre a condição dos ativos.
Além da tecnologia de ponta, a manutenção preditiva requer análise crítica da realidade e estratégia de implementação, ações que dependem totalmente do engajamento das pessoas da operação.
Seis passos para aplicar a manutenção preditiva na operação
Colocar a manutenção preditiva em prática requer dar o primeiro passo, seguido de outros cinco fundamentais para o processo dar certo. [1]
1- O primeiro deles é obter uma visão clara dos dados, isto é saber como estão os seus ativos, que tipo de dados você tem a respeito deles. A busca por essa base de dados acontece em conjunto com a equipe de TI, que vai operacionalizar essa extração e armazenamento de dados de forma segura.
2 - O próximo passo é entender os gaps que foram identificados entre os dados levantados e buscar fechá-los por meio de soluções para que se tenha condições de extrair e visualizar as informações críticas de ativos que possam estar em falta. Nesse ponto de implementação, vale lançar mão de soluções de monitoramento da condição dos ativos com ferramentas de visualização online e integradas aos demais processos da indústria.
3 - O terceiro passo é aprender com as falhas as tendências mais relevantes, isto é, verificar no histórico dos ativos o que levou à falha e transformar essa informação em indicador.
4 - Essa ação de análise das tendências leva ao quarto passo, que é utilizar o histórico para prever a falha antes dela acontecer e assim otimizar a manutenção. Este é o coração da manutenção preditiva: uma pausa estratégica e com foco no problema, o que reduz o tempo de parada e, consequentemente, os custos financeiros provenientes dessa suspensão da operação.
5 - O quinto passo é, na verdade, como dar um passo maior: estude como ampliar esse aprendizado para o negócio como um todo. Aqui é importante ficar claro que a manutenção preditiva pode começar por uma área do negócio e ser expandida para toda a operação, ainda estamos na lógica de passo a passo. Nessa fase em que se busca escalar os benefícios da manutenção preditiva, entram soluções para gerenciamento geral da empresa.
6 - O último passo, e não por isso menos importante, requer a participação das pessoas. Depois de identificar a situação dos dados dos ativos, resolver gaps de informação, aprender as tendências e aplicá-las para prever a falhar antes de acontecer e escalonar isso para outras áreas da empresa, todas as pessoas de todos os níveis da operação precisam estar aculturadas ao processo de manutenção preditiva. Isso significa que todos estarão, em alguma medida, envolvidos com a identificação, compreensão e aplicação de métodos e processos que fomentem a manutenção preditiva.
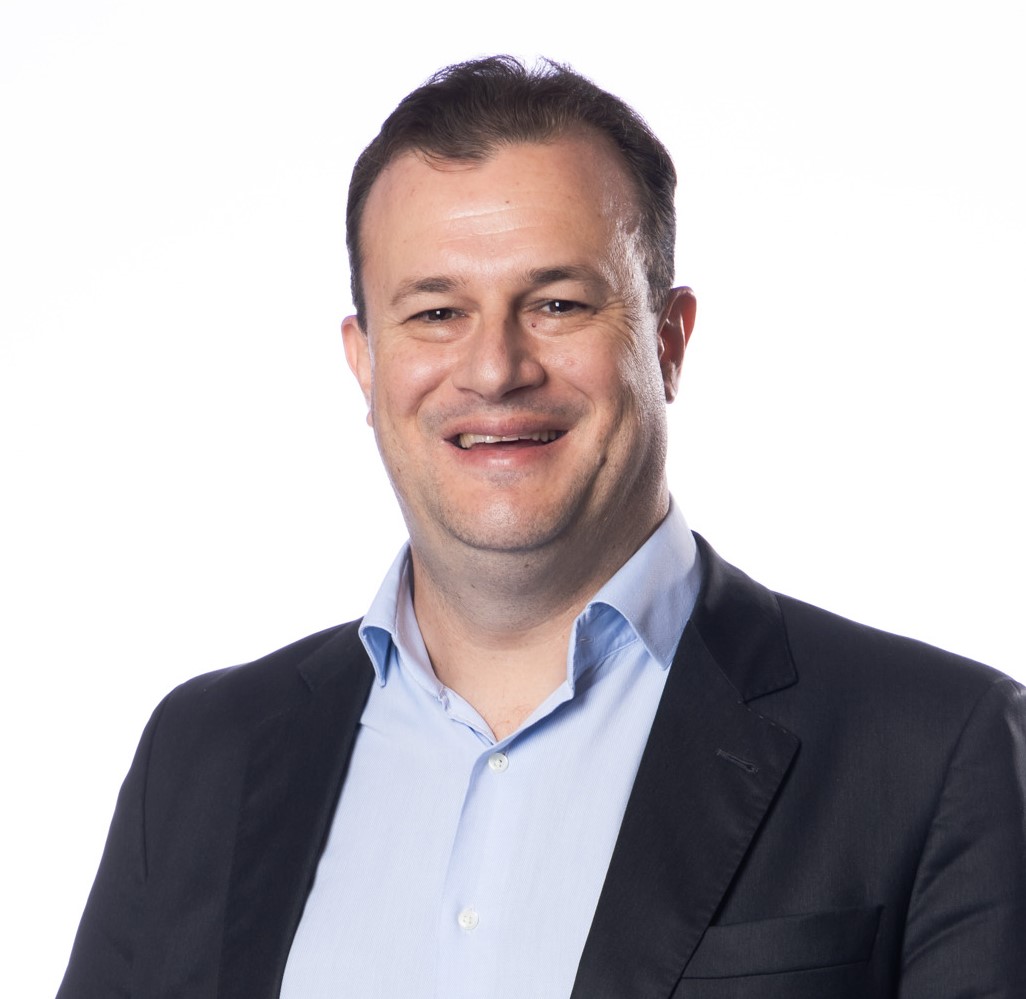
Sem digitalização, é impossível obter dados de qualidade sobre como vai a operação da sua empresa. Sem dados, a manutenção preditiva não pode ser aplicada de forma a retornar redução de tempo de máquina parada e de custos. E sem pessoas dispostas a incorporar a cultura da informação qualificada para uma operação otimizada, nenhum avanço é possível e os passos para a manutenção preditiva, sejam quantos forem, serão dados em vão.