故事背景
傳統鑄造業需求大量的人力,面對人口高齡化的趨勢,加上工廠作業型態常暴露於高溫環境,以及粉塵汙染和噪音危害等問題,使得行業長期以來處於人力短缺。近年來由於客製化產品需求漸增,對物件處理的技術要求也越來越嚴格,看準自動化能克服製造過程中的痛點,企業主紛紛導入先進的機器人設備,設法提升製造能力。
關鍵挑戰
拋光研磨是金屬加工中常見的製程,以往透過人工處理拋光研磨加工,雖尚能滿足一般工件的需求,但過程費時又費工,產出的品質較不穩定,生產成本亦相對高昂。面對類型眾多的金屬加工物件,特別是高價值和特定材料的部件,以及少量多樣的生產需求,如何維持品質一致性、降低不良率,提高光滑平整度、減少表面損傷及裂紋,是製造商迫切需解決的問題。
解決方案
解決方案 機器人研磨拋光解決方案使用 ABB IRB 2600 機器人,整合砂帶機、千葉輪與去毛刺氣動工具,並提供模組化的周邊研磨設備選項,組成一站式的自動化單元。IRB 2600 優異的精度及緊湊的結構設計,適用於工件表面拋光等加工,亦能針對曲面研磨、複雜角度及形狀的鑄件進行表面處理,搭配 ABB RobotStudio 離線編程軟體,能自動生成最佳路徑、優化加工製程,達到「混線」及「快速換線」的彈性生產需求。
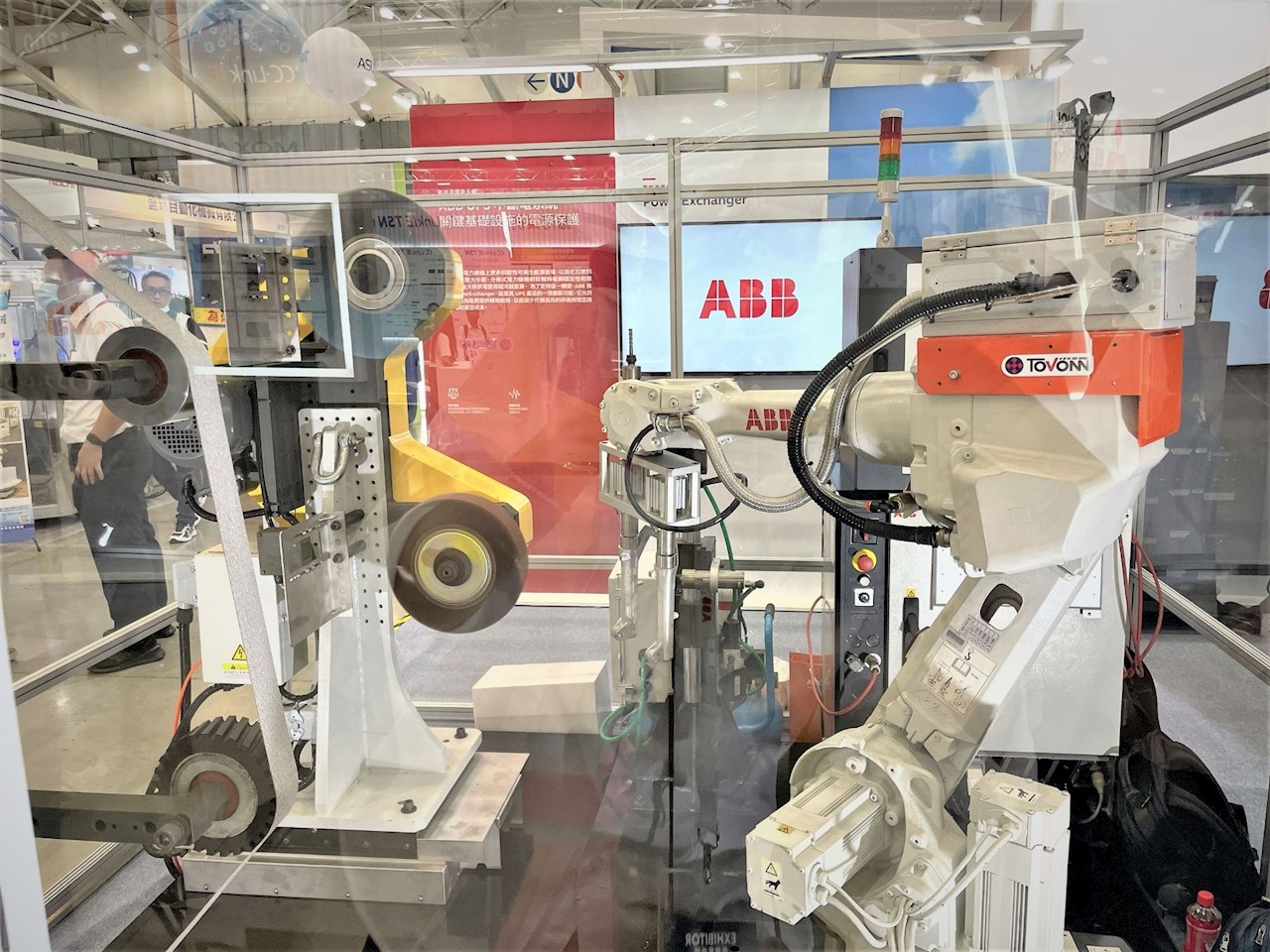
實際應用
機器人是拋光研磨自動化方案的核心,手臂本身的精度及力回饋是關鍵的技術,機器人採用預先定義的路徑與速度進行位置控制,搭配 ABB 的力回饋控制技術 (Force Control),可依照工件狀態調整拋光方向或研磨位置,並根據力傳感器的反饋訊息改變其路徑或速度,減少加工過程所產生的震動,進而增強刀具的耐用性,同時延長設備的使用壽命。透過ABB離線編程軟體 RobotStudio 中的Machining PowerPac,引導使用者從導入的 CAD 模型的表面和邊緣創建精確的目標與路徑,在模擬系統中調控相關工藝參數,透過動態預覽優化走刀路徑及下刀方向,確保加工點位的機器人姿態精準無誤。
成果效益
「機器人研磨拋光解決方案」憑藉機器人的高重複精度優勢,能有效提高生產品質及效率、降低廢品率,助力金屬表面後處理這類講求光滑平整度的應用。針對不同加工應用及製程需求,整合機械設備並建構彈性生產線,實現高效精準、安全穩定的生產,同時降低高風險環境之災害、保障勞動安全,解決勞動力不足及管理不易的問題。該方案目前也已成功導入至金屬加工相關應用,如:汽機車及電動車產業、腳踏車車架、水五金產業、3C產業等行業。