The plant has three cooling towers that produce chilled water for the manufacturing process. Each cooling tower has two fans, each driven by a 37 kW fan motor.
Originally, the fans were star/delta connected, arranged in cascade style so that they would startup, or disconnect, one-by-one as demand varied. This meant the final fan would constantly be switching on and off, sometimes as often as every 10 minutes. With a large 37 kW motor, this would draw significant startup current.
Additionally, whenever an odd number of fans were connected, air from the last fan would blow out through one of the other fans.
The company asked local ABB HVAC partner, Drive Control, to look at the installation and come up with an energy saving solution. This involved installing six 37 kW ABB standard drives for HVAC on the cooling towers, each driving a fan motor.
With the ABB drives, two fans start on the first tower at 20 Hz when the building management system indicates that cooling is needed. If more cooling is required, the next two fans start at 20 Hz and then the remaining two start if there is demand for still more cooling.
For maximum cooling, all six fans run together between 20 Hz and 50 Hz. At an installed cost of 15,000 pounds, an annual saving of 31,400 pounds is achieved. Further energy saving projects with AC drives have since been carried out, enabling X-FAB to reduce electricity use by about 5 percent across the site.
Maintenance costs have also been reduced, as drive belts would previously break at least once a month with the old system.
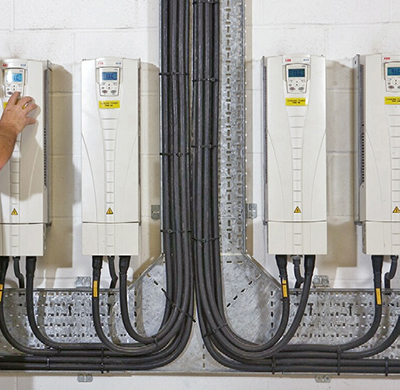
Maintenance costs were reduced through fewer motor belt breakages.